- お役立ち記事
- Mechanism of residual stress generation in plastic molded products, prediction of strength and deformation, and countermeasures against molding defects
月間76,176名の
製造業ご担当者様が閲覧しています*
*2025年3月31日現在のGoogle Analyticsのデータより
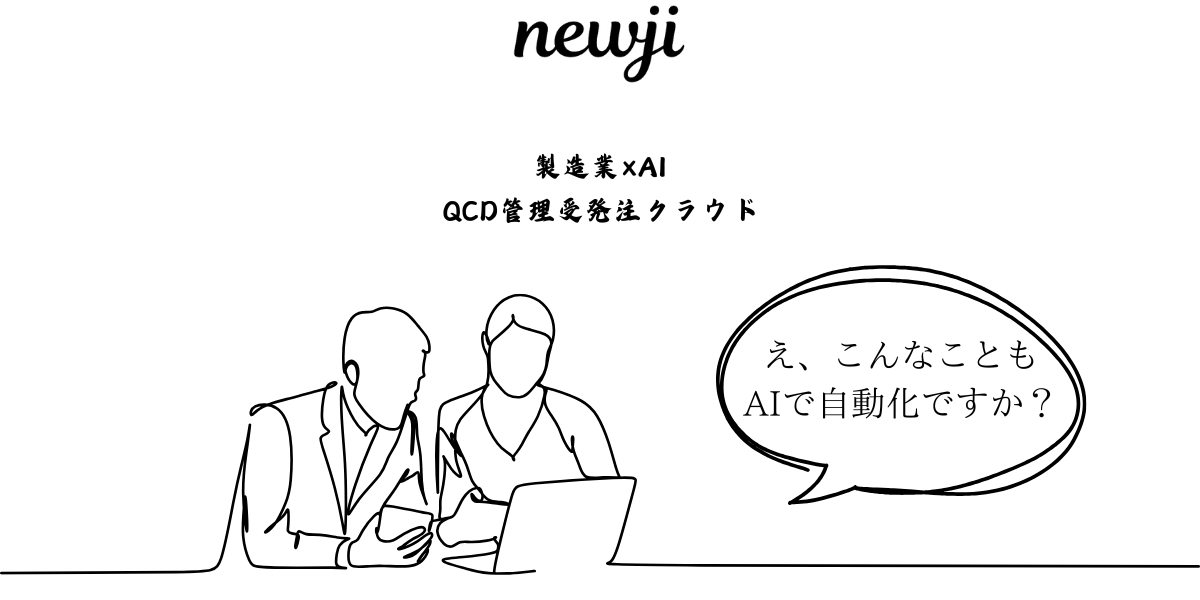
Mechanism of residual stress generation in plastic molded products, prediction of strength and deformation, and countermeasures against molding defects
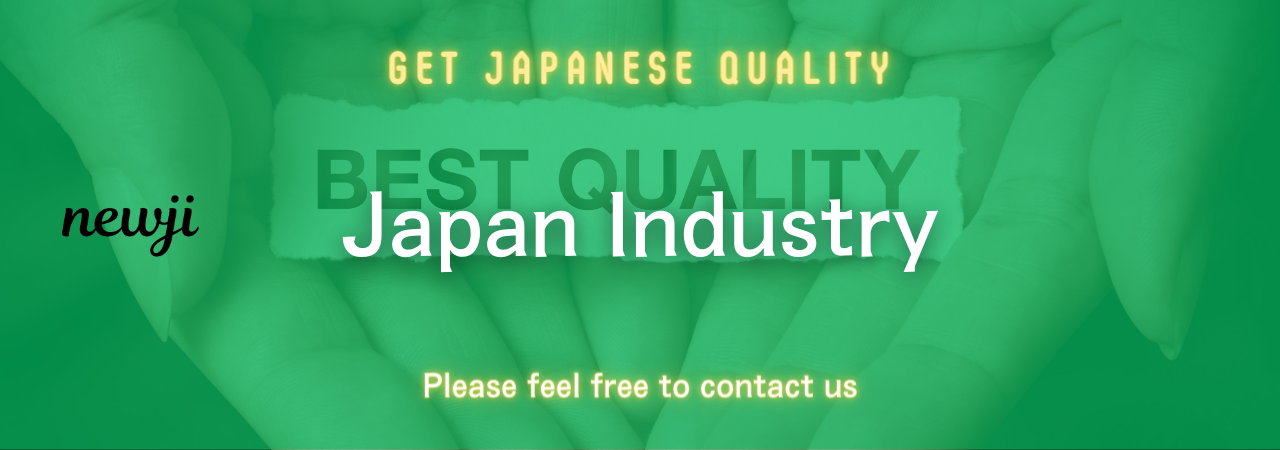
目次
Introduction to Residual Stress in Plastic Molded Products
Plastic molded products are essential components in various industries due to their versatility and durability.
However, the process of molding plastics often results in residual stresses, which can significantly affect the performance and quality of the final product.
Understanding the mechanism of residual stress generation, predicting strength and deformation, and implementing effective countermeasures against molding defects are crucial for manufacturers.
