- お役立ち記事
- Mechanism of metal fatigue and fatigue life prediction necessary for fatigue-resistant design and how to utilize it for “fatigue design using FEM”
月間76,176名の
製造業ご担当者様が閲覧しています*
*2025年3月31日現在のGoogle Analyticsのデータより
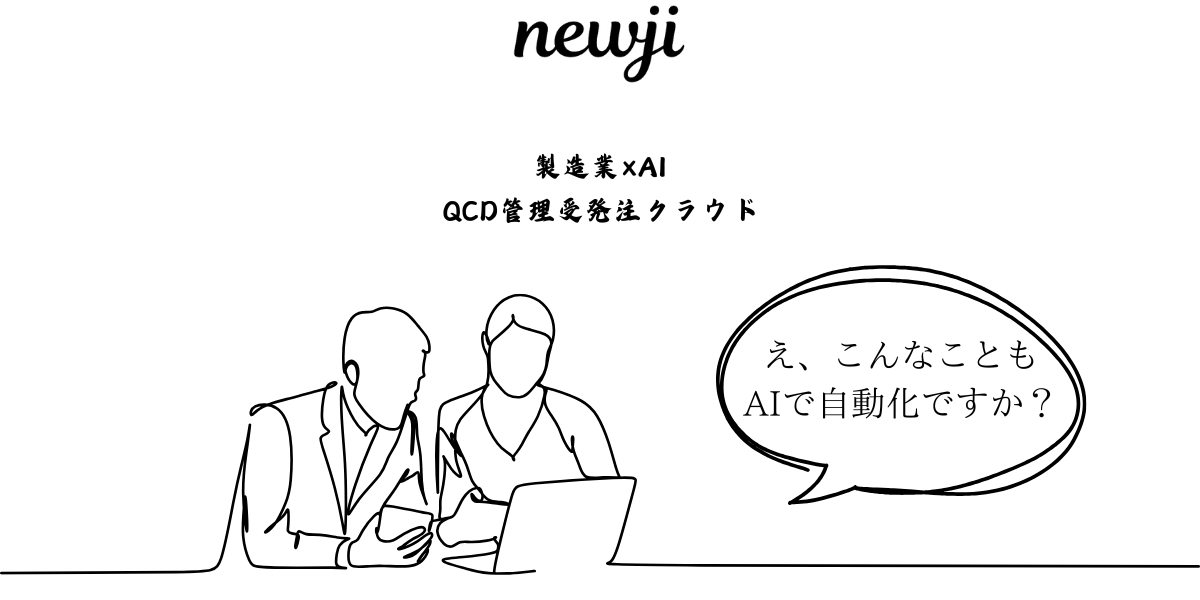
Mechanism of metal fatigue and fatigue life prediction necessary for fatigue-resistant design and how to utilize it for “fatigue design using FEM”
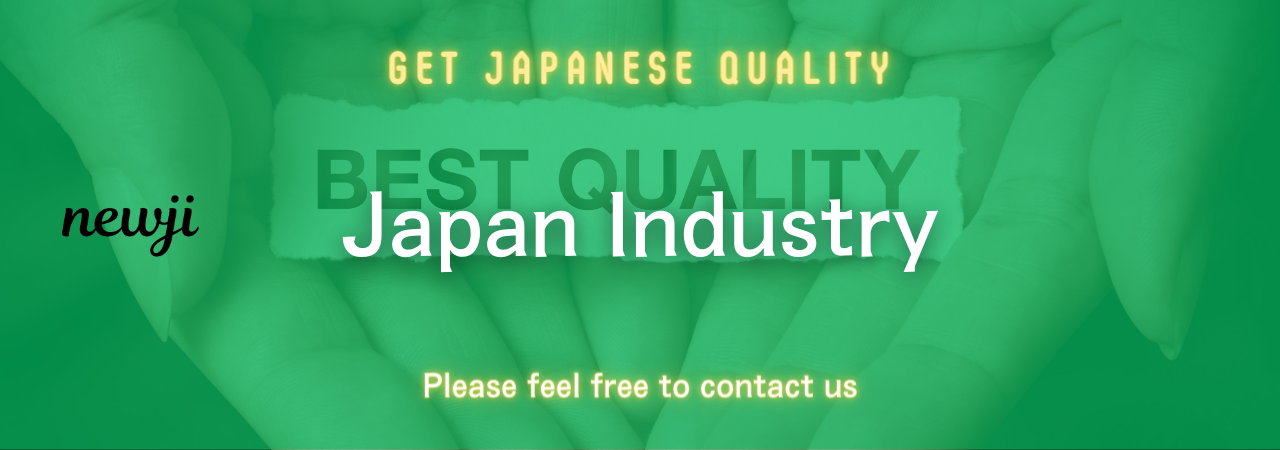
目次
Understanding Metal Fatigue
Metal fatigue is a phenomenon where a material experiences progressive structural damage when subjected to cyclic loading.
Over time, this can lead to cracks and fractures, even if the applied stress is below the material’s ultimate tensile strength.
The process is often slow and insidious, making it a critical focus for engineers, especially in the fields of aerospace, automotive, and structural engineering.
