- お役立ち記事
- Methods for Optimizing Gate Design to Prevent Molding Defects
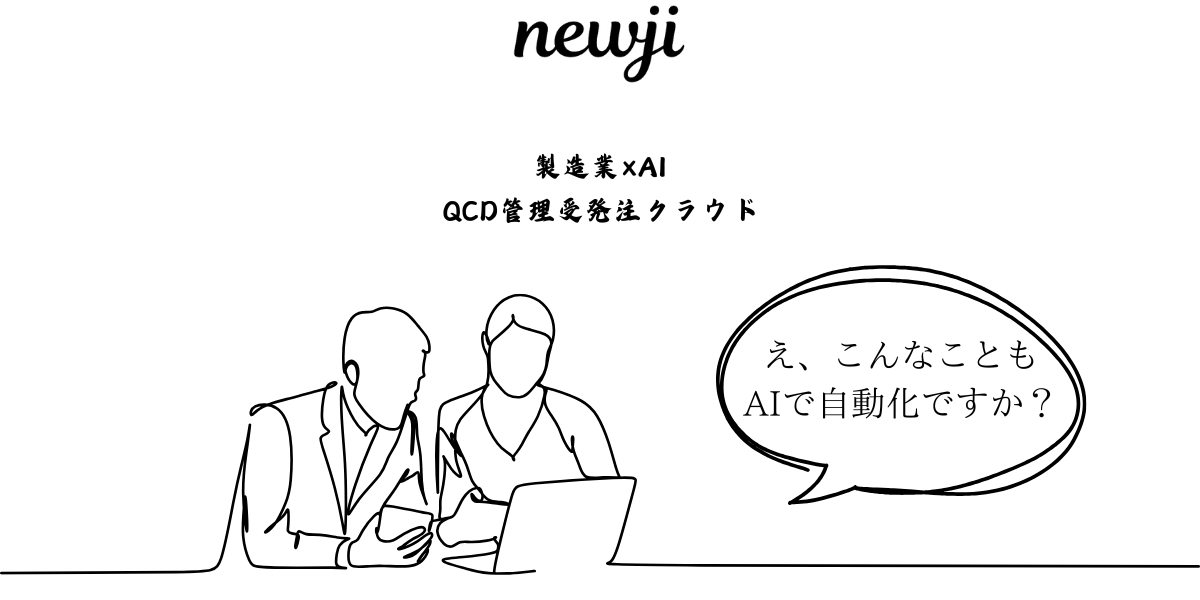
Methods for Optimizing Gate Design to Prevent Molding Defects
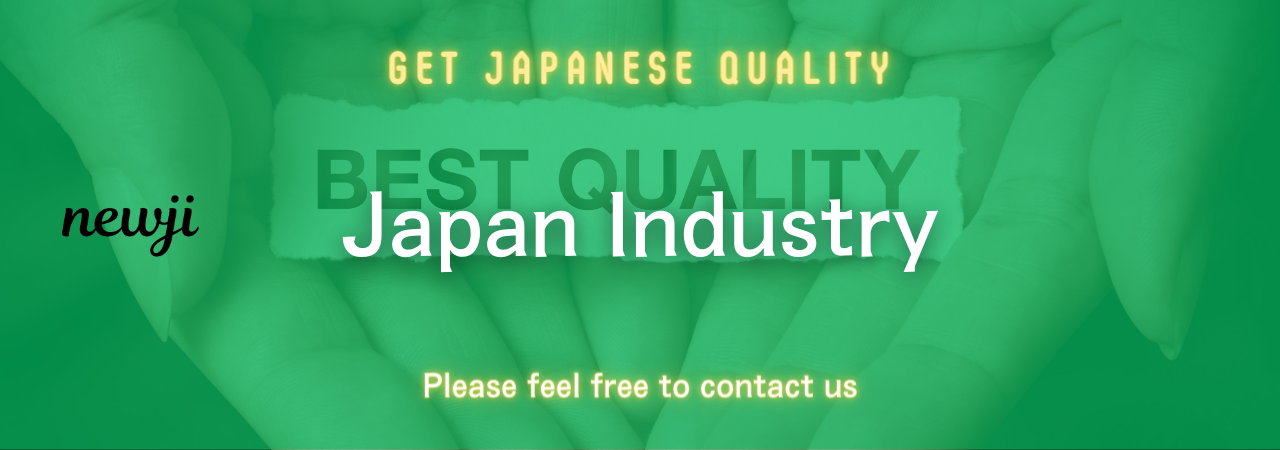
目次
Introduction to Gate Design in Molding
Gate design is a critical aspect of the molding process, influencing the quality and consistency of the final product.
