- お役立ち記事
- Method and significance of process capability analysis in manufacturing
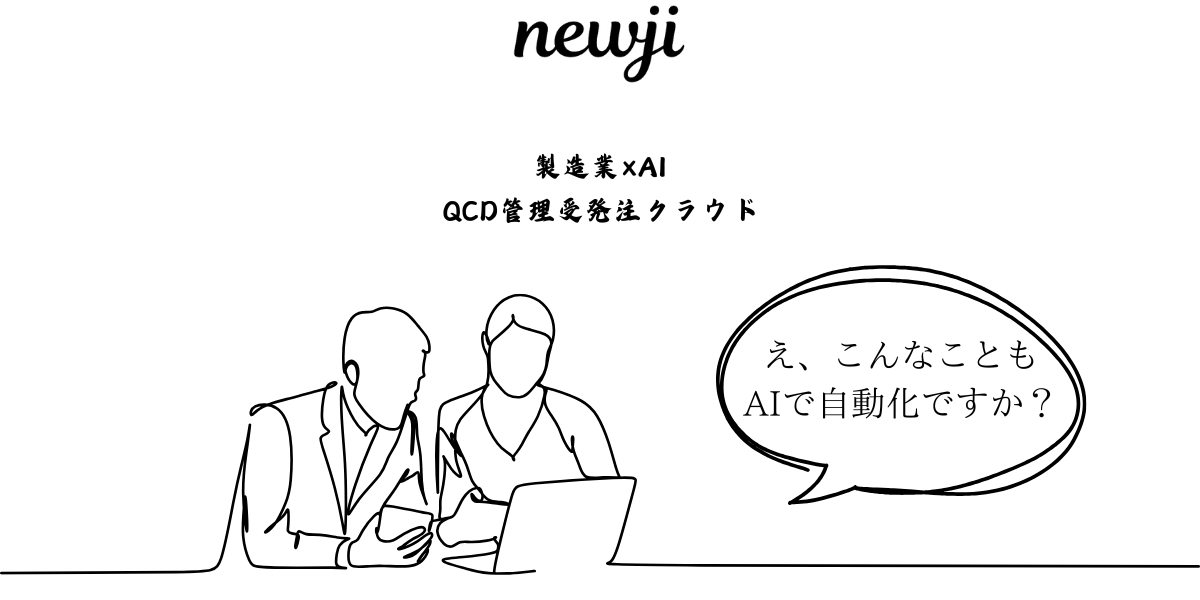
Method and significance of process capability analysis in manufacturing
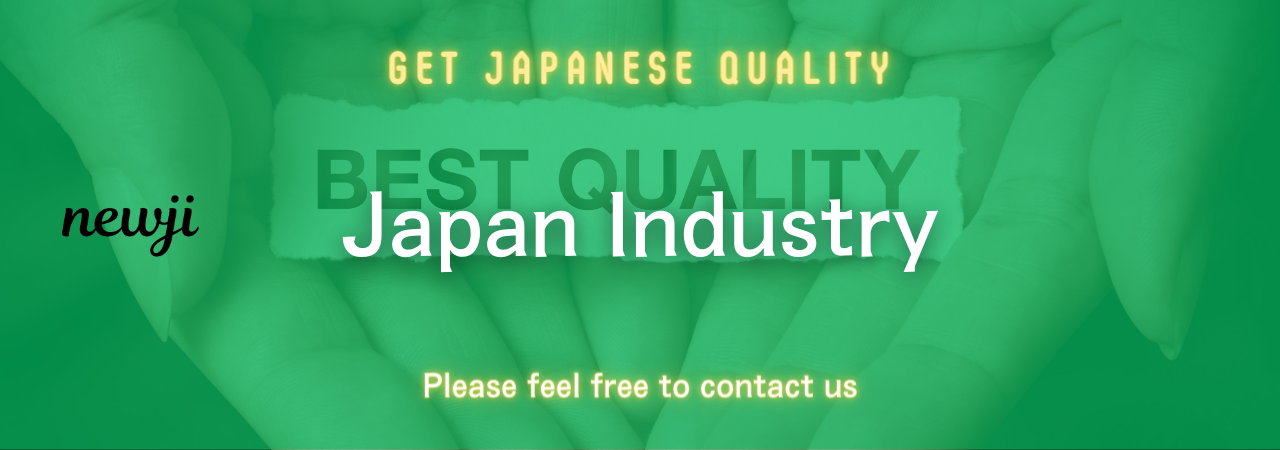
目次
Understanding Process Capability Analysis
In manufacturing, understanding how well a process performs is crucial.
Process capability analysis is a statistical tool that helps measure how well a process meets specifications.
By comparing the output of a process to the desired standards, we can determine if a process is capable of consistently producing items within the target limits.
