- お役立ち記事
- Metal corrosion damage mechanism, effective corrosion prevention technology and practical know-how
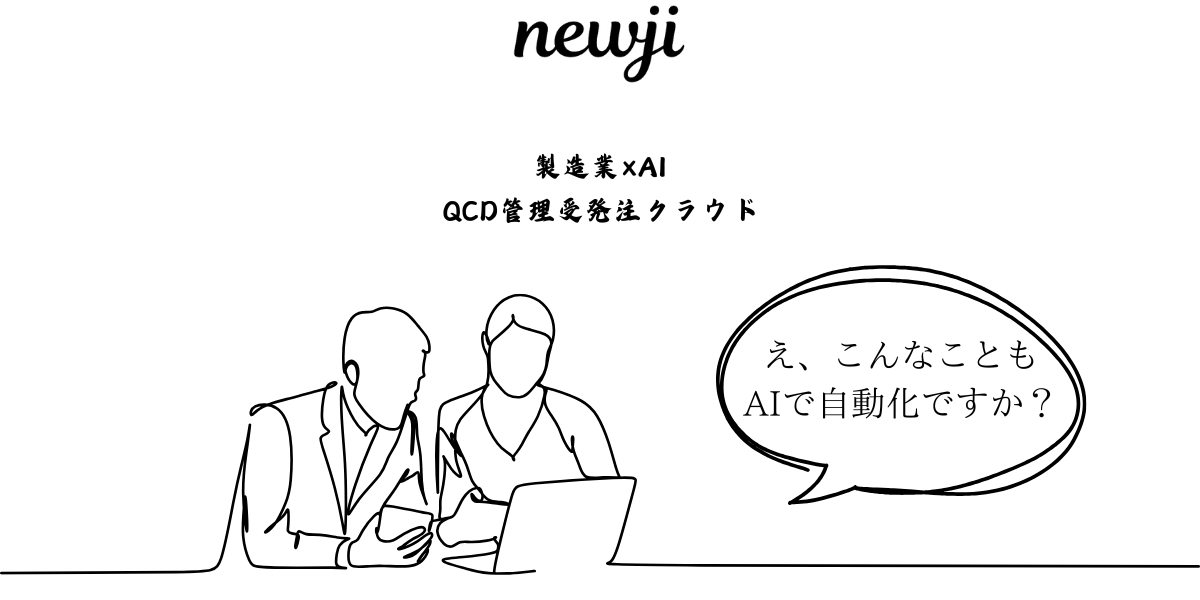
Metal corrosion damage mechanism, effective corrosion prevention technology and practical know-how
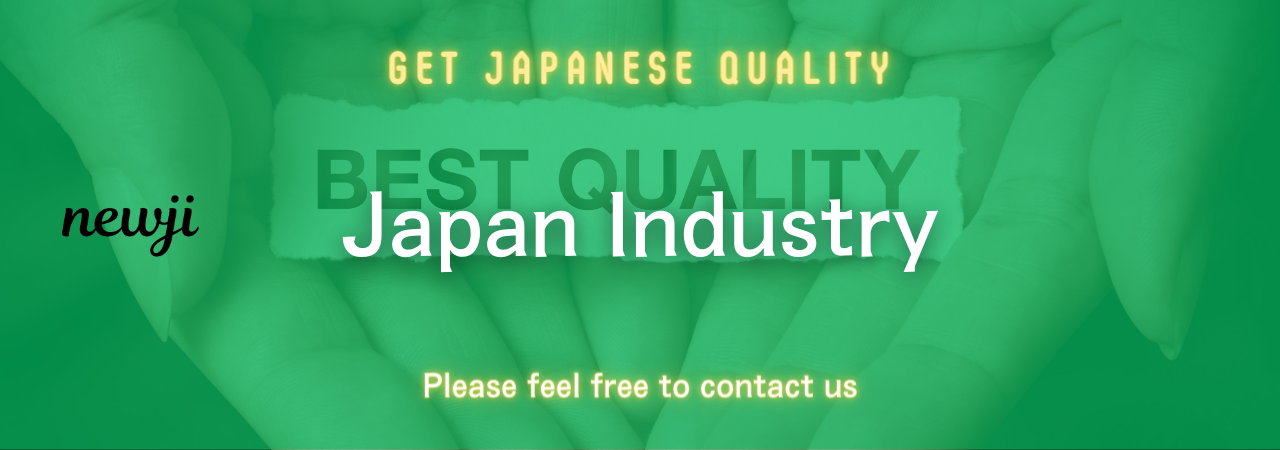
目次
Understanding Metal Corrosion
Metal corrosion is a natural process that deteriorates metal materials due to environmental interactions.
It is a common phenomenon that can cause significant damage if not properly managed.
The most recognizable form of corrosion is rust, which occurs when iron reacts with oxygen and moisture.
However, various metals undergo different types of corrosion based on their environment and chemical composition.
Corrosion can be broadly classified into several types, including uniform corrosion, galvanic corrosion, crevice corrosion, pitting corrosion, intergranular corrosion, and stress corrosion cracking.
Each type has its unique characteristics and mechanisms of action.
Understanding these corrosion types is essential for developing effective prevention and maintenance strategies.
Uniform Corrosion
Uniform corrosion occurs evenly across the surface of a metal.
It is the most common form of corrosion and is generally less damaging than localized forms because it proceeds at a consistent rate.
This type of corrosion is predictable and can often be controlled using protective coatings, inhibitors, or cathodic protection.
Galvanic Corrosion
Galvanic corrosion occurs when two dissimilar metals are in electrical contact with each other in the presence of an electrolyte.
