- お役立ち記事
- Methods and key points of effective layout design in manufacturing
Methods and key points of effective layout design in manufacturing
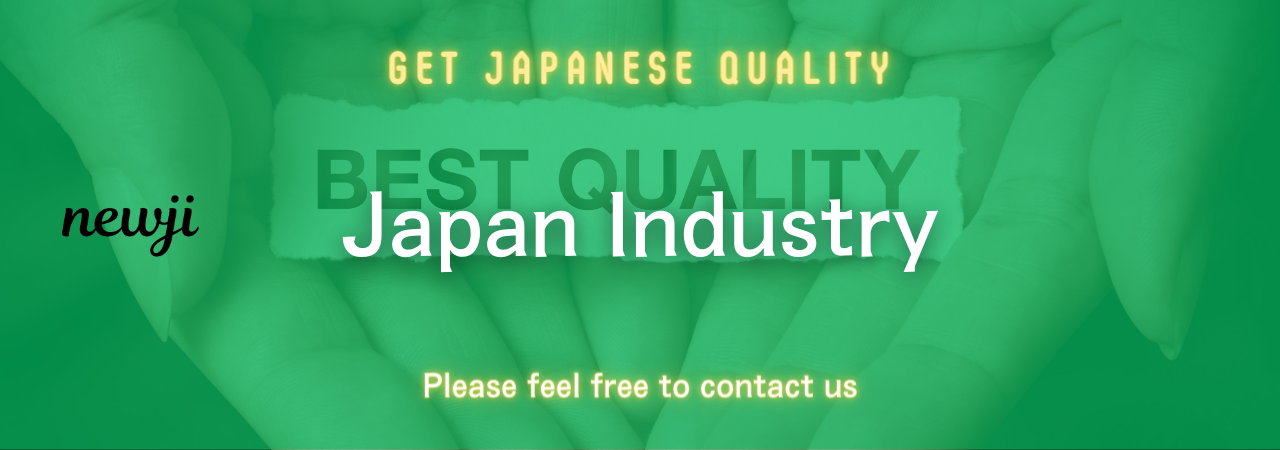
Effective layout design in manufacturing is crucial for optimizing productivity, reducing costs, and improving overall operational efficiency. It involves strategic planning and organization of machines, workstations, and storage areas to ensure a smooth workflow and minimize wasted time and materials. This article will explore key methods and essential points to consider when designing an effective manufacturing layout.
目次
Optimize Space Utilization
The first step in effective layout design is to make optimum use of the available space. Every square foot of a manufacturing facility is valuable, and the objective is to maximize its utility. Here are some tips for optimizing space:
1. Compact Layout: Arrange machines and workstations closely without compromising safety. A compact layout reduces the distance workers need to travel, thereby decreasing non-productive time.
2. Vertical Storage: Use vertical storage solutions like shelves and racks to keep the floor space clear. This method allows easy access to materials and tools while keeping the workspace organized.
3. Multi-functional Areas: Designate areas that can serve multiple purposes, such as flexible workstations that can be easily reconfigured for different tasks.
Workflow Efficiency
Efficiency of workflow is a critical consideration in layout design. An optimized workflow minimizes bottlenecks and ensures a steady production pace:
1. Linear Flow: Arrange machinery and workstations in a linear sequence that follows the production process. This method reduces backtracking and ensures a logical flow from start to finish.
2. Minimize Material Handling: Position machines and stations in a way that minimizes the need for material handling. This involves placing raw materials close to the initial process and finished goods storage near the final point of production.
3. Simplified Movement: Implement straightforward pathways for both workers and materials. Clearly marked aisles and designated walking paths help prevent accidents and confusion.
Flexibility and Scalability
A good manufacturing layout should be flexible and scalable to adapt to changes in production requirements:
1. Modular Design: Utilize a modular approach, where different sections of the layout can be modified or expanded without significant downtime or disruption.
2. Future Expansion: Plan for future growth by incorporating expandable areas or leaving room for additional machinery and workstations.
3. Reconfigurable Workstations: Invest in adjustable and movable workstations that can be adapted for different production tasks as needed.
Safety Considerations
Worker safety should be a top priority in any layout design. Ensuring a safe environment protects employees and reduces the potential for accidents:
1. Clear Emergency Exits: Ensure that all emergency exits are easily accessible and well-marked. Regularly inspect these exits to make sure they are not obstructed.
