- お役立ち記事
- Measures to improve traceability throughout the supply chain that purchasing departments should focus on
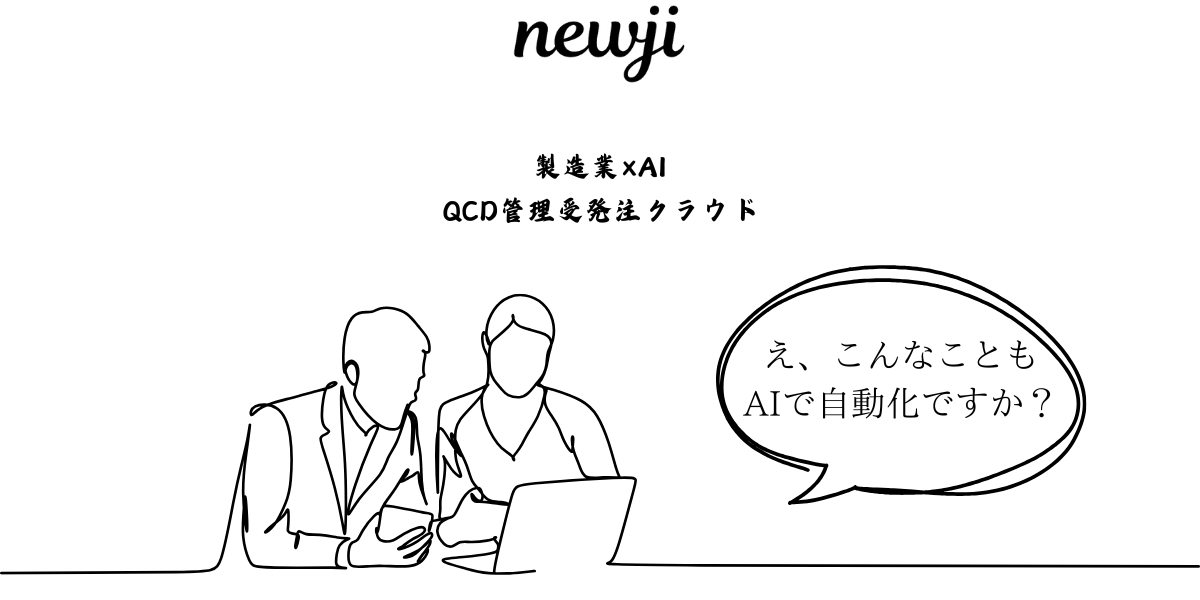
Measures to improve traceability throughout the supply chain that purchasing departments should focus on
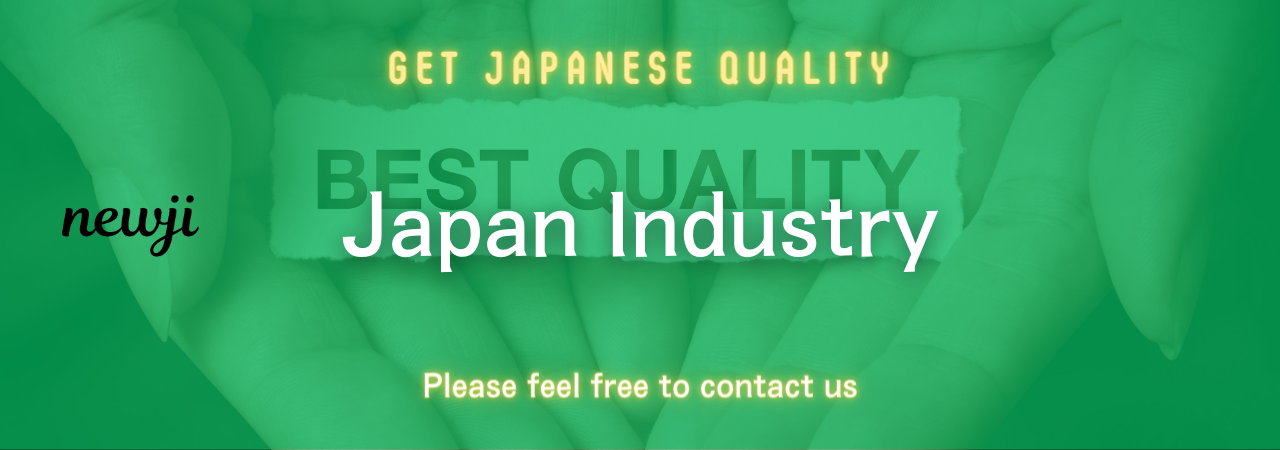
目次
Understanding Traceability in the Supply Chain
Traceability in the supply chain refers to the ability to track all parts, processes, and finished products from the very start of production to their final destination.
This concept is fundamental in ensuring product quality, safety, and compliance with regulatory standards.
For purchasing departments, focusing on traceability is crucial for minimizing risks, enhancing operational efficiency, and building trust with consumers.
By being able to pinpoint each step a product takes along the supply chain, companies can quickly identify a problem’s origin, leading to faster resolutions and improved overall transparency.
