- お役立ち記事
- Mechanism of stress concentration and key points of CAE analysis technology and strength evaluation method
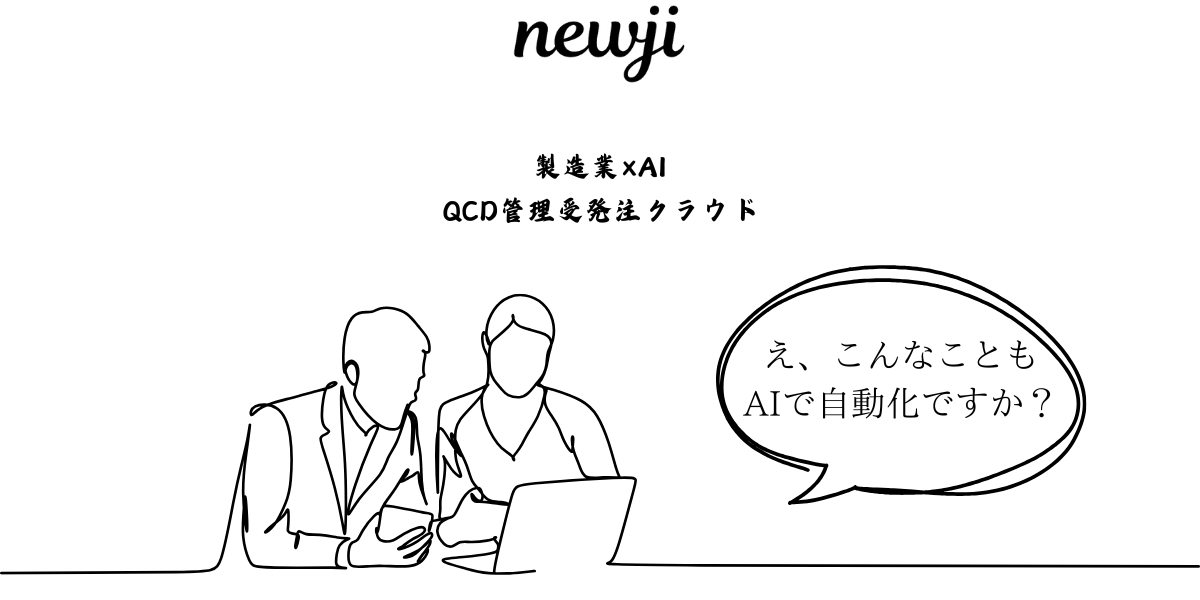
Mechanism of stress concentration and key points of CAE analysis technology and strength evaluation method
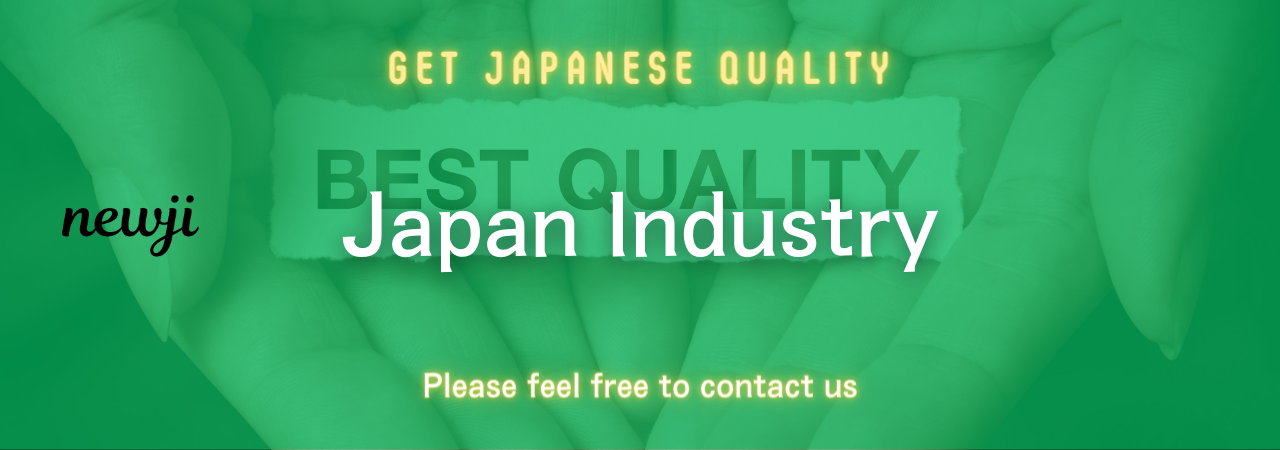
目次
Understanding Stress Concentration
Stress concentration refers to the accumulation of stress in a material, often occurring in areas such as sharp corners, holes, notches, or other irregularities that disrupt the uniform distribution of stress.
These concentrations can significantly affect the mechanical properties of a material, leading to failure if not properly managed.
Understanding the mechanisms of stress concentration is essential for engineers and designers in optimizing both the structural integrity and longevity of components.
