- お役立ち記事
- Medical equipment department required! Latest information on QMS (Quality Management System) and laws and regulations
Medical equipment department required! Latest information on QMS (Quality Management System) and laws and regulations
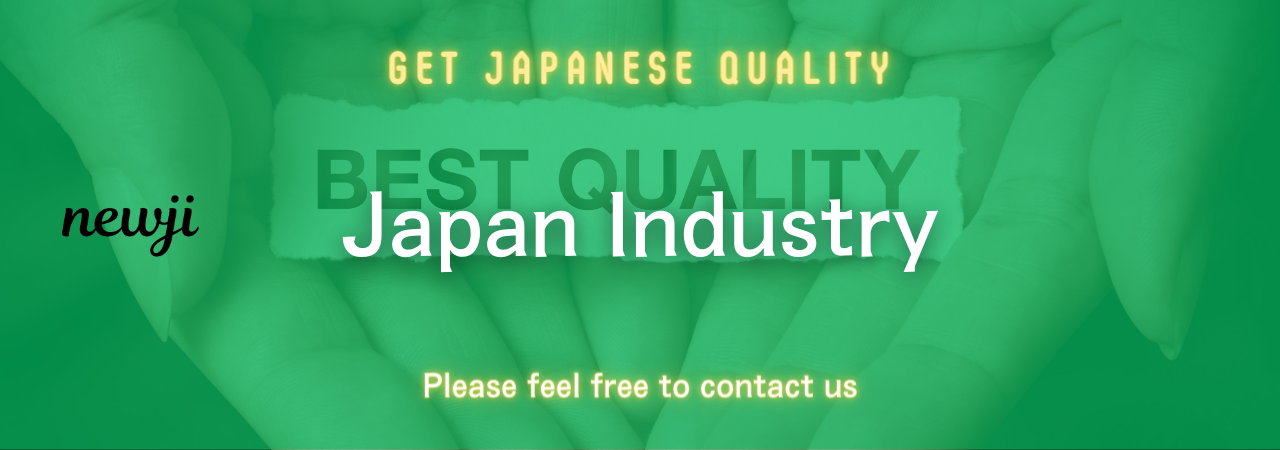
目次
Understanding the Basics of QMS in Medical Equipment
In nearly every industry today, quality management systems (QMS) play a crucial role in ensuring that products and services meet the highest standards.
In the medical equipment industry, a QMS is not just essential but is often a legal requirement.
These systems help manufacturers to consistently meet client needs while complying with regulatory standards.
QMS is essentially a framework of procedures and processes focused on achieving quality policies and objectives.
In the medical equipment sector, these systems guarantee the safety, efficacy, and reliability of products used in healthcare facilities.
It covers the entire lifecycle from design and development to production, packaging, labeling, distribution, and post-market surveillance.
A well-defined QMS helps companies improve processes, drive efficiency, and mitigate risks.
It ensures that patient safety is prioritized while also meeting legal and regulatory demands.
Medical equipment manufacturers that consistently maintain an efficient QMS gain a competitive advantage by delivering high-quality products that meet or exceed customer expectations.
Legal Requirements and Regulations for Medical Equipment
The medical equipment industry is one of the most heavily regulated worldwide.
Regulations are imposed to ensure the safety and effectiveness of medical devices as they directly impact patient health.
Understanding and adhering to these regulations is critical for all manufacturers and distributors.
Several key regulations and standards guide the QMS for medical equipment.
ISO 13485 is the internationally recognized standard for quality management in the medical device industry.
It focuses on maintaining the effectiveness of the quality management system and satisfying regulatory requirements applicable to medical equipment.
In the United States, the Food and Drug Administration (FDA) governs the quality management practices of medical device manufacturers.
They must comply with the Quality System Regulation (QSR), which enforces stringent quality management requirements.
Compliance with the FDA’s 21 CFR Part 820, covering the QSR, is mandatory for all medical device manufacturers intending to market their products in the U.S.
In the European Union, the Medical Device Regulation (MDR) sets guidelines for medical device manufacturers.
The MDR requires that a QMS be established and maintained, ensuring compliance with EU legislation and standards for medical devices.
The MDR is more stringent than previous directives, emphasizing greater scrutiny and oversight.
Recent Updates in QMS Regulations
For medical equipment manufacturers, keeping informed about the latest updates in QMS regulations is critical.
Recent changes in regulatory frameworks and standards must be addressed to maintain compliance and safeguard product quality.
One of the recent developments is the ISO 13485:2016 standard, which introduced additional requirements regarding risk management, supply chain control, and the involvement of the senior management.
Medical device companies have to monitor their suppliers more closely and implement more robust risk management strategies.
The Medical Device Coordination Group (MDCG) guidelines, published by the European Commission, offer valuable insights for complying with MDR.
