- お役立ち記事
- Method and benefits of changing from dicing blade to straight blade
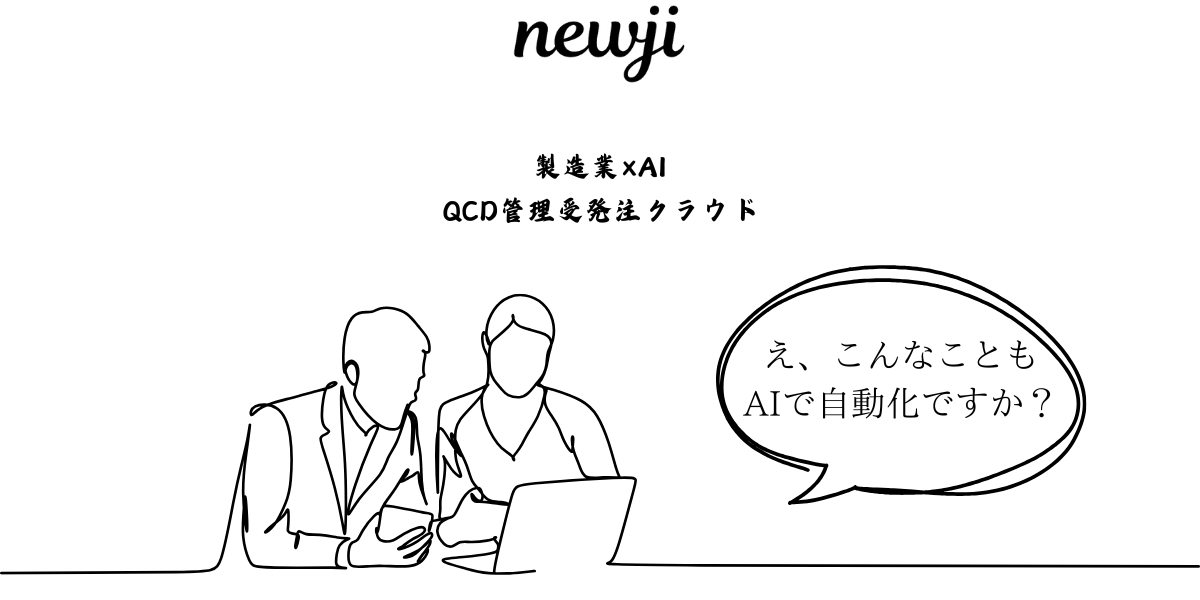
Method and benefits of changing from dicing blade to straight blade
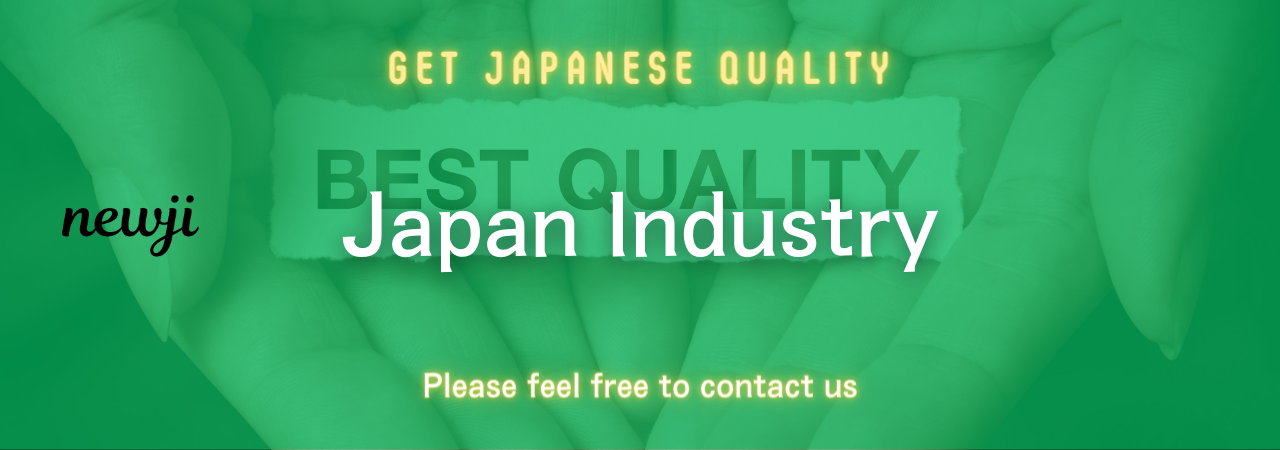
目次
Understanding the Basics: What are Dicing Blades and Straight Blades?
In the world of manufacturing and material processing, cutting tools play an essential role.
Two common types of cutting blades are dicing blades and straight blades.
Dicing blades are typically used for precision cutting, especially in the electronics industry.
They are circular, often with a diamond coating, and are designed for cutting hard materials into small, precise pieces.
