- お役立ち記事
- Methods for SMEs to Achieve Cost Reduction in Grinding
月間76,176名の
製造業ご担当者様が閲覧しています*
*2025年3月31日現在のGoogle Analyticsのデータより
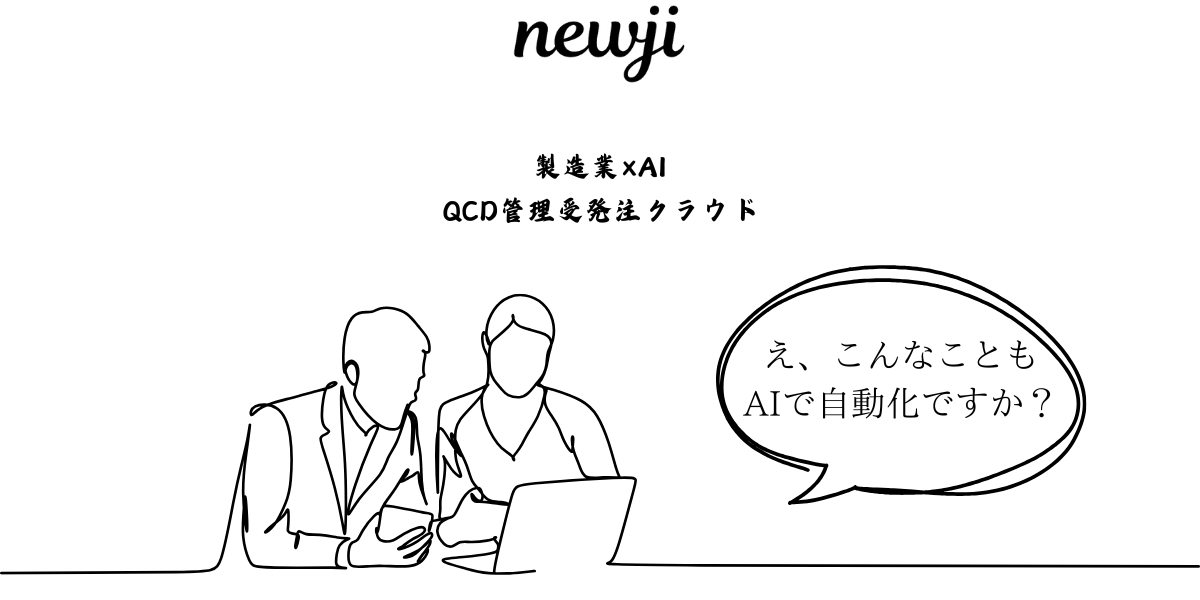
Methods for SMEs to Achieve Cost Reduction in Grinding
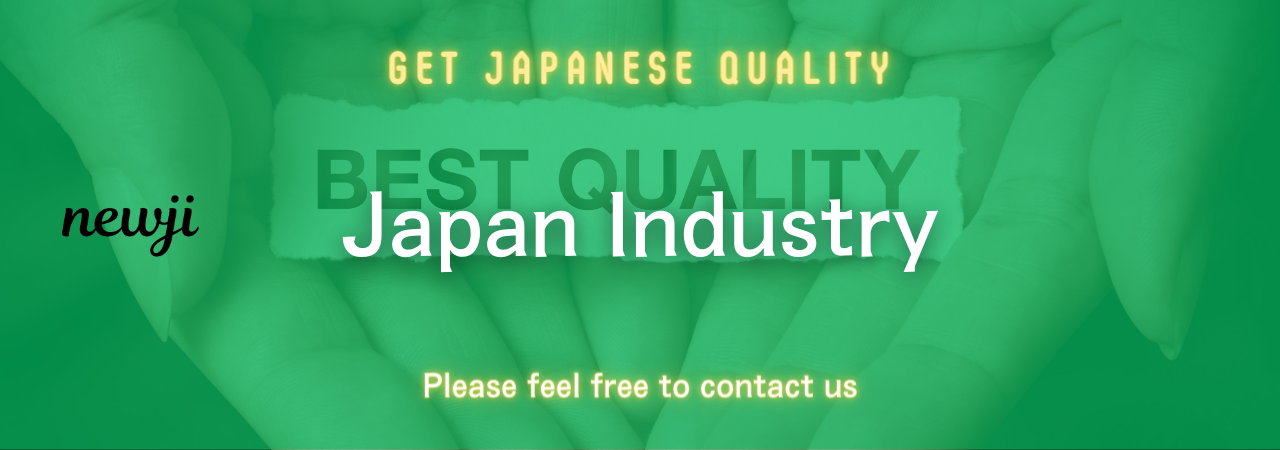
Grinding is a crucial process in many industries, and it is no different for small and medium-sized enterprises (SMEs). However, the costs associated with grinding operations can quickly add up. Here’s how SMEs can achieve cost reduction in their grinding processes without compromising on quality.
目次
Understanding Your Grinding Process
Before making any changes, it is vital to understand the specifics of your current grinding process. Gather data about the types of materials you grind, the frequency of grinding, and the equipment you use. This information will serve as the foundation for making informed decisions about where cost reductions can be implemented.
