- お役立ち記事
- Mechanisms and countermeasures for plastic molding defects, prevention techniques, and their key points
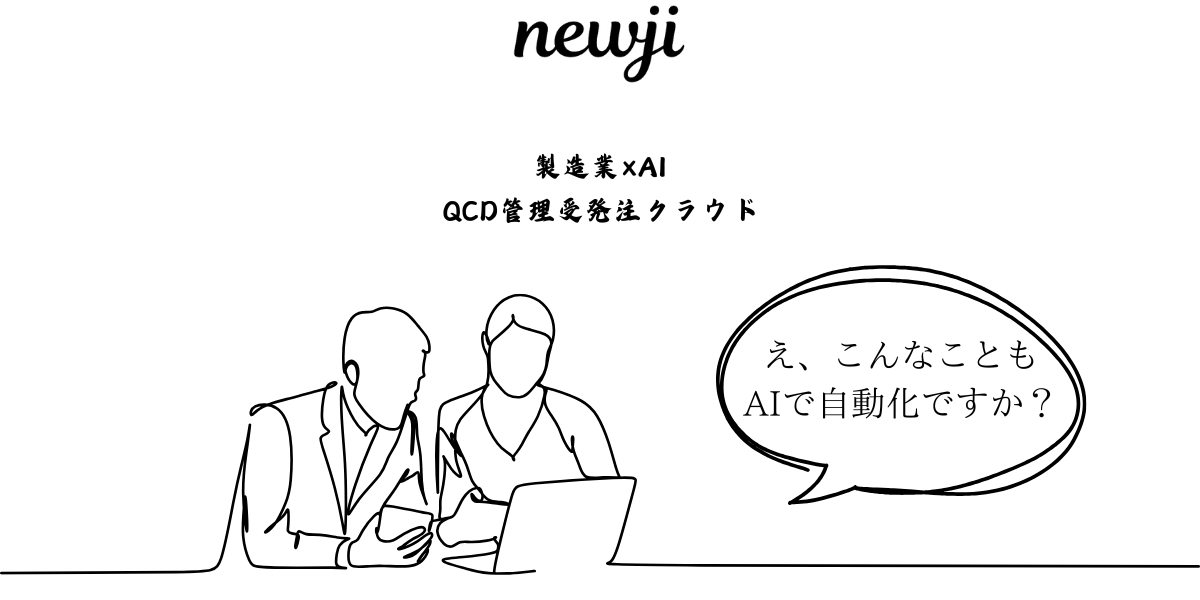
Mechanisms and countermeasures for plastic molding defects, prevention techniques, and their key points
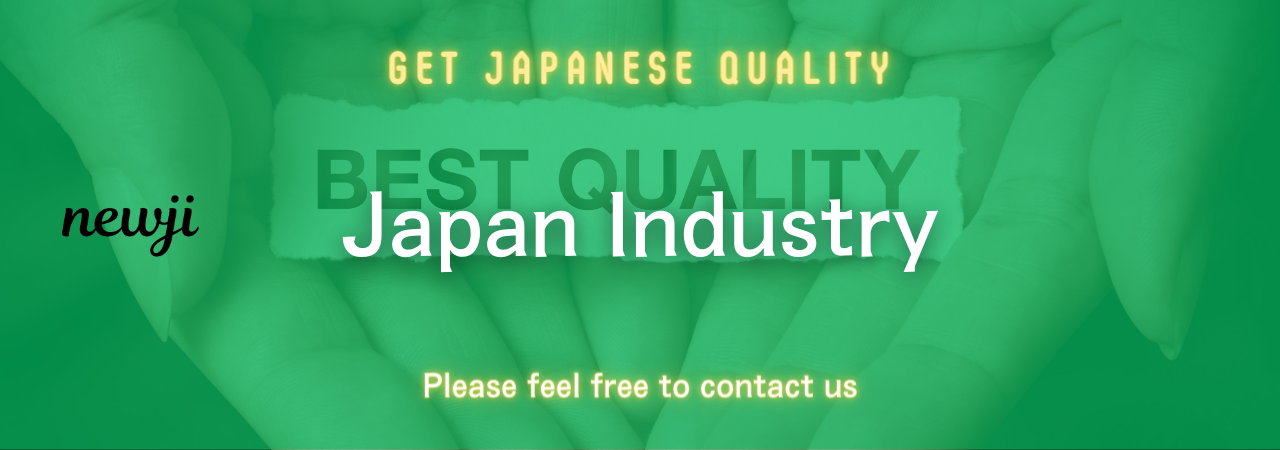
目次
Introduction to Plastic Molding Defects
Plastic molding is a widely used manufacturing process in which plastic materials are shaped into desired products.
