- お役立ち記事
- Mechanism to prevent soldering defects and reliability deterioration
月間76,176名の
製造業ご担当者様が閲覧しています*
*2025年3月31日現在のGoogle Analyticsのデータより
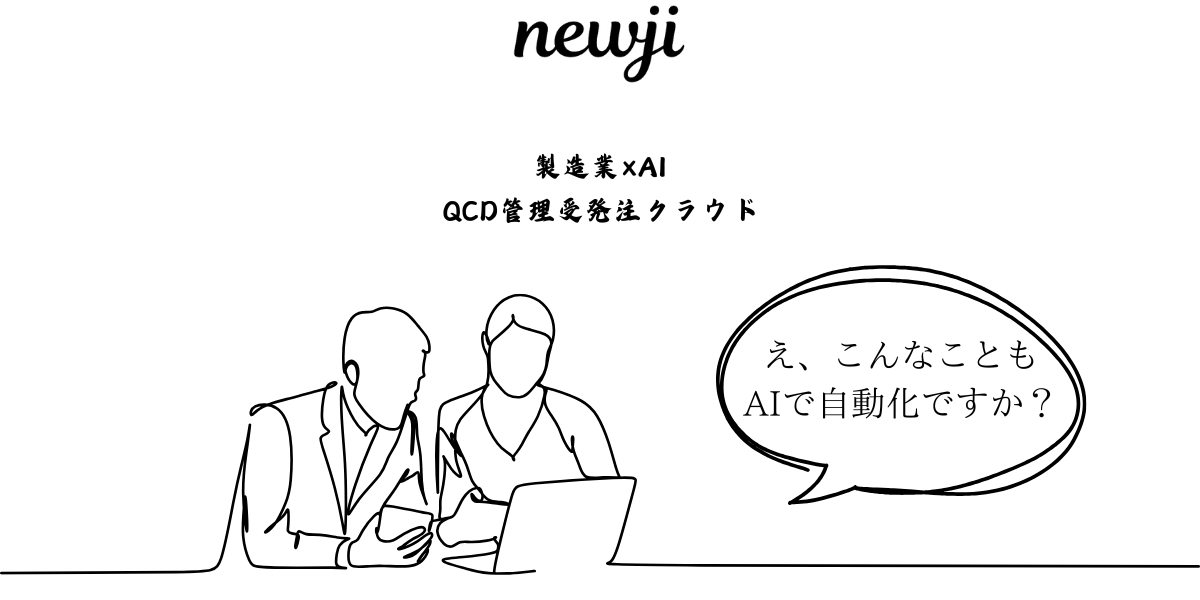
Mechanism to prevent soldering defects and reliability deterioration
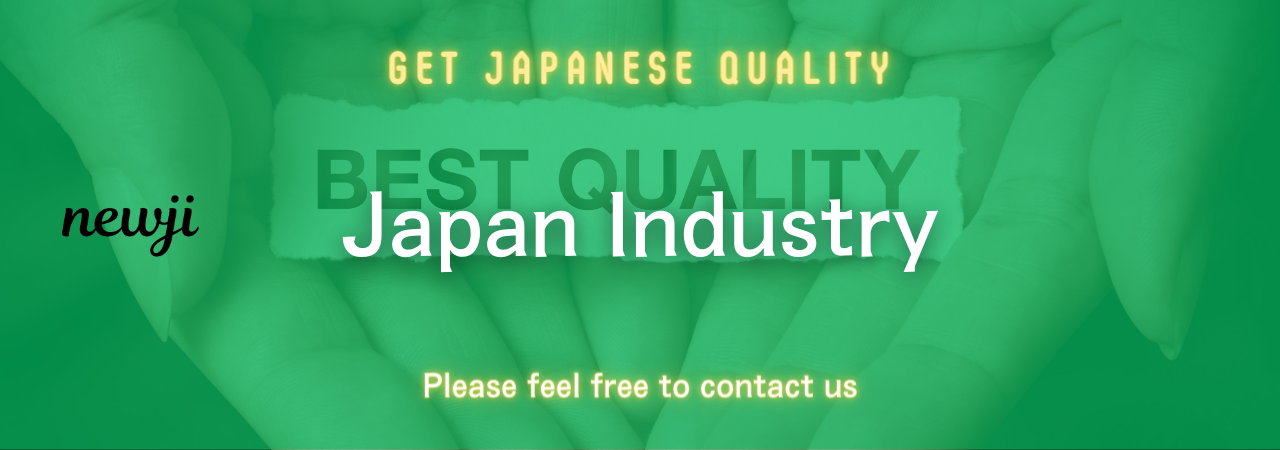
目次
Understanding Soldering Defects
Soldering is a critical process in the manufacturing of electronic devices, where components are mounted onto printed circuit boards (PCBs).
However, this process is often prone to several defects that can affect the final product’s functionality and reliability.
Soldering defects can occur due to various reasons, including poor environmental conditions, incorrect materials, and improper technique.
Common defects include solder bridges, cold joints, and voids, each of which can lead to performance issues or even device failure.
To maintain the quality and reliability of soldered connections, it is essential to understand these defects and implement mechanisms to prevent them.