In plastic molding, the gate is an opening through which the molten plastic is injected into the mold cavity.
The design and positioning of the gate play a crucial role in determining the efficiency of the process and the quality of the molded product.
Optimizing gate design helps in minimizing defects, reducing cycle times, and improving product quality.
However, if not properly designed, it can lead to various molding defects such as short shots, warping, and air traps.
This article explores effective methods for optimizing gate design to prevent common molding defects.
Understanding Common Molding Defects
Before discussing optimization techniques, it’s vital to understand the common defects that can occur during the molding process.
Short Shots
One of the most common defects is the short shot, where the mold cavity is not completely filled with the molten material.
This can be due to inadequate gate size, incorrect location, or improper balance between flow rates.
Warping
Warping occurs when there is a discrepancy in shrinkage rates across the molded part.
This can be a result of uneven flow, inappropriate cooling rate, or poor gate design.
Air Traps
Air traps happen when air is trapped inside the mold cavity, leading to incomplete filling and weak spots in the final product.
Improper gate positioning often causes air traps, hindering the escape of air during the fill phase.
Key Considerations in Gate Design
To address these issues and optimize gate design, several key factors should be considered.
Gate Type and Size
Selecting the appropriate gate type (such as pin, edge, or fan gate) and size according to the part and material is essential.
The gate should be as large as possible to ensure sufficient flow, yet suitably small to avoid excessive pressure.
Gate Location
Placement of the gate is crucial for balanced flow and uniform pressure distribution.
Locating the gate near thicker sections can enhance the fill but may need careful cooling control to prevent warping.
The gate should also be positioned to minimize flow length and prevent jetting.
Number of Gates
Determining the number of gates required is dependent on the size, complexity, and shape of the part.
Using multiple gates can facilitate balanced flow, reducing pressure and cycle time.
However, this must be balanced against complexities in mold design and potential weld lines.
Techniques for Optimizing Gate Design
Applying certain methodologies and techniques can help achieve optimal gate design, reducing molding defects significantly.
Computer-Aided Design and Simulation
Utilizing computer-aided design (CAD) tools and simulation software assists in visualizing the flow of material through the mold.
These tools enable predictions of potential defects and allow adjustments in gate size and placement before the actual production begins.
Flow Analysis
Conducting a detailed flow analysis helps in understanding the behavior of plastic melt through the mold.
It enables the prediction and prevention of potential issues like short shots, air traps, and imbalances in flow.
Flow analysis assists in determining optimal gate size, location, and number.
Collaborating with Material Experts
Each material has unique flow properties that can influence gate design decisions.
Collaborating with material experts can provide insights into the best practices for the specific material being used.
These experts can recommend appropriate processing conditions and suitable gate designs for desired outcomes.
Iterative Testing and Refinement
Finally, adopting an iterative approach for testing and refinement helps in continuously improving gate design.
By conducting small-scale trials and analyzing the results, adjustments can be made without extensive resource investments.
Conclusion
Optimizing gate design is paramount in preventing common molding defects and improving product quality.
By considering factors such as gate type, size, location, and using advanced modeling tools, manufacturers can significantly reduce defects like short shots, warping, and air traps.
Effective gate design not only enhances product quality but also contributes to efficient manufacturing processes, reducing waste and cost.
Taking a systematic approach and leveraging technology and expertise will ensure the best outcomes in molding design.
資料ダウンロード
QCD調達購買管理クラウド「newji」は、調達購買部門で必要なQCD管理全てを備えた、現場特化型兼クラウド型の今世紀最高の購買管理システムとなります。
ユーザー登録
調達購買業務の効率化だけでなく、システムを導入することで、コスト削減や製品・資材のステータス可視化のほか、属人化していた購買情報の共有化による内部不正防止や統制にも役立ちます。
NEWJI DX
製造業に特化したデジタルトランスフォーメーション(DX)の実現を目指す請負開発型のコンサルティングサービスです。AI、iPaaS、および先端の技術を駆使して、製造プロセスの効率化、業務効率化、チームワーク強化、コスト削減、品質向上を実現します。このサービスは、製造業の課題を深く理解し、それに対する最適なデジタルソリューションを提供することで、企業が持続的な成長とイノベーションを達成できるようサポートします。
オンライン講座
製造業、主に購買・調達部門にお勤めの方々に向けた情報を配信しております。
新任の方やベテランの方、管理職を対象とした幅広いコンテンツをご用意しております。
お問い合わせ
コストダウンが利益に直結する術だと理解していても、なかなか前に進めることができない状況。そんな時は、newjiのコストダウン自動化機能で大きく利益貢献しよう!
(Β版非公開)