- お役立ち記事
- Methods to Improve Quality by Optimizing Production Processes
月間76,176名の
製造業ご担当者様が閲覧しています*
*2025年3月31日現在のGoogle Analyticsのデータより
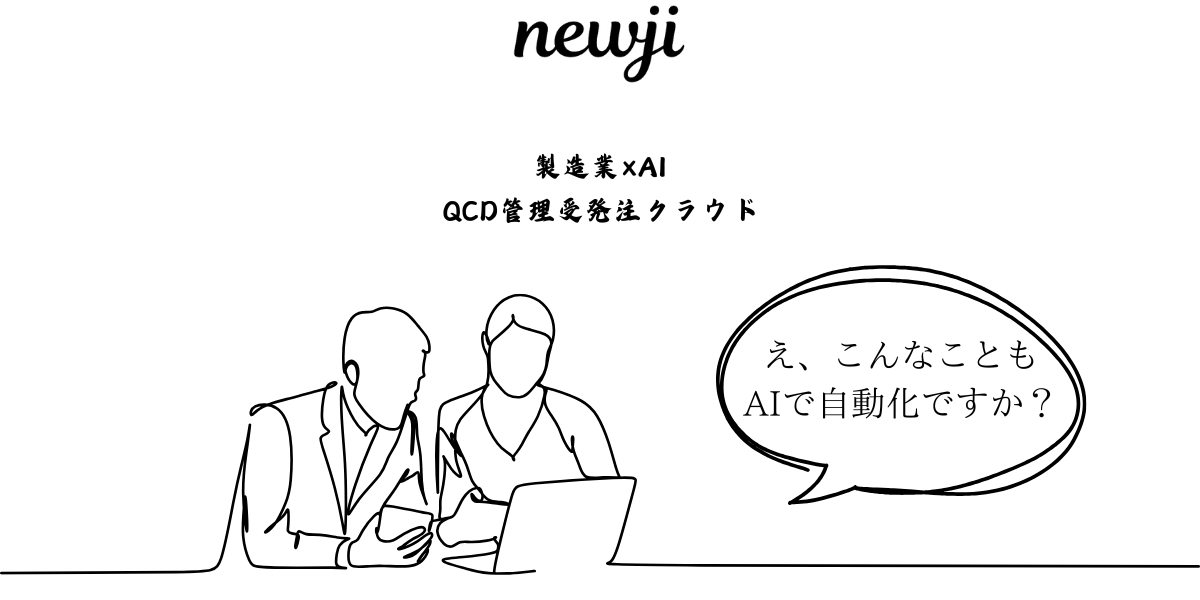
Methods to Improve Quality by Optimizing Production Processes
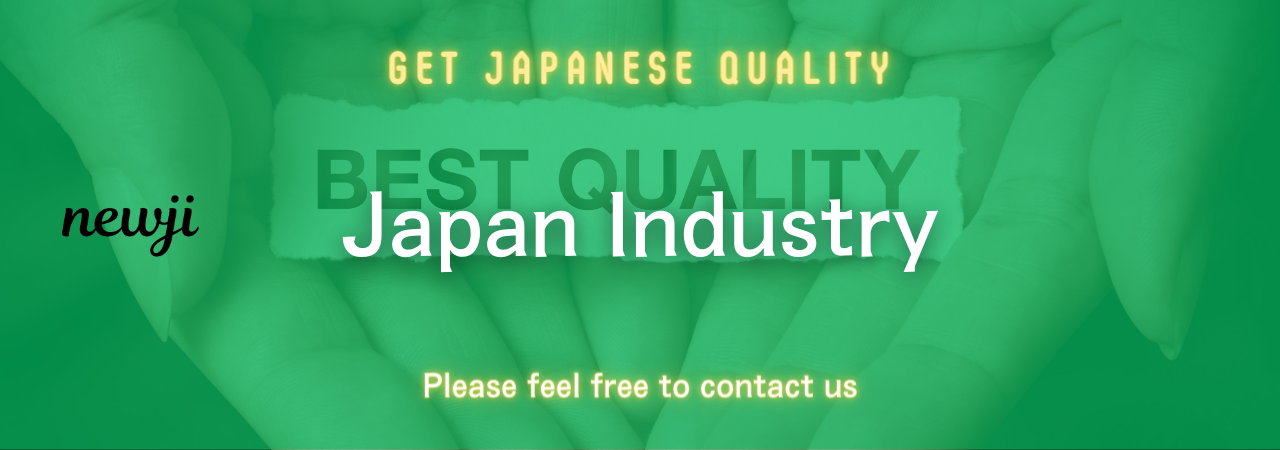
Optimizing production processes is a crucial aspect of improving the quality of products in any industry.
Companies that are eager to excel in today’s competitive market have to focus on streamlining their production methods.
This article will explore various methods to enhance production processes and, consequently, improve product quality.
目次
Defining Production Processes
Production processes involve the steps taken to convert raw materials into finished products.
These processes vary across industries, but they generally include design, material selection, manufacturing, assembly, and inspection.
By optimizing these steps, companies can achieve higher efficiency and better quality outcomes.
Understanding the Importance of Quality
Quality is the standard of a product or service as measured against similar products.
High-quality products meet the needs and expectations of customers, leading to greater satisfaction and loyalty.
Poor quality can result in customer dissatisfaction, increased returns, and potentially, lost business.
Therefore, focusing on optimizing production processes is essential for maintaining high quality.
Analyzing and Identifying Inefficiencies
Before making any changes, it’s essential to analyze current production processes and identify inefficiencies.
