- お役立ち記事
- “Measures to prevent ordering errors”—management methods and checklists that should be thoroughly followed by the purchasing department
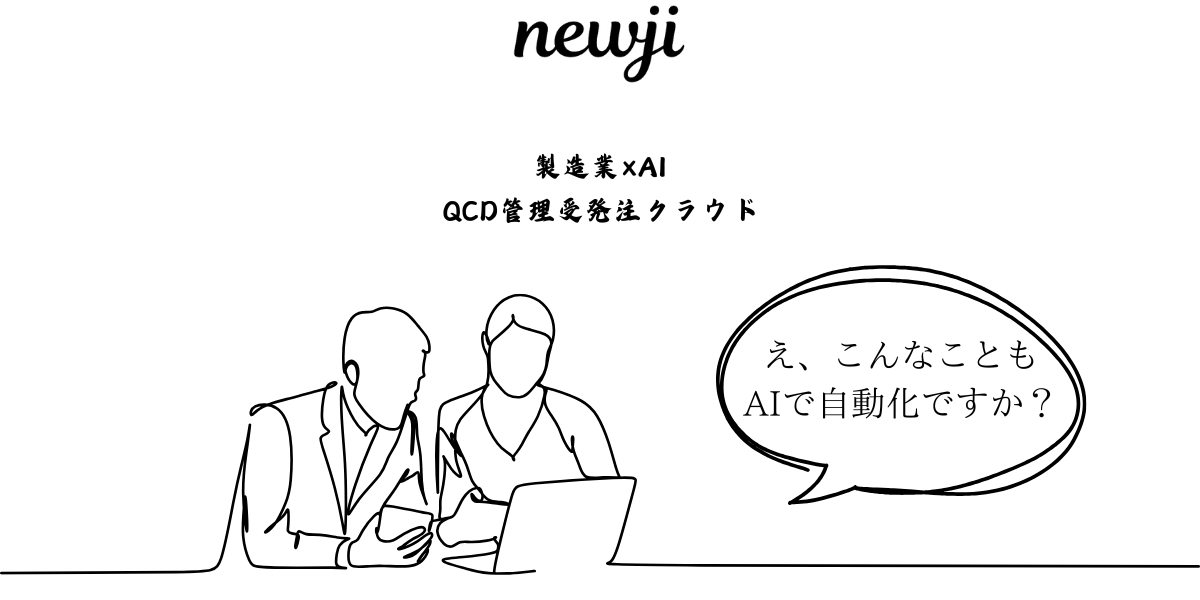
“Measures to prevent ordering errors”—management methods and checklists that should be thoroughly followed by the purchasing department
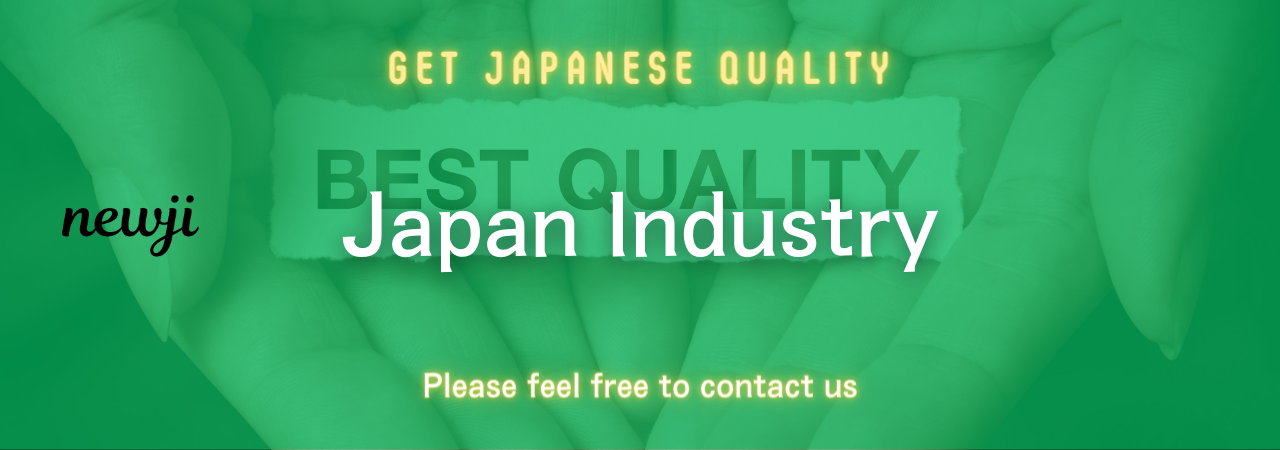
目次
Understanding Ordering Errors
Ordering errors in the purchasing department can lead to significant operational disruptions.
These errors can result in stock shortages or excess inventory, both of which can have financial implications for the business.
Such mistakes may occur due to human error, misunderstanding of supplier specifications, or miscommunication between departments.
To avoid these outcomes, it is essential to understand the nature of ordering errors and implement effective measures to prevent them.
Common Causes of Ordering Errors
There are several common causes for ordering errors, each of which presents unique challenges.
