- お役立ち記事
- Mechanism of defective solder joints and countermeasure techniques
月間77,185名の
製造業ご担当者様が閲覧しています*
*2025年2月28日現在のGoogle Analyticsのデータより
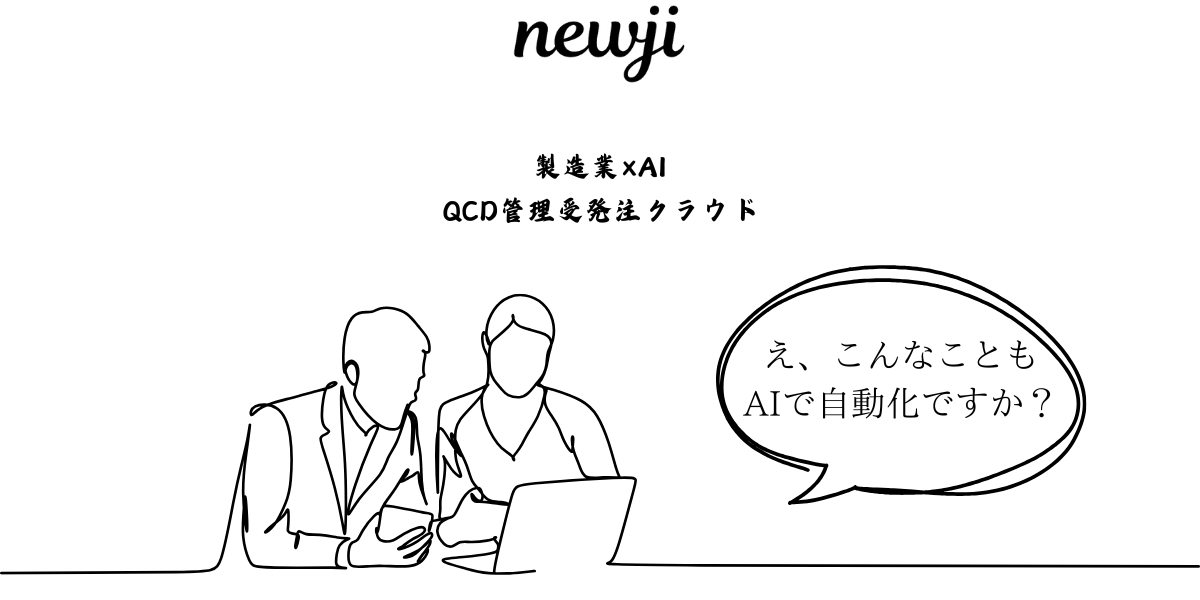
Mechanism of defective solder joints and countermeasure techniques
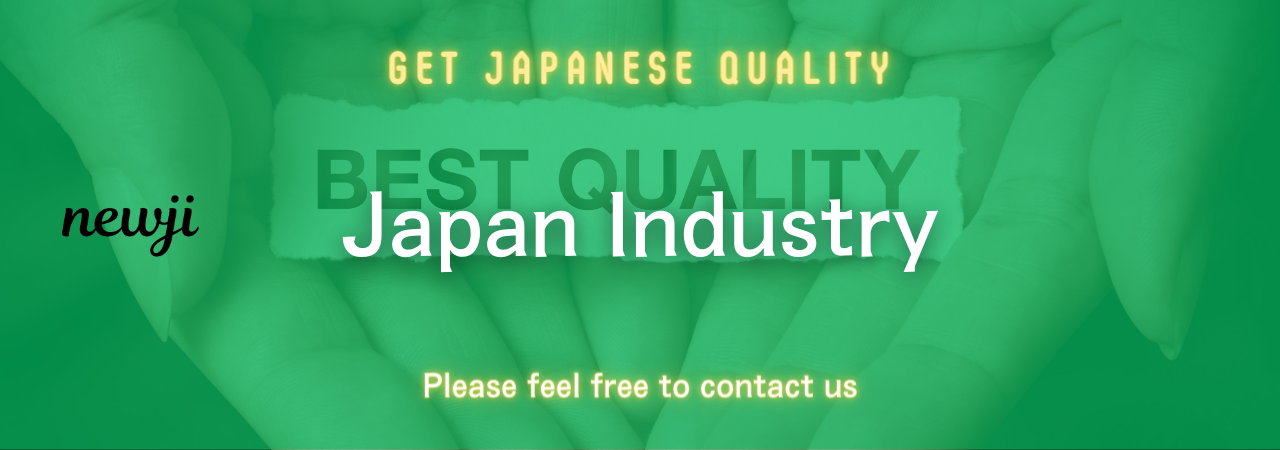
目次
Understanding Defective Solder Joints
Solder joints play a crucial role in the reliability and performance of electronic devices, as they ensure that components are effectively connected to the circuit board.
However, defects in solder joints can lead to various issues, such as poor electrical connections, mechanical failures, or complete device breakdowns.
This article explores the mechanisms that lead to defective solder joints and discusses techniques to counteract these problems.