Causes of Metal Fatigue
Metal fatigue occurs due to repetitive or fluctuating stress that causes microscale damage to propagate over time.
Factors contributing to metal fatigue include stress concentration, environmental conditions like temperature and corrosion, and the material’s intrinsic properties.
For example, notches, sharp corners, or surface defects can act as stress concentrators, accelerating the fatigue process.
Furthermore, temperature fluctuations can exacerbate fatigue, as can exposure to corrosive environments which may weaken the material’s integrity.
The Stages of Metal Fatigue
The metal fatigue process comprises three primary stages: crack initiation, crack propagation, and final fracture.
Initially, under cyclic stress, microscopic changes occur at localized areas, leading to the initiation of cracks.
As stress continues to be applied, these cracks begin to propagate.
If undetected, they eventually cause a complete fracture, potentially leading to catastrophic failure.
Fatigue Life Prediction
Predicting the fatigue life of a component is crucial for designing long-lasting and safe structures.
Fatigue life prediction involves estimating how long a material will withstand cyclic loading before failure.
This process enables engineers to create designs with adequate safety margins.
Methods for Fatigue Life Prediction
Various methods exist for predicting fatigue life, each with its advantages and limitations.
The S-N curve (Stress-Life method) is among the most familiar, plotting stress against the number of cycles to failure.
The curve indicates how many cycles a material can endure at a specific stress level before failing.
Another approach is the Local Stress-Strain method, which evaluates the component’s response to localized stresses and strains.
This method is particularly useful for parts with complex geometries where stress concentration may be significant.
The Fracture Mechanics method involves analyzing crack propagation, assessing how small cracks grow under cyclic stress until they reach a critical size.
Fatigue-Resistant Design
Designing components to resist fatigue involves understanding and applying these predictions effectively.
Material Selection
Choosing the right material is one of the first steps in fatigue-resistant design.
Materials with high fatigue strength, such as certain alloys and composites, are preferred.
However, the choice also depends on other factors like cost, weight, and the operating environment of the component.
Geometric Design
Minimizing stress concentrations can significantly enhance fatigue resistance.
This can be achieved through careful geometric design.
Smooth transitions, fillets, and the elimination of sharp corners reduce hotspots where stress concentrations might occur.
Surface Treatments
Techniques such as shot peening, surface hardening, and coating can extend the fatigue life of components.
These treatments enhance surface strength or provide protective barriers against environmental factors.
Fatigue Design Using Finite Element Method (FEM)
The Finite Element Method (FEM) is a powerful computational tool used for fatigue-resistant design, allowing for the detailed analysis of complex structures.
Why Use FEM?
FEM divides a large system into simpler parts called finite elements.
These are solved simultaneously to simulate how the system behaves under stress.
Using FEM, engineers can identify potential failure points, stress concentrations, and deformation patterns within a design.
Application of FEM in Fatigue Design
FEM facilitates the optimization of component geometry to minimize fatigue risk.
By simulating real-world loading conditions, engineers can refine designs to extend fatigue life before physical testing.
Furthermore, FEM allows for virtual prototyping, saving time and cost in product development.
Design iterations can be tested and refined in the virtual environment before producing physical prototypes.
Challenges with FEM
While FEM is a powerful tool, it requires accurate input data and expert interpretation.
Erroneous assumptions or data can lead to misleading results.
Thus, engineers must validate FEM models against experimental data to ensure reliability.
Conclusion
Understanding the mechanisms of metal fatigue and effectively predicting fatigue life are essential components in the design of fatigue-resistant materials and structures.
By employing methods such as FEM, engineers can create designs that withstand the demands of real-world applications, ensuring safety and reliability.
Advancements in predictive methodologies and computational tools continue to improve our ability to anticipate and mitigate the impacts of metal fatigue, making engineering designs more robust than ever before.
資料ダウンロード
QCD管理受発注クラウド「newji」は、受発注部門で必要なQCD管理全てを備えた、現場特化型兼クラウド型の今世紀最高の受発注管理システムとなります。
ユーザー登録
受発注業務の効率化だけでなく、システムを導入することで、コスト削減や製品・資材のステータス可視化のほか、属人化していた受発注情報の共有化による内部不正防止や統制にも役立ちます。
NEWJI DX
製造業に特化したデジタルトランスフォーメーション(DX)の実現を目指す請負開発型のコンサルティングサービスです。AI、iPaaS、および先端の技術を駆使して、製造プロセスの効率化、業務効率化、チームワーク強化、コスト削減、品質向上を実現します。このサービスは、製造業の課題を深く理解し、それに対する最適なデジタルソリューションを提供することで、企業が持続的な成長とイノベーションを達成できるようサポートします。
製造業ニュース解説
製造業、主に購買・調達部門にお勤めの方々に向けた情報を配信しております。
新任の方やベテランの方、管理職を対象とした幅広いコンテンツをご用意しております。
お問い合わせ
コストダウンが利益に直結する術だと理解していても、なかなか前に進めることができない状況。そんな時は、newjiのコストダウン自動化機能で大きく利益貢献しよう!
(β版非公開)