- お役立ち記事
- Mechanisms of stress cracks and solvent cracks in plastic molded products and points for countermeasures against breakage problems
月間76,176名の
製造業ご担当者様が閲覧しています*
*2025年3月31日現在のGoogle Analyticsのデータより
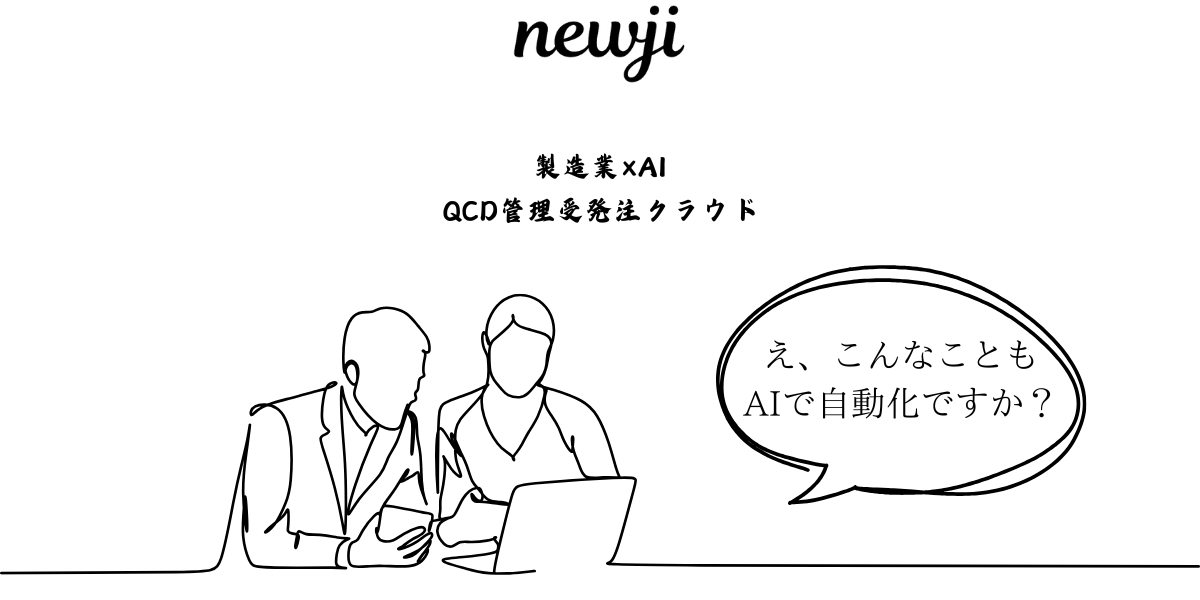
Mechanisms of stress cracks and solvent cracks in plastic molded products and points for countermeasures against breakage problems
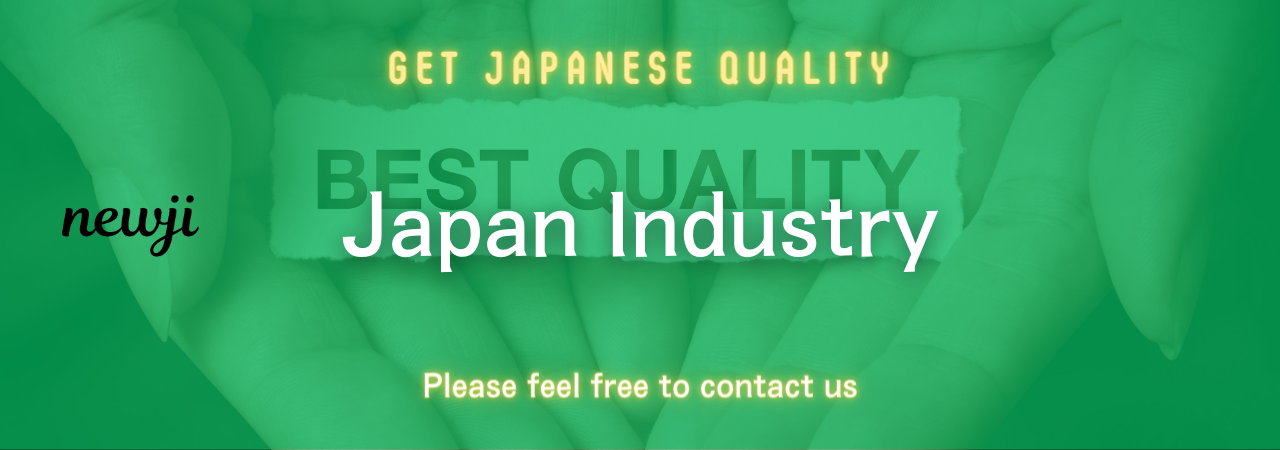
目次
Understanding Stress Cracks in Plastic Molded Products
Stress cracks are a common problem in plastic molded products.
They occur when internal stresses exceed the plastic’s ability to maintain integrity.
These cracks can compromise the durability and functionality of the product.
There are several causes of stress cracks.
One primary factor is the differential shrinkage that happens during the cooling phase of the molding process.
When different parts of the plastic cool at different rates, the resultant stress can lead to cracking.
Another factor contributing to stress cracks is the use of unsuitable processing conditions.
