- お役立ち記事
- Methods to increase production efficiency and vendor selection in designing and manufacturing group insertion equipment
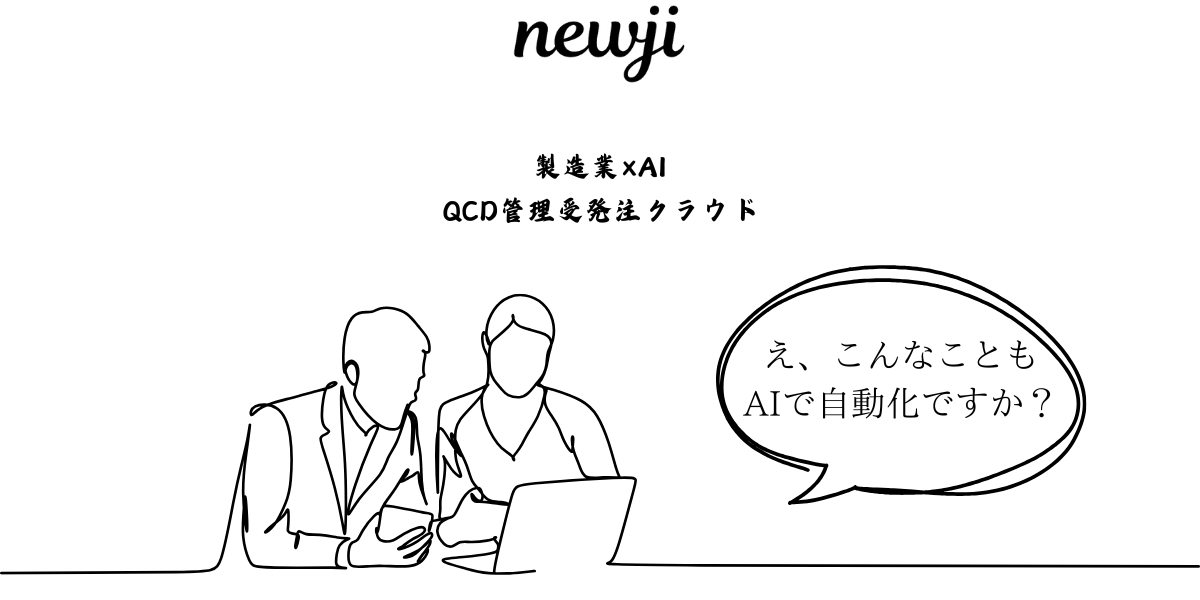
Methods to increase production efficiency and vendor selection in designing and manufacturing group insertion equipment
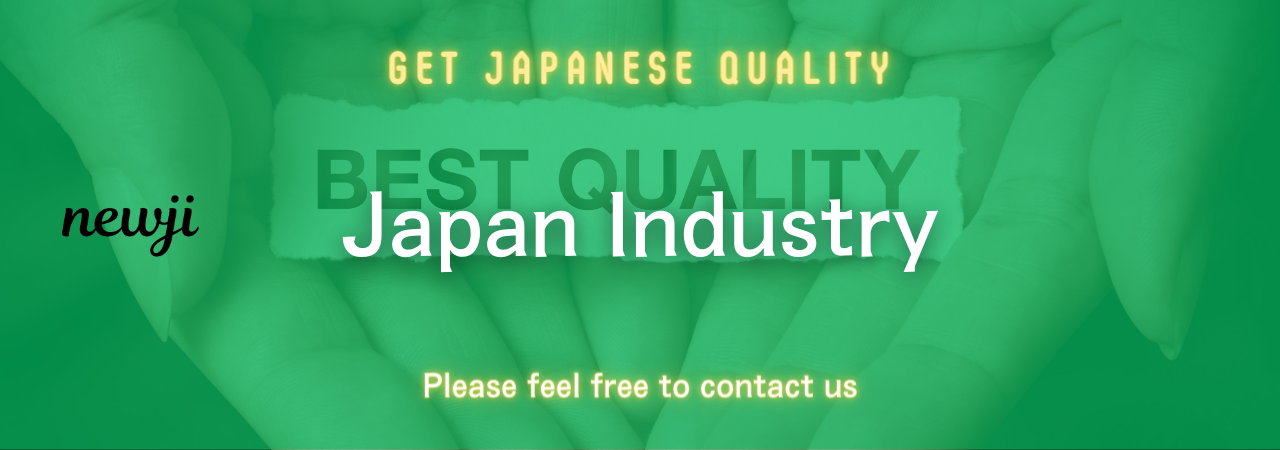
目次
Understanding Group Insertion Equipment
Group insertion equipment plays a crucial role in the manufacturing sector, especially when dealing with printed circuit boards (PCBs) and other complex electronic assemblies.
These sophisticated machines are designed to insert components into a substrate or board, streamlining the assembly process and reducing the need for manual labor.
In industries where precision and speed are paramount, leveraging group insertion equipment can significantly boost production efficiency.
The Importance of Production Efficiency
Production efficiency is a key goal for any manufacturing business.
Higher efficiency means reduced waste, lower costs, and increased output.
This, in turn, can lead to higher profits and improved competitiveness in the market.
