- お役立ち記事
- Mechanisms necessary for metal fatigue design and FEM analysis utilization methods
月間76,176名の
製造業ご担当者様が閲覧しています*
*2025年3月31日現在のGoogle Analyticsのデータより
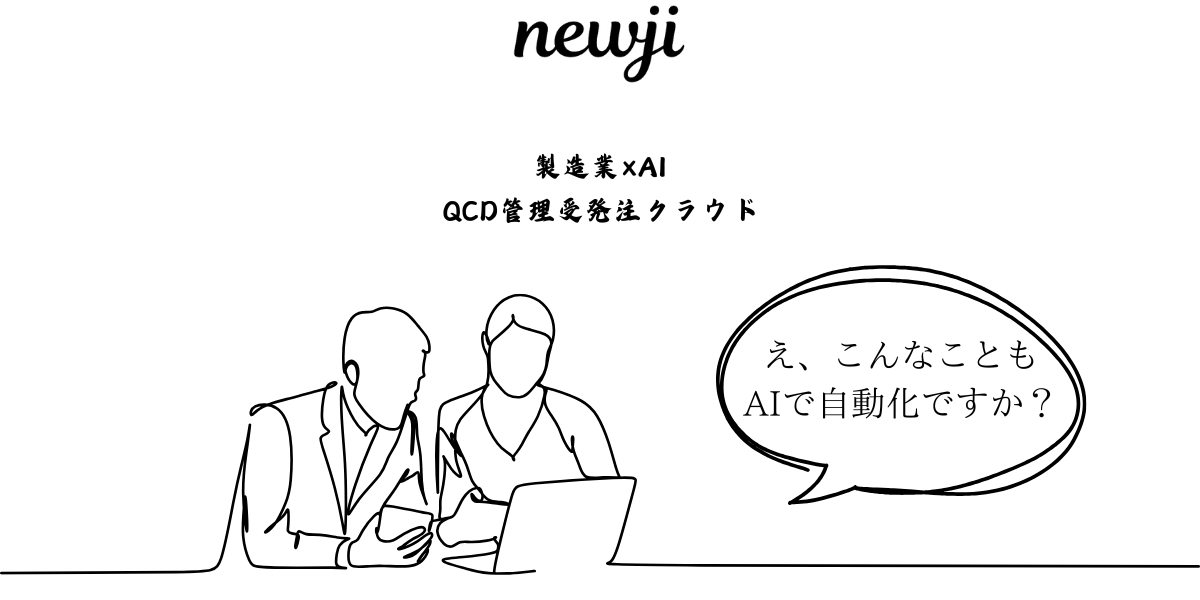
Mechanisms necessary for metal fatigue design and FEM analysis utilization methods
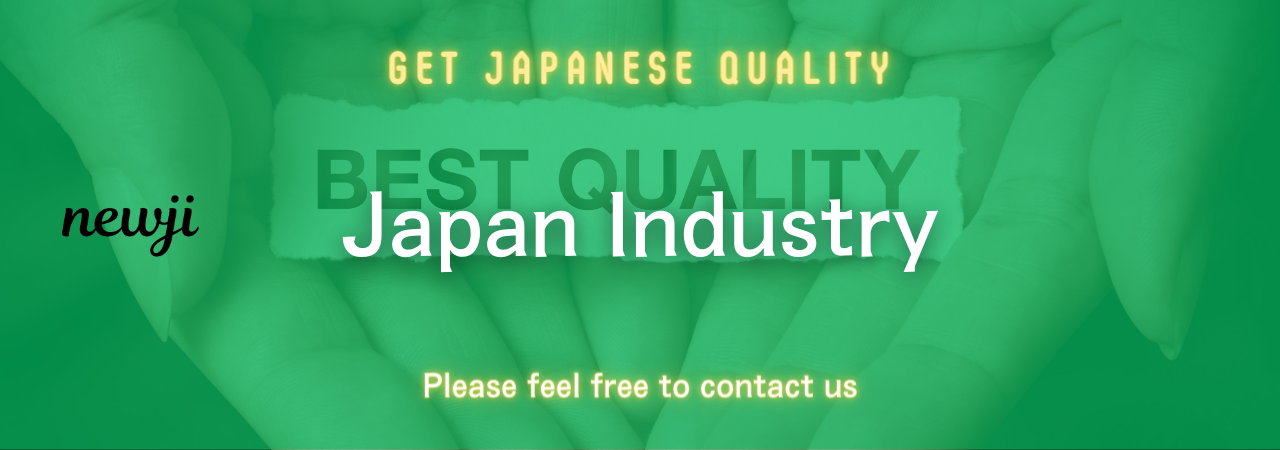
目次
Understanding Metal Fatigue
Metal fatigue is a critical concept in the design and analysis of engineering structures that experience cyclic loading.
When metal structures undergo fluctuating stresses, they can gradually weaken, leading to failure over time even if the stress levels are below the material’s yield strength.
Understanding this process is crucial in engineering to ensure the safety and longevity of metallic components in various applications, including automotive, aerospace, and construction industries.
The Causes of Metal Fatigue
Metal fatigue is primarily caused by repetitive stress cycles, leading to the initiation and propagation of microscopic cracks within the material.
These stresses can be due to mechanical load variations, thermal cycles, or other operational factors.
The fatigue process is typically divided into three stages: crack initiation, crack propagation, and final failure.
