- お役立ち記事
- Mechanisms of fracture/environmental stress cracking in plastic molded products and points for dealing with breakage problems
Mechanisms of fracture/environmental stress cracking in plastic molded products and points for dealing with breakage problems
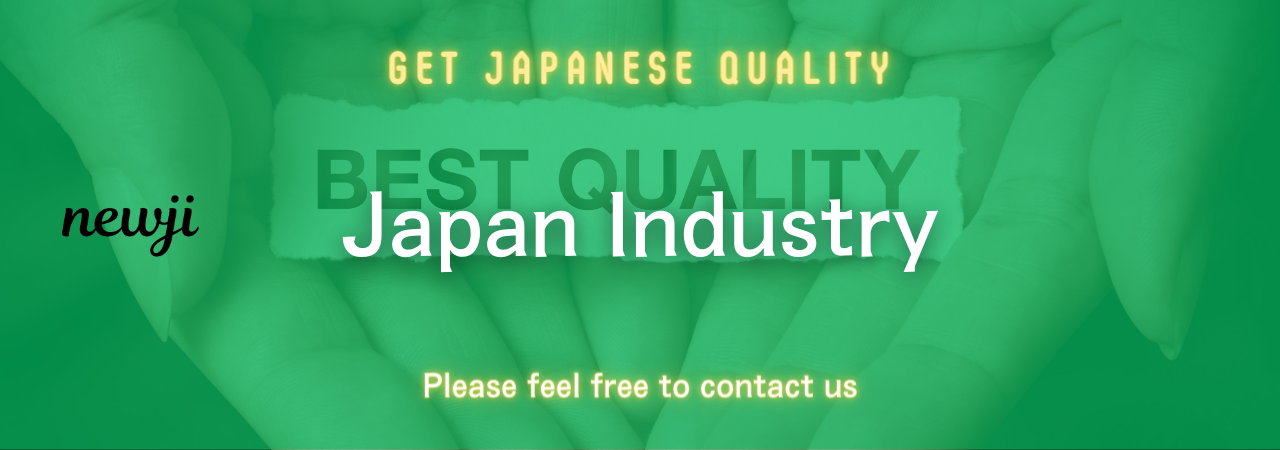
目次
Understanding Fracture Mechanisms in Plastic Molded Products
Plastic molded products are widely used across various industries due to their versatility, durability, and lightweight nature.
However, like any other material, plastics are prone to fracture under certain conditions.
Understanding the mechanisms behind these fractures is crucial for improving product design, enhancing durability, and preventing potential failures.
A fracture in plastic materials can occur due to various reasons, including mechanical stress, impact, environmental factors, or a combination of these.
Among the different types of fractures, environmental stress cracking (ESC) is a common issue that manufacturers face.
This phenomenon involves the formation of cracks in plastic materials when exposed to specific environmental conditions and mechanical loads.
Factors Contributing to Fracture
1. **Material Composition:**
The composition of the plastic, including its polymer structure and any additives, significantly affects its susceptibility to fracture.
Plastics with a higher molecular weight or those with reinforcing fillers typically exhibit better resistance to cracking.
2. **Manufacturing Process:**
The methods used in the molding process, such as injection molding or extrusion, can impact the mechanical properties of the finished product.
Factors such as cooling rates, molding pressure, and residual stresses introduced during manufacturing play a critical role in determining fracture behavior.
3. **Mechanical Stress:**
Excessive mechanical loads or repetitive stresses can introduce cracks in plastic products.
This is commonly seen in products subjected to high-impact forces or those that undergo frequent bending or stretching.
4. **Environmental Conditions:**
Conditions such as temperature fluctuations, UV exposure, and contact with chemicals can accelerate the degradation of plastic materials.
These factors can lead to embrittlement, which increases the likelihood of fracture.
What is Environmental Stress Cracking (ESC)?
Environmental Stress Cracking (ESC) is a specific type of fracture that occurs when a plastic material is exposed to chemical agents or specific environmental conditions.
This leads to the weakening of the material, resulting in the formation of cracks under stress.
ESC is particularly problematic because it can occur even under relatively low mechanical loads.
The process involves the absorption of certain chemicals or solvents by the plastic, which causes plasticization or swelling.
This reduces the intermolecular forces within the material, making it more susceptible to stress-induced cracking.