The metal with a lower electrochemical potential becomes the anode and corrodes faster than it would alone, while the metal with a higher potential acts as the cathode and corrodes more slowly.
This type of corrosion is common in marine environments and can be managed by selecting compatible metal pairings and using insulators.
Crevice Corrosion
Crevice corrosion occurs in confined spaces where the metal is shielded from the environment, such as under gaskets, washers, or bolt heads.
The stagnation of corrosive substances in these areas can lead to rapid deterioration.
Preventing crevice corrosion involves designing structures to minimize crevices and ensuring clean, dry surfaces before assembly.
Pitting Corrosion
Pitting corrosion is a localized form of corrosion that results in small pits or holes on the metal surface.
It is particularly dangerous because it can lead to structural failure with minimal overall metal loss.
Metals like stainless steel, which are generally resistant to corrosion, are susceptible to pitting in chloride-containing environments.
Regular inspections and the use of protective coatings are crucial for prevention.
Intergranular Corrosion
Intergranular corrosion attacks the grain boundaries within a metal.
It often results from improper heat treatment and is a concern for specific alloys, like stainless steel.
This corrosion type can cause severe weakening without visible surface damage, making it vital to use proper fabrication techniques and heat treatments.
Stress Corrosion Cracking
Stress corrosion cracking (SCC) is a combination of chemical and mechanical effects that lead to cracking.
It typically occurs in susceptible alloys when exposed to specific environments under tensile stress.
Industries like aerospace or chemical processing are particularly vigilant about SCC due to the catastrophic failures it can cause.
To prevent SCC, it is crucial to reduce residual stresses in metal components and avoid exposure to aggressive environments.
Effective Corrosion Prevention Technologies
Various technologies and methods can be employed to prevent or mitigate corrosion, ensuring the longevity and safety of metal components.
Material Selection
One of the most effective ways to prevent corrosion is by choosing the right materials.
Using metals and alloys that are inherently resistant to corrosion, such as stainless steel, titanium, or aluminum, can significantly reduce the risk.
Additionally, knowing the operating environment helps in selecting materials that can withstand specific conditions.
Protective Coatings
Applying protective coatings, such as paints, enamels, or galvanization, creates a barrier between the metal and its environment.
These coatings prevent corrosive elements from reaching the metal surface.
Regular maintenance and inspections ensure the integrity of these coatings over time.
Cathodic Protection
Cathodic protection is a technique used to control the corrosion of a metal surface by making it the cathode of an electrochemical cell.
This can be achieved either by attaching a more easily corroded “sacrificial anode” to the metal surface, or by connecting the metal to an external power source.
This method is commonly used in pipelines and ship hulls.
Corrosion Inhibitors
Corrosion inhibitors are chemicals that reduce the rate of metal corrosion.
They function by either forming a protective film on the metal surface or by altering the environment to make it less corrosive.
Inhibitors are widely used in industries such as oil and gas, water treatment, and chemical processing.
Environmental Control
Controlling the environment around metal structures is a practical way to reduce corrosion risk.
This may involve reducing exposure to moisture, aggressive chemicals, and pollutants.
Humidity control, ventilation, and moisture barriers can all contribute to minimizing corrosion.
Practical Know-How for Corrosion Management
To effectively manage corrosion, understanding both the science and practical aspects is essential.
Regular Inspections
Regular inspections are vital for detecting early signs of corrosion and assessing the condition of metal structures.
These inspections should be systematic and detailed, focusing on potential problem areas like joints, welds, and under protective coatings.
Maintenance and Repairs
Timely maintenance and repairs are crucial in extending the life of metal components.
Addressing small issues promptly can prevent more significant, costly problems later.
This includes repairing any damaged coatings, replacing worn parts, and conducting stress-relief treatments.
Training and Awareness
Educating personnel about the importance of preventing corrosion and the best practices to achieve it is critical.
Proper training ensures that everyone involved understands the potential risks and how to mitigate them effectively.
Documentation and Monitoring
Keeping detailed records of maintenance, inspections, and environmental conditions helps in understanding trends and predicting future corrosion issues.
Using monitoring tools to track environmental factors and metal conditions can provide valuable data to guide decision-making.
Implementing these strategies and being proactive about corrosion management can prevent costly damage and improve the longevity and reliability of metal structures.
By combining scientific knowledge with practical application, industries can significantly reduce the impact of metal corrosion.
資料ダウンロード
QCD調達購買管理クラウド「newji」は、調達購買部門で必要なQCD管理全てを備えた、現場特化型兼クラウド型の今世紀最高の購買管理システムとなります。
ユーザー登録
調達購買業務の効率化だけでなく、システムを導入することで、コスト削減や製品・資材のステータス可視化のほか、属人化していた購買情報の共有化による内部不正防止や統制にも役立ちます。
NEWJI DX
製造業に特化したデジタルトランスフォーメーション(DX)の実現を目指す請負開発型のコンサルティングサービスです。AI、iPaaS、および先端の技術を駆使して、製造プロセスの効率化、業務効率化、チームワーク強化、コスト削減、品質向上を実現します。このサービスは、製造業の課題を深く理解し、それに対する最適なデジタルソリューションを提供することで、企業が持続的な成長とイノベーションを達成できるようサポートします。
オンライン講座
製造業、主に購買・調達部門にお勤めの方々に向けた情報を配信しております。
新任の方やベテランの方、管理職を対象とした幅広いコンテンツをご用意しております。
お問い合わせ
コストダウンが利益に直結する術だと理解していても、なかなか前に進めることができない状況。そんな時は、newjiのコストダウン自動化機能で大きく利益貢献しよう!
(Β版非公開)