- お役立ち記事
- Measures to strengthen traceability required for quality control in the purchasing process
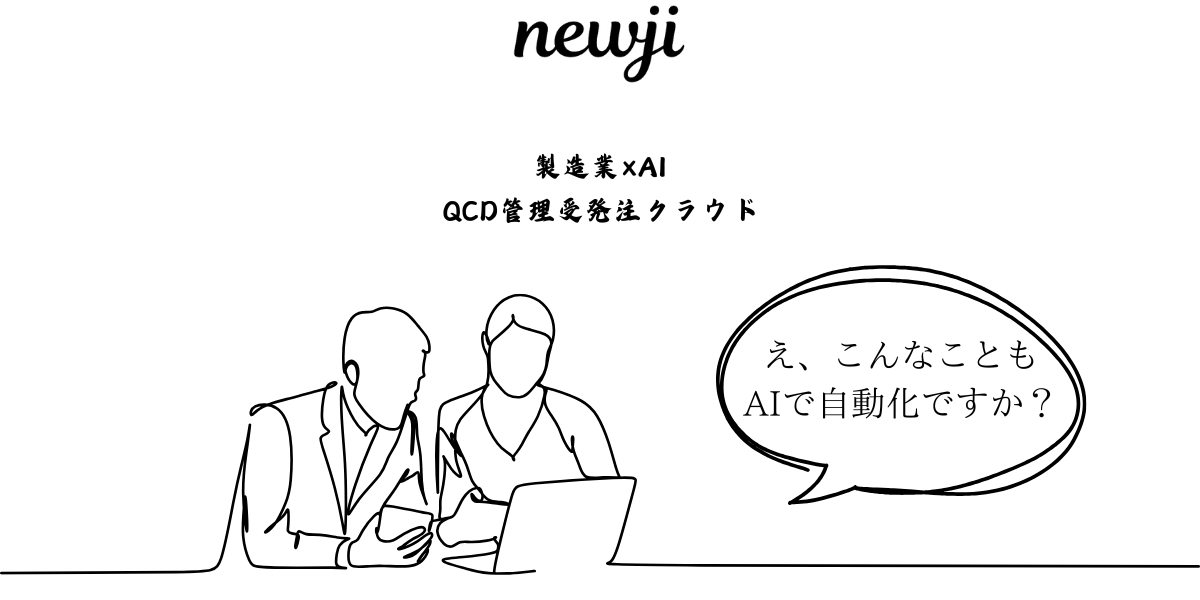
Measures to strengthen traceability required for quality control in the purchasing process
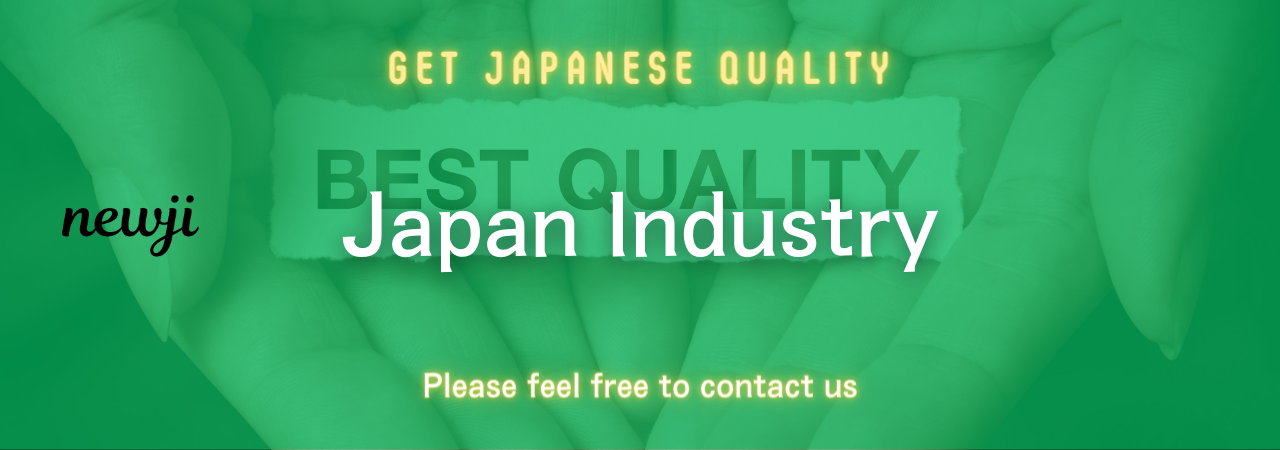
目次
Understanding Traceability in the Purchasing Process
Traceability is a critical component in the purchasing process, especially when it comes to maintaining quality control.
In simple terms, traceability refers to the ability to track the history, application, or location of an entity through recorded documentation.
In the context of procurement, this means having detailed records of every stage of the purchasing process—from the initial supplier selection to the final delivery of products.
A robust traceability system ensures that all products meet required quality standards and that any issues can be swiftly identified and addressed.
With markets and supply chains becoming increasingly complex, the need for effective traceability measures is more important than ever.
This transformation has been driven by a mix of regulatory demands, consumer expectations, and technological advancements.
Ensuring traceability not only enhances quality control but also helps in managing risks, optimizing processes, and building trust with consumers and business partners.
The Importance of Quality Control
Quality control is essential for businesses to ensure that their products meet specific quality standards consistently.
This process involves testing products to identify defects and taking necessary actions to correct them.
