- お役立ち記事
- Measures to improve the quality of prototypes through precision cutting
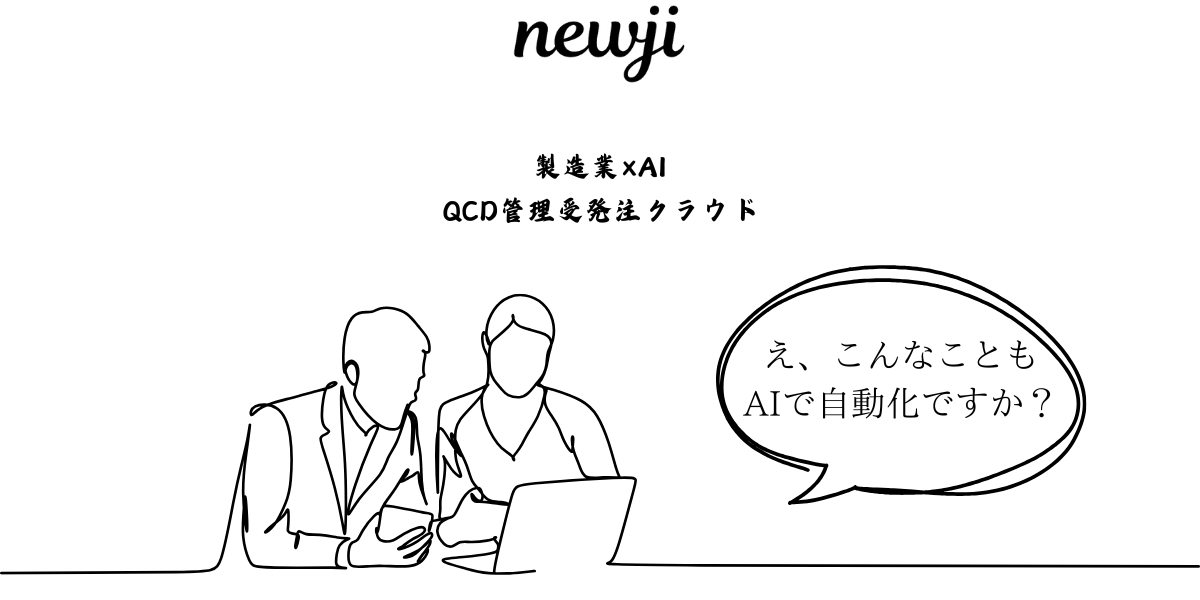
Measures to improve the quality of prototypes through precision cutting
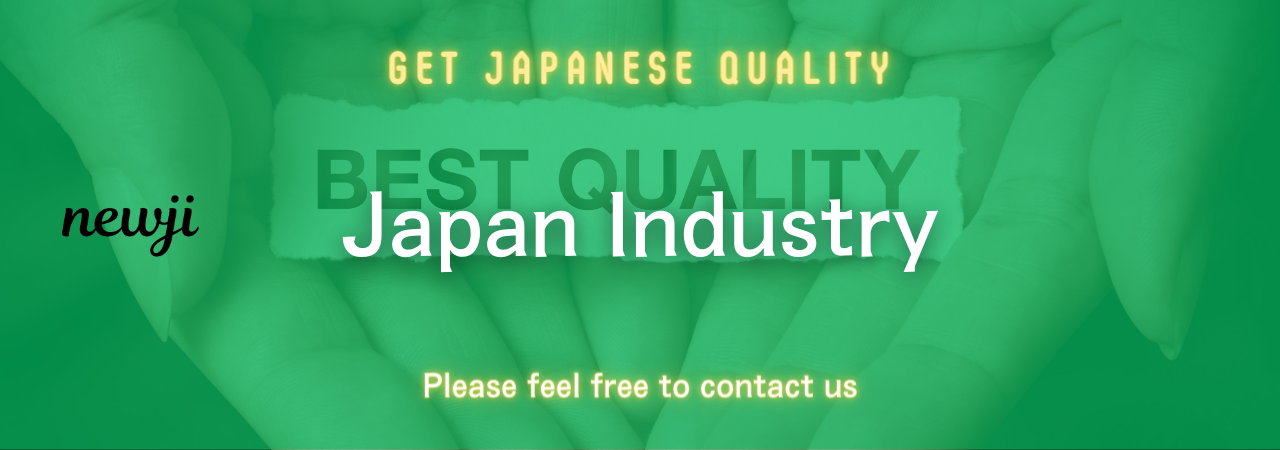
目次
Understanding Precision Cutting
Precision cutting is a critical technique used in manufacturing and prototyping to achieve superior quality and accuracy in components.
It’s an essential part of producing prototypes that meet exact specifications and function effectively.
The process involves using advanced machinery capable of making very specific cuts to ensure that the dimensions and features of the material are precise.
The significance of precision cutting cannot be overstated when it comes to prototyping.
It directly influences the functionality and assembly of the manufactured parts, which are crucial in developing a successful product.
By implementing precision cutting, manufacturers can reduce errors and ensure that prototypes are as close to the final product as possible.
Benefits of Precision Cutting in Prototyping
There are several benefits to using precision cutting in prototyping, making it a preferred method in modern manufacturing processes.
