- お役立ち記事
- Mechanism of fine particle dispersion, optimal selection of dispersants and dispersion machines, key points for use, and troubleshooting
月間76,176名の
製造業ご担当者様が閲覧しています*
*2025年3月31日現在のGoogle Analyticsのデータより
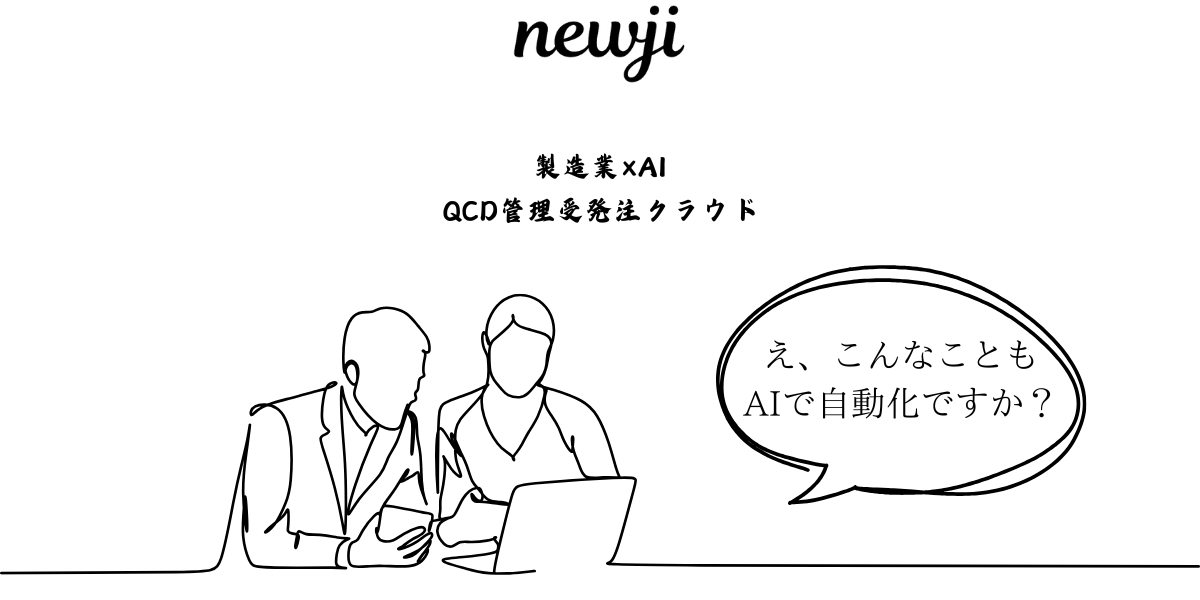
Mechanism of fine particle dispersion, optimal selection of dispersants and dispersion machines, key points for use, and troubleshooting
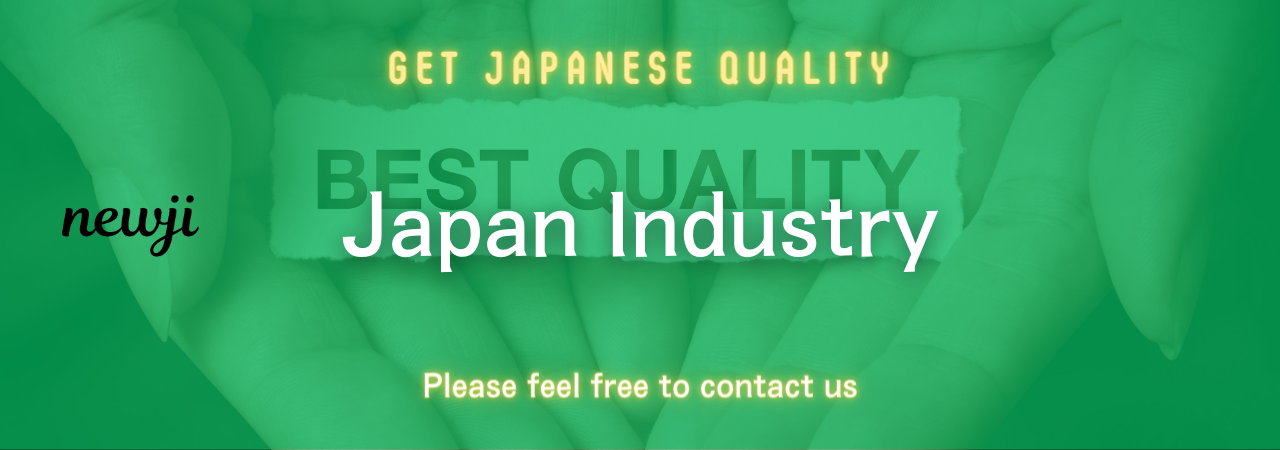
目次
Understanding Fine Particle Dispersion
Fine particle dispersion is a crucial process in various industries, including pharmaceuticals, paints, food, and cosmetics.
Essentially, it involves distributing tiny particles uniformly throughout a medium or matrix.
The success of the dispersion process impacts the final product’s quality, performance, and stability.
To understand the mechanism of fine particle dispersion, we need to delve into the basics of particle interactions and the role of dispersants.
The Role of Van der Waals Forces
At the heart of fine particle dispersion are various forces that dictate particle behavior.
Van der Waals forces are attractive forces between particles that can cause them to clump together, forming aggregates.
These forces need to be counteracted to achieve proper dispersion.
