- お役立ち記事
- Methods for Maintaining a Safe Workplace Through Work Environment Measurement
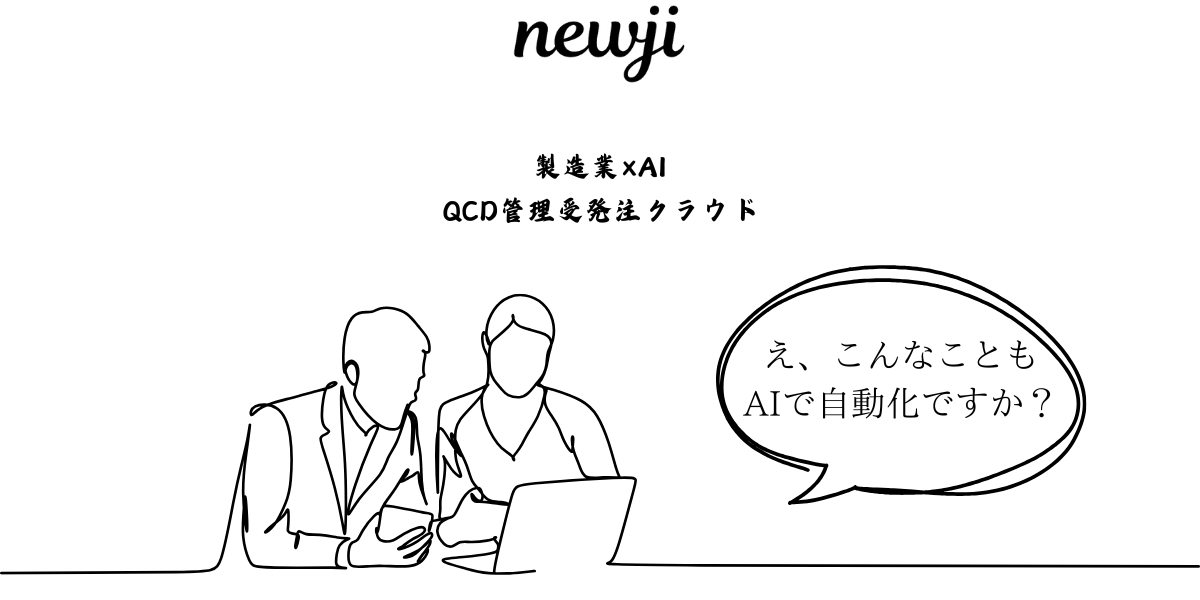
Methods for Maintaining a Safe Workplace Through Work Environment Measurement
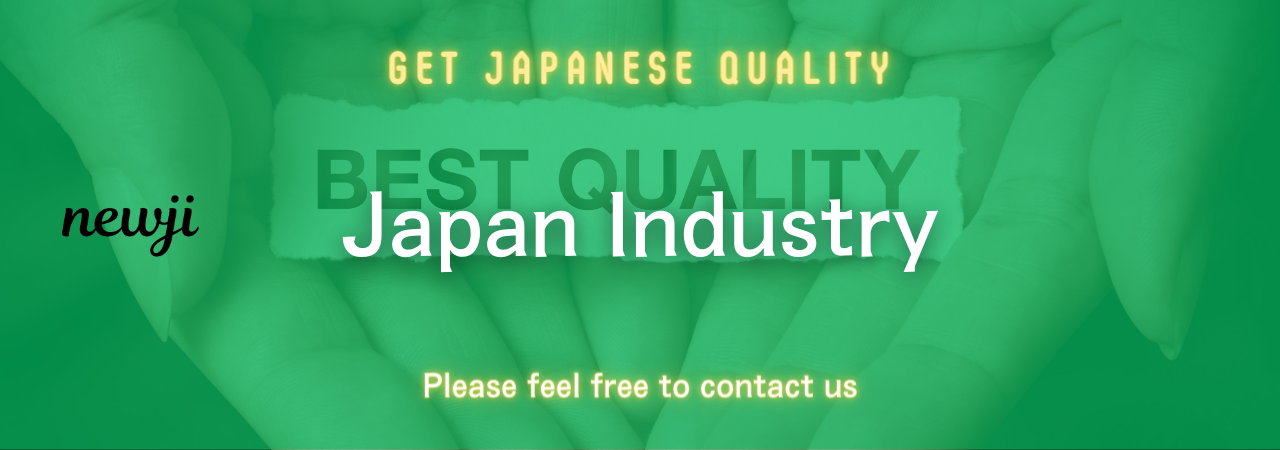
Creating a safe workplace is essential for the well-being of employees and the overall productivity of a business.
One of the most effective ways to ensure workplace safety is through work environment measurement.
This involves assessing various factors within the work environment that could affect health and safety negatively.
By identifying potential hazards and implementing corrective actions, companies can reduce workplace accidents and illnesses dramatically.
目次
Understanding Work Environment Measurement
Work environment measurement is a systematic approach to evaluating the conditions in which employees work.