In the purchasing process, quality control ensures that the raw materials or components used are up to standard, thereby maintaining the integrity of the final product.
An effective quality control system can prevent costly recalls, reduce waste, and enhance customer satisfaction.
When traceability is integrated into quality control, it becomes easier to monitor and verify every aspect of the supply chain.
This integration allows businesses to swiftly respond to any issues, reducing downtime and ensuring consistent product quality.
Challenges in Implementing Traceability
Implementing traceability in the purchasing process is not without its challenges.
First and foremost, it requires a significant investment in systems and technology.
Businesses need to develop or adopt software that can track and manage all relevant data seamlessly.
Another challenge is ensuring that all supply chain partners are on board and compliant with traceability requirements.
This often involves standardizing processes and ensuring that suppliers are capable of providing required documentation and data.
Moreover, as supply chains become more global, ensuring consistent traceability across borders can be difficult.
Different countries have varying regulations, and businesses must navigate this complex web to ensure compliance.
Technological Solutions for Enhanced Traceability
The advancement of technology has provided businesses with numerous tools to enhance traceability.
Radio-frequency identification (RFID), blockchain, and Internet of Things (IoT) technologies are some examples of innovations being used to meet traceability needs.
RFID tags are used to provide real-time tracking of products throughout the supply chain.
These tags contain information about the product and can be scanned at various points to ensure accuracy and traceability.
Blockchain technology, known for its secure and transparent nature, offers a way to maintain an immutable record of all transactions and processes within the supply chain.
By decentralizing and securing data, blockchain helps ensure that all traceability information is accurate and tamper-proof.
IoT technology aids traceability by enabling devices and systems to communicate and exchange data automatically.
Sensors can provide real-time updates on the status and location of materials, improving the overall traceability process.
The Role of Regulations
Regulations play a vital role in driving the requirement for traceability within supply chains.
Governments and regulatory bodies globally have established strict guidelines to ensure product safety and to protect consumer rights.
These regulations often mandate traceability as a component of compliance, requiring businesses to demonstrate their ability to provide documented evidence of their purchasing and quality control processes.
For example, in the food industry, regulations like the Food Safety Modernization Act (FSMA) require businesses to have traceability plans in place to quickly manage any food safety issues.
Similarly, the pharmaceutical industry has regulations such as the Drug Supply Chain Security Act (DSCSA), which calls for a comprehensive system to track and trace prescription drugs.
Such regulations compel businesses to implement robust traceability systems to avoid penalties, recalls, and damage to brand reputation.
Benefits of Strengthened Traceability
Investing in robust traceability systems offers numerous benefits to businesses.
First, it increases transparency across the supply chain, which can significantly enhance trust with partners and customers.
Customers today are particularly interested in knowing the origin of products and whether they have been ethically sourced.
Traceability also aids in effective risk management by enabling businesses to quickly identify and address any issues within the supply chain.
This ability to swiftly recall or halt distribution in event of a failure minimizes potential losses and protects the brand’s reputation.
Furthermore, traceability promotes efficiency by optimizing inventory management and reducing waste, leading to cost savings for businesses.
How to Strengthen Traceability
To strengthen traceability, businesses should start by conducting a comprehensive analysis of their current processes to identify potential gaps.
This process involves mapping out the entire supply chain, from supplier to end customer, to understand where improvements can be made.
Investing in advanced technologies like RFID, blockchain, and IoT will enhance the ability to track products accurately throughout the supply chain.
Additionally, businesses should work towards compliance with industry regulations to ensure they are maintaining the required standards.
Collaboration with suppliers is crucial, as their cooperation is necessary to implement effective traceability.
Clear communication and agreed-upon standards can help ensure all parties are on the same page.
Finally, training employees to handle traceability tools and processes efficiently ensures the system runs smoothly and errors are minimized.
In conclusion, while implementing traceability measures in the purchasing process presents certain challenges, the benefits far outweigh the difficulties.
A robust traceability system is key to enhancing quality control, optimizing supply chain processes, and building consumer trust.
As the market landscape continues to evolve, having these measures in place will position businesses well for future success.
資料ダウンロード
QCD調達購買管理クラウド「newji」は、調達購買部門で必要なQCD管理全てを備えた、現場特化型兼クラウド型の今世紀最高の購買管理システムとなります。
ユーザー登録
調達購買業務の効率化だけでなく、システムを導入することで、コスト削減や製品・資材のステータス可視化のほか、属人化していた購買情報の共有化による内部不正防止や統制にも役立ちます。
NEWJI DX
製造業に特化したデジタルトランスフォーメーション(DX)の実現を目指す請負開発型のコンサルティングサービスです。AI、iPaaS、および先端の技術を駆使して、製造プロセスの効率化、業務効率化、チームワーク強化、コスト削減、品質向上を実現します。このサービスは、製造業の課題を深く理解し、それに対する最適なデジタルソリューションを提供することで、企業が持続的な成長とイノベーションを達成できるようサポートします。
オンライン講座
製造業、主に購買・調達部門にお勤めの方々に向けた情報を配信しております。
新任の方やベテランの方、管理職を対象とした幅広いコンテンツをご用意しております。
お問い合わせ
コストダウンが利益に直結する術だと理解していても、なかなか前に進めることができない状況。そんな時は、newjiのコストダウン自動化機能で大きく利益貢献しよう!
(Β版非公開)