Despite being highly efficient, this process is prone to defects that can affect the quality and functionality of the final product.
Understanding the mechanisms behind these defects and implementing preventive measures are crucial for maintaining high manufacturing standards.
Common Plastic Molding Defects
Several defects can occur during the plastic molding process, each with distinct characteristics.
Some of the most common defects include:
1. Warping
Warping is a distortion that occurs when different parts of a molded piece cool and contract at different rates.
This imbalance can lead to uneven surfaces and dimensions.
2. Sink Marks
These are small depressions formed when the inner parts of a molded product contract more than the outer layer.
This usually happens when the cooling process is not uniform.
3. Short Shots
A short shot occurs when the molten plastic does not completely fill the mold cavity.
This results in incomplete products with missing sections.
4. Flash
Flash is the excess plastic that escapes from the mold cavity and solidifies around the edges of the product.
This occurs when the mold does not close properly or if there is excessive injection pressure.
5. Burn Marks
Burn marks appear as black or brown spots on the surface of the molded product, often caused by trapped air or excessive heating of the plastic material.
Mechanisms Behind Plastic Molding Defects
Understanding the root causes of these defects is key to developing effective strategies for prevention and correction.
Material Issues
The choice and preparation of materials significantly impact the quality of the molded product.
Impurities, moisture content, or inappropriate material selection can lead to defects like sink marks and voids.
Process Parameters
Factors such as temperature, pressure, and cooling rate need precise control.
Incorrect setting of these parameters can lead to defects like warping and short shots.
Mold Design
The design of the mold itself plays a crucial role.
Inadequate venting and poor alignment can cause issues like flash and burn marks.
Machine Calibration
Machines that are not properly calibrated may apply incorrect pressure or temperature, increasing the likelihood of defects.
Countermeasures for Plastic Molding Defects
Implementing effective countermeasures can mitigate the occurrence of defects significantly.
Optimize Mold Design
Ensure that the mold design allows for even distribution of material and adequate venting to prevent air from being trapped.
Regular maintenance and precise machining are essential to avoid misalignment.
Control Process Parameters
Monitor and adjust parameters such as temperature, pressure, and cooling rates to match the material’s specifications.
Using advanced software aids in maintaining the optimal conditions required for defect-free molding.
Material Selection and Preparation
Choose materials that are suitable for the product’s intended use.
Properly dry the plastic materials before molding to eliminate moisture that can lead to defects like bubbles and burn marks.
Regular Machine Maintenance
Perform routine maintenance and calibration on all molding equipment.
Ensure that all machine parts are functional and precisely calibrated for each production run.
Prevention Techniques and Their Key Points
Being proactive is more effective than applying reactive measures.
Here’s how to be preventive rather than corrective:
Employee Training
Provide employees with adequate training on machinery operation and defect recognition.
Understanding potential defects helps in early detection and rectification.
Quality Control Systems
Implement robust quality control systems to inspect products at various stages of production.
Early identification of defects can save time and resources.
Data Monitoring and Analysis
Utilize data analytics to monitor production processes in real-time.
Analyzing trends and fluctuations in process parameters can pinpoint potential areas of improvement.
Conclusion
Plastic molding defects, while common, can be effectively prevented and corrected through a combination of sound material selection, precise process control, and regular maintenance.
Investing in preventive measures not only enhances the quality of the products but also boosts overall production efficiency and customer satisfaction.
資料ダウンロード
QCD調達購買管理クラウド「newji」は、調達購買部門で必要なQCD管理全てを備えた、現場特化型兼クラウド型の今世紀最高の購買管理システムとなります。
ユーザー登録
調達購買業務の効率化だけでなく、システムを導入することで、コスト削減や製品・資材のステータス可視化のほか、属人化していた購買情報の共有化による内部不正防止や統制にも役立ちます。
NEWJI DX
製造業に特化したデジタルトランスフォーメーション(DX)の実現を目指す請負開発型のコンサルティングサービスです。AI、iPaaS、および先端の技術を駆使して、製造プロセスの効率化、業務効率化、チームワーク強化、コスト削減、品質向上を実現します。このサービスは、製造業の課題を深く理解し、それに対する最適なデジタルソリューションを提供することで、企業が持続的な成長とイノベーションを達成できるようサポートします。
オンライン講座
製造業、主に購買・調達部門にお勤めの方々に向けた情報を配信しております。
新任の方やベテランの方、管理職を対象とした幅広いコンテンツをご用意しております。
お問い合わせ
コストダウンが利益に直結する術だと理解していても、なかなか前に進めることができない状況。そんな時は、newjiのコストダウン自動化機能で大きく利益貢献しよう!
(Β版非公開)