- お役立ち記事
- Mechanisms of friction and wear, wear reduction technology and applications
月間77,185名の
製造業ご担当者様が閲覧しています*
*2025年2月28日現在のGoogle Analyticsのデータより
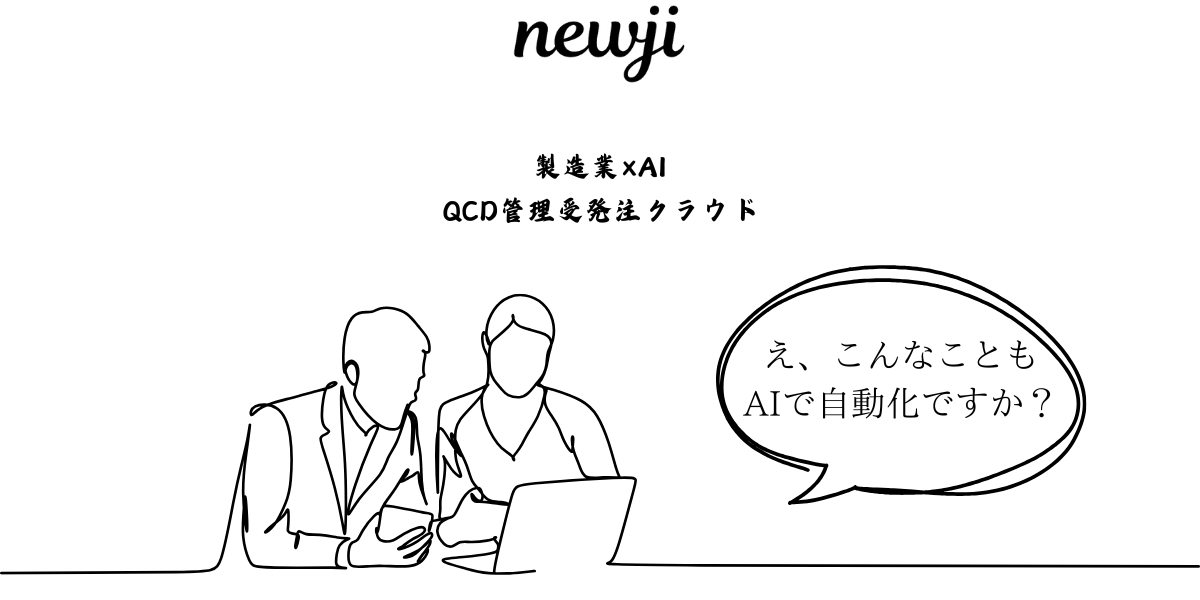
Mechanisms of friction and wear, wear reduction technology and applications
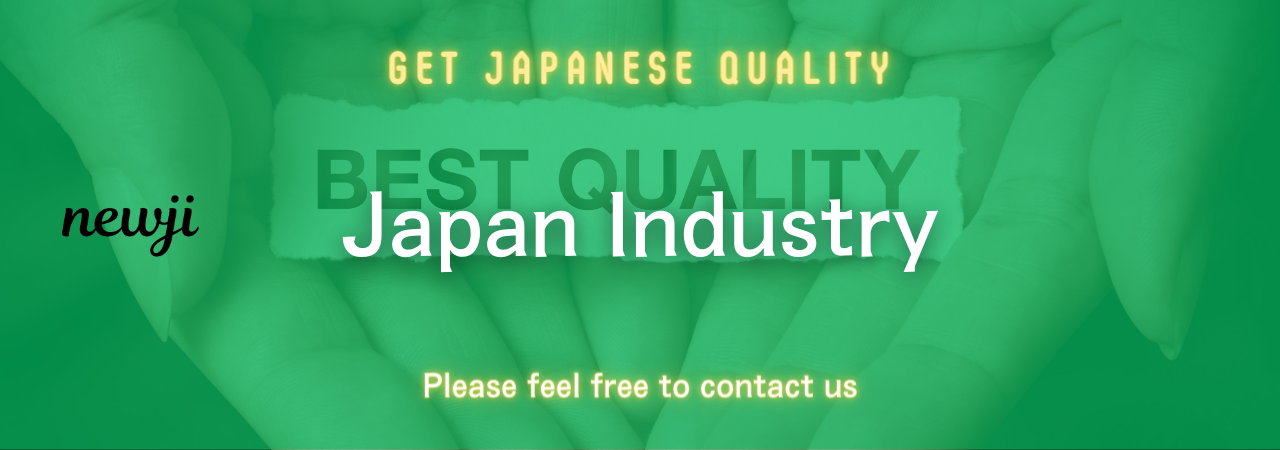
目次
Understanding Friction and Wear
Friction is the resistance that one surface or object encounters when moving over another.
We experience friction in everyday activities, from walking to writing.
While it can be beneficial, providing traction, it also leads to energy loss and wear and tear of objects.
Wear, on the other hand, refers to the gradual removal or deformation of material at solid surfaces.
It occurs when mechanical action causes the material to detach from a surface.