Solder Bridges
Solder bridges occur when excess solder connects two adjacent components or conductors.
This can create an unwanted electrical path that may cause short circuits and damage the circuit’s functionality.
To prevent solder bridges, it’s vital to control the volume of solder applied during the process.
Employing the right soldering techniques, such as precise temperature control and using appropriate soldering tips, can also help mitigate this issue.
Additionally, ensuring proper spacing between components on the PCB design can reduce the likelihood of solder bridges forming.
Cold Joints
Cold joints happen when solder fails to flow adequately between the component lead and the PCB pad.
This results in a weak connection that may not conduct electricity efficiently.
The primary reason for cold joints is insufficient heat at the solder joint.
Therefore, maintaining consistent and appropriate soldering temperatures is critical.
Using soldering irons with temperature control features and pre-heating the components can help prevent cold joints.
Additionally, using the right solder alloy and flux can ensure a smooth flow and solid connection.
Voids in Solder
Voids in the solder joint are small pockets of air or flux residue trapped within the joint.
While a certain amount of voiding is acceptable, excessive voids can weaken the solder joint and reduce heat dissipation.
To minimize voids, it is crucial to optimize the reflow soldering profile.
This involves carefully controlling the ramp-up, soak, and peak temperatures during the process.
Using appropriate solder paste with lower volatility and ensuring its even application can also help in reducing void formation.
Moreover, implementing effective cleaning processes before soldering can increase the joint’s reliability by removing contaminants that contribute to void formation.
The Importance of Environmental Control
The environment in which soldering takes place can significantly impact the quality of the solder joints.
Temperature, humidity, and dust levels all play a role in the formation of defects.
Maintaining a controlled environment within the manufacturing facility ensures that the soldering process is stable and reliable.
Having systems in place to monitor and adjust environmental conditions can reduce the risk of defects.
Furthermore, using soldering equipment with built-in controls and feedback mechanisms can ensure consistent performance.
Temperature
The ambient temperature in the manufacturing environment should be consistently controlled.
Sudden changes can affect the temperature of soldering equipment and, consequently, the soldering process.
A stable temperature environment helps maintain the viscosity of the solder paste, ensuring better flow and adhesion.
Humidity
Excessive humidity can lead to oxidation and moisture absorption, affecting the solderability of components.
Conversely, very low humidity can create static electricity issues.
Keeping humidity levels in check is important for achieving optimal solder joint quality.
Dust and Contaminants
Dust and other airborne contaminants can cause defects by introducing impurities onto the solder joint, leading to poor connectivity and reliability issues.
Regular cleaning and maintenance of the work environment are necessary to prevent contamination.
Enhancing Reliability Through Quality Control
Besides preventing defects, enhancing the reliability of soldered connections is equally crucial.
Implementing quality control measures throughout the soldering process can catch issues early and ensure that the product meets the desired standards.
Inspection and Testing
Visual inspection of the solder joints can help identify issues like cold joints and solder bridges early in the process.
Advanced techniques such as X-ray inspection can also be used to detect hidden defects like voids.
Regular electrical testing ensures that the circuit operates correctly before the product proceeds to the next manufacturing stage.
Reworking and Repairing
Despite precautions, defects can still occur.
Having efficient rework and repair processes in place can mitigate the impact of these defects on overall product reliability.
Reworking involves removing the defective solder joint and re-soldering it correctly.
This can restore functionality and prevent failures in the field.
However, reworking should be limited as it can introduce further reliability concerns if done excessively.
Conclusion
Preventing soldering defects and ensuring the reliability of electronic components are crucial steps in producing high-quality products.
By understanding common defects like solder bridges, cold joints, and voids, manufacturers can implement effective prevention strategies.
Additionally, maintaining a controlled environment and employing rigorous quality control measures can significantly enhance the reliability of soldered connections.
With these mechanisms in place, faulty soldering can be minimized, leading to safer, more reliable electronic products that meet the demands of today’s technology-driven world.
資料ダウンロード
QCD管理受発注クラウド「newji」は、受発注部門で必要なQCD管理全てを備えた、現場特化型兼クラウド型の今世紀最高の受発注管理システムとなります。
ユーザー登録
受発注業務の効率化だけでなく、システムを導入することで、コスト削減や製品・資材のステータス可視化のほか、属人化していた受発注情報の共有化による内部不正防止や統制にも役立ちます。
NEWJI DX
製造業に特化したデジタルトランスフォーメーション(DX)の実現を目指す請負開発型のコンサルティングサービスです。AI、iPaaS、および先端の技術を駆使して、製造プロセスの効率化、業務効率化、チームワーク強化、コスト削減、品質向上を実現します。このサービスは、製造業の課題を深く理解し、それに対する最適なデジタルソリューションを提供することで、企業が持続的な成長とイノベーションを達成できるようサポートします。
製造業ニュース解説
製造業、主に購買・調達部門にお勤めの方々に向けた情報を配信しております。
新任の方やベテランの方、管理職を対象とした幅広いコンテンツをご用意しております。
お問い合わせ
コストダウンが利益に直結する術だと理解していても、なかなか前に進めることができない状況。そんな時は、newjiのコストダウン自動化機能で大きく利益貢献しよう!
(β版非公開)