- お役立ち記事
- Metal joining technology and application to dissimilar metal joining
月間77,185名の
製造業ご担当者様が閲覧しています*
*2025年2月28日現在のGoogle Analyticsのデータより
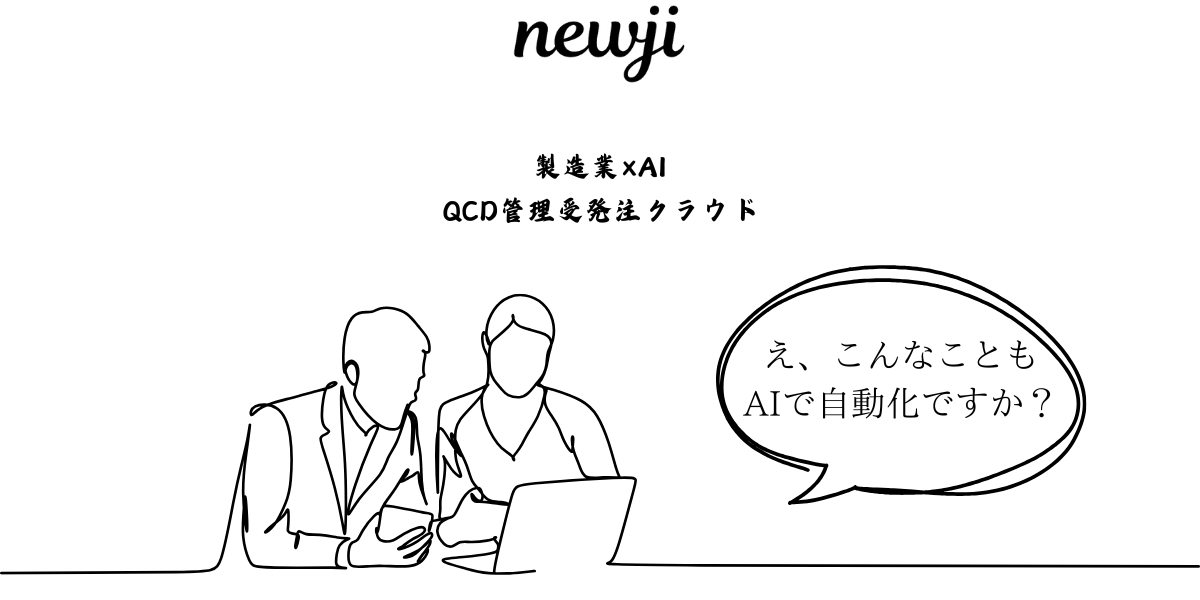
Metal joining technology and application to dissimilar metal joining
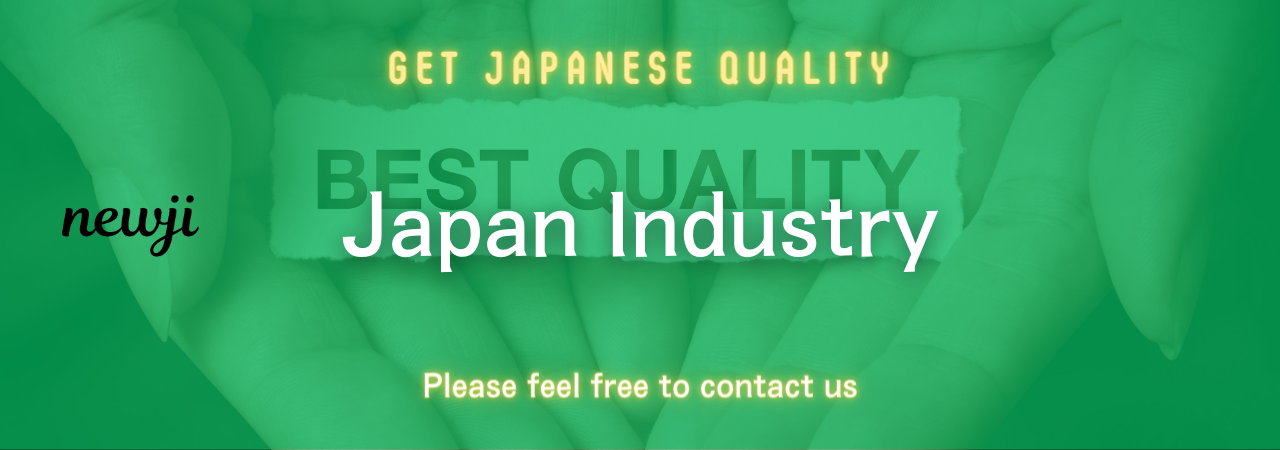
目次
Understanding Metal Joining Technology
Metal joining technology is a vital aspect of modern manufacturing and engineering.
It involves various techniques used to unite two or more metal pieces into a single structure.
These techniques can range from traditional methods like welding and soldering to more advanced processes like laser welding and adhesive bonding.
The primary focus of metal joining technology is to create strong, reliable, and durable connections between metal components.
This is essential in various industries such as automotive, aerospace, construction, and electronics, where strong metal joints are crucial for safety and performance.
Welding: A Traditional Approach
Welding is one of the oldest and most widely used methods in metal joining technology.
It involves melting the base metals along with a filler material to create a strong joint upon cooling.
There are several types of welding techniques, each suitable for different materials and applications.