A common issue is poor communication, which can result from unclear or incomplete information being shared internally or with suppliers.
Mistakes can also arise from similar SKU numbers or product descriptions that confuse the purchasing staff.
Another factor is the failure to update inventory levels regularly, leading to misinformed procurement decisions.
Finally, pressure to meet tight deadlines can contribute to oversight and errors in the ordering process.
Management Methods to Prevent Errors
Implementing robust management methods is crucial to minimizing ordering errors.
A systematic approach ensures that purchasing departments align with organizational goals and standards.
Implementing Standard Operating Procedures (SOPs)
Standard Operating Procedures are detailed, written instructions that describe how to perform routine activities.
Having well-documented SOPs ensures that employees follow consistent steps when placing orders.
This reduces the likelihood of errors and establishes a clear protocol for addressing any issues that arise.
Regular training sessions are essential to ensure that all employees are up to date with these procedures.
Leveraging Technology and Automation
Technology can play a significant role in error reduction.
Utilizing procurement software can help automate routine tasks, such as order placement and invoice processing, reducing human error.
Inventory management systems connected with the ordering platform can provide real-time data on stock levels, ensuring that orders are accurate and timely.
Additionally, implementing automatic reorder points can prevent stockouts while avoiding excess inventory.
Supplier Communication and Relationship Management
Maintaining clear and open communication with suppliers is vital for preventing ordering errors.
Regular meetings with suppliers help to clarify product specifications and expectations.
Building strong relationships can also lead to better collaboration and the ability to resolve issues quickly.
It’s essential to have regular feedback and review sessions with suppliers to address any concerns regarding order accuracy.
Checklist for the Purchasing Department
A comprehensive checklist can serve as a vital tool for ensuring accuracy in the purchasing process.
This checklist should be tailored to the needs of the organization and address key areas vulnerable to errors.
Pre-Order Verification
Before placing an order, verify the current inventory levels to avoid unnecessary purchases.
Check supplier information, including pricing and product specifications, to ensure no discrepancies exist.
Review the order request with the requesting department to confirm that all details are correct and meet business needs.
Review and Approval Process
Implementing a multi-tiered review and approval process can reduce errors.
Before finalizing an order, have it reviewed by multiple stakeholders to ensure accuracy.
This process can include cross-checking details with inventory records and confirming supplier terms and conditions.
Post-Order Tracking and Evaluation
Once an order is placed, track its progress closely and communicate with the supplier to ensure timely delivery.
Upon receipt, evaluate the order to ensure that the delivered items match the order specifications.
Regularly analyze ordering errors and delivery discrepancies to identify patterns and areas for improvement.
Continuous Improvement and Training
To maintain a high level of accuracy and efficiency, continuous improvement and training programs are crucial.
Regular Audits and Assessments
Conduct regular audits of the purchasing process to identify any deviations from established procedures.
Assess the effectiveness of current methods and make necessary adjustments to optimize the process.
Use audits as opportunities to uncover recurring issues and develop strategies to mitigate them.
Ongoing Employee Training and Development
Investing in ongoing training ensures that employees remain informed about changes in purchasing processes and industry best practices.
Training programs should be designed to enhance employees’ skills and understanding of procurement software and tools.
Encourage a culture of learning, where employees are proactive in seeking out new information and improving their knowledge.
In conclusion, ordering errors can have significant impacts on an organization’s efficiency and profitability.
By understanding the common causes of these errors and implementing effective management methods and checklists, purchasing departments can significantly reduce mistakes.
Leveraging technology, maintaining clear supplier communication, performing regular audits, and investing in training will ensure that the ordering process is both accurate and efficient.
These practices not only enhance the purchasing function but also contribute to the overall success and competitiveness of the organization.
資料ダウンロード
QCD調達購買管理クラウド「newji」は、調達購買部門で必要なQCD管理全てを備えた、現場特化型兼クラウド型の今世紀最高の購買管理システムとなります。
ユーザー登録
調達購買業務の効率化だけでなく、システムを導入することで、コスト削減や製品・資材のステータス可視化のほか、属人化していた購買情報の共有化による内部不正防止や統制にも役立ちます。
NEWJI DX
製造業に特化したデジタルトランスフォーメーション(DX)の実現を目指す請負開発型のコンサルティングサービスです。AI、iPaaS、および先端の技術を駆使して、製造プロセスの効率化、業務効率化、チームワーク強化、コスト削減、品質向上を実現します。このサービスは、製造業の課題を深く理解し、それに対する最適なデジタルソリューションを提供することで、企業が持続的な成長とイノベーションを達成できるようサポートします。
オンライン講座
製造業、主に購買・調達部門にお勤めの方々に向けた情報を配信しております。
新任の方やベテランの方、管理職を対象とした幅広いコンテンツをご用意しております。
お問い合わせ
コストダウンが利益に直結する術だと理解していても、なかなか前に進めることができない状況。そんな時は、newjiのコストダウン自動化機能で大きく利益貢献しよう!
(Β版非公開)