The Importance of Improved Traceability
Improving traceability in the supply chain offers numerous benefits.
First, it ensures regulatory compliance, which is a critical aspect for many industries.
For instance, food and pharmaceutical sectors are highly regulated, and companies in these fields must meet stringent traceability requirements.
Better traceability also translates to increased product safety.
If an issue arises, such as contamination or defect in a product, having a robust traceability system allows for prompt recalls, thus reducing potential harm to consumers.
Moreover, traceability enhances customer trust and satisfaction.
Consumers are becoming more conscious about the products they buy and expect transparency about their origins and manufacturing processes.
Being able to provide this information can differentiate a company in a competitive marketplace.
Key Traceability Measures for Purchasing Departments
1. Utilize Advanced Technology Systems
One of the most effective ways for purchasing departments to enhance traceability is through the adoption of advanced technology systems.
Implementing software that integrates blockchain, RFID, or IoT devices can create a digital trail that captures each step of the supply chain process.
These technologies provide real-time data, allowing for improved accuracy and speed in tracking products.
2. Collaborate with Suppliers
Strong relationships with suppliers are essential for traceability.
Purchasing departments should work closely with their suppliers to ensure that they adhere to standards that facilitate traceability.
This includes requiring them to use digital tracking systems and sharing important data regarding production and transportation.
Creating agreements or contracts that stipulate adherence to traceability practices can also help in maintaining consistent and reliable data across the supply chain.
3. Implement Standardized Processes
Standardizing processes across the supply chain is vital for effective traceability.
Clear protocols should be established for data collection, storage, and sharing to ensure consistency.
Purchasing departments can benefit from implementing regulations and guidelines that outline these processes.
This simplifies tracking and ensures that everyone in the supply chain is on the same page.
4. Conduct Regular Audits
Conducting regular audits of the supply chain is necessary to maintain traceability.
These audits identify any weaknesses or gaps in the current traceability systems, allowing for timely improvements.
Purchasing departments should conduct both internal and external audits, ensuring all parties involved are compliant with the stated traceability standards.
Challenges in Enhancing Traceability
While improving traceability is vital, it does come with its own set of challenges.
One of the main obstacles is the cost associated with implementing advanced technologies and systems required for effective traceability.
Purchasing departments often face budget constraints, making it difficult to invest in new technologies.
Also, the complexity of global supply chains can pose significant hurdles.
Coordinating traceability efforts across multiple countries with varying regulations and standards is challenging but necessary.
It requires a well-organized system and extensive collaboration with international partners.
Furthermore, the need for accurate and real-time data can be difficult to achieve without the right systems in place.
Purchasing departments must ensure that they have access to reliable data to avoid misinformation or gaps in the supply chain trail.
Future Trends in Supply Chain Traceability
As technology continues to evolve, the future of supply chain traceability looks increasingly promising.
Artificial intelligence and machine learning are expected to play a significant role in enhancing traceability.
These technologies can analyze large datasets more efficiently, helping companies predict and mitigate potential supply chain disruptions.
Furthermore, the adoption of blockchain technology is anticipated to grow.
Blockchain provides an immutable ledger of all transactions, which can greatly increase transparency and trust across the supply chain.
The demand for sustainability is also shaping traceability efforts.
Consumers and governments are pushing for environmentally friendly products and processes, compelling companies to provide more detailed information on their supply chain’s environmental impact.
Conclusion
Improving traceability throughout the supply chain is a critical focus for purchasing departments.
By leveraging advanced technology, fostering strong supplier relationships, and maintaining standardized processes, companies can significantly enhance their traceability practices.
While challenges exist, the benefits of improved product safety, regulatory compliance, and customer satisfaction make it a worthwhile endeavor.
As the landscape continues to evolve, staying informed about emerging trends and adapting accordingly will be vital for purchasing departments looking to lead in traceability.
資料ダウンロード
QCD調達購買管理クラウド「newji」は、調達購買部門で必要なQCD管理全てを備えた、現場特化型兼クラウド型の今世紀最高の購買管理システムとなります。
ユーザー登録
調達購買業務の効率化だけでなく、システムを導入することで、コスト削減や製品・資材のステータス可視化のほか、属人化していた購買情報の共有化による内部不正防止や統制にも役立ちます。
NEWJI DX
製造業に特化したデジタルトランスフォーメーション(DX)の実現を目指す請負開発型のコンサルティングサービスです。AI、iPaaS、および先端の技術を駆使して、製造プロセスの効率化、業務効率化、チームワーク強化、コスト削減、品質向上を実現します。このサービスは、製造業の課題を深く理解し、それに対する最適なデジタルソリューションを提供することで、企業が持続的な成長とイノベーションを達成できるようサポートします。
オンライン講座
製造業、主に購買・調達部門にお勤めの方々に向けた情報を配信しております。
新任の方やベテランの方、管理職を対象とした幅広いコンテンツをご用意しております。
お問い合わせ
コストダウンが利益に直結する術だと理解していても、なかなか前に進めることができない状況。そんな時は、newjiのコストダウン自動化機能で大きく利益貢献しよう!
(Β版非公開)