This can be done through various methods, including:
Data Collection and Analysis
Gathering and analyzing data from different stages of production can highlight where inefficiencies exist.
This data can include production times, defect rates, and resource usage.
Employee Feedback
Employees working directly in the production process often have insights into where bottlenecks or issues occur.
Encouraging open communication and feedback can reveal valuable information for optimization.
Using Process Flowcharts
Creating flowcharts of the production process can provide a visual understanding of each step.
These charts can help identify redundant or slow processes that need improvement.
Implementing Lean Manufacturing
Lean manufacturing focuses on minimizing waste without sacrificing productivity.
Implementing lean principles can lead to significant improvements in production efficiency and product quality.
5S Methodology
The 5S methodology stands for Sort, Set in Order, Shine, Standardize, and Sustain.
Applying these steps can organize the workplace, reduce waste, and improve efficiency.
Value Stream Mapping
Value stream mapping involves analyzing the flow of materials and information required to bring a product to the customer.
By optimizing this flow, companies can reduce delays and eliminate non-value-adding activities.
Continuous Improvement (Kaizen)
Kaizen promotes continuous, incremental improvements in production processes.
Encouraging employees to seek small, daily improvements can lead to significant long-term gains.
Utilizing Technology for Process Optimization
Technology can play a crucial role in optimizing production processes.
Implementing advanced tools and systems can help enhance precision, reduce errors, and increase efficiency.
Automation
Automating repetitive and labor-intensive tasks can speed up production and reduce human errors.
Automation can include the use of robotics, conveyor systems, and automated quality inspections.
Quality Management Systems (QMS)
QMS software helps monitor and manage quality throughout the production process.
These systems can track defects, manage compliance, and ensure that quality standards are consistently met.
Real-Time Monitoring
Implementing real-time monitoring systems can provide instant feedback on production performance.
This allows for quick adjustments and corrections, minimizing the impact of any issues that arise.
Training and Developing Skilled Workforce
The skills and knowledge of employees play a significant role in the quality of production.
Investing in training and development can improve efficiency and attention to detail in the production process.
Regular Training Programs
Conducting regular training sessions for employees on the latest techniques and technologies can keep them updated and proficient.
This is essential for maintaining high standards of quality.
Cross-Training
Cross-training employees to handle multiple roles can provide flexibility in the production process.
It ensures that there are no disruptions due to the absence of key personnel and helps in quick problem resolution.
Quality Awareness Programs
Implementing quality awareness programs can emphasize the importance of quality in every aspect of production.
Encouraging a culture of quality among employees can lead to better products.
Implementing Regular Audits and Reviews
Regular audits and reviews are essential to ensure that production processes are being followed correctly and are continuously improving.
Internal Audits
Conducting internal audits can help identify discrepancies and areas for improvement within the production process.
These audits should be regular and thorough.
Third-Party Audits
Engaging third-party auditors can provide an unbiased review of production processes.
External audits can often uncover issues that internal teams might overlook.
Performance Reviews
Regular performance reviews of the production process can help track progress and the effectiveness of implemented changes.
These reviews should be data-driven and include input from various stakeholders.
Focusing on Supplier Quality Management
The quality of raw materials significantly impacts the final product’s quality.
Therefore, it’s crucial to ensure that suppliers also maintain high-quality standards.
Supplier Audits
Conducting regular audits of suppliers can ensure that they follow quality standards.
This can involve reviewing their production processes, quality systems, and compliance with regulations.
Supplier Partnerships
Developing strong partnerships with suppliers can lead to better communication and collaboration.
Working closely with suppliers can help in resolving quality issues quickly and efficiently.
Supplier Performance Metrics
Tracking and analyzing supplier performance metrics can help in assessing their reliability and quality.
Key metrics can include on-time delivery, defect rates, and responsiveness to issues.
Conclusion
Optimizing production processes is an ongoing effort that requires a comprehensive approach.
By analyzing and identifying inefficiencies, implementing lean manufacturing techniques, utilizing technology, training the workforce, conducting regular audits, and managing supplier quality, companies can significantly improve their production processes and product quality.
In the ever-evolving market, continuous improvement and adaptation are key to maintaining high standards and achieving long-term success.
資料ダウンロード
QCD管理受発注クラウド「newji」は、受発注部門で必要なQCD管理全てを備えた、現場特化型兼クラウド型の今世紀最高の受発注管理システムとなります。
ユーザー登録
受発注業務の効率化だけでなく、システムを導入することで、コスト削減や製品・資材のステータス可視化のほか、属人化していた受発注情報の共有化による内部不正防止や統制にも役立ちます。
NEWJI DX
製造業に特化したデジタルトランスフォーメーション(DX)の実現を目指す請負開発型のコンサルティングサービスです。AI、iPaaS、および先端の技術を駆使して、製造プロセスの効率化、業務効率化、チームワーク強化、コスト削減、品質向上を実現します。このサービスは、製造業の課題を深く理解し、それに対する最適なデジタルソリューションを提供することで、企業が持続的な成長とイノベーションを達成できるようサポートします。
製造業ニュース解説
製造業、主に購買・調達部門にお勤めの方々に向けた情報を配信しております。
新任の方やベテランの方、管理職を対象とした幅広いコンテンツをご用意しております。
お問い合わせ
コストダウンが利益に直結する術だと理解していても、なかなか前に進めることができない状況。そんな時は、newjiのコストダウン自動化機能で大きく利益貢献しよう!
(β版非公開)