These guidelines are designed to assist stakeholders in understanding and implementing the requirements of the regulation effectively.
In the United States, the FDA has released draft guidance on computer software assurance for production and quality system software.
These regulations target manufacturers who leverage software in their production and quality assurance processes, emphasizing risk evaluation and testing strategies.
The Role of QMS in Enhancing Patient Safety
At its core, the prime goal of a QMS in the medical device industry is to enhance patient safety.
While regulatory compliance is non-negotiable, the overarching priority is to prevent devices from causing harm to patients.
A thorough QMS approach ensures that every aspect of production and delivery is aligned with the safety needs of patients.
This includes the design, testing, and validation stages, which are critical in identifying and mitigating potential risks.
Document management is another crucial element that enhances patient safety.
Recording procedures, audits, and corrective actions create a transparent and reliable resource that supports continuous improvement.
Employee training, ensured through a QMS, is fundamental to maintaining high standards.
Proper education and training translate to fewer mistakes and a more robust execution of safety protocols.
In the post-market phase, surveillance processes contribute substantially to safety.
QMS-driven strategies in gathering feedback and monitoring performance allow manufacturers to address vulnerabilities swiftly and effectively.
Ways to Improve QMS in Medical Equipment Manufacturing
Improving QMS within medical equipment manufacturing requires commitment and strategic enhancements.
Here are several effective measures manufacturers can adopt:
1. **Strengthen Risk Management:**
Emphasizing a risk-based approach allows manufacturers to preemptively address potential issues, preventing them from escalating into serious problems.
2. **Leverage Technology:**
Utilize advanced tools and software that facilitate real-time monitoring and data-driven insights.
This enables more efficient tracking of production processes and quality checks.
3. **Focus on Training and Development:**
Regular training ensures that the workforce is fully equipped to comply with evolving regulations and maintain high standards.
Educating employees about the importance of quality and safety improves performance across the board.
4. **Foster a Culture of Quality:**
Encourage employees at all levels to prioritize quality.
Integrating quality management into the company culture ensures every member contributes to maintaining excellence.
5. **Conduct Regular Audits:**
Frequent internal and external audits help identify areas of improvement and ensure continuous adherence to standards and regulations.
Future Trends in QMS for Medical Equipment
The landscape of medical equipment manufacturing is constantly evolving, reflecting advancements in technology and changing regulatory environments.
Emerging trends in QMS point towards greater efficiency, smarter manufacturing processes, and heightened focus on data integrity.
The integration of Artificial Intelligence (AI) and machine learning is expected to revolutionize QMS practices.
These technologies can predict quality issues, automate decision-making processes, and enhance supply chain management.
Digital transformation is another critical trend, with more manufacturers adopting cloud-based QMS platforms for seamless integration across operations.
These systems enhance collaboration, improve communication, and facilitate a streamlined approach to quality management.
Data security will become increasingly important, ensuring that sensitive patient and product information is protected against breaches and unauthorized access.
Compliance with data protection regulations, such as GDPR, will remain a priority.
The global commitment towards environmental sustainability will also influence QMS in medical equipment.
Manufacturers are likely to adopt eco-friendly practices, recycling programs, and sustainable sourcing as a vital part of their quality frameworks.
By staying informed about QMS regulations and integrating innovative solutions, medical equipment manufacturers can reliably produce safe and effective devices.
The continuous pursuit of quality excellence is essential for enhancing patient safety and sustaining compliance in the ever-changing medical landscape.
資料ダウンロード
QCD調達購買管理クラウド「newji」は、調達購買部門で必要なQCD管理全てを備えた、現場特化型兼クラウド型の今世紀最高の購買管理システムとなります。
ユーザー登録
調達購買業務の効率化だけでなく、システムを導入することで、コスト削減や製品・資材のステータス可視化のほか、属人化していた購買情報の共有化による内部不正防止や統制にも役立ちます。
NEWJI DX
製造業に特化したデジタルトランスフォーメーション(DX)の実現を目指す請負開発型のコンサルティングサービスです。AI、iPaaS、および先端の技術を駆使して、製造プロセスの効率化、業務効率化、チームワーク強化、コスト削減、品質向上を実現します。このサービスは、製造業の課題を深く理解し、それに対する最適なデジタルソリューションを提供することで、企業が持続的な成長とイノベーションを達成できるようサポートします。
オンライン講座
製造業、主に購買・調達部門にお勤めの方々に向けた情報を配信しております。
新任の方やベテランの方、管理職を対象とした幅広いコンテンツをご用意しております。
お問い合わせ
コストダウンが利益に直結する術だと理解していても、なかなか前に進めることができない状況。そんな時は、newjiのコストダウン自動化機能で大きく利益貢献しよう!
(Β版非公開)