- お役立ち記事
- Methods to Achieve High Precision in Surface Treatment with Electroplating
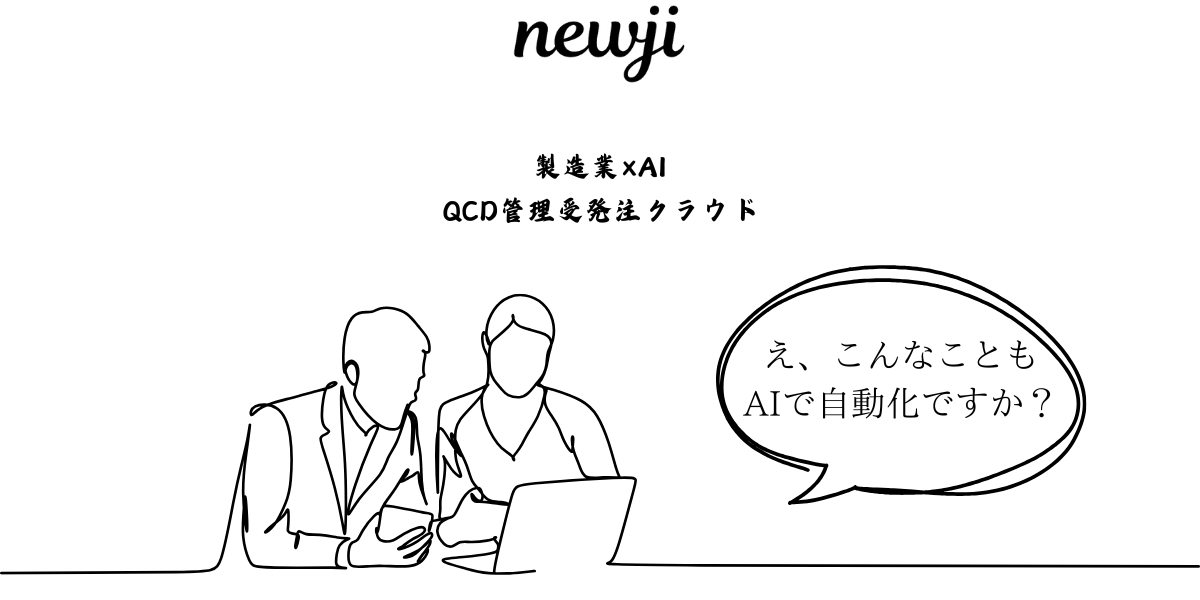
Methods to Achieve High Precision in Surface Treatment with Electroplating
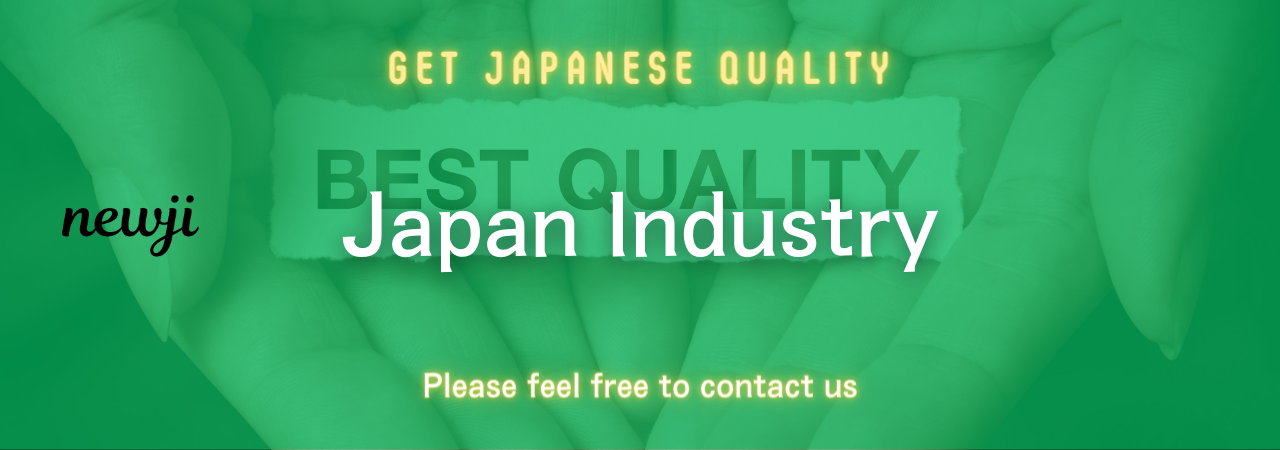
Electroplating is a technique widely used to enhance the surface properties of various materials.
It involves coating an object with a thin layer of metal through an electrochemical process.
Achieving high precision in surface treatment with electroplating is crucial for ensuring durability, aesthetic appeal, and functional performance.
This article delves into the methods and practices that lead to superior precision in electroplating.
目次
Understanding the Basics of Electroplating
Electroplating is a process that uses an electric current to reduce dissolved metal cations, allowing them to form a coherent metal coating on an electrode.
The object to be plated acts as the cathode, while the metal to be deposited serves as the anode.
The electrolyte solution facilitates the transfer of metal ions between the electrodes.
Understanding the fundamental concepts of this process sets the foundation for achieving high-precision results.
Choosing the Right Electroplating Solution
Types of Electroplating Solutions
Various electroplating solutions exist, each suited for different metals and applications.
Common types include acidic, alkaline, and neutral solutions.