Identifying and predicting when and where these cracks will occur are vital aspects of fatigue design.
Factors Affecting Metal Fatigue
Several factors can influence the fatigue life of a metal component:
1. **Material Properties**: Different metals and alloys have varying resistance to fatigue based on their mechanical and microstructural characteristics.
2. **Stress Concentrations**: Notches, sharp corners, and other geometrical features can amplify stress, accelerating fatigue crack initiation.
3. **Surface Finish**: Smooth surfaces tend to have longer fatigue lives because surface irregularities can serve as crack initiation sites.
4. **Environment**: Corrosive environments can exacerbate fatigue processes, making environmental conditions an important consideration.
5. **Load Type and Frequency**: The magnitude, direction, and frequency of loads play significant roles in determining fatigue life.
Design Strategies to Mitigate Metal Fatigue
Employing effective design strategies is essential for mitigating the risk of metal fatigue in engineering components.
Here are some strategies that designers use:
Material Selection
Choosing the right material is the first step in combating metal fatigue.
Materials with high fatigue strength and good fracture toughness are generally preferred.
Engineers might also opt for specific alloys that have been designed to resist fatigue in particular environmental conditions.
Improved Geometry
By designing components with smoother transitions and avoiding sharp edges, stress concentrations can be minimized.
This geometry optimization can significantly enhance the fatigue life of a component.
Surface Treatments
Implementing surface treatments such as shot peening, polishing, or coating can enhance fatigue resistance.
These treatments work by reducing surface imperfections and inducing residual compressive stresses.
Fatigue Analysis and Testing
Conducting fatigue analysis and testing during the design phase can help predict failures and implement corrective measures.
Fatigue tests allow engineers to gather empirical data to refine their designs.
Leveraging FEM Analysis in Fatigue Design
Finite Element Method (FEM) analysis is a powerful computational tool used to predict and evaluate fatigue in metal structures.
This technique divides a large, complex problem into smaller, manageable elements, which make it easier to analyze stresses and strains across a structure.
Benefits of FEM in Fatigue Analysis
FEM provides several advantages when applied to fatigue analysis:
1. **Detailed Insights**: It offers a comprehensive view of stress distributions, pinpointing critical areas prone to fatigue.
2. **Simulation of Complex Geometries**: FEM can accurately model intricate shapes and complex assemblies that traditional methods may overlook.
3. **Efficient Iterations**: Designers can rapidly test different scenarios and load conditions, optimizing designs before manufacturing.
4. **Cost-Effectiveness**: By identifying potential failure points early, FEM reduces the need for costly physical prototypes and experiments.
Steps in FEM-Based Fatigue Analysis
To effectively utilize FEM in fatigue design, engineers typically follow these steps:
1. **Modeling**: Create a detailed finite element model of the structure, considering material properties and geometric details.
2. **Loading Conditions**: Define the load cases, which might include cyclic loads, static loads, and varied environmental factors.
3. **Boundary Conditions**: Apply constraints reflecting how the component would be supported or connected in real applications.
4. **Analysis**: Use FEM software to perform the detailed analysis, interpreting results to understand stress concentrations and potential fatigue zones.
5. **Validation**: Compare FEM results with experimental data or field observations to confirm accuracy and improve the model.
Integrating FEM with Other Design Tools
FEM is most effective when integrated with other design and analysis tools, creating a comprehensive approach to engineering problems.
Crack Growth Simulation
Advanced FEM techniques can simulate crack initiation and growth, allowing for proactive design changes.
These simulations can predict how cracks will propagate under varying load conditions, enabling the design of safer, more reliable structures.
Life Prediction Software
Combining FEM with life prediction software provides an overall assessment of component lifespan under cyclic loading.
This integration helps engineers to make informed decisions about maintenance schedules and replacement timelines.
Conclusion
Incorporating metal fatigue design principles and leveraging FEM analysis are paramount for designing robust and durable metal components.
By understanding the intricacies of metal fatigue and employing advanced computational tools, engineers can significantly enhance the safety, reliability, and efficiency of engineering systems.
With continued advancements in simulation technologies, the future of fatigue analysis and design looks promising, paving the way for innovative solutions in engineering design and safety.
資料ダウンロード
QCD管理受発注クラウド「newji」は、受発注部門で必要なQCD管理全てを備えた、現場特化型兼クラウド型の今世紀最高の受発注管理システムとなります。
ユーザー登録
受発注業務の効率化だけでなく、システムを導入することで、コスト削減や製品・資材のステータス可視化のほか、属人化していた受発注情報の共有化による内部不正防止や統制にも役立ちます。
NEWJI DX
製造業に特化したデジタルトランスフォーメーション(DX)の実現を目指す請負開発型のコンサルティングサービスです。AI、iPaaS、および先端の技術を駆使して、製造プロセスの効率化、業務効率化、チームワーク強化、コスト削減、品質向上を実現します。このサービスは、製造業の課題を深く理解し、それに対する最適なデジタルソリューションを提供することで、企業が持続的な成長とイノベーションを達成できるようサポートします。
製造業ニュース解説
製造業、主に購買・調達部門にお勤めの方々に向けた情報を配信しております。
新任の方やベテランの方、管理職を対象とした幅広いコンテンツをご用意しております。
お問い合わせ
コストダウンが利益に直結する術だと理解していても、なかなか前に進めることができない状況。そんな時は、newjiのコストダウン自動化機能で大きく利益貢献しよう!
(β版非公開)