- お役立ち記事
- Mechanisms, examples, and countermeasures for forced vibration/self-excited vibration
月間76,176名の
製造業ご担当者様が閲覧しています*
*2025年3月31日現在のGoogle Analyticsのデータより
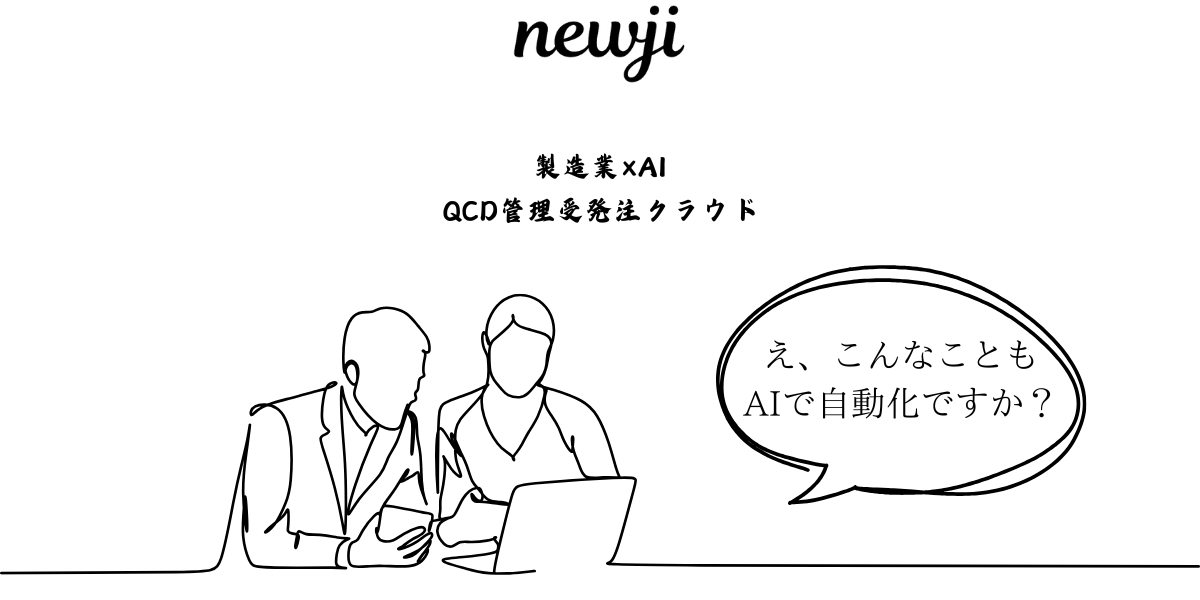
Mechanisms, examples, and countermeasures for forced vibration/self-excited vibration
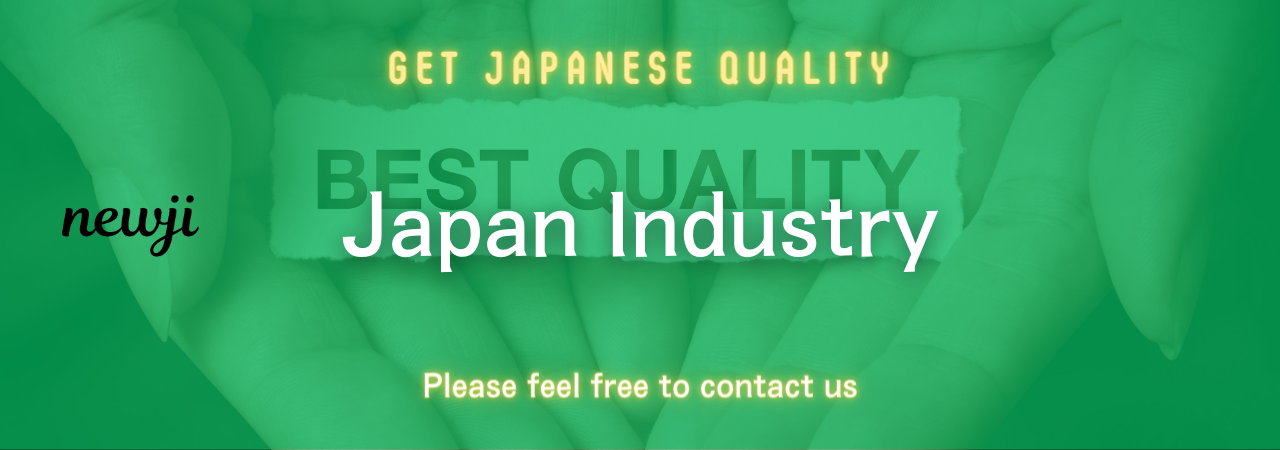
目次
Introduction to Vibrations
Vibrations are oscillations that occur due to mechanical movements and dynamic processes.
They can be classified into various types, with forced vibrations and self-excited vibrations being two important categories.
