- お役立ち記事
- Mechanism of human error (mistake) and prevention measures, and quality improvement measures using the poka-yoke system
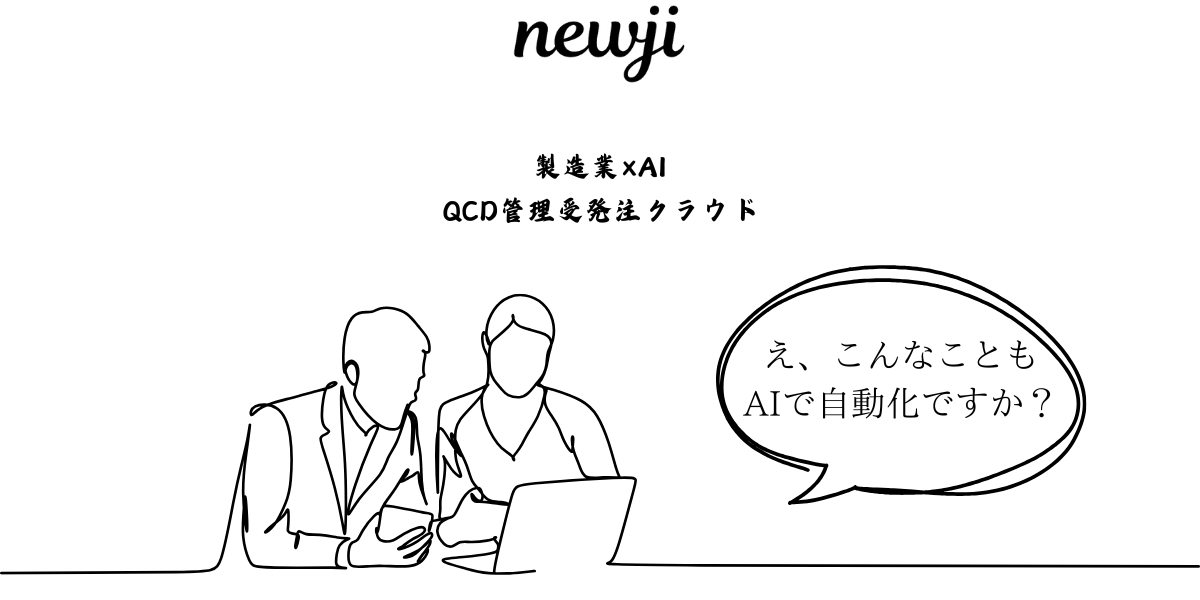
Mechanism of human error (mistake) and prevention measures, and quality improvement measures using the poka-yoke system
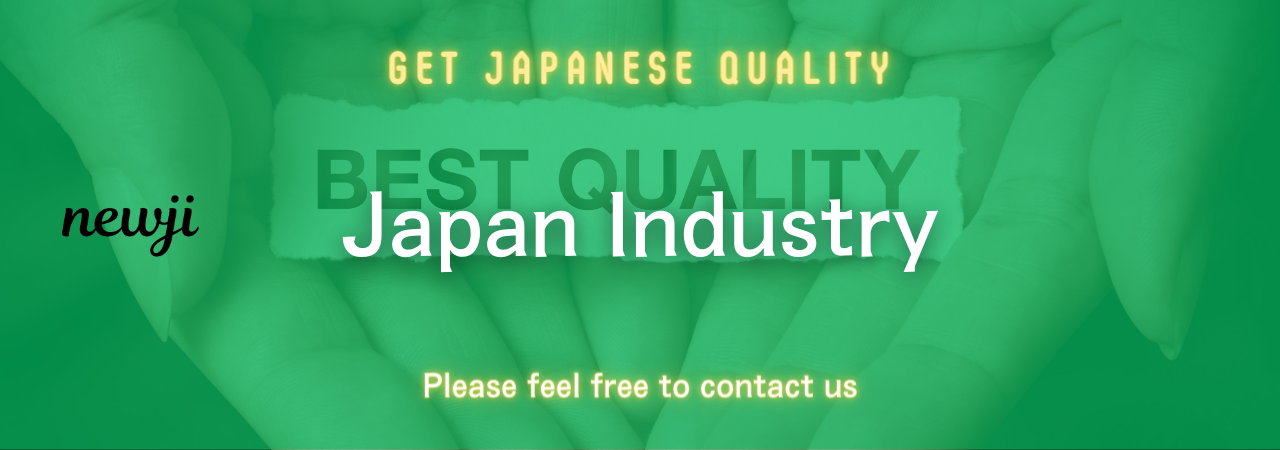
Understanding Human Error
Human error is an inevitable part of life that affects various aspects, from simple daily chores to complex industrial operations.
Errors occur when actions deviate from intended outcomes, often due to lapses in judgment, memory, or attentiveness.
Understanding the mechanisms of human error is key to developing effective prevention strategies and ensuring quality improvement.
Types of Human Error
Human errors can be categorized into different types based on their nature and the context in which they occur.
