- お役立ち記事
- Measuring the Effectiveness of QFD in Manufacturing: Maximizing Outcomes
Measuring the Effectiveness of QFD in Manufacturing: Maximizing Outcomes
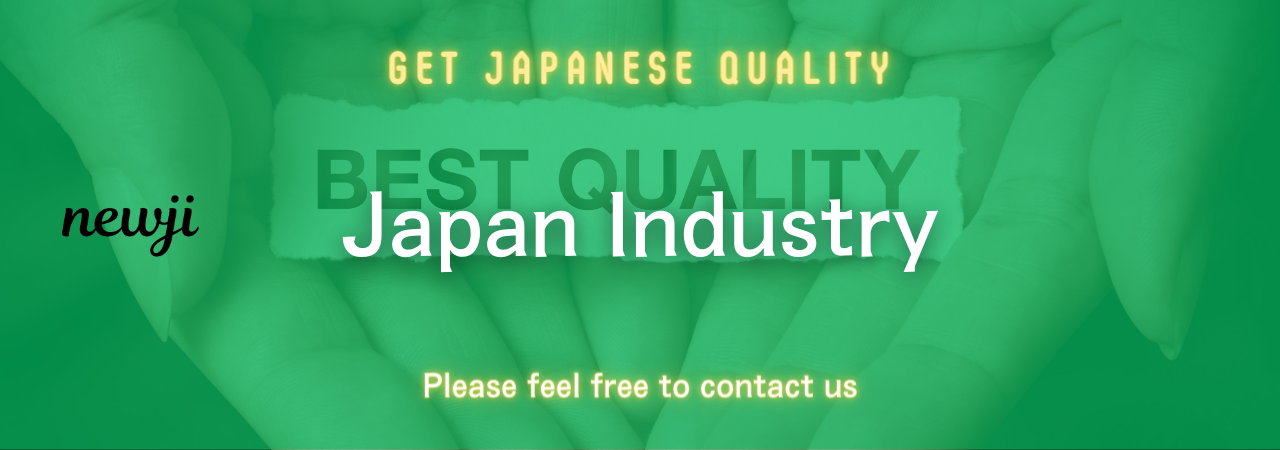
In the competitive world of manufacturing, companies constantly strive to improve their processes and outcomes.
One powerful tool that has gained widespread use is Quality Function Deployment (QFD).
Measuring the effectiveness of QFD in manufacturing is essential to maximizing outcomes and ensuring continuous improvement.
目次
Understanding Quality Function Deployment (QFD)
QFD is a structured method used to translate customer needs into specific technical requirements.
It involves four primary phases: product planning, product design, process planning, and process control.
The concept originated in Japan and has since become a standard in many industries worldwide.
Product Planning
The first phase of QFD involves identifying customer needs and preferences.
This information is gathered through surveys, focus groups, and market research.
The collected data is then used to create a “House of Quality,” a matrix that correlates customer demands with product features.
Product Design
In the second phase, the focus shifts to detailed design specifications.
Engineers and designers use the House of Quality to develop technical requirements that meet customer needs.
This phase ensures that the final product not only meets customer expectations but also aligns with the company’s capabilities.
Process Planning
The third phase is all about planning the processes needed to manufacture the product.
This involves selecting the best methods, materials, and technologies.
Process planning ensures that production is efficient, cost-effective, and able to meet quality standards.
Process Control
The final phase of QFD is process control.
This involves monitoring and controlling production processes to maintain quality and consistency.
Continuous feedback and adjustments are necessary to ensure that the final product meets the established requirements.
Measuring Effectiveness
To determine the effectiveness of QFD in manufacturing, it is crucial to establish measurable criteria.
Some of the key performance indicators (KPIs) include customer satisfaction, product quality, and production efficiency.
Customer Satisfaction
One of the primary goals of QFD is to enhance customer satisfaction.
By translating customer needs into technical requirements, companies can produce products that better meet market demands.
Surveys, reviews, and feedback are essential tools for measuring customer satisfaction.
Product Quality
Quality is a critical aspect of any manufacturing process.
