- お役立ち記事
- Mechanisms of fracture and environmental stress cracking in plastic molded products and key points for troubleshooting
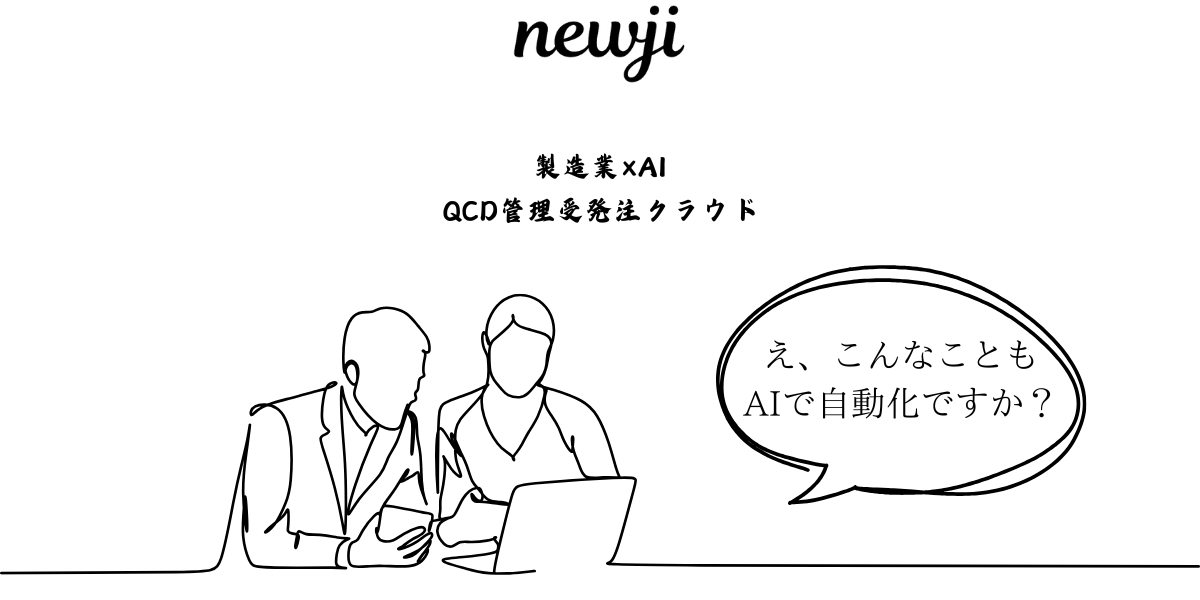
Mechanisms of fracture and environmental stress cracking in plastic molded products and key points for troubleshooting
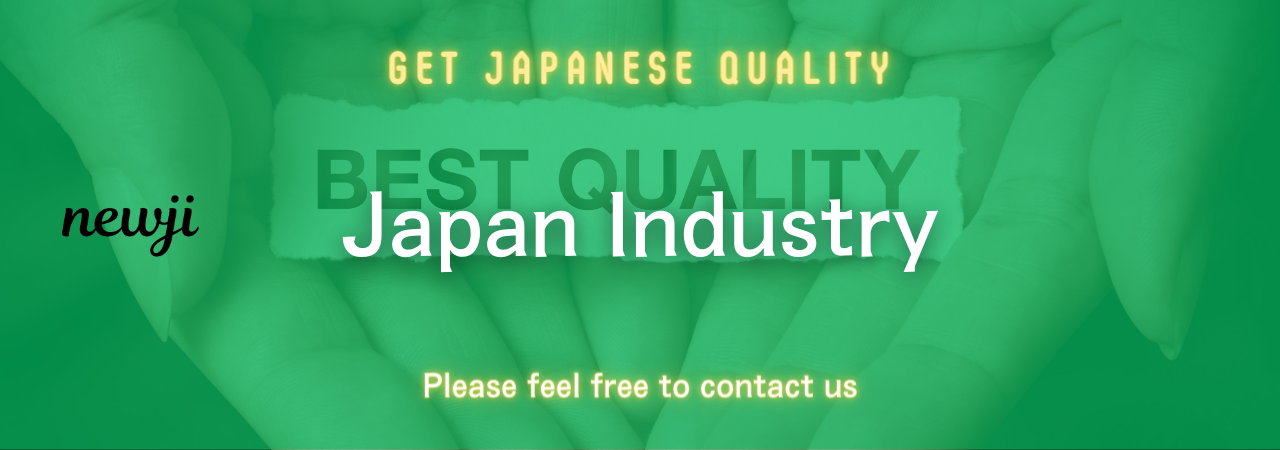
目次
Introduction to Plastic Fracture and Stress Cracking
Plastic molded products are an essential part of everyday life, found in everything from household items to industrial machinery.
However, despite their durability, they are not immune to damage.
Two specific challenges they face are fracture and environmental stress cracking (ESC).
Understanding these phenomena and how to troubleshoot them is crucial for manufacturers and consumers alike.
The Basics of Plastic Fracture
The fracture of plastic products occurs when the material fails under stress.
This can happen instantly or over time, depending on the type and the conditions to which the plastic is exposed.
Plastic fracture is primarily influenced by three factors: the physical properties of the plastic, the design of the product, and the environment in which the product is used.
Types of Plastic Fracture
There are primarily two types of fracture in plastics: ductile and brittle.
