- お役立ち記事
- Mechanism of fatigue failure
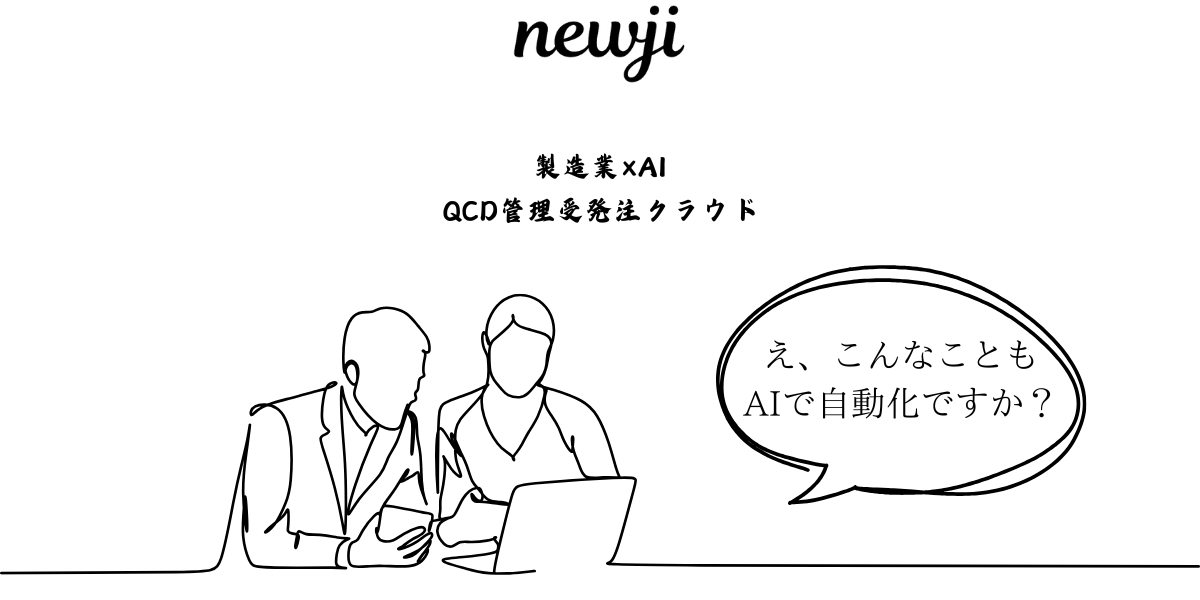
Mechanism of fatigue failure
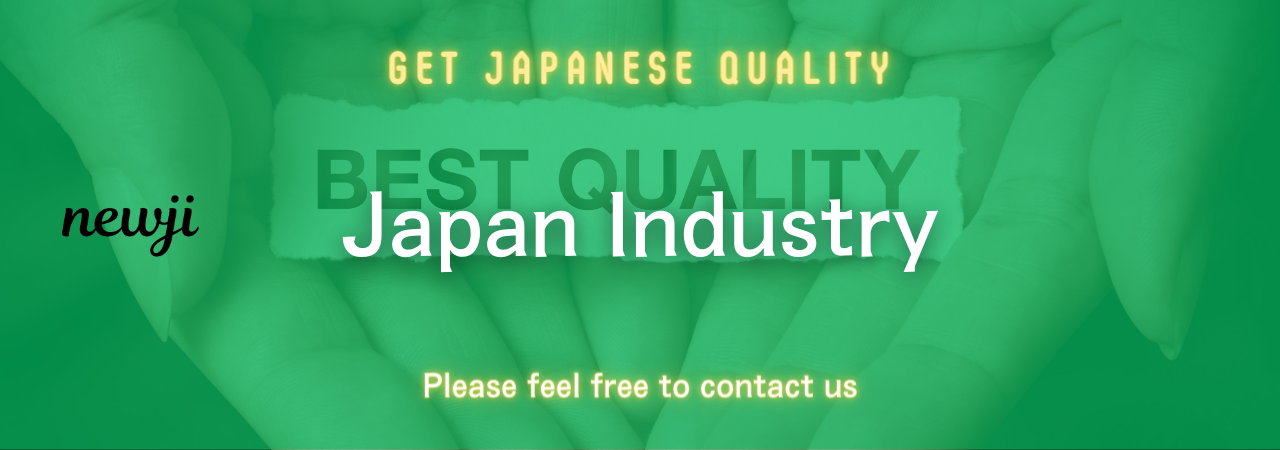
Understanding Fatigue Failure
Fatigue failure is a critical concept in engineering, where materials fail after repeated stress, even if these forces are below the maximum strength of the material.
This phenomenon can lead to unexpected breakdowns in machines, structures, and components, posing risks and causing economic losses.
Understanding the mechanism of fatigue failure is important for designing durable materials and components that can withstand repetitive loads over time.
What is Fatigue Failure?
Fatigue failure occurs when a material is subjected to cyclic stress over time, leading to the initiation and growth of cracks.
These repeated stresses cause microstructural changes, accumulating damage until the material ultimately fails.
The failure occurs even though the applied stress may be lower than the material’s tensile strength.
Fatigue failure can happen in various types of materials, such as metals, polymers, and composites.
It is often categorized by three stages: crack initiation, crack propagation, and final fracture.
In engineering, understanding these stages helps in predicting the lifespan of components and preventing failure.
Stages of Fatigue Failure
Understanding the stages of fatigue failure is essential for recognizing how materials ultimately break down.