One common type is **slip**, which happens when a person intends to perform an action correctly but executes it incorrectly due to stray attention or memory lapses.
**Mistakes**, on the other hand, occur when there is a flaw in the planning or decision-making process.
These typically arise from misjudgments, lack of knowledge, or inappropriate application of rules.
Another type is **lapse**, characterized by forgetting a step in a process or losing memory of information critical to completing a task.
Understanding these types of errors helps pinpoint where preventive measures might be most effective.
Factors Contributing to Human Error
Several factors can contribute to human error, including environmental conditions, individual characteristics, and the complexity of tasks.
For instance, workplaces with poor lighting, excessive noise, or insufficient equipment maintenance can increase the likelihood of errors.
On an individual level, stress, fatigue, and inadequate training can hamper performance and lead to mistakes.
Complex tasks that demand high cognitive load or involve multitasking also heighten the risk of errors occurring.
Preventing Human Error
Preventing human error involves deploying strategies that minimize risk factors and bolster human performance.
Training and Education
Investing in comprehensive training programs helps individuals develop the necessary skills and knowledge to perform tasks correctly.
Regularly updated training ensures that employees stay informed about new procedures or technologies.
Environment and Workplace Design
Creating a work environment conducive to focus and efficiency can greatly reduce errors.
This includes proper lighting, noise reduction measures, and ensuring that equipment is well-maintained.
Ergonomic design principles can be applied to workplace layout and tools to minimize physical strain and cognitive load on workers.
Standardization and Simplification
Implementing standardized procedures helps reduce confusion and ensures consistency in task execution.
Simplifying complex processes by breaking them into clear, manageable steps aids understanding and decreases opportunities for error.
Quality Improvement with Poka-Yoke
The poka-yoke system, a Japanese term for “mistake-proofing,” provides a practical approach to preventing errors and improving quality.
Poka-yoke involves designing processes and systems so they inherently prevent errors from occurring or immediately highlight them.
Examples of Poka-Yoke
Poka-yoke techniques can be found in everyday objects and sophisticated manufacturing processes alike.
For instance, a USB plug can only be inserted in one direction, preventing users from making connection errors.
In manufacturing, assembly lines might include sensors that detect improperly assembled parts, stopping production to address the error.
Implementing Poka-Yoke in the Workplace
To incorporate poka-yoke into a workplace, businesses can begin by identifying common points of failure in their processes.
This involves analyzing historical error data and engaging with employees to understand where mistakes frequently occur.
From there, solutions can be designed to either eliminate these errors or make them easily detectable and correctable.
Benefits of Poka-Yoke
The poka-yoke approach offers numerous benefits, including reducing error rates, improving product quality, increasing operational efficiency, and boosting customer satisfaction.
By minimizing mistakes, businesses also experience reduced waste and cost savings.
Continuous Improvement and Monitoring
Implementing measures for error prevention and quality improvement is not a one-time effort.
Organizations should embrace a culture of continuous improvement, regularly reviewing and refining their processes.
Monitoring performance through metrics and feedback helps ensure that prevention measures remain effective and adapt to changing conditions.
Cultivating a Culture of Quality
Beyond implementing specific systems and strategies, fostering a culture that values quality and encourages mistake-proofing is crucial.
This involves promoting open communication, learning from errors without assigning blame, and encouraging innovation in error prevention techniques.
By emphasizing a commitment to quality at all levels, organizations can create an environment where human error is recognized, addressed, and minimized.
In conclusion, while human error may never be completely eradicated, understanding its mechanisms, employing preventive measures, and utilizing systems like poka-yoke can significantly reduce its impacts.
By prioritizing quality improvement, organizations can enhance efficiency, safeguard against errors, and provide exceptional value to their customers.
資料ダウンロード
QCD調達購買管理クラウド「newji」は、調達購買部門で必要なQCD管理全てを備えた、現場特化型兼クラウド型の今世紀最高の購買管理システムとなります。
ユーザー登録
調達購買業務の効率化だけでなく、システムを導入することで、コスト削減や製品・資材のステータス可視化のほか、属人化していた購買情報の共有化による内部不正防止や統制にも役立ちます。
NEWJI DX
製造業に特化したデジタルトランスフォーメーション(DX)の実現を目指す請負開発型のコンサルティングサービスです。AI、iPaaS、および先端の技術を駆使して、製造プロセスの効率化、業務効率化、チームワーク強化、コスト削減、品質向上を実現します。このサービスは、製造業の課題を深く理解し、それに対する最適なデジタルソリューションを提供することで、企業が持続的な成長とイノベーションを達成できるようサポートします。
オンライン講座
製造業、主に購買・調達部門にお勤めの方々に向けた情報を配信しております。
新任の方やベテランの方、管理職を対象とした幅広いコンテンツをご用意しております。
お問い合わせ
コストダウンが利益に直結する術だと理解していても、なかなか前に進めることができない状況。そんな時は、newjiのコストダウン自動化機能で大きく利益貢献しよう!
(Β版非公開)