2. Safety Zones: Establish designated safety zones around high-risk areas, such as machinery with moving parts. Use barriers or floor markings to separate these zones from walkways.
3. Ergonomic Design: Implement ergonomic principles to reduce the risk of repetitive strain injuries. This includes adjustable workstations, proper lighting, and anti-fatigue mats for standing workers.
Technology Integration
The integration of technology can significantly enhance manufacturing efficiency and productivity:
1. Automated Systems: Incorporate automated systems for repetitive and labor-intensive tasks. Automation can improve consistency and reduce human error.
2. Real-Time Monitoring: Use real-time monitoring systems to track production metrics and machine performance. This data can help identify potential issues before they escalate.
3. Digital Layout Planning: Employ digital tools and software for layout planning and simulation. These tools can model different layout scenarios and optimize the design before implementation.
Lean Manufacturing Principles
Lean manufacturing principles aim to reduce waste and increase efficiency. Integrating these principles into the layout design can lead to substantial improvements:
1. 5S Methodology: This system emphasizes Sort, Set in order, Shine, Standardize, and Sustain to create an organized and efficient workspace.
2. Value Stream Mapping: Analyze the entire production process to identify and eliminate waste. Focus on value-added activities and streamline non-value-added tasks.
3. Continuous Improvement: Foster a culture of continuous improvement by encouraging feedback from workers and regularly reviewing and refining the layout.
Employee Input and Training
Involve employees in the layout design process and provide adequate training to ensure they can operate efficiently within the new layout:
1. Worker Feedback: Solicit input from the employees who will be using the space. They can offer valuable insights into potential inefficiencies and suggest practical improvements.
2. Training Programs: Implement comprehensive training programs to acquaint workers with the new layout and any new equipment or processes.
3. Adaptability: Encourage workers to adapt to changes and be flexible in their approach. Provide support and resources to help them transition smoothly.
Regular Assessment and Adjustment
Lastly, an effective layout is not static. Regular assessment and adjustment are necessary to maintain and improve efficiency:
1. Periodic Reviews: Conduct scheduled reviews of the layout to identify areas that may need adjustment. This allows the facility to evolve with changing production needs.
2. Performance Metrics: Use key performance indicators (KPIs) to measure the effectiveness of the layout. Metrics such as cycle time, throughput, and downtime can provide insights into areas for improvement.
3. Feedback Loop: Establish a feedback loop where employees can continuously report issues and suggest improvements. This ensures that the layout remains dynamic and responsive to the operational environment.
In conclusion, effective layout design in manufacturing is a multi-faceted process that requires careful planning and consideration of various factors. From optimizing space and workflow efficiency to integrating technology and ensuring safety, each element plays a vital role in creating a productive and efficient manufacturing environment. By incorporating these methods and key points, manufacturers can enhance their operational performance and maintain a competitive edge in the industry.
資料ダウンロード
QCD調達購買管理クラウド「newji」は、調達購買部門で必要なQCD管理全てを備えた、現場特化型兼クラウド型の今世紀最高の購買管理システムとなります。
ユーザー登録
調達購買業務の効率化だけでなく、システムを導入することで、コスト削減や製品・資材のステータス可視化のほか、属人化していた購買情報の共有化による内部不正防止や統制にも役立ちます。
NEWJI DX
製造業に特化したデジタルトランスフォーメーション(DX)の実現を目指す請負開発型のコンサルティングサービスです。AI、iPaaS、および先端の技術を駆使して、製造プロセスの効率化、業務効率化、チームワーク強化、コスト削減、品質向上を実現します。このサービスは、製造業の課題を深く理解し、それに対する最適なデジタルソリューションを提供することで、企業が持続的な成長とイノベーションを達成できるようサポートします。
オンライン講座
製造業、主に購買・調達部門にお勤めの方々に向けた情報を配信しております。
新任の方やベテランの方、管理職を対象とした幅広いコンテンツをご用意しております。
お問い合わせ
コストダウンが利益に直結する術だと理解していても、なかなか前に進めることができない状況。そんな時は、newjiのコストダウン自動化機能で大きく利益貢献しよう!
(Β版非公開)