1. Crack Initiation
Crack initiation is the first stage of fatigue failure.
It is characterized by the formation of small cracks, usually at points of stress concentration, such as notches, scratches, or surface defects.
Repeating stress cycles cause microscopic dislocations, leading to the concentration of stress in these areas.
The initial cracks are typically very small and may not be visible to the naked eye.
However, with continued cyclic stress, these cracks begin to grow and multiply, setting the stage for further material degradation.
2. Crack Propagation
In this stage, the previously formed micro-cracks start to grow through the material.
Crack propagation is characterized by incremental growth of the crack with each stress cycle.
This stage is often the longest part of the fatigue life, as the crack spreads slowly through the material.
The rate of crack propagation can be influenced by various factors, including the material properties, the magnitude of stress, the frequency of the load cycles, and environmental conditions.
Engineers often use tools like fracture mechanics to predict the growth rate and remaining life of a component.
3. Final Fracture
The final stage of fatigue failure is fracture, where the material can no longer sustain the load and suddenly breaks.
Once the crack reaches a critical size, it propagates rapidly until catastrophic failure occurs.
This stage happens quickly, often resulting in a sudden and complete break of the material.
Final fracture is generally characterized by a brittle or ductile fracture surface, depending on the material and other conditions.
At this point, the material has exhausted its ability to withstand repeated stresses, leading to its complete failure.
Factors Affecting Fatigue Failure
Several factors can influence the likelihood and severity of fatigue failure.
Recognizing these factors can help in designing more robust systems.
1. Material Properties
Different materials have different resistance levels to fatigue.
Metals like steel and titanium are generally more resistant to fatigue than polymers.
Material properties such as hardness, grain size, and alloy composition can also impact fatigue strength.
Choosing the right material for the application, considering its fatigue properties, is crucial in reducing the risk of failure.
2. Surface Conditions
Surface imperfections such as scratches, notches, and roughness can act as stress concentrators, increasing the chance of crack initiation.
Improving surface quality through processes like polishing or coating can help reduce fatigue failure risk.
Ensuring a smooth, defect-free surface reduces stress concentration and helps prolong the material’s life under cyclic loading.
3. Environmental Conditions
Environmental factors such as temperature, humidity, and corrosive elements can accelerate fatigue failure.
For example, exposure to corrosive environments can lead to pitting corrosion, reducing material strength and increasing fatigue susceptibility.
Designing for specific environments can help mitigate the effects of environmental stressors on materials.
4. Type and Frequency of Loading
The type of loading, including its magnitude, frequency, and nature (e.g., tensile, compressive, or torsional), also influences fatigue failure.
Higher loads and more frequent cycles accelerate damage accumulation, shortening fatigue life.
Understanding the loading conditions a material will face is critical for accurate fatigue life prediction.
Preventing Fatigue Failure
Preventing fatigue failure involves understanding its mechanism and influencing factors, then applying practical design and maintenance strategies.
1. Design Modifications
Incorporating features to distribute stress evenly can reduce stress concentrations and delay crack initiation.
Using fillets instead of sharp corners, avoiding abrupt changes in cross-section, and incorporating redundant load paths are common design strategies.
Engineers also use computational methods, such as finite element analysis, to identify and mitigate potential fatigue hot spots in designs.
2. Material Selection
Choosing materials with high fatigue resistance and appropriate mechanical properties for the specific application can greatly reduce failure risk.
Using coatings or surface treatments can also enhance fatigue resistance by improving surface quality and protecting against environmental factors.
Materials with better crack growth resistance can extend the fatigue life significantly.
3. Regular Inspection and Maintenance
Routine inspections can help detect early signs of fatigue damage, allowing for repairs before catastrophic failure occurs.
Non-destructive testing methods, like ultrasonic testing or magnetic particle inspection, are common techniques for identifying hidden cracks.
Timely maintenance, including surface repairs and component replacements, keeps structures and machines operating safely.
By understanding fatigue failure and implementing strategies to manage it, engineers and manufacturers can design more durable, reliable, and safe products and structures.
Regular monitoring and proactive measures ensure systems perform well, minimizing the risks associated with fatigue failure.
資料ダウンロード
QCD調達購買管理クラウド「newji」は、調達購買部門で必要なQCD管理全てを備えた、現場特化型兼クラウド型の今世紀最高の購買管理システムとなります。
ユーザー登録
調達購買業務の効率化だけでなく、システムを導入することで、コスト削減や製品・資材のステータス可視化のほか、属人化していた購買情報の共有化による内部不正防止や統制にも役立ちます。
NEWJI DX
製造業に特化したデジタルトランスフォーメーション(DX)の実現を目指す請負開発型のコンサルティングサービスです。AI、iPaaS、および先端の技術を駆使して、製造プロセスの効率化、業務効率化、チームワーク強化、コスト削減、品質向上を実現します。このサービスは、製造業の課題を深く理解し、それに対する最適なデジタルソリューションを提供することで、企業が持続的な成長とイノベーションを達成できるようサポートします。
オンライン講座
製造業、主に購買・調達部門にお勤めの方々に向けた情報を配信しております。
新任の方やベテランの方、管理職を対象とした幅広いコンテンツをご用意しております。
お問い合わせ
コストダウンが利益に直結する術だと理解していても、なかなか前に進めることができない状況。そんな時は、newjiのコストダウン自動化機能で大きく利益貢献しよう!
(Β版非公開)