The choice of solution significantly impacts the quality of the plating.
For instance, acidic solutions are often used for plating metals like gold and silver, while alkaline solutions might be preferred for zinc or cadmium plating.
Optimizing Solution Composition
The composition of the electroplating solution is integral to achieving precision.
Concentration of metal ions, pH levels, and the presence of additives like brighteners or leveling agents must be meticulously controlled.
Regular monitoring and maintenance of the solution’s composition help in preventing defects like pitting, roughness, or uneven thickness.
Surface Preparation Techniques
Cleaning the Substrate
Before electroplating, the substrate must be thoroughly cleaned to ensure proper adhesion of the metal layer.
Contaminants such as oils, dirt, and oxidation can hinder the plating process.
Methods such as alkaline cleaning, acid etching, and ultrasonic cleaning are effective in preparing the surface.
Each cleaning technique must be chosen based on the type of substrate and the desired outcome.
Surface Conditioning
Surface conditioning involves modifying the surface properties to improve the adhesion of the electroplated layer.
Techniques such as mechanical polishing, sandblasting, or chemical treatments can be employed.
The goal is to create a uniform, defect-free surface that promotes high-quality plating.
Controlling the Electroplating Process
Current Density and Distribution
One of the critical factors in electroplating precision is the control of current density.
The current density affects the rate of deposition and the overall thickness of the plated layer.
Uniform current distribution ensures even coating without defects.
Using conforming anodes and auxiliary cathodes helps in achieving consistent current density, especially on complex geometries.
Temperature Regulation
The temperature of the electroplating bath influences the deposition rate and the physical properties of the plated layer.
Maintaining an optimal temperature range is essential for achieving uniform and smooth coatings.
Temperature fluctuations can lead to inconsistent thickness and reduced adhesion strength.
Employing temperature control systems ensures a stable electroplating environment.
Advanced Techniques for Precision Electroplating
Pulse Electroplating
Pulse electroplating involves the application of intermittent current pulses instead of a continuous direct current.
This technique allows for better control over the deposition process, resulting in finer grain structures and improved surface quality.
Pulse parameters such as on-time, off-time, and peak current must be optimized to achieve the desired results.
Brush Electroplating
Brush electroplating is a selective plating technique where a brush saturated with electrolyte solution is used to apply the metal coating.
This method is ideal for localized surface treatment or repair work.
It offers high precision in targeting specific areas without affecting the surrounding material.
Proper brush selection and technique are crucial for achieving a high-quality finish.
Quality Control and Inspection
Thickness Measurement
Accurate measurement of the plated layer’s thickness is vital for ensuring that it meets the desired specifications.
Techniques such as X-ray fluorescence (XRF), eddy current testing, and micrometer measurements are commonly used.
Regular thickness inspections help in maintaining consistency and adherence to quality standards.
Surface Roughness and Defect Analysis
Surface roughness and the presence of defects such as cracks, pits, or inclusions can impact the performance and appearance of the plated layer.
Advanced inspection methods like scanning electron microscopy (SEM) and atomic force microscopy (AFM) provide detailed analysis of the surface topography.
Implementing stringent quality control protocols helps in identifying and rectifying issues early in the process.
Post-Plating Treatments
Heat Treatment
Post-plating heat treatment can improve the mechanical properties and adhesion strength of the plated layer.
Processes such as annealing or baking help in relieving internal stresses and enhancing the bond between the substrate and the coating.
The specific heat treatment parameters depend on the type of metal and the desired properties.
Passivation and Sealing
Passivation treatments involve the application of protective coatings to enhance the corrosion resistance of the plated layer.
Sealing processes can also improve the wear resistance and longevity of the surface.
Choosing the appropriate post-plating treatment ensures that the electroplated components meet their intended performance criteria.
Achieving high precision in surface treatment with electroplating requires a comprehensive understanding of the process and meticulous control over various parameters.
From selecting the right electroplating solution to implementing advanced techniques and maintaining stringent quality control, each step plays a vital role in producing superior, high-quality coatings.
Through diligent practice and continuous improvement, industries can ensure that their electroplated products exhibit the desired characteristics and stand the test of time.
資料ダウンロード
QCD調達購買管理クラウド「newji」は、調達購買部門で必要なQCD管理全てを備えた、現場特化型兼クラウド型の今世紀最高の購買管理システムとなります。
ユーザー登録
調達購買業務の効率化だけでなく、システムを導入することで、コスト削減や製品・資材のステータス可視化のほか、属人化していた購買情報の共有化による内部不正防止や統制にも役立ちます。
NEWJI DX
製造業に特化したデジタルトランスフォーメーション(DX)の実現を目指す請負開発型のコンサルティングサービスです。AI、iPaaS、および先端の技術を駆使して、製造プロセスの効率化、業務効率化、チームワーク強化、コスト削減、品質向上を実現します。このサービスは、製造業の課題を深く理解し、それに対する最適なデジタルソリューションを提供することで、企業が持続的な成長とイノベーションを達成できるようサポートします。
オンライン講座
製造業、主に購買・調達部門にお勤めの方々に向けた情報を配信しております。
新任の方やベテランの方、管理職を対象とした幅広いコンテンツをご用意しております。
お問い合わせ
コストダウンが利益に直結する術だと理解していても、なかなか前に進めることができない状況。そんな時は、newjiのコストダウン自動化機能で大きく利益貢献しよう!
(Β版非公開)