Invest in High-Quality Grinding Equipment
One way to reduce costs in the long run is by investing in high-quality grinding equipment. Although the initial outlay may be higher, top-of-the-line machinery often requires less maintenance and has a longer lifespan. Look for equipment that offers high efficiency and low energy consumption. This can lead to significant savings over time.
Optimize Grinding Techniques
Proper Wheel Selection
The type of grinding wheel you use can have a significant impact on both the efficiency and cost of your grinding process. Selecting the correct wheel for the material being ground and the type of grinding operation can reduce wear and tear on your equipment, lower energy consumption, and produce better results in less time.
Regular Wheel Dressing
Dressing the grinding wheel regularly is essential for maintaining its efficiency. A well-dressed wheel cuts cleaner and faster, reducing the time and energy required for each operation. This practice also extends the life of the wheel, further contributing to cost savings.
Coolant Usage
Using the appropriate coolant and ensuring proper application can help prevent overheating and damage to both the grinding wheel and the workpiece. This not only improves the quality of your finished product but also extends the life of your equipment and reduces the need for costly repairs.
Employee Training
Well-trained employees are crucial for optimizing grinding operations. Invest in ongoing training programs to ensure your staff is knowledgeable about the latest techniques and technologies. Skilled operators can adjust the grinding process to be more efficient, further reducing costs.
Maintenance and Repairs
Preventive Maintenance
Implementing a preventive maintenance program can save you considerable amounts of money. Regularly scheduled maintenance checks can identify potential issues before they turn into costly repairs. This not only keeps your equipment running smoothly but also extends its lifespan.
In-House Repairs
Training in-house staff to perform basic repairs can also be a cost-saving measure. While some repairs should always be left to the experts, minor fixes can often be handled internally. This reduces downtime and eliminates the need for expensive service calls.
Material Handling and Waste Reduction
Efficient Material Handling
Efficient handling of raw materials can reduce waste and lower costs. Ensure that materials are stored correctly and that they are brought to the grinding area in an orderly fashion. Minimizing the distance materials need to be transported can also reduce labor costs and time.
Recycle and Reuse
Look for opportunities to recycle and reuse materials whenever possible. Not only is this good for the environment, but it can also lead to significant cost savings. Scrap metal and other waste materials can often be repurposed for other operations, reducing the need to purchase new materials.
Energy Efficiency
Electricity costs can be substantial in grinding operations. Consider switching to more energy-efficient equipment and using energy-saving practices to reduce overall consumption. Monitor energy usage and look for patterns or spikes that could indicate inefficiencies.
Automation and Technology
CNC Grinding Machines
Investing in CNC (Computer Numerical Control) grinding machines can increase productivity and reduce labor costs. These machines offer high precision and can be programmed to perform repetitive tasks, freeing up your skilled workers for more complex tasks.
IoT and Industry 4.0
The Internet of Things (IoT) and Industry 4.0 technologies can help monitor and optimize grinding operations. Sensors can provide real-time data on equipment performance, allowing for predictive maintenance and reduced downtime. These technologies can help you make data-driven decisions, leading to more efficient operations.
Outsourcing
In some cases, outsourcing specific grinding tasks to specialized companies can be more cost-effective. This allows you to focus on your core competencies while leaving the grinding operations to experts who already have the necessary equipment and expertise. Be sure to perform a cost-benefit analysis to determine if outsourcing is a viable option for your business.
Conclusion
Reducing costs in grinding operations involves a combination of investing in high-quality equipment, optimizing techniques, training employees, and implementing preventive maintenance programs. By taking a comprehensive approach, SMEs can achieve significant cost savings without compromising on the quality of their products. Remember, the key is to be proactive and continually look for opportunities to improve and innovate.
資料ダウンロード
QCD管理受発注クラウド「newji」は、受発注部門で必要なQCD管理全てを備えた、現場特化型兼クラウド型の今世紀最高の受発注管理システムとなります。
ユーザー登録
受発注業務の効率化だけでなく、システムを導入することで、コスト削減や製品・資材のステータス可視化のほか、属人化していた受発注情報の共有化による内部不正防止や統制にも役立ちます。
NEWJI DX
製造業に特化したデジタルトランスフォーメーション(DX)の実現を目指す請負開発型のコンサルティングサービスです。AI、iPaaS、および先端の技術を駆使して、製造プロセスの効率化、業務効率化、チームワーク強化、コスト削減、品質向上を実現します。このサービスは、製造業の課題を深く理解し、それに対する最適なデジタルソリューションを提供することで、企業が持続的な成長とイノベーションを達成できるようサポートします。
製造業ニュース解説
製造業、主に購買・調達部門にお勤めの方々に向けた情報を配信しております。
新任の方やベテランの方、管理職を対象とした幅広いコンテンツをご用意しております。
お問い合わせ
コストダウンが利益に直結する術だと理解していても、なかなか前に進めることができない状況。そんな時は、newjiのコストダウン自動化機能で大きく利益貢献しよう!
(β版非公開)