For instance, incorrect mold temperatures, injection pressures, or cycle times can introduce stress.
While these conditions can often be corrected, they highlight the importance of setting the right parameters when designing and manufacturing plastic parts.
Using the wrong material for the specific application can also lead to stress cracks.
Each type of resin has distinct characteristics and not all are suitable for every use.
Selecting a material with inadequate properties for the intended environmental conditions, such as temperature variations, can result in stress-related issues.
Preventing Stress Cracks
Preventing stress cracks in plastic products begins with thorough design and material assessment.
Selecting a resin with appropriate mechanical and thermal properties for the intended use is essential.
It is also crucial to optimize the processing conditions.
Ensuring that the mold temperature, injection pressure, and cooling rates are correctly set reduces the likelihood of introducing unnecessary stresses.
Simulation software can assist in predicting potential stress areas and give insights into necessary adjustments.
Attention should be paid to the design of the part itself.
Including adequate thickness, avoiding sharp corners, and ensuring uniform wall thickness can lessen stress concentration points.
Regular maintenance and calibration of machinery are also vital in preventing stress cracks.
Any deviation in machine operations can lead to defects in the final product.
Exploring Solvent Cracks in Plastics
Solvent cracks, also known as environmental stress cracks, occur when certain chemicals interact with the polymer.
Unlike stress cracks that are primarily due to mechanical forces, solvent cracks result from a chemical reaction.
The presence of solvents can weaken the bonds within the polymer structure.
This issue can be more pronounced when stress is already present in the material, compounded by the chemical exposure.
Such cracking typically appears when plastic comes into contact with specific chemicals or environmental conditions unintentionally.
Common culprits include cleaning agents, oils, or even prolonged exposure to harsh weather conditions.
These elements can cause microscopic fissures that may develop into full cracks over time.
Minimizing Solvent Cracks
To minimize solvent cracking, identify and limit exposure to potential chemicals.
Ensure that any necessary cleaners or agents used with the product are compatible with the plastic.
Furthermore, consider using additives or surface treatments to enhance chemical resistance.
These treatments can protect the surface and prolong the life of the plastic.
Selecting a polymer known for better chemical resistance, depending on the expected environment, can significantly reduce the risks.
Considerations during the design and manufacturing phases can lead to better choices in materials and processes.
Points for Countermeasures Against Breakage Problems
Addressing breakage problems in plastic molded products involves a multifaceted approach encompassing design, material selection, and process optimization.
Comprehensive Design Analysis
Evaluate the product’s design to identify potential stress and chemical exposure points.
Redesign any elements that may contribute to higher stress concentrations or increased chemical exposure.
Use computer-aided design (CAD) tools to simulate real-world conditions.
This helps in visualizing areas prone to stress or exposure, allowing for preemptive design modifications.
Material Selection and Testing
Choose materials based on the application environment.
Select a polymer with properties that match the physical and chemical expectations of its use.
Conduct thorough testing of materials against expected stresses and chemical exposures to ensure reliability.
Testing includes evaluating the mechanical properties under various conditions and ensuring that the polymer can withstand all anticipated forces and chemicals.
Process Optimization
Ensure that all machinery involved in production is maintained and calibrated regularly.
Optimum operation settings prevent unnecessary internal stresses in the product.
Implement stringent quality checks at various stages of production.
These checks allow for early detection of potential issues, thus allowing corrective measures before full-scale production begins.
Feedback and Continuous Improvement
Adopt a feedback-driven approach for continuous improvement.
Collect data on product performance and look for patterns or frequent weak points that need addressing.
Engage with end-users and manufacturers to understand the practical challenges they face.
This cooperative communication can lead to effective solutions and further improvements in design and manufacturing processes.
By understanding the mechanisms of stress and solvent cracks, and implementing comprehensive countermeasures, the integrity and longevity of plastic molded products can be significantly enhanced.
This approach not only reduces breakage problems but also enhances customer satisfaction and loyalty.
資料ダウンロード
QCD管理受発注クラウド「newji」は、受発注部門で必要なQCD管理全てを備えた、現場特化型兼クラウド型の今世紀最高の受発注管理システムとなります。
ユーザー登録
受発注業務の効率化だけでなく、システムを導入することで、コスト削減や製品・資材のステータス可視化のほか、属人化していた受発注情報の共有化による内部不正防止や統制にも役立ちます。
NEWJI DX
製造業に特化したデジタルトランスフォーメーション(DX)の実現を目指す請負開発型のコンサルティングサービスです。AI、iPaaS、および先端の技術を駆使して、製造プロセスの効率化、業務効率化、チームワーク強化、コスト削減、品質向上を実現します。このサービスは、製造業の課題を深く理解し、それに対する最適なデジタルソリューションを提供することで、企業が持続的な成長とイノベーションを達成できるようサポートします。
製造業ニュース解説
製造業、主に購買・調達部門にお勤めの方々に向けた情報を配信しております。
新任の方やベテランの方、管理職を対象とした幅広いコンテンツをご用意しております。
お問い合わせ
コストダウンが利益に直結する術だと理解していても、なかなか前に進めることができない状況。そんな時は、newjiのコストダウン自動化機能で大きく利益貢献しよう!
(β版非公開)