Residual stresses are internal forces trapped within a material, even when no external load is applied.
These stresses can lead to issues such as warping, cracking, or other structural deformities, compromising the functionality of the plastic product.
Therefore, identifying these stresses during the design and manufacturing stages is vital for ensuring the reliability of the molded items.
Mechanism of Residual Stress Generation
Residual stresses originate from various factors during the plastic molding process.
One major cause is the differential cooling rates.
When a plastic product cools unevenly, different parts of the material contract at varying rates, leading to internal stresses.
Thicker sections tend to cool more slowly compared to thinner areas, creating a stress differential within the product.
Another contributing factor is phase transformation.
As the plastic solidifies, it transitions from a liquid to a solid state.
This transformation is not instantaneous and can induce internal stresses due to volume changes and material flow patterns during solidification.
Additionally, anisotropic shrinkage — where the material contracts differently in various directions — can result in residual stresses.
This usually occurs due to the molecular orientation developed during the molding process, as the polymer chains generally align in the direction of flow.
Molding conditions, such as temperature, pressure, and cooling time, also play crucial roles in the formation of residual stresses.
Higher molding pressures can lead to more pronounced residual stresses, while rapid cooling rates can exacerbate stress disparities.
Prediction of Strength and Deformation
Predicting the strength and deformation of plastic molded products involves analyzing the impact of residual stresses on material properties.
This prediction is essential for ensuring that the product meets performance criteria and safety standards.
Advanced computer simulations can model the stress distribution during the molding process.
Finite element analysis (FEA) is a powerful tool that engineers use to simulate the behavior of plastics under various conditions.
By inputting variables such as temperature, pressure, and material properties into the simulation, engineers can predict where residual stresses are likely to develop.
These simulations help in forecasting deformations, allowing for adjustments in design and process parameters to mitigate potential issues.
For instance, optimizing the geometry of the mold and adjusting processing conditions can significantly reduce stress concentrations, leading to more uniform stress distributions.
In addition to simulations, experimental techniques such as photoelasticity and X-ray diffraction can be employed to measure residual stresses directly.
These methods provide insights into stress patterns, aiding manufacturers in validating the accuracy of predictive models.
Countermeasures Against Molding Defects
Implementing effective countermeasures is crucial for minimizing the adverse effects of residual stress and preventing molding defects.
Several strategies can be applied to mitigate these issues and enhance product quality.
One approach is optimizing the design and production process.
By carefully selecting the right materials, modifying mold designs, and controlling processing parameters, manufacturers can reduce the extent of residual stresses.
For instance, uniform wall thickness and gradual transitions in thickness can alleviate stress concentrations.
Cooling rates play a significant role in stress formation.
Implementing controlled and gradual cooling can help manage the differential shrinkage, reducing stress disparities.
Using cooling circuits within the mold can ensure even cooling, diminishing the risk of warping and deformation.
Post-processing techniques such as annealing can also be effective in relieving residual stresses.
Annealing involves heating the molded product to a specific temperature, then allowing it to cool slowly.
This process helps redistribute and relax stresses within the material, enhancing its overall stability and performance.
Furthermore, integrating quality control measures throughout the production process ensures early detection and correction of potential defects.
Using non-destructive testing methods and regular inspections can help identify issues before they compromise the product’s integrity.
Conclusion
Residual stresses in plastic molded products present challenges to manufacturers, but understanding the mechanisms of their generation allows for effective prediction and mitigation strategies.
By leveraging advanced simulation techniques and implementing strategic design and process improvements, manufacturers can enhance the quality and reliability of plastic molded products.
Continuous innovation and research in this field are essential for developing new materials and technologies to further address molding challenges.
Ultimately, a proactive approach to managing residual stresses not only ensures product performance but also enhances customer satisfaction and trust in plastic molded products.
資料ダウンロード
QCD管理受発注クラウド「newji」は、受発注部門で必要なQCD管理全てを備えた、現場特化型兼クラウド型の今世紀最高の受発注管理システムとなります。
ユーザー登録
受発注業務の効率化だけでなく、システムを導入することで、コスト削減や製品・資材のステータス可視化のほか、属人化していた受発注情報の共有化による内部不正防止や統制にも役立ちます。
NEWJI DX
製造業に特化したデジタルトランスフォーメーション(DX)の実現を目指す請負開発型のコンサルティングサービスです。AI、iPaaS、および先端の技術を駆使して、製造プロセスの効率化、業務効率化、チームワーク強化、コスト削減、品質向上を実現します。このサービスは、製造業の課題を深く理解し、それに対する最適なデジタルソリューションを提供することで、企業が持続的な成長とイノベーションを達成できるようサポートします。
製造業ニュース解説
製造業、主に購買・調達部門にお勤めの方々に向けた情報を配信しております。
新任の方やベテランの方、管理職を対象とした幅広いコンテンツをご用意しております。
お問い合わせ
コストダウンが利益に直結する術だと理解していても、なかなか前に進めることができない状況。そんな時は、newjiのコストダウン自動化機能で大きく利益貢献しよう!
(β版非公開)