In the context of group insertion equipment, maximizing production efficiency involves both optimizing the machines themselves and streamlining the processes in which they are involved.
Strategies to Increase Production Efficiency
Automate Where Possible
Automation is central to enhancing production efficiency.
Group insertion equipment can be programmed to handle repetitive and time-consuming tasks with precision.
By automating these processes, human operators are freed up to focus on more complex tasks that require critical thinking and problem-solving skills.
Automation also reduces the likelihood of errors that can occur during manual assembly.
Regular Maintenance and Upgrades
To keep group insertion equipment operating at peak efficiency, regular maintenance is essential.
This includes routine checks, cleaning, and replacing worn parts.
Upgrades to the machinery’s software and hardware can also enhance performance.
Staying updated with the latest technology ensures that your equipment remains competitive and efficient.
Training and Skill Development
The human element in using group insertion equipment cannot be ignored.
Workers need regular training to ensure they are fully competent in operating these machines.
Training programs can also focus on improving overall workflow, troubleshooting common issues, and understanding the equipment’s capabilities.
This kind of investment in human capital can lead to significant gains in production efficiency.
Monitor and Analyze Data
Modern group insertion equipment often comes with data monitoring capabilities.
These systems collect valuable data on performance metrics such as cycle times, component placements, and error rates.
Analyzing this data allows manufacturers to identify bottlenecks and inefficiencies.
With this information, processes can be modified and optimized to improve throughput.
Vendor Selection for Group Insertion Equipment
Choosing the right vendor for your group insertion equipment is as critical as selecting the equipment itself.
A vendor who understands your specific needs and industry requirements can offer great advantages in terms of both equipment quality and long-term support.
Assessing Vendor Reputation and Experience
The reputation and experience of a vendor in the industry are important factors to consider.
A vendor with a proven track record of high-quality products and reliable support services can be invaluable.
Seek testimonials or reviews from other businesses in your sector to gauge a vendor’s credibility.
Technical Support and Services
Quality technical support is essential for maintaining uptime and production efficiency.
Ensure your vendor offers robust support services, including timely maintenance, spare parts availability, and expert technical assistance when needed.
A vendor’s commitment to customer service can significantly impact your manufacturing operations.
Product Range and Customization
A vendor that offers a wide range of group insertion equipment along with customization options can better meet your specific manufacturing needs.
Customization may include software adaptations, machine configurations, or tool adaptations to accommodate unique production demands.
Having these options can improve the alignment of the equipment with your production processes.
Cost Considerations and ROI
While price is an important consideration, it should not be the only factor.
Consider the total cost of ownership, which includes purchase price, maintenance, energy consumption, and expected lifespan.
Analyzing the potential return on investment (ROI) will help you understand the long-term financial benefits of the equipment.
Integrating Group Insertion Equipment in Your Facility
Once you’ve selected the appropriate group insertion equipment and vendor, the next step is integrating it seamlessly into your manufacturing process.
Layout and Space Planning
Effective layout and space planning are vital for successful integration.
Ensure that the equipment has sufficient space for operation, maintenance, and operator access.
Proper planning can prevent workflow disruptions and contribute to efficient production.
Workflow and Process Optimization
Re-evaluate your existing workflow to identify areas that could benefit from the new equipment.
Optimizing processes will not only improve efficiency but also ensure that the equipment’s capabilities are fully utilized.
Collaborate with your team to streamline these processes and monitor results.
Continuous Improvement and Feedback Loop
Establish a feedback loop to constantly gather information about the equipment’s performance and its impact on production efficiency.
Encourage your team to provide input, identifying issues and suggesting improvements.
A continuous improvement approach will contribute to long-term success.
By considering these strategies and factors, manufacturers can enhance their production efficiency and make informed decisions about vendor selection, ultimately enabling them to stay competitive in today’s fast-paced manufacturing landscape.
資料ダウンロード
QCD調達購買管理クラウド「newji」は、調達購買部門で必要なQCD管理全てを備えた、現場特化型兼クラウド型の今世紀最高の購買管理システムとなります。
ユーザー登録
調達購買業務の効率化だけでなく、システムを導入することで、コスト削減や製品・資材のステータス可視化のほか、属人化していた購買情報の共有化による内部不正防止や統制にも役立ちます。
NEWJI DX
製造業に特化したデジタルトランスフォーメーション(DX)の実現を目指す請負開発型のコンサルティングサービスです。AI、iPaaS、および先端の技術を駆使して、製造プロセスの効率化、業務効率化、チームワーク強化、コスト削減、品質向上を実現します。このサービスは、製造業の課題を深く理解し、それに対する最適なデジタルソリューションを提供することで、企業が持続的な成長とイノベーションを達成できるようサポートします。
オンライン講座
製造業、主に購買・調達部門にお勤めの方々に向けた情報を配信しております。
新任の方やベテランの方、管理職を対象とした幅広いコンテンツをご用意しております。
お問い合わせ
コストダウンが利益に直結する術だと理解していても、なかなか前に進めることができない状況。そんな時は、newjiのコストダウン自動化機能で大きく利益貢献しよう!
(Β版非公開)