Straight blades, on the other hand, are used for more broad cutting tasks.
They are linear and can be used in a variety of industries, including food processing, paper, and textiles.
Deciding on the Change: Why Switch from Dicing Blades to Straight Blades?
The decision to switch from dicing blades to straight blades can come down to several factors.
One primary reason is the nature of the material being cut.
If the product requires straight, clean cuts, straight blades might be more effective.
They are also generally easier to maintain and replace, providing efficiency benefits.
Another factor is the type of cut required.
While dicing blades are excellent for precision, they can be slow for larger cuts.
Straight blades can often complete tasks faster, saving valuable production time.
Cost considerations also play a big role in this decision.
Dicing blades, particularly those with diamond coatings, can be expensive.
Switching to straight blades can reduce costs, especially if precision is not critical.
Steps to Successful Transition: Implementing the Change
Step 1: Evaluate Your Cutting Needs
Before deciding on a switch, it’s important to analyze your current cutting processes.
Assess the types of materials you handle, the precision of cuts required, and the rate of production.
This evaluation will guide your decision on whether switching blades is beneficial.
Step 2: Choose the Right Straight Blade
Not all straight blades are created equal.
Selecting the appropriate straight blade involves considering the hardness of the materials to cut.
Additionally, you should account for the expected blade life and maintenance needs.
Consult with blade manufacturers or suppliers to find a suitable option for your operation.
Step 3: Adjust Machine Settings
After deciding to use straight blades, adjusting the settings of your cutting machines is crucial.
This might involve changing the blade alignment, adjusting the speed, and even recalibrating machines to ensure optimal performance.
Consult the manufacturer’s guidelines or hire a professional if necessary.
Step 4: Conduct a Pilot Test
Before fully committing to the use of straight blades, conduct a pilot test.
This involves testing the blades on a small batch of products to gauge performance.
During this phase, pay attention to the quality of cuts, timeframe for completion, and any equipment strain.
The data gathered can offer insights and highlight necessary adjustments before a full-scale switch.
Step 5: Train Your Staff
Your production team should be familiar with the new operational changes.
Conduct training sessions covering both the technical aspects of the straight blades and safety protocols.
Ensuring the workforce is comfortable with the new tools and methods will result in a smoother transition.
Benefits of Switching to Straight Blades
Improved Efficiency and Speed
One of the significant benefits of using straight blades is increased speed and efficiency.
They allow for faster cuts in materials that do not require precision.
This ensures that production lines move quicker, increasing throughput.
Cost-Effectiveness
Straight blades are often less expensive than dicing blades, especially those designed with costly materials like diamonds.
Over time, this can result in significant cost savings.
Additionally, straight blades can be less demanding on maintenance budgets, as they generally have a longer lifespan.
Easier Maintenance and Replacement
Straight blades are simpler to maintain compared to dicing blades.
They can be quickly replaced or sharpened, limiting downtime.
Their straightforward design also makes them easy to handle, minimizing the risk of operational errors.
Versatility in Use
Another advantage of straight blades is their versatility.
They are suitable for cutting a wide range of materials across different industries.
Whether cutting fabrics in the textiles industry or slicing items in food processing, straight blades are highly adaptable.
Conclusion: Weighing the Options for Optimal Results
Switching from dicing blades to straight blades involves careful planning and consideration.
While there are clear benefits, each organization must weigh these against its specific needs and constraints.
Successfully implementing this change can lead to improved productivity, cost savings, and streamlined operations.
Ultimately, assessing the unique demands of your cutting tasks will help guide the decision towards the most effective blade choice.
資料ダウンロード
QCD調達購買管理クラウド「newji」は、調達購買部門で必要なQCD管理全てを備えた、現場特化型兼クラウド型の今世紀最高の購買管理システムとなります。
ユーザー登録
調達購買業務の効率化だけでなく、システムを導入することで、コスト削減や製品・資材のステータス可視化のほか、属人化していた購買情報の共有化による内部不正防止や統制にも役立ちます。
NEWJI DX
製造業に特化したデジタルトランスフォーメーション(DX)の実現を目指す請負開発型のコンサルティングサービスです。AI、iPaaS、および先端の技術を駆使して、製造プロセスの効率化、業務効率化、チームワーク強化、コスト削減、品質向上を実現します。このサービスは、製造業の課題を深く理解し、それに対する最適なデジタルソリューションを提供することで、企業が持続的な成長とイノベーションを達成できるようサポートします。
オンライン講座
製造業、主に購買・調達部門にお勤めの方々に向けた情報を配信しております。
新任の方やベテランの方、管理職を対象とした幅広いコンテンツをご用意しております。
お問い合わせ
コストダウンが利益に直結する術だと理解していても、なかなか前に進めることができない状況。そんな時は、newjiのコストダウン自動化機能で大きく利益貢献しよう!
(Β版非公開)