- お役立ち記事
- Measures to reduce risk in purchasing departments by strengthening supplier management
月間76,176名の
製造業ご担当者様が閲覧しています*
*2025年3月31日現在のGoogle Analyticsのデータより
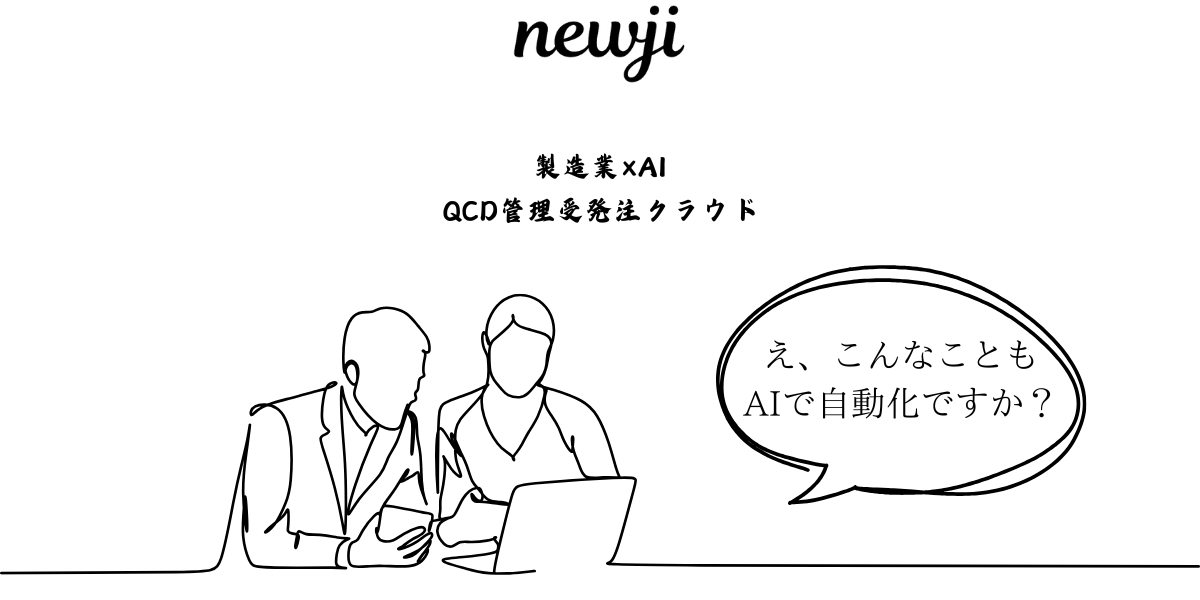
Measures to reduce risk in purchasing departments by strengthening supplier management
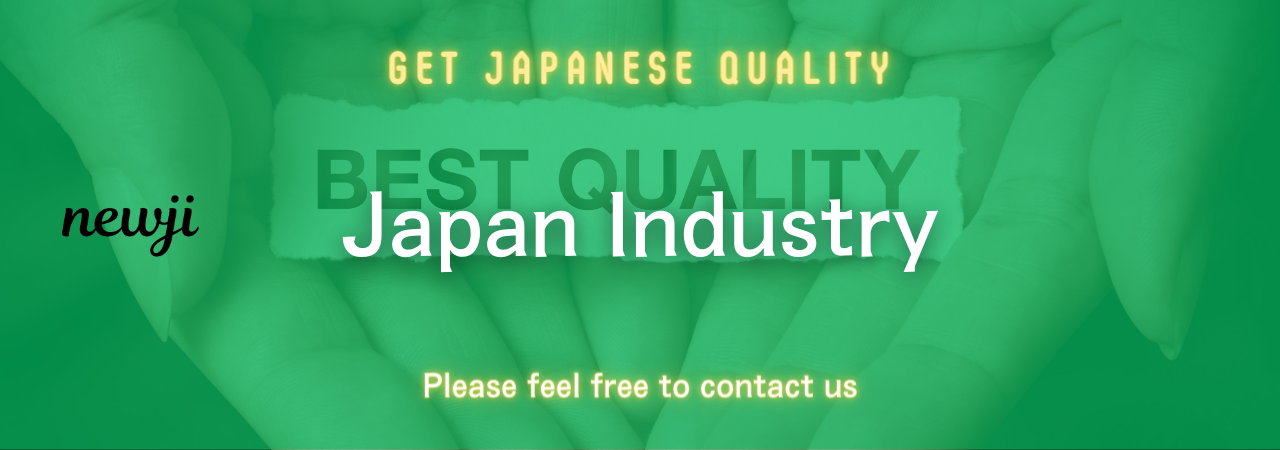
目次
Understanding the Importance of Supplier Management
The purchasing department plays a crucial role in the smooth operation of any company.
Its main responsibility is to procure the necessary goods and services that the company needs to function efficiently.
However, with this responsibility comes the risk of potential disruptions or issues with suppliers.
To mitigate these risks and ensure uninterrupted supply, it is essential to strengthen supplier management.
