- お役立ち記事
- Mechanisms of friction and wear and points for improving wear resistance
Mechanisms of friction and wear and points for improving wear resistance
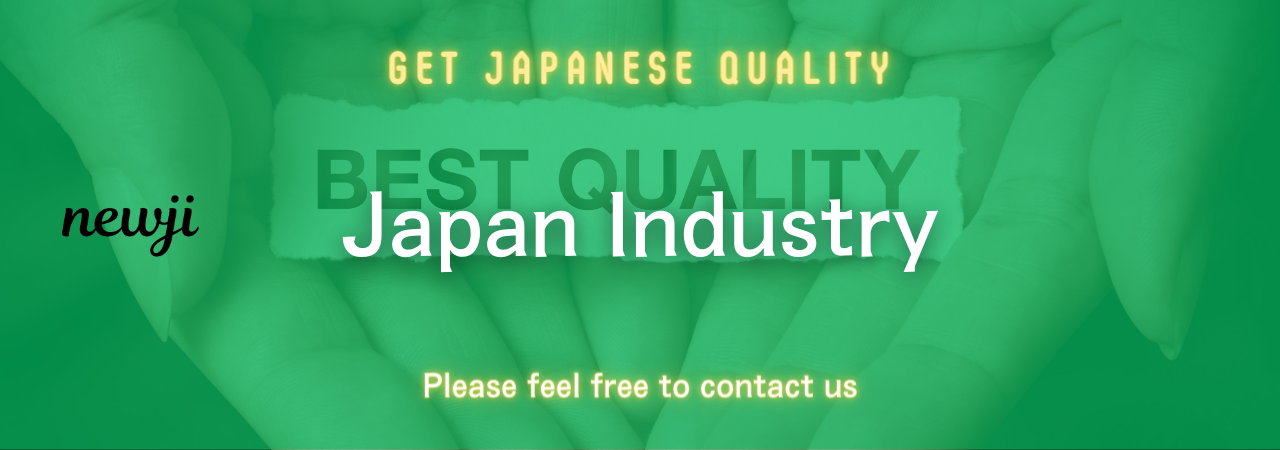
目次
Understanding Friction and Its Mechanisms
Friction is a common physical phenomenon that we encounter in our daily lives.
It is the resistance that one surface or object encounters when moving over another.
The understanding of friction is crucial in numerous applications ranging from simple machinery to sophisticated vehicles.
At its core, friction occurs due to the interactions between surface irregularities of two contacting materials.
When these surfaces move relative to each other, these irregularities interlock and create resistance.
Though friction is necessary for tasks like walking or driving, it also leads to wear and tear, which can be detrimental to equipment longevity.
Types of Friction
Friction manifests in several forms, primarily static, kinetic, and rolling friction.
Static friction acts on objects that are not moving.
It must be overcome to initiate movement.
Kinetic friction, on the other hand, occurs when objects slide past each other and is typically less than static friction.
Rolling friction is experienced by objects that roll, like wheels, and is generally smaller than kinetic friction.
Each type of friction has its unique properties and implications for wear.
The Science of Wear
Wear, the gradual removal or deformation of material at solid surfaces, is a result of mechanical action.
It encompasses several complex processes that alter the surface properties of materials.
Wear can be divided into different categories, including adhesive wear, abrasive wear, fatigue wear, and corrosive wear.
Adhesive Wear
Adhesive wear happens when materials adhere to each other’s surfaces and transfer between them as they move.
This typically occurs under high pressures and temperatures, where surface material can easily weld together and be torn apart.
Abrasive Wear
Abrasive wear occurs when hard particles or rough surfaces slide against softer surfaces, leading to material loss.
It’s similar to a grinding action and is a major concern in industries like mining and construction, where equipment operates in harsh conditions.
Fatigue Wear
Fatigue wear results from cyclic stress on a material.
Over time, repeated mechanical loading leads to the initiation and propagation of cracks until the material fails.
Improving Wear Resistance
Endeavoring to enhance wear resistance can extend the service lives of components, save costs, and improve efficiency.
Various techniques can be employed to reduce wear and improve the reliability of mechanical systems.
Material Selection
Choosing the right material is fundamental to improving wear resistance.
Materials with inherent hardness or those that can be surface-treated for enhancement are often preferred.
The use of alloys, composite materials, and ceramics can provide significant benefits due to their robust wear properties.
Surface Coating
Coating a surface with a more durable material can effectively reduce wear.
Techniques like electroplating, thermal spraying, and chemical vapor deposition (CVD) coat surfaces with protective layers that resist wear better than the original material.
Lubrication
Lubricants are applied to surfaces to minimize direct contact and reduce friction.
They form a film that separates the surfaces, thereby reducing wear.
Lubrication can also help manage the heat produced by friction.
Design Considerations for Wear Resistance
Design plays a critical role in mitigating wear.
Engineers should consider factors like load distribution, surface finish, and fit in the design phase to enhance durability.
Load Distribution
Distributing loads across a larger surface area reduces the pressure at any given point, lessening wear.
This can be achieved by increasing bearing surfaces or incorporating support structures.
Surface Finish
A smoother surface helps reduce the friction between contacting parts.
Machining, grinding, and polishing can achieve desired surface finishes that minimize wear.
Mechanical Fit
Proper fitting of parts ensures that excessive vibrations and misalignments, which contribute to wear, are avoided.
Utilizing design techniques that ensure precise tolerances and alignments is essential.
Conclusion
Understanding the mechanisms of friction and wear is key to improving the service life of products and machinery.
By selecting appropriate materials, utilizing surface coatings, incorporating effective lubrication, and considering design implications, wear resistance can be significantly enhanced.
Employing these strategies not only ensures better performance but also contributes to cost-efficiency and sustainability in mechanical systems.
資料ダウンロード
QCD調達購買管理クラウド「newji」は、調達購買部門で必要なQCD管理全てを備えた、現場特化型兼クラウド型の今世紀最高の購買管理システムとなります。
ユーザー登録
調達購買業務の効率化だけでなく、システムを導入することで、コスト削減や製品・資材のステータス可視化のほか、属人化していた購買情報の共有化による内部不正防止や統制にも役立ちます。
NEWJI DX
製造業に特化したデジタルトランスフォーメーション(DX)の実現を目指す請負開発型のコンサルティングサービスです。AI、iPaaS、および先端の技術を駆使して、製造プロセスの効率化、業務効率化、チームワーク強化、コスト削減、品質向上を実現します。このサービスは、製造業の課題を深く理解し、それに対する最適なデジタルソリューションを提供することで、企業が持続的な成長とイノベーションを達成できるようサポートします。
オンライン講座
製造業、主に購買・調達部門にお勤めの方々に向けた情報を配信しております。
新任の方やベテランの方、管理職を対象とした幅広いコンテンツをご用意しております。
お問い合わせ
コストダウンが利益に直結する術だと理解していても、なかなか前に進めることができない状況。そんな時は、newjiのコストダウン自動化機能で大きく利益貢献しよう!
(Β版非公開)