- お役立ち記事
- Methods for SMEs to Improve Quality and Productivity in Contract Manufacturing
月間76,176名の
製造業ご担当者様が閲覧しています*
*2025年3月31日現在のGoogle Analyticsのデータより
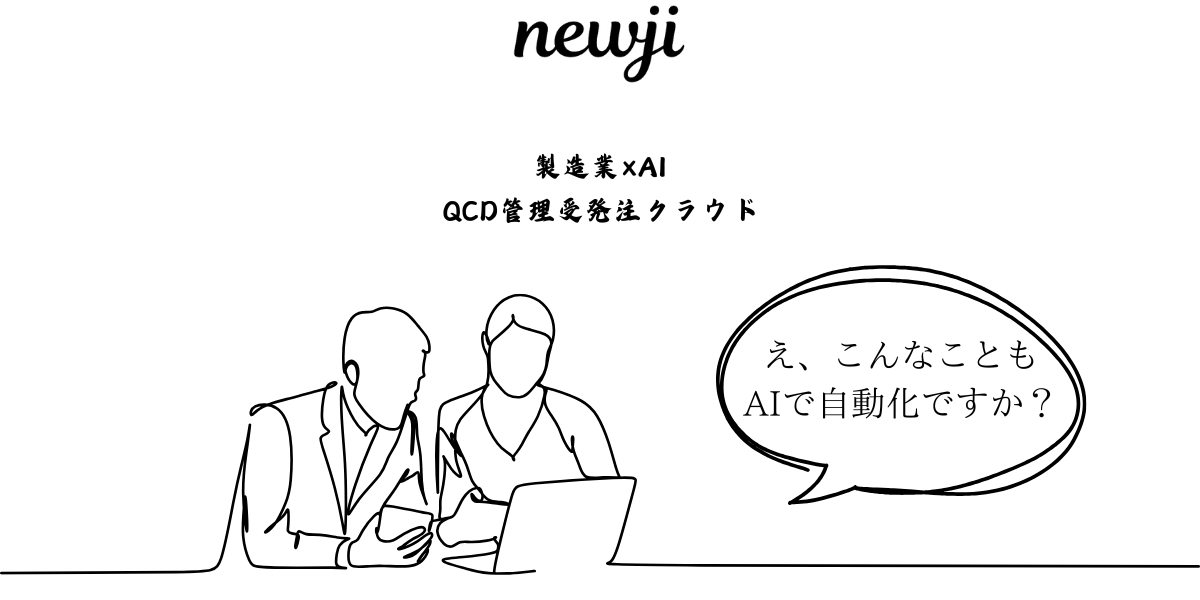
Methods for SMEs to Improve Quality and Productivity in Contract Manufacturing
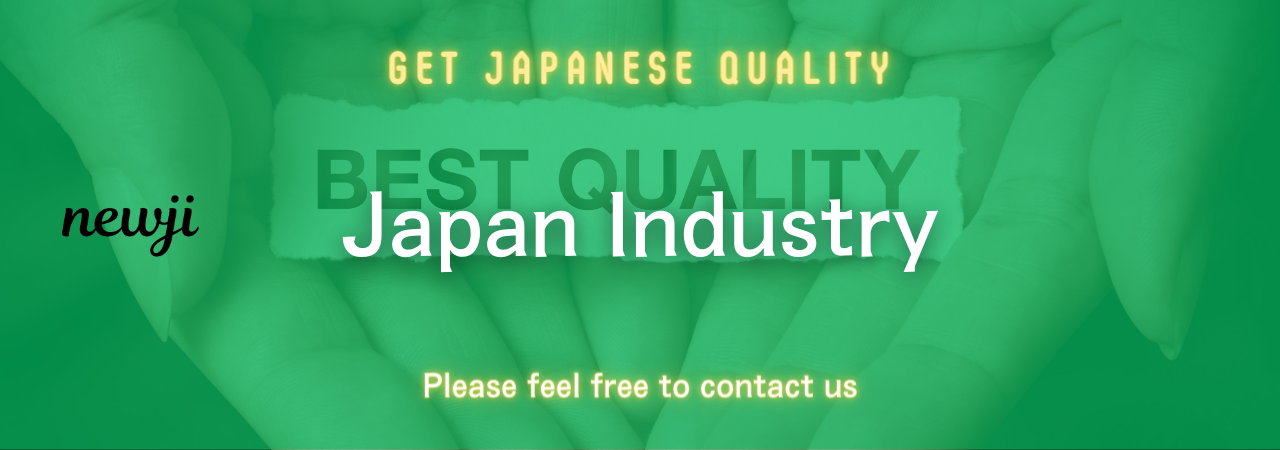
Small and medium-sized enterprises (SMEs) face unique challenges in contract manufacturing.
Competing against larger firms with more resources requires creative and efficient strategies.
Improving quality and productivity is not just a goal but a necessity for survival and growth.
This article explores some effective methods that SMEs can adopt to enhance their contract manufacturing processes.