Common Triggers for ESC
1. **Chemical Exposure:**
Certain chemicals, such as oils, detergents, or industrial solvents, can penetrate the plastic and initiate stress cracking.
The chemical structure of the plastic determines its sensitivity to different agents.
2. **Temperature Variations:**
Extreme temperatures, whether high or low, can alter the mechanical properties of plastics.
This makes them more vulnerable to cracking when subjected to stress.
3. **Humidity and Moisture:**
Some plastics can absorb water, leading to swelling and increased internal stresses.
This is particularly true for hygroscopic materials, such as nylon.
Preventing and Managing Fracture Issues
Addressing fracture issues in plastic molded products requires a comprehensive understanding of the material properties, environmental conditions, and the specific application of the product.
Here are some strategies to prevent and manage fracture problems effectively:
Material Selection
Choosing the right material for a specific application is crucial.
Engineers should consider factors such as mechanical strength, impact resistance, and environmental compatibility.
Opting for materials with additives that enhance resistance to UV light or chemicals can also be beneficial.
Design Considerations
Product design plays a significant role in preventing fractures.
Incorporating features like radiused corners instead of sharp edges, uniform wall thickness, and reinforcements can help distribute stress more evenly, reducing the risk of breakage.
Optimizing Manufacturing Processes
Fine-tuning the manufacturing process can help minimize residual stresses and defects that contribute to fracture.
This includes control over parameters like cooling rates, molding cycle times, and pressure settings.
Regular Testing and Inspection
Implementing a regular testing and inspection routine can help identify potential fracture points before a product fails.
Non-destructive testing methods, such as ultrasonic testing or X-ray inspection, can be used to detect internal defects or areas of high stress concentration.
Environmental Protection
Applying protective coatings or barriers can shield plastics from harmful environmental factors, such as UV radiation or chemical exposure.
For certain applications, selecting environments that minimize contact with aggressive chemicals is vital for long-term durability.
Addressing Fracture Problems in Existing Products
If a fracture issue arises in an existing plastic product, a systematic approach is essential to address and mitigate the problem.
Here are some steps to consider:
Root Cause Analysis
Conducting a thorough investigation to identify the underlying cause of the fracture is crucial.
This may involve mechanical testing, chemical analysis, and reviewing the product’s history and usage conditions.
Redesign or Material Change
Based on the findings of the root cause analysis, it may be necessary to redesign the product or switch to a more suitable material that can withstand the operating conditions.
Monitoring and Feedback
Implement a feedback mechanism to monitor the performance of the revised product in the field.
This will help track improvements and identify further areas for enhancement.
Conclusion
Understanding the mechanisms of fracture, particularly environmental stress cracking, in plastic molded products is essential for preventing product failures and enhancing longevity.
By carefully selecting materials, optimizing design, and considering environmental conditions, manufacturers can significantly reduce the risk of fractures.
Additionally, a proactive approach to testing and inspecting products can help identify potential issues before they escalate, ensuring reliable and safe products for consumers.
資料ダウンロード
QCD調達購買管理クラウド「newji」は、調達購買部門で必要なQCD管理全てを備えた、現場特化型兼クラウド型の今世紀最高の購買管理システムとなります。
ユーザー登録
調達購買業務の効率化だけでなく、システムを導入することで、コスト削減や製品・資材のステータス可視化のほか、属人化していた購買情報の共有化による内部不正防止や統制にも役立ちます。
NEWJI DX
製造業に特化したデジタルトランスフォーメーション(DX)の実現を目指す請負開発型のコンサルティングサービスです。AI、iPaaS、および先端の技術を駆使して、製造プロセスの効率化、業務効率化、チームワーク強化、コスト削減、品質向上を実現します。このサービスは、製造業の課題を深く理解し、それに対する最適なデジタルソリューションを提供することで、企業が持続的な成長とイノベーションを達成できるようサポートします。
オンライン講座
製造業、主に購買・調達部門にお勤めの方々に向けた情報を配信しております。
新任の方やベテランの方、管理職を対象とした幅広いコンテンツをご用意しております。
お問い合わせ
コストダウンが利益に直結する術だと理解していても、なかなか前に進めることができない状況。そんな時は、newjiのコストダウン自動化機能で大きく利益貢献しよう!
(Β版非公開)