- お役立ち記事
- Measures to improve traceability throughout the supply chain led by the purchasing department
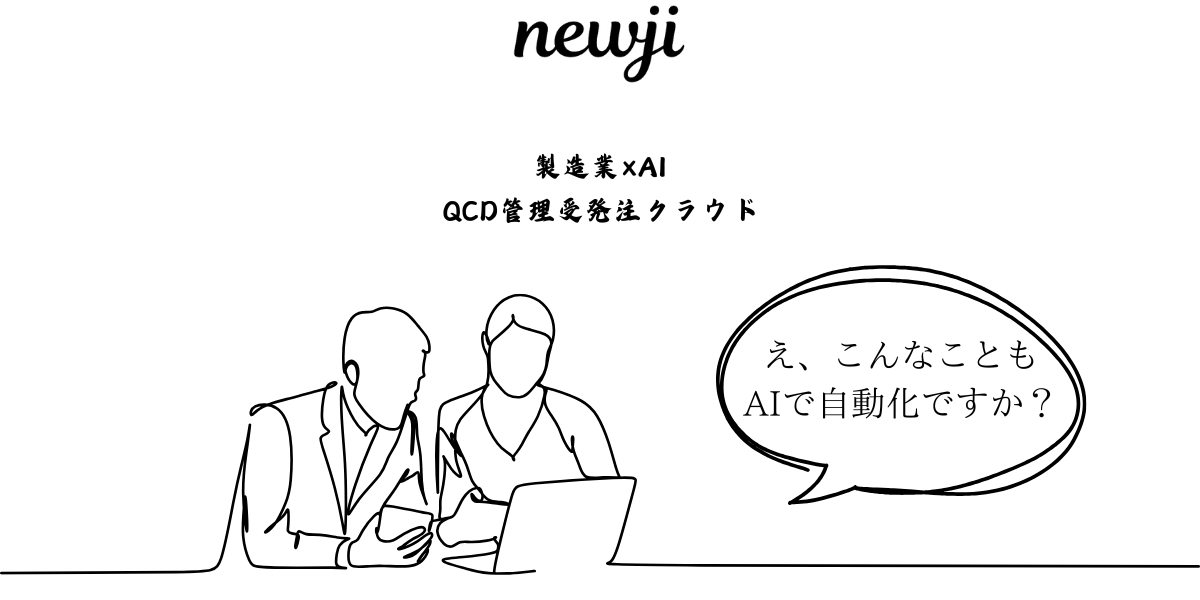
Measures to improve traceability throughout the supply chain led by the purchasing department
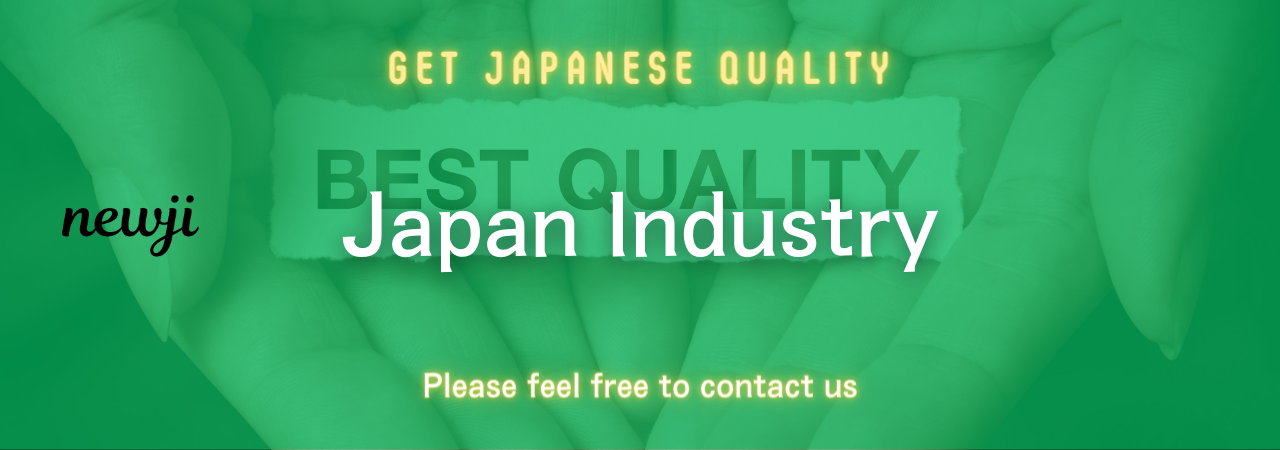
目次
Understanding Traceability in the Supply Chain
Traceability in the supply chain refers to the ability to track the origin, movement, and final destination of goods and their components throughout the entire manufacturing process.
It’s a crucial aspect for businesses aiming to enhance efficiency, ensure quality, and meet compliance requirements.
Improving traceability is particularly pertinent for the purchasing department, as its role in sourcing materials and managing suppliers directly affects the entire chain.
Why the Purchasing Department is Key
The purchasing department holds a central position in the supply chain due to its responsibility for acquiring raw materials and services required for production.
By leading traceability efforts, the department can ensure that all stakeholders in the supply chain are aligned and informed.