Using dispersants can effectively minimize these forces, promoting better particle separation.
Electrostatic and Steric Stabilization
Dispersants work through electrostatic and steric stabilization.
Electrostatic stabilization involves adding charged particles to the dispersion medium, creating repulsive forces that prevent particles from coming too close.
This is common in systems where water or another polar medium is used.
Steric stabilization, on the other hand, relies on using polymers and surfactants to create a physical barrier around particles.
This barrier prevents them from aggregating, regardless of the medium used.
Selecting the Right Dispersants
Selecting the appropriate dispersant is vital for effective fine particle dispersion.
The choice of dispersant depends on the nature of the particles and the dispersion medium.
Compatibility with the Medium
The first consideration is the compatibility of the dispersant with the medium.
Dispersants must be soluble in the medium to function correctly.
In aqueous systems, water-soluble dispersants are ideal, while non-aqueous systems require dispersants that dissolve in organic solvents.
Particle Surface Chemistry
Another key factor is the particle surface chemistry.
Different particles possess varying surface charges, affecting their interaction with dispersants.
Selecting a dispersant that complements the particle’s surface characteristics can enhance the dispersion process.
Molecular Weight and Concentration
The molecular weight and concentration of the dispersant also play a significant role.
Higher molecular weight polymers may offer better steric stabilization due to longer polymer chains.
However, the concentration must be carefully controlled, as too much or too little dispersant can lead to poor dispersion.
Choosing the Right Dispersion Machines
Alongside selecting the right dispersant, choosing the appropriate dispersion machinery is critical for optimizing fine particle dispersion.
High-Shear Mixers
High-shear mixers are widely used in industries where a rapid and effective dispersion is required.
These machines use a rotating impeller to create intense shear forces, breaking down agglomerates and dispersing the particles evenly.
They are particularly useful for dispersing pigments in paints and inks.
Ultrasonic Homogenizers
Ultrasonic homogenizers use ultrasonic waves to achieve particle dispersion.
These machines produce high-frequency sound waves that create microscopic bubbles in the medium.
When these bubbles collapse, they generate shock waves that disperse the particles.
This method is beneficial for delicate materials that may degrade under high-shear conditions.
Ball Mills
Ball mills are traditional dispersion machines that use grinding media to break down particles.
While less common in modern industry due to their slower processing times, they are still employed for certain applications where other methods may not be suitable.
Key Points for Effective Use
Achieving optimal dispersion requires careful attention to several key points in the process.
Control of Process Parameters
Monitoring and controlling process parameters such as temperature, mixing speed, and time is crucial.
Each parameter can significantly impact the dispersion process and, ultimately, the final product quality.
Stepwise Addition of Dispersants
Adding dispersants gradually can help better control the dispersion process.
Adding them in stages rather than all at once allows for more thorough mixing and better interaction with particles.
Regular Equipment Maintenance
Regular maintenance of dispersion machinery ensures that it operates at peak efficiency.
Worn-out parts or equipment failure can lead to inadequate dispersion, affecting product quality.
Troubleshooting Common Issues
Even with the right dispersants and machines, issues can arise.
Understanding common problems and how to address them is essential for maintaining high-quality dispersion.
Poor Dispersion Quality
If the dispersion quality is subpar, it could be due to insufficient shear forces or improper dispersant selection.
Adjusting process parameters and evaluating the dispersant choice might resolve the issue.
Flocculation of Particles
Flocculation, where dispersed particles re-agglomerate, can be troublesome.
It might be caused by insufficient dispersant concentration or improper pH levels in aqueous systems.
Increasing dispersant or adjusting pH can help maintain stable dispersion.
Equipment Malfunction
Equipment malfunctions can disrupt the dispersion process.
Regularly inspecting machinery and promptly addressing any mechanical issues are critical steps to prevent downtime and maintain productivity.
By understanding the mechanisms of fine particle dispersion, selecting appropriate dispersants and dispersion machines, and implementing key usage points and troubleshooting strategies, industries can achieve high-quality products and processes.
Ultimately, mastering the art and science of fine particle dispersion can significantly enhance product performance, stability, and customer satisfaction.
資料ダウンロード
QCD管理受発注クラウド「newji」は、受発注部門で必要なQCD管理全てを備えた、現場特化型兼クラウド型の今世紀最高の受発注管理システムとなります。
ユーザー登録
受発注業務の効率化だけでなく、システムを導入することで、コスト削減や製品・資材のステータス可視化のほか、属人化していた受発注情報の共有化による内部不正防止や統制にも役立ちます。
NEWJI DX
製造業に特化したデジタルトランスフォーメーション(DX)の実現を目指す請負開発型のコンサルティングサービスです。AI、iPaaS、および先端の技術を駆使して、製造プロセスの効率化、業務効率化、チームワーク強化、コスト削減、品質向上を実現します。このサービスは、製造業の課題を深く理解し、それに対する最適なデジタルソリューションを提供することで、企業が持続的な成長とイノベーションを達成できるようサポートします。
製造業ニュース解説
製造業、主に購買・調達部門にお勤めの方々に向けた情報を配信しております。
新任の方やベテランの方、管理職を対象とした幅広いコンテンツをご用意しております。
お問い合わせ
コストダウンが利益に直結する術だと理解していても、なかなか前に進めることができない状況。そんな時は、newjiのコストダウン自動化機能で大きく利益貢献しよう!
(β版非公開)