Key Factors Leading to Stress Concentration
Several factors contribute to the development of stress concentration in materials:
1. **Geometry**: Shapes with sudden changes, like notches or sharp edges, easily concentrate stress.
2. **Material Properties**: Variations in material properties, such as different elasticities in composite materials, can cause imbalances in stress distribution.
3. **Load Conditions**: Uneven or unusual load applications, such as point loads or bending, can create concentrated stress zones.
4. **Environmental Conditions**: Temperature changes, humidity, and exposure to corrosive environments can exacerbate stress concentration by changing the material’s properties or dimensions.
The Role of CAE in Stress Analysis
Computer-Aided Engineering (CAE) plays a crucial role in analyzing and addressing stress concentration.
With advancements in technology, CAE tools have become integral in simulating and predicting how stress is distributed across a structure.
This allows for a more precise assessment of potential failure points and areas that require design improvement.
Benefits of CAE Analysis
1. **Enhanced Accuracy**: CAE tools provide accurate simulations based on complex algorithms, taking into account all relevant variables.
2. **Time Efficiency**: Simulating stress distribution through CAE can save significant time compared to traditional manual calculations or trial-and-error methods.
3. **Cost Reduction**: By predicting issues early in the design phase, CAE analysis helps avoid costly redesigns or material wastage.
4. **Design Optimization**: CAE enables optimization by allowing engineers to test different design scenarios quickly and efficiently before actual production starts.
Strength Evaluation Methodologies
Strength evaluation is essential in determining how materials and components will react under various stress conditions.
Various methodologies are employed to evaluate strength, focusing on understanding and mitigating stress concentration effects.
Finite Element Analysis (FEA)
Finite Element Analysis (FEA) is a widely used computational method that breaks down a structure into smaller, manageable finite elements.
Each element is analyzed to determine how it reacts under stress, allowing engineers to identify high-stress areas effectively.
– **Process**: The process involves meshing the component, defining boundary conditions, applying loads, and analyzing the results.
– **Advantages**: FEA provides detailed insights into stress distribution, deformation, and potential failure points.
Fatigue Testing
Fatigue testing evaluates how materials perform under repeated stress cycles to predict their long-term behavior.
– **Method**: The material is subjected to cyclic stress until failure occurs, providing data on its limits and lifecycle.
– **Importance**: This testing is crucial for components exposed to fluctuating stress, such as in automotive or aerospace industries.
Key Points for Effective Stress Management
Managing stress concentration effectively requires a multi-faceted approach combined with appropriate technological implementation.
Design Modifications
– **Smooth Transitions**: Implement gradual transitions in design to minimize abrupt changes in geometry that lead to stress concentration.
– **Filleting**: Adding fillets to sharp corners can distribute stress more evenly, reducing the likelihood of stress-induced failure.
Material Selection
Choosing the right material with appropriate properties can significantly impact the success of engineering designs under stress.
– **Composites**: Use composite materials where suitable for better stress distribution and to leverage their inherent properties.
– **Alloys**: Consider using alloys that offer a good balance between strength and ductility.
Regular Inspections and Maintenance
Routine inspections can help in early detection of stress concentration issues that could lead to material failure.
– **Non-Destructive Testing (NDT)**: Techniques such as ultrasound or X-ray can detect underlying stress without damaging the component, aiding in preventative maintenance strategies.
Conclusion
Understanding the mechanisms behind stress concentration, the capabilities of CAE analysis, and effective strength evaluation methods form the cornerstone of efficient engineering design.
By implementing superior design practices, choosing appropriate materials, and leveraging technology like CAE, the risks associated with stress concentration can be minimized, ensuring safety and longevity in the utilization of materials and components.
These strategies are essential for engineers seeking to optimize their designs and prevent potential failures, ultimately contributing to the reliability and durability of engineered products.
資料ダウンロード
QCD調達購買管理クラウド「newji」は、調達購買部門で必要なQCD管理全てを備えた、現場特化型兼クラウド型の今世紀最高の購買管理システムとなります。
ユーザー登録
調達購買業務の効率化だけでなく、システムを導入することで、コスト削減や製品・資材のステータス可視化のほか、属人化していた購買情報の共有化による内部不正防止や統制にも役立ちます。
NEWJI DX
製造業に特化したデジタルトランスフォーメーション(DX)の実現を目指す請負開発型のコンサルティングサービスです。AI、iPaaS、および先端の技術を駆使して、製造プロセスの効率化、業務効率化、チームワーク強化、コスト削減、品質向上を実現します。このサービスは、製造業の課題を深く理解し、それに対する最適なデジタルソリューションを提供することで、企業が持続的な成長とイノベーションを達成できるようサポートします。
オンライン講座
製造業、主に購買・調達部門にお勤めの方々に向けた情報を配信しております。
新任の方やベテランの方、管理職を対象とした幅広いコンテンツをご用意しております。
お問い合わせ
コストダウンが利益に直結する術だと理解していても、なかなか前に進めることができない状況。そんな時は、newjiのコストダウン自動化機能で大きく利益貢献しよう!
(Β版非公開)