This proactive approach helps in identifying any disruptions at the source and addresses quality issues promptly before they escalate further along the chain.
Advantages of Improved Traceability
Enhanced Quality Control
One of the direct benefits of improved traceability is better quality control.
When purchasing departments can trace materials to their origins, they are in a better position to ensure that suppliers adhere to quality standards.
This not only reduces defects in final products but also boosts customer satisfaction.
Increased Transparency
Transparency in the supply chain fosters trust among all parties involved, from suppliers to customers.
By implementing traceability measures, the purchasing department can provide clear and precise information about product origins, thus enhancing the company’s credibility and market reputation.
Better Risk Management
Risks like recalls, non-compliance penalties, and supply chain disruptions can be effectively managed with improved traceability.
The purchasing department can identify potential risks early and take corrective measures to mitigate them efficiently.
This not only safeguards the brand image but also minimizes financial losses.
Cost Efficiency
Although setting up a robust traceability system might involve upfront costs, it leads to savings in the long run.
Improved supply chain visibility helps the purchasing department in optimizing inventory, reducing waste, and negotiating better terms with suppliers.
Steps for the Purchasing Department to Improve Traceability
Adopt Technology Solutions
Leveraging advanced technologies such as blockchain, IoT, and AI can significantly improve supply chain traceability.
For instance, blockchain provides a decentralized ledger that can securely record every transaction, ensuring transparency and preventing tampering.
IoT devices and sensors, on the other hand, can constantly track products and materials in real-time.
Establish Clear Traceability Goals
The purchasing department should start by defining clear goals that align with the organization’s overall supply chain strategy.
These goals could range from reducing product recall risks to enhancing supplier accountability.
Having a clear vision and specific objectives makes it easier to prioritize actions and allocate resources effectively.
Collaborate with Suppliers
Strong collaboration with suppliers is key to achieving comprehensive traceability.
Purchasing departments should communicate traceability expectations and requirements clearly to suppliers.
Developing supplier partnerships that emphasize compliance and accountability builds a more resilient supply chain.
Utilize Barcode and RFID Technologies
Implementing barcode or RFID systems can enhance traceability by enabling the tracking of raw materials and products through each stage of the supply chain.
These technologies provide accurate data regarding the movement and status of goods, which the purchasing department can analyze to improve decision-making.
Conduct Regular Audits and Assessments
Regular audits of suppliers and internal processes are vital to maintaining traceability standards.
The purchasing department should establish a routine for assessing the compliance of suppliers and the effectiveness of traceability mechanisms.
Continuous improvement based on audit results ensures that traceability is consistently upheld.
Challenges in Improving Traceability
While the benefits of improved traceability are clear, several challenges must be acknowledged:
Integration with Legacy Systems
Many organizations still rely on outdated legacy systems that lack the capability to integrate advanced traceability technologies seamlessly.
It often requires a strategic approach and investment to update these systems without disrupting current operations.
Cost of Implementation
The cost of implementing new traceability solutions can be a significant barrier, especially for smaller companies.
Purchasing departments must justify these costs by illustrating the potential return on investment through enhanced efficiency and risk reduction.
Data Management
With increased transparency comes the challenge of managing vast amounts of data generated across the supply chain.
The purchasing department needs to establish systems for collecting, storing, and analyzing this data effectively to derive actionable insights.
Conclusion
Improving traceability throughout the supply chain is essential for businesses seeking a competitive edge in today’s market.
The purchasing department plays a pivotal role in driving these efforts by utilizing technology, defining clear goals, collaborating with suppliers, and ensuring compliance.
Despite challenges such as integration costs and data management, the benefits of enhanced traceability in terms of quality control, transparency, risk management, and cost efficiency make it a worthwhile endeavor.
By committing to these improvements, purchasing departments can help their organizations not only meet regulatory requirements and customer expectations but also achieve operational excellence.
資料ダウンロード
QCD調達購買管理クラウド「newji」は、調達購買部門で必要なQCD管理全てを備えた、現場特化型兼クラウド型の今世紀最高の購買管理システムとなります。
ユーザー登録
調達購買業務の効率化だけでなく、システムを導入することで、コスト削減や製品・資材のステータス可視化のほか、属人化していた購買情報の共有化による内部不正防止や統制にも役立ちます。
NEWJI DX
製造業に特化したデジタルトランスフォーメーション(DX)の実現を目指す請負開発型のコンサルティングサービスです。AI、iPaaS、および先端の技術を駆使して、製造プロセスの効率化、業務効率化、チームワーク強化、コスト削減、品質向上を実現します。このサービスは、製造業の課題を深く理解し、それに対する最適なデジタルソリューションを提供することで、企業が持続的な成長とイノベーションを達成できるようサポートします。
オンライン講座
製造業、主に購買・調達部門にお勤めの方々に向けた情報を配信しております。
新任の方やベテランの方、管理職を対象とした幅広いコンテンツをご用意しております。
お問い合わせ
コストダウンが利益に直結する術だと理解していても、なかなか前に進めることができない状況。そんな時は、newjiのコストダウン自動化機能で大きく利益貢献しよう!
(Β版非公開)