Key Metrics in Process Capability Analysis
Process Capability Index (Cp)
The Process Capability Index, or Cp, is one of the fundamental metrics in process capability analysis.
Cp compares the width of the process spread to the width of the specification limits.
A higher Cp value indicates that the process is capable of producing items within the specified limits more consistently.
Process Performance Index (Pp)
While Cp measures the potential capability, Pp measures actual performance.
The Process Performance Index considers the distribution’s mean and variability.
It reflects how the process performs in real-world conditions, taking into account shifts in the process mean.
Capability Ratio (Cpk)
The Capability Ratio, or Cpk, adjusts Cp by accounting for any shift in the process mean.
Cpk shows how close the process mean is to the target value while also considering the spread of the process.
A higher Cpk value indicates better alignment with specification limits.
Steps to Conduct Process Capability Analysis
Step 1: Select a Process
The first step in process capability analysis is to choose the process you wish to evaluate.
Selecting a critical process that significantly impacts product quality is essential.
Step 2: Define Specification Limits
Next, define the upper and lower specification limits for the process.
These limits are the acceptable range of values that the process output must fall within.
Step 3: Collect Data
Collect data from the process under normal operating conditions.
Ensure the data is representative of the process performance over time.
Step 4: Calculate Key Metrics
Using the collected data, calculate the key metrics such as Cp, Cpk, and Pp.
These calculations will give you insights into how well the process performs relative to the set specifications.
Step 5: Analyze Results
Analyze the results to identify any areas where the process may need improvement.
Higher values of Cp and Cpk indicate a capable process, while lower values suggest the need for process improvement.
Significance of Process Capability Analysis
Quality Improvement
One of the primary benefits of process capability analysis is that it helps in improving quality.
By identifying processes that are not capable, manufacturers can take corrective actions to bring them within specifications.
This leads to higher-quality products and increased customer satisfaction.
Cost Reduction
Process capability analysis can also lead to cost savings.
By ensuring processes are capable, manufacturers can reduce scrap, rework, and waste.
This efficiency translates into lower production costs and higher profit margins.
Predictive Maintenance
Regular process capability analysis helps in predictive maintenance.
By monitoring key metrics, manufacturers can predict when a process might drift out of specification.
Timely interventions can prevent production issues and avoid costly downtime.
Compliance and Standards
Many industries have stringent compliance and quality standards.
Process capability analysis ensures that manufacturing processes meet these standards.
This compliance is critical for maintaining certifications and avoiding legal issues.
Customer Satisfaction
Producing consistent, high-quality products leads to higher customer satisfaction.
When customers receive products that meet or exceed their expectations consistently, it builds trust and loyalty to the brand.
Challenges in Process Capability Analysis
Data Collection Issues
One of the significant challenges is collecting accurate and representative data.
Poor data quality can lead to incorrect conclusions, making it essential to have robust data collection systems.
Process Variability
All processes have inherent variability, and separating this natural variation from special causes can be challenging.
Understanding and controlling variability is crucial for accurate process capability analysis.
Changing Specifications
In some cases, customer requirements and specifications may change over time.
This requires continuous monitoring and adjusting of processes to remain compliant with new standards.
Conclusion
Process capability analysis is a vital tool in manufacturing that helps ensure processes are within acceptable limits.
By understanding and analyzing key metrics such as Cp, Cpk, and Pp, manufacturers can improve quality, reduce costs, and enhance customer satisfaction.
While there are challenges in data collection and variability, the benefits of conducting regular process capability analysis far outweigh the difficulties.
Embracing this analytical approach leads to more efficient and effective manufacturing processes, ultimately driving business success.
資料ダウンロード
QCD調達購買管理クラウド「newji」は、調達購買部門で必要なQCD管理全てを備えた、現場特化型兼クラウド型の今世紀最高の購買管理システムとなります。
ユーザー登録
調達購買業務の効率化だけでなく、システムを導入することで、コスト削減や製品・資材のステータス可視化のほか、属人化していた購買情報の共有化による内部不正防止や統制にも役立ちます。
NEWJI DX
製造業に特化したデジタルトランスフォーメーション(DX)の実現を目指す請負開発型のコンサルティングサービスです。AI、iPaaS、および先端の技術を駆使して、製造プロセスの効率化、業務効率化、チームワーク強化、コスト削減、品質向上を実現します。このサービスは、製造業の課題を深く理解し、それに対する最適なデジタルソリューションを提供することで、企業が持続的な成長とイノベーションを達成できるようサポートします。
オンライン講座
製造業、主に購買・調達部門にお勤めの方々に向けた情報を配信しております。
新任の方やベテランの方、管理職を対象とした幅広いコンテンツをご用意しております。
お問い合わせ
コストダウンが利益に直結する術だと理解していても、なかなか前に進めることができない状況。そんな時は、newjiのコストダウン自動化機能で大きく利益貢献しよう!
(Β版非公開)