- お役立ち記事
- Mechanism of metal corrosion, anti-corrosion technology, and application to troubleshooting
月間76,176名の
製造業ご担当者様が閲覧しています*
*2025年3月31日現在のGoogle Analyticsのデータより
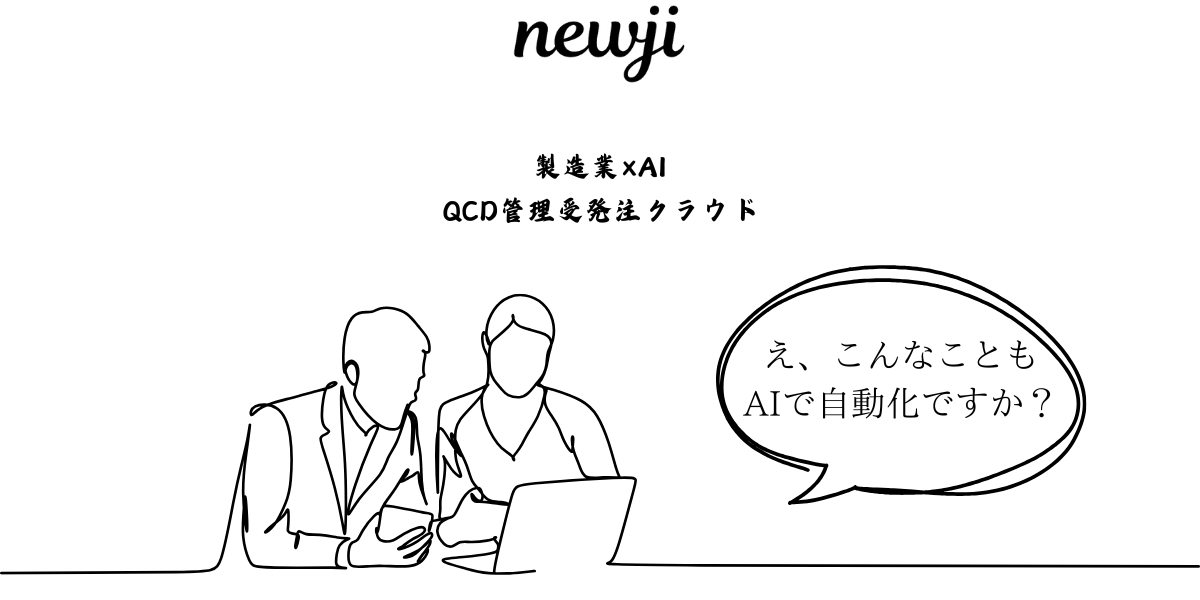
Mechanism of metal corrosion, anti-corrosion technology, and application to troubleshooting
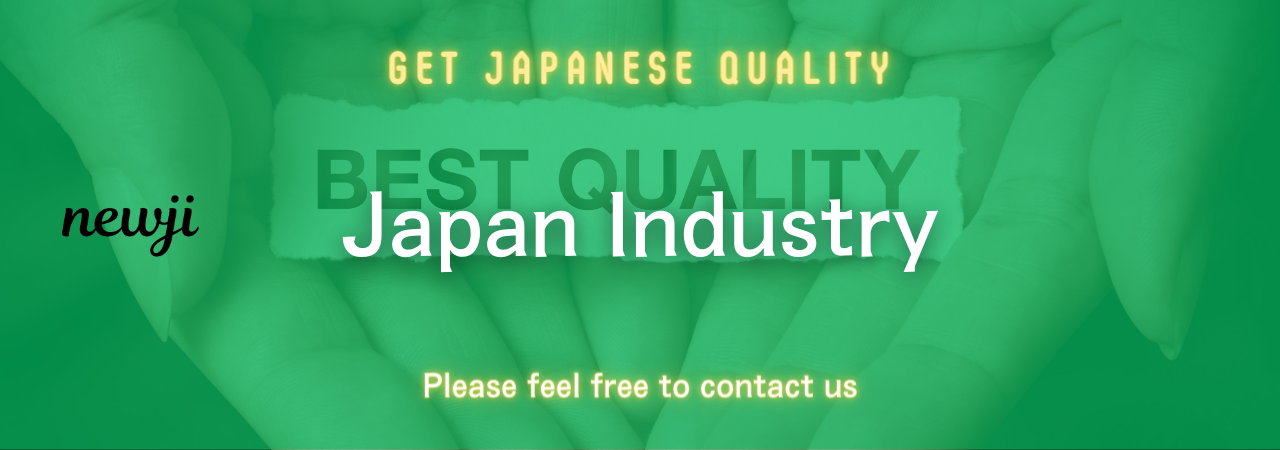
目次
Understanding Metal Corrosion
Metal corrosion is a natural process that gradually deteriorates metal objects, impacting their strength and functionality.
Corrosion occurs when metals react with environmental elements, leading to their degradation over time.
This chemical reaction results in the conversion of metal into more stable forms like oxides or sulfides.
The most common type of corrosion is rust, which typically affects iron and its alloys.
Understanding the mechanism of metal corrosion is crucial in devising strategies to prevent it.
The Chemistry Behind Corrosion
Corrosion primarily involves electrochemical reactions between metal and its environment.
Two important components of this process are the anode and the cathode.
The anode is the area on the metal where oxidation, or the loss of electrons, occurs.