A ductile fracture is characterized by significant deformation before breaking, often resulting in a stretched or deformed product.
On the other hand, brittle fracture happens suddenly with little to no prior deformation, leading to a sharp and clean break.
Understanding whether a product is prone to ductile or brittle fracture is essential in selecting the right material and design for its intended use.
Environmental Stress Cracking (ESC)
Environmental stress cracking is a type of failure that occurs when the plastic is exposed to stress and environmental factors.
These can include chemicals, humidity, and temperature extremes.
Unlike mechanical stress, ESC is significantly affected by the environment surrounding the plastic product.
This phenomenon is particularly problematic because it can damage plastics even when they do not appear to be under any measurable mechanical stress.
How ESC Occurs
ESC begins at the microscopic level when external environmental factors weaken the molecular bonds within the plastic.
Over time, these weakened bonds become areas of weakness that can eventually form cracks.
The presence of certain chemicals can accelerate this process, as some plastics are particularly sensitive to solvents, oils, and detergents.
Detecting ESC
Detecting environmental stress cracking before it leads to major failure is crucial.
Early signs include surface crazing, a network of fine cracks that may be visible under magnification.
Regular inspections and monitoring can help in catching these issues early.
If detected, steps can be taken to alter environmental conditions or choose a different plastic material less susceptible to ESC.
Factors Contributing to Fracture and ESC
Material Selection
One of the first lines of defense against fracture and ESC is selecting the correct material from the start.
Different plastics have varying resistance to mechanical and environmental stress.
Polyethylene, for example, is known for its chemical resistance, while polycarbonate offers high impact resistance but is more susceptible to certain chemicals.
Choosing the appropriate type of plastic for the product’s intended environment simplifies later troubleshooting and maintenance.
Manufacturing Process
The way a plastic product is manufactured also affects its susceptibility to fracture and ESC.
Processes such as injection molding, extrusion, and blow molding can introduce varying levels of stress during production.
Managing these stresses to ensure even distribution throughout the plastic is vital for long-term durability.
Manufacturer quality control plays a key role here in detecting and preventing these issues before products leave the factory.
Product Design
Design plays a significant role in a product’s resilience.
Sharp corners, high-stress concentration points, and inconsistent wall thickness can all predispose a plastic product to stress cracking.
By using advanced computer-aided design (CAD) tools, designers can anticipate areas of weakness and redesign those elements to improve resilience.
Balancing aesthetics with functional durability is essential in product design.
Troubleshooting Fracture and ESC Issues
Assessment of Environmental Conditions
The first step in troubleshooting is assessing the environment in which the product is used.
If the environment is too harsh or incompatible with the selected type of plastic, steps need to be taken to either change the environment or switch to a more suitable material.
This may involve controlling temperature fluctuations, reducing chemical exposure, or selecting a different plastic blend.
Improving Material Selection
When existing materials are consistently breaking or cracking, consider utilizing more advanced or composite materials.
These materials are engineered to withstand specific stresses and environmental conditions.
Advancements in polymer science continually introduce new options that can replace traditional plastics, mitigating the risk of fracture and ESC.
Enhancing Manufacturing Practices
Improving manufacturing processes can also alleviate issues related to stress.
Implementing better quality control measures during production will help in detecting internal faults before they become issues.
Techniques like ultrasonic testing and thermal imaging can be used to inspect products without damaging them.
Design Revisions
If design flaws contribute to product failure, redesigning the affected areas may be necessary.
Alterations like rounding out sharp corners, reinforcing weak areas, or uniformly distributing material thickness can significantly improve a product’s durability.
These revisions help in preventing areas of high stress concentration, which are often the starting points for fractures and cracks.
Conclusion
Understanding the mechanisms of fracture and environmental stress cracking in plastic molded products is critical for longevity and reliability.
By considering factors such as material selection, manufacturing processes, and product design, manufacturers can mitigate risks.
Effective troubleshooting requires a comprehensive approach that acknowledges the complex interactions between these factors and the prevailing environmental conditions.
With these strategies, the resilience of plastic products can be significantly enhanced, extending their useful life and improving user satisfaction.
資料ダウンロード
QCD調達購買管理クラウド「newji」は、調達購買部門で必要なQCD管理全てを備えた、現場特化型兼クラウド型の今世紀最高の購買管理システムとなります。
ユーザー登録
調達購買業務の効率化だけでなく、システムを導入することで、コスト削減や製品・資材のステータス可視化のほか、属人化していた購買情報の共有化による内部不正防止や統制にも役立ちます。
NEWJI DX
製造業に特化したデジタルトランスフォーメーション(DX)の実現を目指す請負開発型のコンサルティングサービスです。AI、iPaaS、および先端の技術を駆使して、製造プロセスの効率化、業務効率化、チームワーク強化、コスト削減、品質向上を実現します。このサービスは、製造業の課題を深く理解し、それに対する最適なデジタルソリューションを提供することで、企業が持続的な成長とイノベーションを達成できるようサポートします。
オンライン講座
製造業、主に購買・調達部門にお勤めの方々に向けた情報を配信しております。
新任の方やベテランの方、管理職を対象とした幅広いコンテンツをご用意しております。
お問い合わせ
コストダウンが利益に直結する術だと理解していても、なかなか前に進めることができない状況。そんな時は、newjiのコストダウン自動化機能で大きく利益貢献しよう!
(Β版非公開)