- お役立ち記事
- Metal-to-metal joining technology: joining method that maintains conductivity and vendor selection
月間76,176名の
製造業ご担当者様が閲覧しています*
*2025年3月31日現在のGoogle Analyticsのデータより
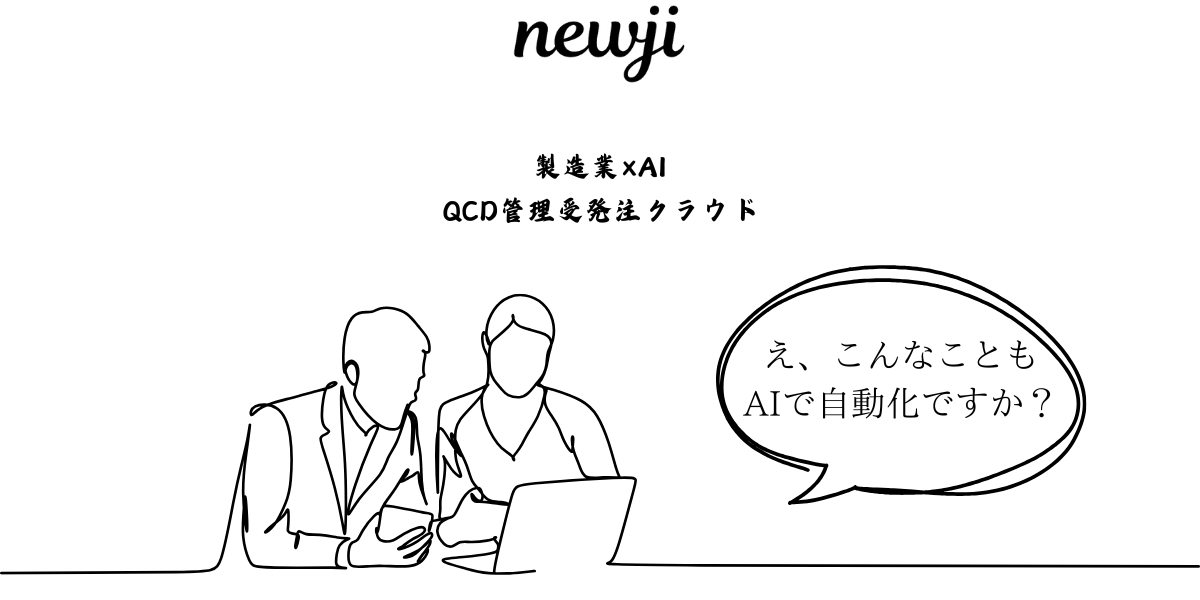
Metal-to-metal joining technology: joining method that maintains conductivity and vendor selection
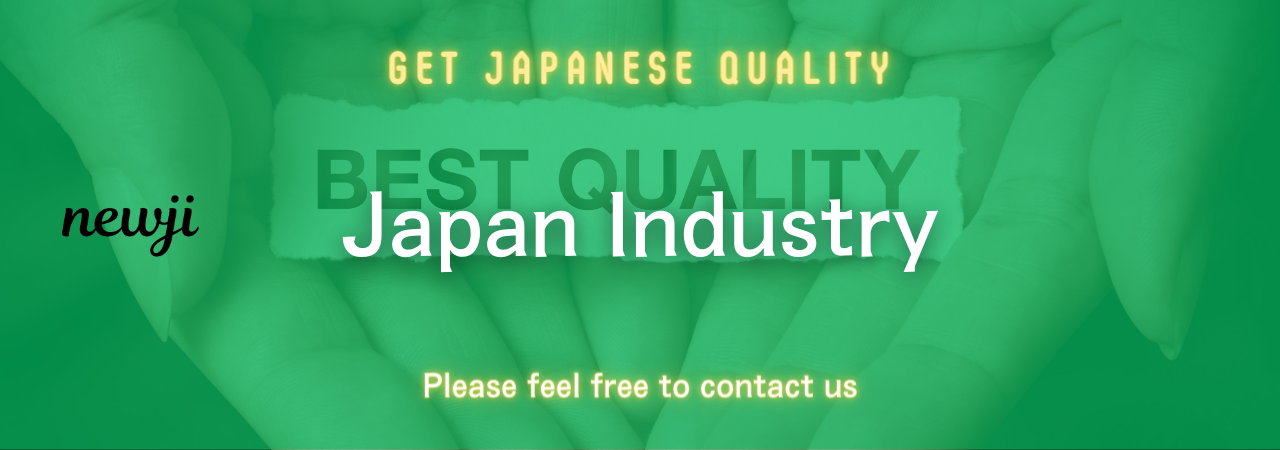
目次
Understanding Metal-to-Metal Joining Technology
Metal-to-metal joining technology is essential in various industries, including automotive, aerospace, electronics, and construction.
This technology involves connecting two or more metal pieces to form a single, cohesive structure.
The right joining method is crucial for maintaining conductivity and ensuring the integrity of the final product.
In this article, we will explore different methods of joining metals and offer guidance on selecting a suitable vendor for your project’s needs.