This results in the metal deteriorating.
The cathode, on the other hand, is where reduction, or the gain of electrons, happens.
For corrosion to occur, an electrolyte—often water—is needed to facilitate the movement of ions between these two sites.
Environmental factors like humidity, temperature, and the presence of salts accelerate corrosion processes.
Types of Corrosion
1. **Uniform Corrosion:** This is the most common type, where corrosion occurs evenly across the surface of the metal.
It is predictable and often mitigated through protective coatings.
2. **Pitting Corrosion:** This type results in small holes or pits on the metal surface and is difficult to detect.
It can lead to the failure of metal structures if not identified in time.
3. **Galvanic Corrosion:** Occurs when two different metals come into electrical contact while in the presence of an electrolyte.
One metal (the anode) will corrode faster than it would alone, while the other (the cathode) corrodes slower.
4. **Crevice Corrosion:** Common in spaces like joints or under gaskets, crevice corrosion happens where there is a stagnant microenvironment.
5. **Stress Corrosion Cracking (SCC):** This is a failure mechanism caused by the simultaneous action of tensile stress and a corrosive environment, often leading to sudden failures.
Anti-Corrosion Technologies
To combat the detrimental effects of corrosion, a variety of anti-corrosion technologies have been developed.
These strategies aim to either slow down the corrosion process or prevent it entirely.
Protective Coatings
One of the most effective methods to prevent corrosion is applying protective coatings to metal surfaces.
These coatings act as a physical barrier that prevents environmental elements from contacting the metal.
Common coatings include paints, varnishes, and galvanization, where a protective zinc layer is applied to iron or steel.
Cathodic Protection
This technique involves converting the entire metal surface into a cathode, thereby preventing it from corroding.
It is achieved by either connecting a more reactive metal to act as the sacrificial anode or by using an impressed current system.
Cathodic protection is widely used in pipelines, tanks, and ships.
Corrosion Inhibitors
Corrosion inhibitors are chemicals added to the environment that significantly slow down the corrosion process.
These inhibitors form a complex with the metal surface, effectively blocking corrosive compounds.
They are commonly used in cooling systems, oil refineries, and industrial processes.
Materials Selection and Design
Choosing the right materials can also play a significant role in preventing corrosion.
Alloys are often designed and selected based on their resistance to corrosion, especially in environments known to be particularly harsh.
Good design practices encourage creating shapes that do not trap moisture and allow for easy maintenance access.
Application in Troubleshooting
Understanding and combating corrosion is essential in troubleshooting metal failure issues in various industries.
Corrosion can lead to unexpected shutdowns, costly repairs, and safety hazards.
Recognizing the signs and types of corrosion early can inform prompt corrective measures and proactive maintenance strategies.
Inspection and Monitoring
Regular inspection and monitoring are vital in identifying areas vulnerable to corrosion.
Technologies like ultrasonic testing, radiography, and corrosion coupons are employed to measure corrosion rates and monitor structural integrity.
Failure Analysis
When metal structures fail, a detailed analysis is essential in determining the root cause.
Failure analysis helps in understanding whether the failure was due to corrosion, mechanical stress, or other factors.
This information is crucial for modifying existing maintenance strategies or redesigning components.
Implementing Preventive Measures
Based on the findings of inspections and failure analyses, systematic preventive measures can be implemented.
These measures may include regular maintenance schedules, applying new protective coatings, or installing cathodic protection systems.
The aim is to extend the metal’s lifespan and reduce the likelihood of future failures.
The Importance of Education and Training
Educating employees and engineers on the importance of corrosion and its prevention plays a significant role in maintaining infrastructure longevity.
Training programs should focus on the identification of early signs of corrosion, proper material selection, and the application of anti-corrosion technologies.
Organizations benefit greatly from investing in such training, as it leads to improved safety, enhanced efficiency, and significant cost savings in the long run.
Understanding the mechanisms behind metal corrosion and the available technologies to prevent it can save industries from significant losses and improve the safety of structures.
By applying the knowledge strategically, industries can mitigate the risks associated with metal corrosion, ensuring longevity and reliability in their operations.
資料ダウンロード
QCD管理受発注クラウド「newji」は、受発注部門で必要なQCD管理全てを備えた、現場特化型兼クラウド型の今世紀最高の受発注管理システムとなります。
ユーザー登録
受発注業務の効率化だけでなく、システムを導入することで、コスト削減や製品・資材のステータス可視化のほか、属人化していた受発注情報の共有化による内部不正防止や統制にも役立ちます。
NEWJI DX
製造業に特化したデジタルトランスフォーメーション(DX)の実現を目指す請負開発型のコンサルティングサービスです。AI、iPaaS、および先端の技術を駆使して、製造プロセスの効率化、業務効率化、チームワーク強化、コスト削減、品質向上を実現します。このサービスは、製造業の課題を深く理解し、それに対する最適なデジタルソリューションを提供することで、企業が持続的な成長とイノベーションを達成できるようサポートします。
製造業ニュース解説
製造業、主に購買・調達部門にお勤めの方々に向けた情報を配信しております。
新任の方やベテランの方、管理職を対象とした幅広いコンテンツをご用意しております。
お問い合わせ
コストダウンが利益に直結する術だと理解していても、なかなか前に進めることができない状況。そんな時は、newjiのコストダウン自動化機能で大きく利益貢献しよう!
(β版非公開)