- お役立ち記事
- Mechanisms of friction and wear, wear reduction technology and applications
Mechanisms of friction and wear, wear reduction technology and applications
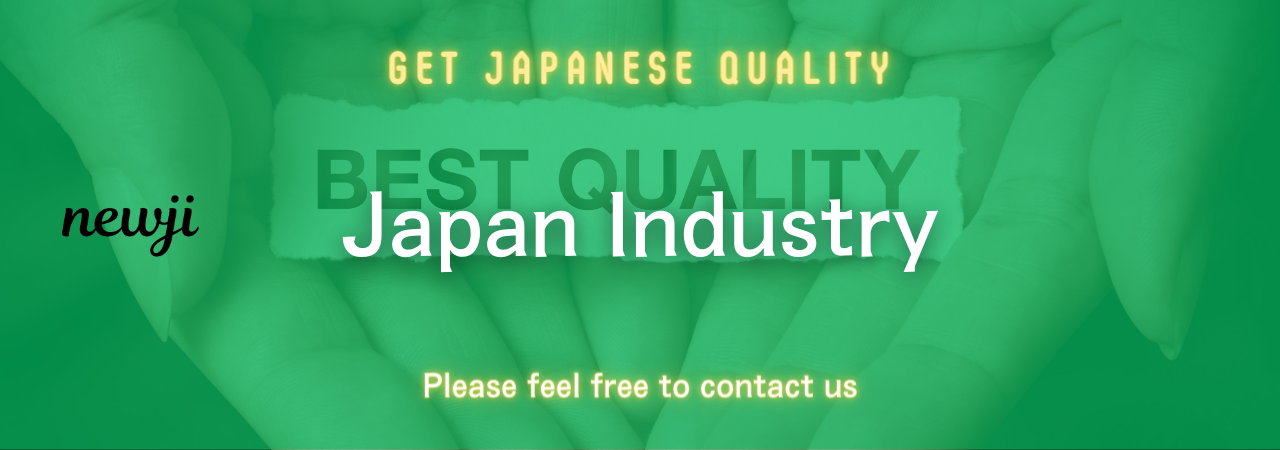
目次
Understanding Friction and Wear
Friction and wear are everyday phenomena that occur when two surfaces come into contact and move against each other.
These processes can lead to the gradual degradation of materials, impacting their performance and longevity.
Understanding the mechanisms behind friction and wear is crucial for developing technologies that can reduce their detrimental effects.
Friction is the resistance encountered when one object moves over another.
It is caused by the interactions between surface asperities, which are the microscopic high points found on material surfaces.
The level of friction depends on several factors, including the nature of the materials in contact, surface roughness, and the presence of lubricants or contaminants.
Wear, on the other hand, refers to the removal of material from a solid surface due to mechanical action.
It can result from abrasion, adhesion, fatigue, or corrosion.
Abrasion occurs when a hard rough surface slides across a softer one, leading to material loss.
Adhesion involves the bonding of materials at their surfaces, which can also lead to wear when they are pulled apart.
Types and Causes of Wear
Wear can be categorized into different types based on how it occurs.
Each type has distinct characteristics and causes, and understanding them can aid in selecting appropriate wear reduction strategies.
Abrasion
Abrasion is the most common form of wear and occurs when harder materials scratch against softer surfaces.
It is often caused by external particles introduced to the system or by surface roughness.
Industries such as mining, agriculture, and manufacturing often experience abrasion wear due to the constant presence of dirt, dust, and debris.
Adhesion
Adhesive wear occurs when two surfaces come into intimate contact, causing material transfer from one surface to another.
This can happen due to molecular interaction between the surfaces or when micro-welded junctions form and break as they slide past each other.
Adhesive wear is prevalent in industries that require precise movement like robotics and precision tooling.
Fatigue
Fatigue wear is the result of repetitive stress cycles that lead to material failure over time.
This can occur in mechanical components subjected to consistent loading and unloading, like gears and bearings in automotive applications.
The material eventually weakens, leading to cracks and surface degradation.
Corrosion
Corrosion wear involves chemical reactions between the surface material and the environment, leading to material removal.
This type of wear is intensified in harsh environmental conditions with exposure to moisture, chemicals, or extreme temperatures.
Pipelines, marine equipment, and outdoor structures are commonly affected by corrosion wear.
Technologies for Reducing Friction and Wear
Reducing friction and wear is fundamental in enhancing the efficiency and lifespan of machinery and devices.