Common Causes of Defective Solder Joints
The formation of a defective solder joint can result from several factors.
One common cause is improper solder composition or choice of materials.
Solders are typically made of a combination of metals, such as tin and lead or their lead-free alternatives, with specific properties that make them suitable for creating effective joints.
If the metallurgical composition is not optimal, it can lead to joints with insufficient strength or conductivity.
Another cause is inadequate soldering temperature control.
Soldering at too low a temperature can prevent a good bond from forming between the metals, while excessively high temperatures can damage components and the circuit board itself.
Both scenarios compromise the integrity of the solder joint.
Poor application technique also contributes to defective joints.
Manual errors during soldering, such as applying too little or too much solder, can create weak connections.
In automated settings, misalignments or improper calibration of machinery can result in inconsistent soldering.
Contamination of the soldering environment is another significant factor.
Dirt, oil, or other residues present on component surfaces or within the solder can hinder proper adhesion and create defects.
Effects of Defective Solder Joints
Defective solder joints can have serious consequences on electronic devices.
One of the most immediate effects is the loss of electrical connectivity.
A poor solder joint may create an open circuit, causing intermittent failures or complete loss of functionality in the device.
Structurally weak solder joints are susceptible to mechanical stresses, such as vibrations or thermal cycling, leading to fatigue and eventual failure.
This is particularly problematic in applications that involve movement or repetitive thermal changes, such as automotive or aerospace electronics.
Another long-term effect is the potential for solder joint corrosion.
Corrosive environments or chemical reactions with flux residues can weaken the joints further, reducing the overall lifespan of the device.
Techniques to Prevent Defective Solder Joints
Preventing defective solder joints requires a combination of proper materials selection, precise process control, and careful attention to the soldering environment.
Optimizing Solder Material
Choosing the right solder material is vital to preventing defects.
For most applications, lead-free solders containing tin, silver, and copper are preferred due to their environmental benefits and robust properties.
It is crucial to select a solder alloy that suits the specific thermal management and mechanical requirements of the device.
Conduct regular assessments of solder joint quality using techniques like X-ray inspection or cross-section analysis.
These methods offer insights into potential defects and allow for early interventions.
Maintaining Optimal Temperature Control
Ensure that soldering processes are performed at the manufacturer’s recommended temperatures.
Implement automated systems where feasible to maintain consistent heating profiles.
Use thermal profiling tools to monitor temperatures during the soldering process, identifying any deviations that could lead to defects.
Enhancing Application Techniques
Ensure that solder is applied evenly and in the right quantity through proper training of personnel involved in manual soldering.
For automated applications, regular calibration and maintenance of equipment are necessary.
Utilize automated soldering machines with precision control to reduce human error and enhance consistency.
Controlling the Soldering Environment
Keep the soldering area clean and free of contaminants.
Implement measures to control dust and humidity, which can affect solder joint quality.
Using flux with appropriate properties can help improve adhesion and reduce the chances of forming defective joints.
Implementing Quality Assurance
Conduct regular assessments of solder joint quality using techniques like X-ray inspection or cross-section analysis.
These methods offer insights into potential defects and allow for early interventions.
Develop a robust quality assurance system that includes testing and feedback mechanisms to continually improve soldering processes.
Conclusion
Understanding the mechanisms behind defective solder joints and implementing effective countermeasures is essential for ensuring the reliability and performance of electronic devices.
By focusing on optimizing solder materials, controlling the soldering process, enhancing application techniques, and maintaining a clean environment, manufacturers can significantly reduce the incidence of defective solder joints.
These steps are critical to extending the lifespan and performance of electronic products, ultimately leading to greater customer satisfaction and success in the market.
資料ダウンロード
QCD管理受発注クラウド「newji」は、受発注部門で必要なQCD管理全てを備えた、現場特化型兼クラウド型の今世紀最高の受発注管理システムとなります。
ユーザー登録
受発注業務の効率化だけでなく、システムを導入することで、コスト削減や製品・資材のステータス可視化のほか、属人化していた受発注情報の共有化による内部不正防止や統制にも役立ちます。
NEWJI DX
製造業に特化したデジタルトランスフォーメーション(DX)の実現を目指す請負開発型のコンサルティングサービスです。AI、iPaaS、および先端の技術を駆使して、製造プロセスの効率化、業務効率化、チームワーク強化、コスト削減、品質向上を実現します。このサービスは、製造業の課題を深く理解し、それに対する最適なデジタルソリューションを提供することで、企業が持続的な成長とイノベーションを達成できるようサポートします。
製造業ニュース解説
製造業、主に購買・調達部門にお勤めの方々に向けた情報を配信しております。
新任の方やベテランの方、管理職を対象とした幅広いコンテンツをご用意しております。
お問い合わせ
コストダウンが利益に直結する術だと理解していても、なかなか前に進めることができない状況。そんな時は、newjiのコストダウン自動化機能で大きく利益貢献しよう!
(β版非公開)