– **Arc Welding**: This is a method where an electric arc is used to melt the metals at the joint.
It includes various techniques like Shielded Metal Arc Welding (SMAW), Metal Inert Gas (MIG) welding, and Tungsten Inert Gas (TIG) welding.
– **Gas Welding**: Also known as oxy-fuel welding, it uses fuel gases and oxygen to weld and cut metals.
It is a traditional method but still valuable for specific applications.
– **Resistance Welding**: In this technique, heat generated by electrical resistance is used to melt and join the metals.
It is commonly used in the automotive industry due to its efficiency in joining sheet metals.
Soldering and Brazing
Unlike welding, soldering and brazing do not involve melting the base metals.
Instead, they use a filler metal with a lower melting point to create the joint.
– **Soldering**: This technique is typically used for electrical connections and small metal components.
It uses solder, a filler metal that has a relatively low melting point.
This makes it ideal for delicate components that could be damaged by high heat.
– **Brazing**: Similar to soldering, but at higher temperatures, brazing uses a filler metal that flows into the joint gap through capillary action.
It is widely used for joining dissimilar metals.
Dissimilar Metal Joining
Joining dissimilar metals is a unique challenge in metal joining technology.
Various properties such as melting temperature, thermal expansion, and chemical composition make it difficult to create strong and long-lasting joints between different metal types.
Challenges of Dissimilar Metal Joining
When joining dissimilar metals, several challenges need to be addressed:
– **Difference in Melting Points**: One of the primary challenges is the significant difference in melting points between the metals.
This can cause one metal to melt or degrade while the other remains solid.
– **Thermal Expansion Coefficients**: When metals with different thermal expansion coefficients are joined, temperature changes can cause stress at the joint, leading to failure over time.
– **Formation of Intermetallic Compounds**: Incompatible metals can form brittle intermetallic compounds at the joint, compromising the joint’s strength and integrity.
Techniques for Joining Dissimilar Metals
To successfully join dissimilar metals, specific techniques have been developed and refined:
– **Laser Welding**: Laser welding provides precise control over the welding heat, making it suitable for dissimilar metals with varying melting points.
It is often used in the automotive and aerospace industries.
– **Ultrasonic Welding**: This technique uses high-frequency ultrasonic vibrations to join metals without melting them.
It is particularly useful for joining small, delicate components and electronics.
– **Adhesive Bonding**: This method involves using specialized adhesives to create strong bonds between different metals.
It is beneficial for applications requiring lightweight and flexible joints.
– **Explosion Welding**: This unique process involves using controlled explosive force to bond dissimilar metals.
The explosive force creates a high-velocity collision that forms a solid-state bond without melting the metals.
Applications of Dissimilar Metal Joining
The ability to join dissimilar metals effectively opens up a wide range of applications across various industries.
Automotive Industry
In the automotive industry, dissimilar metal joining is crucial for manufacturing lightweight and fuel-efficient vehicles.
The combination of different metals, such as aluminum and steel, helps reduce the overall weight of the vehicle while maintaining structural integrity and safety.
Aerospace Industry
The aerospace industry relies heavily on joining dissimilar metals to create lightweight and strong components for aircraft and spacecraft.
The use of materials like titanium and aluminum, joined together, ensures high performance and fuel efficiency.
Electronics Industry
In the electronics industry, dissimilar metal joining is essential for creating compact and efficient components.
Techniques like soldering and adhesive bonding are frequently used to assemble circuit boards and other electronic devices.
Future of Metal Joining Technologies
As technology continues to advance, so will the methods and materials used for metal joining.
Researchers are constantly developing new techniques and improving existing ones to meet the demands of modern industry.
One such advancement is the use of nanotechnology in developing new filler materials and adhesives that offer superior strength and conductivity.
Additionally, automation and robotics are playing a more significant role in metal joining, increasing precision and efficiency in manufacturing processes.
In conclusion, metal joining technology is a critical component of modern industry, enabling the construction of strong and durable metal structures.
With the ongoing development of techniques for joining dissimilar metals, industries have greater flexibility and innovation in design and production, paving the way for future advancements in technology and manufacturing.
資料ダウンロード
QCD管理受発注クラウド「newji」は、受発注部門で必要なQCD管理全てを備えた、現場特化型兼クラウド型の今世紀最高の受発注管理システムとなります。
ユーザー登録
受発注業務の効率化だけでなく、システムを導入することで、コスト削減や製品・資材のステータス可視化のほか、属人化していた受発注情報の共有化による内部不正防止や統制にも役立ちます。
NEWJI DX
製造業に特化したデジタルトランスフォーメーション(DX)の実現を目指す請負開発型のコンサルティングサービスです。AI、iPaaS、および先端の技術を駆使して、製造プロセスの効率化、業務効率化、チームワーク強化、コスト削減、品質向上を実現します。このサービスは、製造業の課題を深く理解し、それに対する最適なデジタルソリューションを提供することで、企業が持続的な成長とイノベーションを達成できるようサポートします。
製造業ニュース解説
製造業、主に購買・調達部門にお勤めの方々に向けた情報を配信しております。
新任の方やベテランの方、管理職を対象とした幅広いコンテンツをご用意しております。
お問い合わせ
コストダウンが利益に直結する術だと理解していても、なかなか前に進めることができない状況。そんな時は、newjiのコストダウン自動化機能で大きく利益貢献しよう!
(β版非公開)