Common Methods of Metal-to-Metal Joining
There are several methods available for metal-to-metal joining, each with specific advantages based on the application.
Understanding these methods helps in selecting the right technique for your project.
Welding
Welding is one of the most popular and effective metal joining methods.
It involves melting the base metal and often a filler material to create a joint.
Welding provides a strong and permanent bond and is ideal for applications requiring high structural integrity.
Brazing
Brazing involves joining metals by melting a filler metal with a lower melting point than the base metals.
The filler flows into the joint by capillary action and solidifies to create a strong bond.
Brazing is suitable for joining dissimilar metals and offers good conductivity and strength.
Soldering
Soldering is similar to brazing but uses a filler metal with an even lower melting point.
It is often used in electronics for its excellent conductivity and the minimal heat required to create the joint.
Soldering is not as strong as welding or brazing but is sufficient for many electrical applications.
Riveting
Riveting involves using metal pins or bolts to fasten materials together.
This method is mechanical and does not involve melting any metals.
Riveting is ideal for joining thin sheets of metal and is commonly used in aerospace and automotive applications.
Adhesive Bonding
Adhesive bonding uses specialized adhesives to join metal surfaces.
It is an effective method for joining dissimilar materials and provides a strong bond without the need for heat.
Adhesive bonding is suitable for applications requiring lightweight components.
Factors to Consider in Maintaining Conductivity
Conductivity is a crucial consideration in metal-to-metal joining, especially in electrical applications.
Here are some factors to ensure that your joints maintain optimal conductivity:
Material Selection
Choose materials with inherent high electrical conductivity, such as copper or aluminum, when conductivity is a priority.
Ensure that the base and filler metals are compatible to avoid galvanic corrosion, which can degrade conductivity.
Joint Design
Proper joint design can significantly affect conductivity.
Minimize the joint area and ensure a smooth, clean surface before joining to maximize the contact area for better electron flow.
Surface Preparation
Proper surface preparation is critical for maintaining conductivity.
Clean the metal surfaces thoroughly to remove any oxides, oils, or contaminants that can impede electrical flow.
Use flux when soldering or brazing to ensure proper wetting of the metal surfaces.
Quality Control
Implementing rigorous quality control measures throughout the joining process will help maintain conductivity.
Regular inspections and testing of the joints can identify any issues early and prevent future problems.
Choosing the Right Vendor for Metal-to-Metal Joining
Selecting the right vendor is crucial for the success of your metal-to-metal joining project.
Here are some steps to help you choose a suitable partner:
Evaluate Experience and Expertise
Look for vendors with a proven track record in metal-to-metal joining within your industry.
Evaluate their expertise with different metals and joining methods to ensure they can meet your specific requirements.
Check Certifications and Standards
Ensure that the vendor complies with relevant industry standards and certifications.
Certifications like ISO and AS9100 indicate a commitment to quality and adherence to recognized protocols.
Assess Technological Capabilities
Consider vendors with advanced technological capabilities that align with your project needs.
State-of-the-art equipment and innovative solutions can improve the quality and efficiency of the joining process.
Review References and Past Work
Request references and review case studies or past project portfolios.
This will provide insight into the vendor’s ability to meet deadlines, handle complex projects, and deliver satisfactory results.
Discuss Cost and Timeline
Conduct detailed discussions about cost estimates and timelines for project completion.
Ensure that the vendor provides transparent pricing and realistic schedules that match your project scope and budget.
In conclusion, metal-to-metal joining technology is a vital aspect of many industries.
Understanding the different methods available and the factors affecting conductivity is essential for selecting the right approach for your needs.
Moreover, choosing a qualified vendor with the necessary experience, certifications, and capabilities can significantly impact the success of your project. By following these guidelines, you can ensure a strong, conductive, and reliable metal-to-metal joint.
資料ダウンロード
QCD管理受発注クラウド「newji」は、受発注部門で必要なQCD管理全てを備えた、現場特化型兼クラウド型の今世紀最高の受発注管理システムとなります。
ユーザー登録
受発注業務の効率化だけでなく、システムを導入することで、コスト削減や製品・資材のステータス可視化のほか、属人化していた受発注情報の共有化による内部不正防止や統制にも役立ちます。
NEWJI DX
製造業に特化したデジタルトランスフォーメーション(DX)の実現を目指す請負開発型のコンサルティングサービスです。AI、iPaaS、および先端の技術を駆使して、製造プロセスの効率化、業務効率化、チームワーク強化、コスト削減、品質向上を実現します。このサービスは、製造業の課題を深く理解し、それに対する最適なデジタルソリューションを提供することで、企業が持続的な成長とイノベーションを達成できるようサポートします。
製造業ニュース解説
製造業、主に購買・調達部門にお勤めの方々に向けた情報を配信しております。
新任の方やベテランの方、管理職を対象とした幅広いコンテンツをご用意しております。
お問い合わせ
コストダウンが利益に直結する術だと理解していても、なかなか前に進めることができない状況。そんな時は、newjiのコストダウン自動化機能で大きく利益貢献しよう!
(β版非公開)