QFD aims to improve product quality by ensuring that technical requirements align with customer needs.
Quality metrics, such as defect rates, return rates, and compliance with standards, can be used to measure the effectiveness of QFD.
Production Efficiency
QFD also aims to enhance production efficiency by optimizing processes and resources.
Efficiency can be measured through production times, resource utilization, and cost savings.
A more efficient production process not only reduces costs but also improves overall output.
Case Studies
Examining real-world examples can provide valuable insights into the effectiveness of QFD in manufacturing.
Automotive Industry
The automotive industry has widely adopted QFD to improve product development cycles.
For instance, a leading car manufacturer used QFD to redesign its braking system based on customer feedback.
The result was not only enhanced safety features but also increased customer satisfaction and reduced production costs.
Consumer Electronics
In the consumer electronics sector, a global company implemented QFD to address customer complaints about battery life.
By focusing on customer needs, the company developed a new battery system that extended usage time.
This improvement led to higher customer satisfaction and a significant increase in sales.
Challenges and Limitations
While QFD offers numerous benefits, it is not without challenges.
One of the main limitations is the extensive time and resources required for implementation.
QFD demands a high level of collaboration among various departments, which can be difficult to achieve.
Resource Intensive
The process of gathering and analyzing customer data, creating the House of Quality, and developing technical specifications can be resource-intensive.
Companies need to allocate sufficient time and budget to ensure successful implementation.
Complexity
QFD is a complex process that requires a deep understanding of both customer needs and technical requirements.
Miscommunication or errors during any phase can lead to suboptimal results.
Proper training and collaboration are essential to mitigate this risk.
Best Practices for Maximizing Outcomes
To maximize the effectiveness of QFD in manufacturing, companies should follow some best practices.
Customer-Centric Approach
A customer-centric approach is vital for the success of QFD.
Companies should prioritize understanding customer needs and preferences through regular surveys and feedback mechanisms.
This information should be the foundation for all subsequent QFD phases.
Cross-Functional Collaboration
Effective QFD implementation requires collaboration across various departments, including marketing, engineering, and production.
Establishing cross-functional teams can enhance communication and ensure that all aspects of the product development process are aligned with customer needs.
Continuous Improvement
Continuous improvement is a key principle of QFD.
Companies should regularly review and update their QFD processes based on feedback and performance metrics.
This ensures that the products consistently meet or exceed customer expectations.
Quality Function Deployment (QFD) is a powerful tool for enhancing customer satisfaction, product quality, and production efficiency in the manufacturing sector.
By understanding its phases, measuring its effectiveness, and addressing its challenges, companies can optimize their outcomes.
Through a customer-centric approach, cross-functional collaboration, and a commitment to continuous improvement, manufacturers can leverage QFD to achieve long-term success.
資料ダウンロード
QCD調達購買管理クラウド「newji」は、調達購買部門で必要なQCD管理全てを備えた、現場特化型兼クラウド型の今世紀最高の購買管理システムとなります。
ユーザー登録
調達購買業務の効率化だけでなく、システムを導入することで、コスト削減や製品・資材のステータス可視化のほか、属人化していた購買情報の共有化による内部不正防止や統制にも役立ちます。
NEWJI DX
製造業に特化したデジタルトランスフォーメーション(DX)の実現を目指す請負開発型のコンサルティングサービスです。AI、iPaaS、および先端の技術を駆使して、製造プロセスの効率化、業務効率化、チームワーク強化、コスト削減、品質向上を実現します。このサービスは、製造業の課題を深く理解し、それに対する最適なデジタルソリューションを提供することで、企業が持続的な成長とイノベーションを達成できるようサポートします。
オンライン講座
製造業、主に購買・調達部門にお勤めの方々に向けた情報を配信しております。
新任の方やベテランの方、管理職を対象とした幅広いコンテンツをご用意しております。
お問い合わせ
コストダウンが利益に直結する術だと理解していても、なかなか前に進めることができない状況。そんな時は、newjiのコストダウン自動化機能で大きく利益貢献しよう!
(Β版非公開)