Several advanced technologies have been developed to combat these challenges.
Lubrication
Lubrication involves applying a substance that reduces friction and wear between surfaces in contact.
Lubricants create a thin film that separates the surfaces and minimizes direct contact.
Depending on the application, lubricants can be liquids, greases, or solid coatings.
In engines, for instance, oil serves to reduce frictional forces, improving performance and efficiency.
Surface Coatings
Applying specialized coatings to surfaces can enhance their resistance to wear.
These coatings are designed to endure harsh conditions and protect the underlying material.
Common coatings include ceramics, chrome, and diamond-like carbon (DLC), each offering unique properties for various applications.
Coatings are particularly useful in fields like aerospace and biomedical engineering, where material integrity is critical.
Material Selection
Selecting the right materials for specific applications can significantly reduce wear.
Advanced materials, including ceramics, composites, and alloys, offer enhanced wear resistance and durability.
In high-stress environments, such as military and space exploration, materials are chosen based on their ability to withstand abrasion, adhesion, and fatigue.
Design Optimization
Optimized design can help minimize wear by distributing loads evenly and reducing stress concentrations on surfaces.
Using computational modeling, engineers can simulate wear conditions and design components that reduce contact pressures and surface degradation.
For example, in automotive engineering, design changes to engine components can lead to improved fuel efficiency and reduced maintenance costs.
Applications of Wear Reduction Technologies
Wear reduction technologies have diverse applications across various industries, enhancing performance and sustainability.
Automotive Industry
In the automotive industry, reducing wear is critical to improving fuel efficiency and extending vehicle lifespan.
Advanced lubricants, surface coatings, and precision-engineered components help minimize friction and wear in engines, transmissions, and braking systems.
This leads to lower emissions, better mileage, and decreased maintenance costs for consumers.
Manufacturing
Manufacturing equipment often experiences abrasive wear due to constant contact with raw materials.
Implementing wear-resistant materials and coatings in tooling, machinery, and conveyor systems extends their usage life and improves productivity.
Lubrication systems are also integral in reducing downtime and ensuring smooth operation throughout the manufacturing process.
Medical Devices
In the medical field, implants and prosthetics must withstand bodily fluids and mechanical stressors without succumbing to wear.
Biocompatible coatings and advanced materials are necessary to ensure durability and safety.
For instance, hip implants are designed using wear-resistant ceramics and polymers to prolong their functionality inside the body.
Energy Sector
Energy generation and transmission systems are prone to wear from high operational demands and harsh environmental conditions.
In wind turbines, for example, lubricants and coatings are employed to reduce wear on bearings and gearboxes, ensuring reliable performance and reducing maintenance costs.
Similarly, pipelines use corrosion-resistant coatings to prevent wear and protect against environmental damage.
Conclusion
The implications of friction and wear extend across industries, affecting the performance, efficiency, and cost-effectiveness of various systems and devices.
By understanding the mechanisms of wear and implementing advanced reduction technologies such as lubrication, coatings, and material innovations, industries can enhance durability and sustainability.
As technological progress continues, the development of even more effective methods to combat friction and wear will play a crucial role in the advancement of modern engineering and manufacturing practices.
資料ダウンロード
QCD調達購買管理クラウド「newji」は、調達購買部門で必要なQCD管理全てを備えた、現場特化型兼クラウド型の今世紀最高の購買管理システムとなります。
ユーザー登録
調達購買業務の効率化だけでなく、システムを導入することで、コスト削減や製品・資材のステータス可視化のほか、属人化していた購買情報の共有化による内部不正防止や統制にも役立ちます。
NEWJI DX
製造業に特化したデジタルトランスフォーメーション(DX)の実現を目指す請負開発型のコンサルティングサービスです。AI、iPaaS、および先端の技術を駆使して、製造プロセスの効率化、業務効率化、チームワーク強化、コスト削減、品質向上を実現します。このサービスは、製造業の課題を深く理解し、それに対する最適なデジタルソリューションを提供することで、企業が持続的な成長とイノベーションを達成できるようサポートします。
オンライン講座
製造業、主に購買・調達部門にお勤めの方々に向けた情報を配信しております。
新任の方やベテランの方、管理職を対象とした幅広いコンテンツをご用意しております。
お問い合わせ
コストダウンが利益に直結する術だと理解していても、なかなか前に進めることができない状況。そんな時は、newjiのコストダウン自動化機能で大きく利益貢献しよう!
(Β版非公開)