Understanding these vibrations is crucial in multiple fields such as engineering, physics, and construction, as they can significantly affect the safety and functionality of structures and systems.
What Are Forced Vibrations?
Forced vibrations happen when an external force drives a system to oscillate at specific frequencies.
This external force could be periodic, such as a sinusoidal force, or non-periodic.
In many mechanical systems, external inputs, such as motor imbalances or unbalanced rotating parts, cause these forced vibrations to occur.
Examples of Forced Vibrations
One common example of forced vibration is in vehicles where the engine’s vibrations propagate through the chassis.
These vibrations are often noticeable when the vehicle runs at specific speeds.
Another example is found in bridges.
When vehicles or pedestrians pass over, the bridge may experience rhythmic forces that cause it to vibrate.
Wind loads also serve as a source of forced vibrations in tall structures and bridges.
Impact of Forced Vibrations
Forced vibrations, if not appropriately managed, can lead to mechanical fatigue or failure over time.
In engines, they may cause parts to wear out prematurely or lead to noisy operations.
Structural integrity can be compromised in buildings and bridges if these vibrations are not controlled.
Understanding Self-Excited Vibrations
Unlike forced vibrations, self-excited vibrations occur without any external periodic force.
They are generated through the interaction of the system’s own dynamic parameters.
Typically, feedback mechanisms within the system lead to self-sustained oscillations.
Examples of Self-Excited Vibrations
A classic example of self-excited vibrations is the phenomenon of flutter in aircraft wings.
At particular airspeeds, the aerodynamic forces can cause the wing to oscillate, leading to potentially disastrous consequences.
In the field of engineering, another example is the phenomenon known as chatter in cutting tools.
During machining, the interaction between the cutting tool and the material can lead to self-sustained vibrations impacting surface finish and tool wear.
Impact of Self-Excited Vibrations
Self-excited vibrations can lead to increased noise, reduced accuracy, and even catastrophic failures in some cases.
In machine tools, they can severely affect the quality of the finished product or damage the equipment.
Countermeasures for Forced and Self-Excited Vibrations
Addressing and mitigating vibrations in mechanical systems and structures is essential to ensure durability, safety, and efficiency.
Counters for Forced Vibrations
1. **Damping and Isolation**: Introducing damping materials or vibration isolators can absorb or redirect the vibrational energy, thereby reducing its impact.
Common materials used include rubber mounts and springs.
2. **Balancing and Alignment**: Properly balancing rotating parts and ensuring correct alignment can significantly reduce forced vibrations.
Regular maintenance checks help in identifying and correcting imbalances.
3. **Active Control Systems**: Employing active vibration control systems that counteract vibrations in real-time can also be effective.
These systems use sensors and actuators to detect and neutralize unwanted oscillations.
Countermeasures for Self-Excited Vibrations
1. **Design Alterations**: Ensuring that the design of the system minimizes feedback loops that promote self-excited vibrations is crucial.
This includes altering geometries or changing natural frequencies to avoid resonance.
2. **Increased Damping**: Similar to forced vibrations, adding damping materials can suppress self-excited oscillations.
Enhanced damping can be particularly vital in structures like bridges or high-rise buildings.
3. **Stiffening Structures**: Altering the stiffness of components can also help in managing self-excited vibrations.
Stiffening reduces the flexibility of components and can help avoid conditions leading to these oscillations.
Conclusion
Understanding the nuances between forced and self-excited vibrations allows engineers and designers to predict and mitigate potential issues.
Whether through design adjustments, material selections, or active control systems, the right strategies can significantly enhance the longevity and performance of mechanical systems and structures.
Implementing these measures not only ensures safety but also leads to better functioning products and systems across various industries.
資料ダウンロード
QCD管理受発注クラウド「newji」は、受発注部門で必要なQCD管理全てを備えた、現場特化型兼クラウド型の今世紀最高の受発注管理システムとなります。
ユーザー登録
受発注業務の効率化だけでなく、システムを導入することで、コスト削減や製品・資材のステータス可視化のほか、属人化していた受発注情報の共有化による内部不正防止や統制にも役立ちます。
NEWJI DX
製造業に特化したデジタルトランスフォーメーション(DX)の実現を目指す請負開発型のコンサルティングサービスです。AI、iPaaS、および先端の技術を駆使して、製造プロセスの効率化、業務効率化、チームワーク強化、コスト削減、品質向上を実現します。このサービスは、製造業の課題を深く理解し、それに対する最適なデジタルソリューションを提供することで、企業が持続的な成長とイノベーションを達成できるようサポートします。
製造業ニュース解説
製造業、主に購買・調達部門にお勤めの方々に向けた情報を配信しております。
新任の方やベテランの方、管理職を対象とした幅広いコンテンツをご用意しております。
お問い合わせ
コストダウンが利益に直結する術だと理解していても、なかなか前に進めることができない状況。そんな時は、newjiのコストダウン自動化機能で大きく利益貢献しよう!
(β版非公開)