This process can be detrimental to machinery and components, as it affects their efficiency and lifespan.
Types of Wear
Understanding the different types of wear is essential in analyzing how to reduce and manage them.
1. **Adhesive Wear**: Occurs when materials transfer between contacting surfaces.
As two surfaces move against each other, particles may detach from one surface and adhere to the other.
This transfer can lead to material loss and surface degradation.
2. **Abrasive Wear**: Happens when hard particles or rough surfaces slide over a soft surface.
The harder surface or particles cut or deform the softer surface, leading to material loss.
3. **Fatigue Wear**: Results from cyclic loading and unloading on a surface.
Over time, repeated stress leads to surface cracks and material degradation.
4. **Corrosive Wear**: Involves chemical reactions between the surface material and its environment.
These reactions lead to gradual material loss, often exacerbated by mechanical action.
Mechanisms of Friction
Friction arises through several mechanisms:
– **Surface Roughness**: The microscopic peaks and valleys on surfaces come into contact, generating resistance.
When two surfaces slide over each other, these irregularities interlock, leading to friction.
– **Intermolecular Forces**: At the microscopic level, attractive forces between molecules of sliding surfaces contribute to friction.
These are weak forces but significant enough to affect motion.
– **Deformation**: When surfaces slide against each other, they deform slightly.
Energy is consumed in the process, leading to heat generation and resistance to motion.
Wear Reduction Technologies
Industries have developed innovative technologies to combat wear and extend the lifespan of components.
Surface Coatings
Surface coatings involve applying a protective layer to materials.
These coatings are designed to enhance resistance against wear, corrosion, and other environmental impacts.
Common materials used include ceramics, metals, and polymers.
For instance, diamond-like carbon coatings are used in precision tools to reduce friction and wear.
Lubrication Methods
Lubricants reduce friction and wear by forming a film between contact surfaces.
They can be oils, greases, or solid lubricants like graphite.
Lubrication serves multiple purposes:
– It minimizes direct contact between surfaces, reducing wear.
– It dissipates heat generated by friction.
– It prevents contaminant adhesion, maintaining surface integrity.
Material Selection
Choosing the right material for an application can significantly affect wear performance.
Materials are selected based on their hardness, toughness, and resistance to environmental factors.
For example, using hardened steel for high-wear applications can reduce the frequency of component replacement.
Applications and Impacts
The study and management of friction and wear have vast applications across different industries.
Automotive and Transport
In the automotive industry, reducing friction and wear enhances vehicle performance and longevity.
Engine components, brakes, and transmissions are optimized using advanced materials and lubrication technologies to improve efficiency.
Manufacturing
Machine tools and equipment in manufacturing face continuous wear.
Implementing wear-resistant materials and coatings helps in maintaining equipment precision and extending operational life.
Aerospace
In aerospace, materials face extreme conditions, requiring robust wear reduction strategies.
Ceramic coatings and advanced composites ensure components withstand the harsh environments of flight, enhancing safety and durability.
Future Trends in Wear Reduction
With rapid advancements in technology, the future holds promising trends in wear reduction.
Nanotechnology
Nanotechnology offers immense potential in reducing wear.
Nano-coatings can provide superior protective properties, offering higher resistance to abrasion and corrosion.
Smart Materials
Smart materials that adapt to environmental changes could foreseeably reduce wear by altering their properties in real-time.
These materials can self-heal or change their surface characteristics to minimize wear.
Data-Driven Approaches
Using data analytics, industries can predict wear patterns and develop proactive strategies.
This approach enhances the lifespan of components by identifying potential wear issues before they become significant.
Maintaining efficiency and extending the lifespan of components is critical across all sectors.
By understanding friction and wear mechanisms, leveraging wear reduction technologies, and embracing future trends, industries can achieve significant improvements in performance and sustainability.
資料ダウンロード
QCD管理受発注クラウド「newji」は、受発注部門で必要なQCD管理全てを備えた、現場特化型兼クラウド型の今世紀最高の受発注管理システムとなります。
ユーザー登録
受発注業務の効率化だけでなく、システムを導入することで、コスト削減や製品・資材のステータス可視化のほか、属人化していた受発注情報の共有化による内部不正防止や統制にも役立ちます。
NEWJI DX
製造業に特化したデジタルトランスフォーメーション(DX)の実現を目指す請負開発型のコンサルティングサービスです。AI、iPaaS、および先端の技術を駆使して、製造プロセスの効率化、業務効率化、チームワーク強化、コスト削減、品質向上を実現します。このサービスは、製造業の課題を深く理解し、それに対する最適なデジタルソリューションを提供することで、企業が持続的な成長とイノベーションを達成できるようサポートします。
製造業ニュース解説
製造業、主に購買・調達部門にお勤めの方々に向けた情報を配信しております。
新任の方やベテランの方、管理職を対象とした幅広いコンテンツをご用意しております。
お問い合わせ
コストダウンが利益に直結する術だと理解していても、なかなか前に進めることができない状況。そんな時は、newjiのコストダウン自動化機能で大きく利益貢献しよう!
(β版非公開)