First and foremost, precision cutting leads to improved accuracy.
With high precision, designers and engineers can develop prototypes that closely match their design intent.
This accuracy reduces the need for multiple prototype iterations, saving both time and resources.
Moreover, precision cutting is cost-effective.
By producing parts that fit seamlessly together from the onset, manufacturers can avoid costly adjustments and rework.
This cost efficiency is particularly beneficial in industries that rely on the rapid development of new products.
Additionally, precision cutting allows for the use of a wide range of materials.
From metals to plastics, precision cutting machines can handle various materials without compromising quality.
This versatility is invaluable for industries with diverse prototyping needs.
Methods of Precision Cutting
There are several methods used to achieve precision cutting in the manufacturing industry.
Each method has its strengths and is chosen based on the material and the specific requirements of the prototype.
One popular method is laser cutting.
Laser cutting uses a focused beam of light to cut through materials with high precision.
It is particularly effective for intricate designs and is widely used in industries such as electronics and automotive manufacturing.
Another method is CNC machining.
CNC (Computer Numerical Control) machining is a subtractive process that uses computer-controlled machines to remove material.
This method is highly precise and is often used for complex parts that require tight tolerances.
Waterjet cutting is another precision cutting method where high-pressure water streams are used to cut through materials.
It’s suitable for both metal and non-metal materials and is especially useful for heat-sensitive materials, as it does not generate heat during the cutting process.
Choosing the Right Method
Selecting the appropriate precision cutting method depends on various factors, including the material, design complexity, and desired outcome.
Manufacturers must consider the strengths and limitations of each method to choose the best one for their prototyping needs.
For instance, if working with delicate or heat-sensitive materials, waterjet cutting might be the preferred choice.
Conversely, for projects requiring high-definition details, laser cutting would be more suitable.
It’s essential to work closely with engineers and designers to determine the best approach for each project.
Improving Prototype Quality
Improving the quality of prototypes through precision cutting requires careful planning and execution.
Manufacturers should focus on a few key areas to ensure the best results.
Firstly, it’s vital to invest in state-of-the-art precision cutting machinery.
Advanced machines offer greater accuracy and flexibility, which are critical for producing high-quality prototypes.
Secondly, training and expertise play a crucial role.
Skilled operators who understand the intricacies of precision cutting techniques can make a significant difference in the final output.
Investing in ongoing training ensures that operators remain proficient and can leverage the latest advancements in technology.
Collaboration across teams is also essential.
Engineers, designers, and manufacturers should work together throughout the prototyping process to identify potential issues early and address them promptly.
Quality Control and Testing
Ensuring the quality of prototypes doesn’t end once the cutting process is complete.
Robust quality control and testing procedures are necessary to verify that the parts meet the required standards.
Regular inspection and testing can identify any discrepancies and ensure that each part is flawless.
Non-destructive testing methods, such as ultrasonic testing, can evaluate the integrity of the parts without causing damage.
By integrating comprehensive testing protocols, manufacturers can be confident in the performance and reliability of the prototypes.
Continuous Improvement in Prototyping
The journey to improving prototype quality through precision cutting is ongoing.
Manufacturers must adopt a mindset of continuous improvement to stay competitive and innovative.
Keeping up with the latest advancements in precision cutting technology is vital.
New developments can offer enhanced capabilities and processes that streamline production.
Feedback loops are also integral to improvement.
Collecting and analyzing feedback from customers and end-users provides valuable insights into areas for enhancement.
By listening to feedback, manufacturers can refine their processes and deliver superior prototypes.
Incorporating these strategies ensures that manufacturers maintain a high standard of quality and continue to meet the evolving demands of the market.
Prototyping is a critical phase in product development.
By implementing precision cutting techniques, producers can enhance accuracy, efficiency, and reliability, leading to successful product launches.
The focus should always be on leveraging technology and expertise to drive innovation and quality in every prototype.
資料ダウンロード
QCD調達購買管理クラウド「newji」は、調達購買部門で必要なQCD管理全てを備えた、現場特化型兼クラウド型の今世紀最高の購買管理システムとなります。
ユーザー登録
調達購買業務の効率化だけでなく、システムを導入することで、コスト削減や製品・資材のステータス可視化のほか、属人化していた購買情報の共有化による内部不正防止や統制にも役立ちます。
NEWJI DX
製造業に特化したデジタルトランスフォーメーション(DX)の実現を目指す請負開発型のコンサルティングサービスです。AI、iPaaS、および先端の技術を駆使して、製造プロセスの効率化、業務効率化、チームワーク強化、コスト削減、品質向上を実現します。このサービスは、製造業の課題を深く理解し、それに対する最適なデジタルソリューションを提供することで、企業が持続的な成長とイノベーションを達成できるようサポートします。
オンライン講座
製造業、主に購買・調達部門にお勤めの方々に向けた情報を配信しております。
新任の方やベテランの方、管理職を対象とした幅広いコンテンツをご用意しております。
お問い合わせ
コストダウンが利益に直結する術だと理解していても、なかなか前に進めることができない状況。そんな時は、newjiのコストダウン自動化機能で大きく利益貢献しよう!
(Β版非公開)