目次
Implementing Lean Manufacturing Principles
Understanding Lean Manufacturing
Lean manufacturing is a systematic method for waste minimization within a manufacturing system.
This is without sacrificing productivity.
It aims to create more value for customers with fewer resources.
For SMEs, implementing lean manufacturing principles can significantly cut costs and improve efficiency.
Reducing Waste
One of the core principles of lean manufacturing is eliminating waste.
This includes everything that does not add value to the end product.
Common types of waste in manufacturing include overproduction, waiting time, excess inventory, and defective products.
By identifying and reducing these wastes, SMEs can enhance their productivity and product quality.
Investing in Employee Training
The Importance of Skilled Workers
Employees are the backbone of any manufacturing process.
For SMEs, having well-trained and skilled workers can make a big difference.
These workers are better equipped to handle complex tasks, leading to fewer mistakes and higher quality.
Continuous Learning
Investing in continuous learning programs ensures that employees are always up-to-date with the latest industry standards and technologies.
Regular training sessions, workshops, and certifications can help employees acquire new skills and improve existing ones.
This, in turn, boosts overall productivity and quality.
Utilizing Advanced Technology
Automation and Robotics
Incorporating advanced technology like automation and robotics can greatly enhance manufacturing efficiency.
Automation reduces human error, speeds up production processes, and can operate around the clock.
For SMEs, investing in automation might seem costly initially but can lead to substantial long-term benefits.
Data Analytics
Data analytics is another powerful tool for improving productivity and quality in contract manufacturing.
By analyzing production data, SMEs can gain insights into process efficiencies and identify areas for improvement.
This data-driven approach helps in making informed decisions that enhance productivity and product quality.
Focusing on Quality Control
Effective Quality Management Systems
Implementing effective quality management systems (QMS) like ISO 9001 can help SMEs meet customer expectations consistently.
A QMS provides a framework for managing and improving manufacturing processes.
This ensures that the end products meet quality standards and customer requirements.
Regular Audits and Inspections
Regular audits and inspections are essential for maintaining high-quality standards.
These audits help identify any deviations from the set processes and allow for timely corrections.
Regular inspections ensure that everything is running smoothly and that the products meet the desired quality levels.
Improving Supplier Relationships
Choosing the Right Suppliers
Suppliers play a crucial role in the manufacturing process.
Choosing reliable and quality-conscious suppliers can make a significant difference in the final product quality.
SMEs should establish strong relationships with their suppliers and work closely with them to ensure materials meet the required standards.
Effective Communication
Maintaining open and effective communication with suppliers is essential.
Clear communication ensures that any issues are addressed promptly.
It also helps in coordinating production schedules, which can improve overall productivity.
Implementing Continuous Improvement
Adopting the Kaizen Philosophy
Kaizen, a Japanese term meaning “continuous improvement,” can be a game-changer for SMEs.
This philosophy focuses on small, incremental changes that lead to significant improvements over time.
Implementing Kaizen involves everyone in the organization, from top management to frontline workers, fostering a culture of continuous improvement.
Regular Review Meetings
Regular review meetings are crucial for continuous improvement.
These meetings provide an opportunity to discuss what is working well and what needs improvement.
By regularly reviewing processes and performances, SMEs can make necessary adjustments to enhance quality and productivity.
Conclusion
Improving quality and productivity in contract manufacturing is essential for SMEs to thrive in a competitive market.
By implementing lean manufacturing principles, investing in employee training, using advanced technology, focusing on quality control, improving supplier relationships, and adopting continuous improvement practices, SMEs can achieve significant improvements in their manufacturing processes.
These steps not only enhance product quality and productivity but also lead to customer satisfaction and business growth.
資料ダウンロード
QCD管理受発注クラウド「newji」は、受発注部門で必要なQCD管理全てを備えた、現場特化型兼クラウド型の今世紀最高の受発注管理システムとなります。
ユーザー登録
受発注業務の効率化だけでなく、システムを導入することで、コスト削減や製品・資材のステータス可視化のほか、属人化していた受発注情報の共有化による内部不正防止や統制にも役立ちます。
NEWJI DX
製造業に特化したデジタルトランスフォーメーション(DX)の実現を目指す請負開発型のコンサルティングサービスです。AI、iPaaS、および先端の技術を駆使して、製造プロセスの効率化、業務効率化、チームワーク強化、コスト削減、品質向上を実現します。このサービスは、製造業の課題を深く理解し、それに対する最適なデジタルソリューションを提供することで、企業が持続的な成長とイノベーションを達成できるようサポートします。
製造業ニュース解説
製造業、主に購買・調達部門にお勤めの方々に向けた情報を配信しております。
新任の方やベテランの方、管理職を対象とした幅広いコンテンツをご用意しております。
お問い合わせ
コストダウンが利益に直結する術だと理解していても、なかなか前に進めることができない状況。そんな時は、newjiのコストダウン自動化機能で大きく利益貢献しよう!
(β版非公開)