Supplier management is the process of evaluating and managing relationships with suppliers.
It involves selecting the right suppliers, monitoring their performance, and maintaining strong relationships with them.
Effective supplier management can help organizations reduce risks, improve quality, and achieve better cost efficiencies.
Identifying Potential Risks
In order to effectively manage suppliers, it’s important to first identify potential risks.
Risks in the supply chain can arise from various factors, including unreliable suppliers, quality issues, delivery delays, and financial instability.
Additionally, external factors such as political instability, natural disasters, or changes in regulations can also pose risks.
Once potential risks are identified, the purchasing department can take proactive measures to address them.
This involves conducting thorough risk assessments and creating strategies to minimize their impact.
Supplier Evaluation and Selection
One of the first steps in reducing risk is a rigorous evaluation and selection process for suppliers.
By carefully assessing each potential supplier, companies can ensure that they only work with those who meet their criteria for reliability and quality.
An effective evaluation process may include background checks, financial stability assessments, and reviews of previous performance.
Conducting site visits and audits can provide additional insights into a supplier’s operations.
Implementing Supplier Performance Metrics
To ensure ongoing quality and reliability, establishing clear performance metrics is essential.
These metrics should be agreed upon between the company and its suppliers from the outset.
Common performance metrics include delivery accuracy, quality of goods, and responsiveness to inquiries.
Regularly monitoring these metrics allows the purchasing department to identify and address any issues swiftly, before they escalate into bigger problems.
Building Strong Supplier Relationships
Strong relationships with suppliers are invaluable in minimizing risk.
Collaborative partnerships lead to better communication, increased trust, and a shared commitment to success.
Maintaining open lines of communication ensures that both parties are aligned in their objectives and expectations.
Regular meetings, feedback sessions, and joint problem-solving initiatives are effective ways to foster these relationships.
The Role of Technology in Supplier Management
In today’s digital age, technology plays a crucial role in supplier management.
From data analytics to automated systems, technology can significantly enhance risk management efforts.
Supplier Management Software
Supplier management software can streamline and automate various processes, such as supplier evaluations, performance tracking, and contract management.
These systems offer centralized platforms for storing supplier information and documents, making it easier to access and share relevant data.
Moreover, supplier management software can provide real-time updates and alerts, helping the purchasing department quickly respond to any emerging risks.
Data Analytics
Leveraging data analytics enables companies to gain deeper insights into supplier performance and risks.
By analyzing historical data and identifying patterns, companies can forecast potential supply chain disruptions.
Predictive analytics can also help in anticipating demand changes and adjusting procurement strategies accordingly.
Developing Contingency Plans
Despite the best efforts in supplier management, it is crucial to have contingency plans in place.
Contingency plans prepare companies for unexpected disruptions and ensure minimal impact on operations.
These plans often include identifying alternative suppliers, maintaining safety stock, and having a well-thought-out logistics strategy.
Regularly reviewing and updating contingency plans ensures that they remain effective and relevant.
Continuous Improvement and Training
Finally, continuous improvement and training within the purchasing department are vital to staying ahead of potential risks.
Encouraging employees to participate in training sessions and workshops can enhance their skills and knowledge.
By staying informed about industry trends and best practices, the purchasing department can adapt and improve their supplier management strategies.
This proactive approach not only reduces risk but also contributes to the overall success and growth of the company.
In conclusion, strengthening supplier management is key to reducing risks in purchasing departments.
Through careful supplier evaluation, performance monitoring, strong relationships, and the use of technology, companies can create a resilient supply chain.
Implementing these measures prepares businesses to handle challenges effectively and ensures they continue to thrive in an ever-changing global landscape.
資料ダウンロード
QCD管理受発注クラウド「newji」は、受発注部門で必要なQCD管理全てを備えた、現場特化型兼クラウド型の今世紀最高の受発注管理システムとなります。
ユーザー登録
受発注業務の効率化だけでなく、システムを導入することで、コスト削減や製品・資材のステータス可視化のほか、属人化していた受発注情報の共有化による内部不正防止や統制にも役立ちます。
NEWJI DX
製造業に特化したデジタルトランスフォーメーション(DX)の実現を目指す請負開発型のコンサルティングサービスです。AI、iPaaS、および先端の技術を駆使して、製造プロセスの効率化、業務効率化、チームワーク強化、コスト削減、品質向上を実現します。このサービスは、製造業の課題を深く理解し、それに対する最適なデジタルソリューションを提供することで、企業が持続的な成長とイノベーションを達成できるようサポートします。
製造業ニュース解説
製造業、主に購買・調達部門にお勤めの方々に向けた情報を配信しております。
新任の方やベテランの方、管理職を対象とした幅広いコンテンツをご用意しております。
お問い合わせ
コストダウンが利益に直結する術だと理解していても、なかなか前に進めることができない状況。そんな時は、newjiのコストダウン自動化機能で大きく利益貢献しよう!
(β版非公開)