- お役立ち記事
- Methods and practices for building design quality through standardization, FMEA/FTA, and quality engineering (Taguchi method)
月間76,176名の
製造業ご担当者様が閲覧しています*
*2025年3月31日現在のGoogle Analyticsのデータより
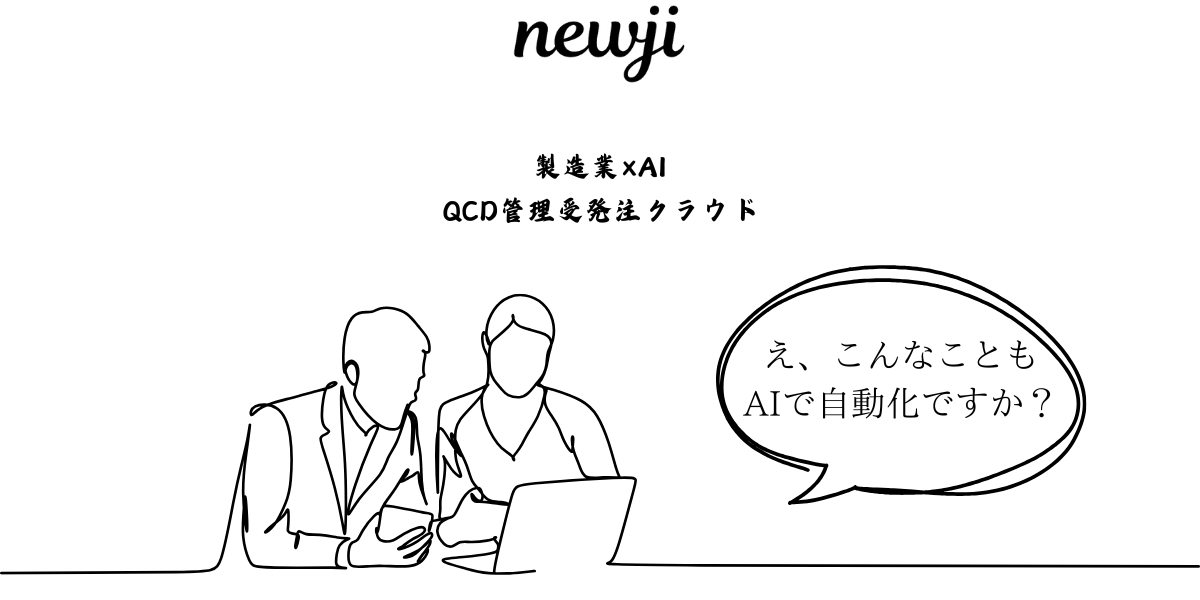
Methods and practices for building design quality through standardization, FMEA/FTA, and quality engineering (Taguchi method)
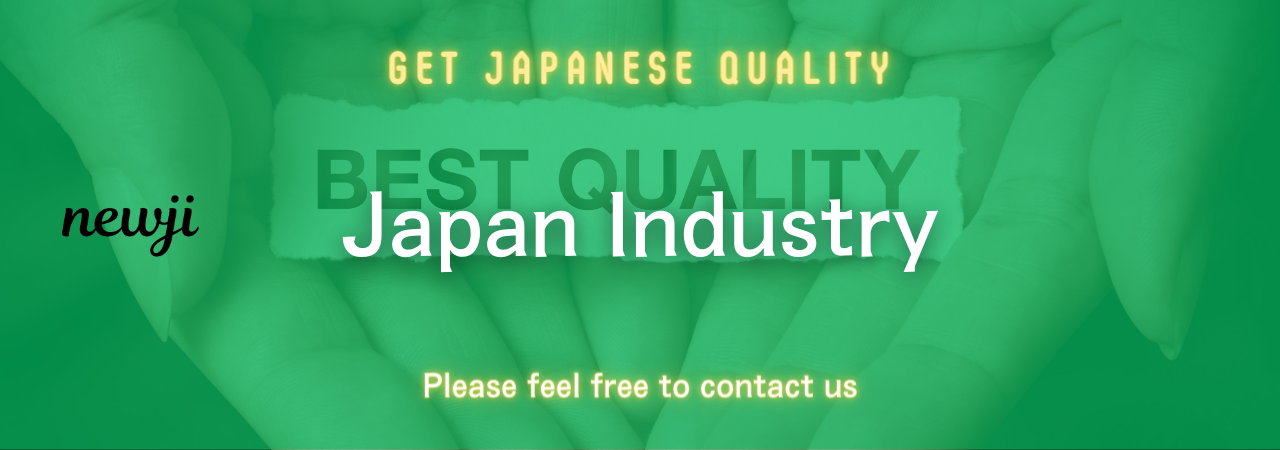
目次
Understanding Standardization in Building Design
Standardization is a critical aspect of building design that ensures consistency, efficiency, and high-quality outcomes.
By implementing standardized processes and guidelines, architects and construction teams can ensure that each project adheres to a set framework that promotes uniformity and reliability.
This approach not only streamlines the design process but also minimizes errors and reduces costs by preventing the repetition of mistakes.
In essence, standardization serves as a foundational tool in enhancing design quality and maintaining high standards across different projects.
Benefits of Standardization
One of the primary benefits of standardization in building design is improved efficiency.
