- お役立ち記事
- Mechanism to prevent soldering defects and reliability deterioration
Mechanism to prevent soldering defects and reliability deterioration
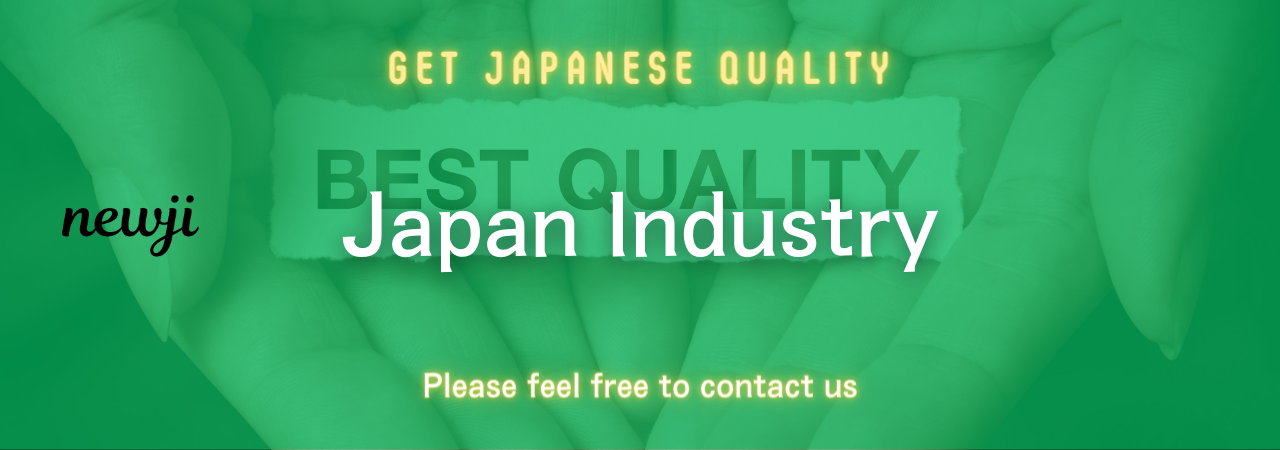
目次
Understanding Soldering Defects
Soldering is a critical process in electronics manufacturing, used to create solid connections between components and circuit boards.
However, defects in soldering can lead to faulty products and reduced reliability.
To mitigate these issues, it’s important to understand the different types of soldering defects and how they occur.
There are several common types of soldering defects.
Among these are solder bridges, insufficient solder, and cold solder joints.
Solder bridges occur when excess solder creates an unintended connection between two points.
Insufficient solder appears when not enough solder is used, resulting in a weak joint.
Cold solder joints result from incomplete melting of the solder, leading to poor adherence and electrical conductivity.
Causes of Soldering Defects
There are various causes of soldering defects, which can be generally categorized under human, process, or material factors.
1. **Human Error**: Improper handling by operators or incorrect settings during the manual soldering process can lead to defects.
A simple mistake, like applying too much or too little pressure or improper soldering temperature, may result in bad connections.
2. **Process Variations**: Variations in the soldering process, such as temperature fluctuation, inadequate process control, or timing inconsistencies, can cause defects.
An uneven temperature profile during the reflow process is a common cause, leading to none-uniform heat distribution.
3. **Material Issues**: The quality and compatibility of the solder, solder paste, and flux, as well as the components and PCBs themselves, can influence soldering outcomes.
Poor-quality materials are prone to defects like oxidation, which inhibits proper bonding.
Preventive Mechanisms
Preventing soldering defects involves a combination of good practices and technology improvements.
Here’s how to enhance reliability:
Quality Control and Training
Implementing stringent quality control procedures can minimize human error.
Regular training programs ensure operators are well-versed in the necessary skills for accurate and effective soldering.
By keeping staff up to date on the latest techniques and technologies, companies can ensure high-quality production.
Process Optimization
Ensuring the soldering process is well-optimized is key.
This includes precise control over temperature and humidity in the manufacturing environment.
Employing automated soldering systems equipped with closed-loop feedback can help maintain stable conditions and adjust parameters in real-time, preventing inconsistent solder joints.
Material Selection
Using high-quality and compatible materials is crucial.
Investigate the thermal and mechanical properties of solder and ensure they conform to the specifications required by the design.
When selecting PCBs and components, consideration of surface finish and material type is important to avoid issues like delamination and oxidation.
Reliability Testing
Testing is an essential step in ensuring and maintaining soldering quality and system reliability.
Several techniques can be employed:
Visual Inspection
Visual inspection using magnifying devices allows operators to catch visible defects, including bridging, inadequate solder coverage, and irregular solder patterns.
This is often the first step in defect identification.
Automated Optical Inspection (AOI)
AOI uses advanced machinery to automatically detect defects by scanning PCBs for identifiable issues.
This precise technology can detect minute defects undetectable to the human eye, improving reliability.
X-Ray Inspection
For non-visible defects such as voids within the solder or under components, X-ray inspection can identify internal issues without harming the PCB.
It’s particularly useful for detecting defects in BGA and other complex components.
Continuous Improvement
While preventive mechanisms and reliable testing are crucial, continuous monitoring and efforts to improve soldering processes are equally important.
Data Analysis
Routine data collection and analysis from production lines provide important insights.
Identifying trends in defect occurrence can help pinpoint where improvements can be made, such as adjusting parameters or optimizing designs.
Feedback Systems
Implementing systems where feedback is always available can lead to quicker corrective actions.
Encouraging teams to report issues and suggest improvements leads to a proactive culture of quality.
Conclusion
Preventing soldering defects and enhancing reliability is an ongoing process that requires dedication, vigilance, and technological advances.
Understanding the causes of defects, implementing preventive mechanisms, utilizing thorough testing, and committing to continuous improvement are all crucial steps in achieving superior soldering reliability.
As the electronic industry evolves, staying informed about new techniques and technologies will enable manufacturers to maintain high-quality production standards.
資料ダウンロード
QCD調達購買管理クラウド「newji」は、調達購買部門で必要なQCD管理全てを備えた、現場特化型兼クラウド型の今世紀最高の購買管理システムとなります。
ユーザー登録
調達購買業務の効率化だけでなく、システムを導入することで、コスト削減や製品・資材のステータス可視化のほか、属人化していた購買情報の共有化による内部不正防止や統制にも役立ちます。
NEWJI DX
製造業に特化したデジタルトランスフォーメーション(DX)の実現を目指す請負開発型のコンサルティングサービスです。AI、iPaaS、および先端の技術を駆使して、製造プロセスの効率化、業務効率化、チームワーク強化、コスト削減、品質向上を実現します。このサービスは、製造業の課題を深く理解し、それに対する最適なデジタルソリューションを提供することで、企業が持続的な成長とイノベーションを達成できるようサポートします。
オンライン講座
製造業、主に購買・調達部門にお勤めの方々に向けた情報を配信しております。
新任の方やベテランの方、管理職を対象とした幅広いコンテンツをご用意しております。
お問い合わせ
コストダウンが利益に直結する術だと理解していても、なかなか前に進めることができない状況。そんな時は、newjiのコストダウン自動化機能で大きく利益貢献しよう!
(Β版非公開)