This comprehensive evaluation can include physical, chemical, biological, and ergonomic factors.
The goal is to identify potential hazards and mitigate them before they cause harm to employees.
Types of Hazards
1. **Physical Hazards:** These include noise, temperature extremes, and radiation.
High noise levels can damage hearing, and temperature extremes can lead to conditions like heat stress or hypothermia.
2. **Chemical Hazards:** These are hazardous substances that employees may be exposed to, such as solvents, fumes, and dust.
Prolonged exposure can lead to serious health issues, including respiratory diseases and skin conditions.
3. **Biological Hazards:** These involve exposure to harmful biological agents like bacteria, viruses, and fungi.
These can cause illness and infections.
4. **Ergonomic Hazards:** These arise from improper workstation design or repetitive movements.
They can lead to musculoskeletal disorders and other physical ailments.
Methods for Measuring the Work Environment
There are several methods used to measure and assess different types of hazards within a workplace.
Each method is tailored to the specific type of hazard being evaluated.
Noise Level Measurement
Noise levels in the workplace can severely affect employees’ hearing.
To measure noise, companies can use sound level meters, which measure the sound pressure levels and provide instantaneous readings.
Another tool is the dosimeter, which workers wear to measure their cumulative noise exposure over a period.
Air Quality Measurement
Air quality is critical, especially in industries where harmful gases, vapors, and particulate matter are present.
Air sampling devices can capture contaminants in the air for analysis.
Additionally, companies may use gas detectors to measure the concentration of specific gases in the workplace atmosphere.
Temperature and Humidity Monitoring
Extreme temperatures and high humidity levels can affect employee health and productivity.
Using thermal hygrometers, companies can monitor the temperature and humidity levels to ensure they remain within a safe range.
By controlling the work environment’s climate, employers can prevent heat stress, dehydration, and other related issues.
Ergonomic Assessment
Ergonomic assessments involve evaluating workstations and tasks to ensure they are designed to fit employees’ needs and capabilities.
This can include analyzing the layout of workstations, tools, and equipment usage.
Effective ergonomic designs can reduce the risk of musculoskeletal injuries and improve overall comfort and productivity.
Implementing Control Measures
Once hazards are identified through work environment measurements, the next step is to implement control measures to mitigate these risks.
Several strategies can be employed depending on the type of hazard identified.
Engineering Controls
These controls involve redesigning processes and equipment to minimize hazards.
For example, installing ventilation systems can improve air quality, while soundproofing materials can reduce noise levels significantly.
Administrative Controls
These involve changing work practices and policies to mitigate risks.
This can include rotating employees to limit exposure to specific hazards and implementing training programs to educate workers about safety practices.
Personal Protective Equipment (PPE)
When engineering and administrative controls are insufficient, PPE can provide an additional layer of protection.
This may include safety goggles, earplugs, gloves, and respirators.
Ensuring that employees have access to the necessary PPE and know how to use it properly is crucial.
Regular Monitoring and Review
Work environment measurement is not a one-time activity.
Regular monitoring and review are essential to maintain a safe work environment.
Employers should conduct periodic assessments to identify any new risks and ensure that existing control measures remain effective.
Continuous Improvement
Workplace safety should be an ongoing focus.
Employers should continually look for ways to improve their safety practices based on the results of their measurements and employee feedback.
This proactive approach can help prevent accidents and ensure a safer working environment.
Compliance with Standards
Adhering to occupational health and safety standards is crucial.
These standards provide guidelines and requirements for maintaining a safe workplace.
Regular work environment measurement ensures compliance with these standards and helps avoid potential legal issues.
Maintaining a safe workplace through work environment measurement is a critical responsibility for employers.
By systematically evaluating and addressing hazards, companies can protect their employees’ health and well-being while enhancing overall productivity.
資料ダウンロード
QCD調達購買管理クラウド「newji」は、調達購買部門で必要なQCD管理全てを備えた、現場特化型兼クラウド型の今世紀最高の購買管理システムとなります。
ユーザー登録
調達購買業務の効率化だけでなく、システムを導入することで、コスト削減や製品・資材のステータス可視化のほか、属人化していた購買情報の共有化による内部不正防止や統制にも役立ちます。
NEWJI DX
製造業に特化したデジタルトランスフォーメーション(DX)の実現を目指す請負開発型のコンサルティングサービスです。AI、iPaaS、および先端の技術を駆使して、製造プロセスの効率化、業務効率化、チームワーク強化、コスト削減、品質向上を実現します。このサービスは、製造業の課題を深く理解し、それに対する最適なデジタルソリューションを提供することで、企業が持続的な成長とイノベーションを達成できるようサポートします。
オンライン講座
製造業、主に購買・調達部門にお勤めの方々に向けた情報を配信しております。
新任の方やベテランの方、管理職を対象とした幅広いコンテンツをご用意しております。
お問い合わせ
コストダウンが利益に直結する術だと理解していても、なかなか前に進めることができない状況。そんな時は、newjiのコストダウン自動化機能で大きく利益貢献しよう!
(Β版非公開)