With clearly defined standards, all team members are on the same page, which facilitates clear communication and collaboration.
It also provides a benchmark for measuring quality, making it easier to identify areas that need improvement.
Additionally, standardization contributes to safer construction practices by reducing variability and ensuring compliance with safety regulations.
Methods for Implementing Standardization
To effectively implement standardization in building design, organizations can adopt various methods.
These include setting up design templates, using pre-defined construction materials, and applying modular construction techniques.
Furthermore, regular training for team members on standardized practices can help reinforce these principles and ensure consistent application across projects.
Exploring FMEA and Its Role in Building Design
Failure Mode and Effects Analysis (FMEA) is a systematic approach used to identify potential failures in a design process.
By analyzing possible failure modes, their causes, and their effects, teams can develop strategies to mitigate risks and improve design robustness.
In the context of building design, FMEA helps in anticipating potential issues and implementing preventive measures, thereby enhancing the overall quality of the project.
Steps Involved in FMEA
The FMEA process involves several key steps.
First, the team identifies all possible failure modes for each component of the design.
Next, they assess the likelihood and potential impact of each failure mode.
This assessment allows the team to prioritize risks based on their severity and likelihood, guiding them in developing appropriate mitigation strategies.
By documenting the entire process, FMEA provides valuable insights that can inform future projects.
Advantages of Using FMEA
The primary advantage of FMEA is its proactive approach to risk management.
By identifying potential problems early in the design process, teams can implement solutions before any issues occur.
This not only prevents costly delays and reworks but also contributes to safer and more reliable building designs.
Moreover, FMEA facilitates continuous improvement by providing a framework for evaluating and learning from past projects.
Introducing FTA in Building Design
Fault Tree Analysis (FTA) is another powerful tool used in building design to enhance quality and reliability.
This technique involves constructing a visual representation of the various pathways that can lead to a particular failure.
By mapping out these pathways, teams can identify root causes of failures and implement corrective actions to prevent their occurrence.
The FTA Process
The FTA process begins with defining the top-level failure or undesired event.
From there, the team creates a fault tree diagram that illustrates all potential causes of the failure, using logical gates to depict how different events are connected.
By analyzing this diagram, teams can pinpoint weak points in the design and develop strategies to address them.
FTA Benefits in Building Design
One of the key benefits of FTA is its ability to provide a comprehensive overview of potential failure scenarios.
This holistic perspective enables teams to understand the interrelationships between different components and how they contribute to overall system failure.
As a result, FTA supports more informed decision-making and fosters the development of robust design solutions.
Quality Engineering with the Taguchi Method
Quality engineering plays a crucial role in building design by ensuring that the final product meets or exceeds client expectations.
The Taguchi Method is an effective approach within quality engineering that focuses on optimizing design parameters to improve quality and performance.
Understanding the Taguchi Method
The Taguchi Method emphasizes the importance of design rather than inspection as the primary driver of quality.
This approach involves conducting controlled experiments to identify optimal design settings that minimize variation and enhance performance.
By using statistical techniques, the Taguchi Method enables teams to systematically evaluate different design variables and determine the best configuration for achieving desired outcomes.
Implementing the Taguchi Method
To implement the Taguchi Method in building design, teams first define the performance objectives and identify key design parameters.
They then perform a series of experiments to test different combinations of these parameters.
The results of these experiments help teams pinpoint the settings that yield the best performance while minimizing variability.
This data-driven approach facilitates continuous improvement and supports the creation of high-quality, cost-effective designs.
Conclusion
Building design quality is significantly enhanced through the integration of standardization, FMEA/FTA, and quality engineering techniques like the Taguchi Method.
Each of these practices offers unique benefits that complement one another.
Standardization ensures consistency and sets a benchmark for quality.
FMEA and FTA proactively identify and address potential failures.
Meanwhile, the Taguchi Method optimizes design parameters to enhance performance.
By adopting these methods, design teams can deliver projects that are not only efficient and reliable but also meet the highest standards of quality.
資料ダウンロード
QCD管理受発注クラウド「newji」は、受発注部門で必要なQCD管理全てを備えた、現場特化型兼クラウド型の今世紀最高の受発注管理システムとなります。
ユーザー登録
受発注業務の効率化だけでなく、システムを導入することで、コスト削減や製品・資材のステータス可視化のほか、属人化していた受発注情報の共有化による内部不正防止や統制にも役立ちます。
NEWJI DX
製造業に特化したデジタルトランスフォーメーション(DX)の実現を目指す請負開発型のコンサルティングサービスです。AI、iPaaS、および先端の技術を駆使して、製造プロセスの効率化、業務効率化、チームワーク強化、コスト削減、品質向上を実現します。このサービスは、製造業の課題を深く理解し、それに対する最適なデジタルソリューションを提供することで、企業が持続的な成長とイノベーションを達成できるようサポートします。
製造業ニュース解説
製造業、主に購買・調達部門にお勤めの方々に向けた情報を配信しております。
新任の方やベテランの方、管理職を対象とした幅広いコンテンツをご用意しております。
お問い合わせ
コストダウンが利益に直結する術だと理解していても、なかなか前に進めることができない状況。そんな時は、newjiのコストダウン自動化機能で大きく利益貢献しよう!
(β版非公開)