- お役立ち記事
- Methods to Maximize Cost Efficiency by Shortening Filling Time
月間76,176名の
製造業ご担当者様が閲覧しています*
*2025年3月31日現在のGoogle Analyticsのデータより
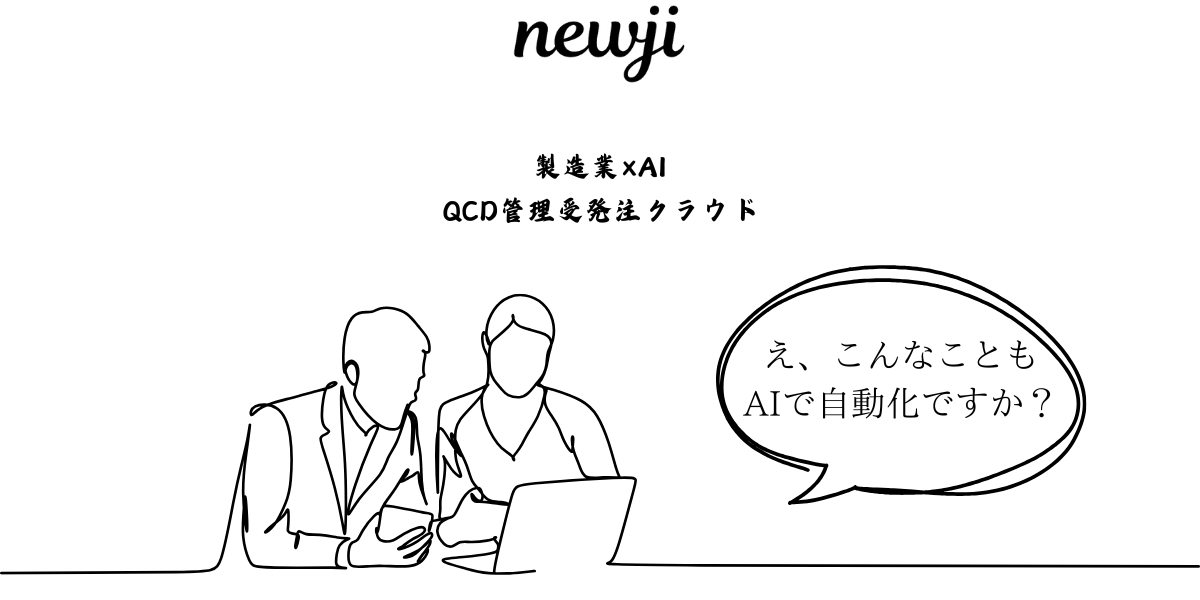
Methods to Maximize Cost Efficiency by Shortening Filling Time
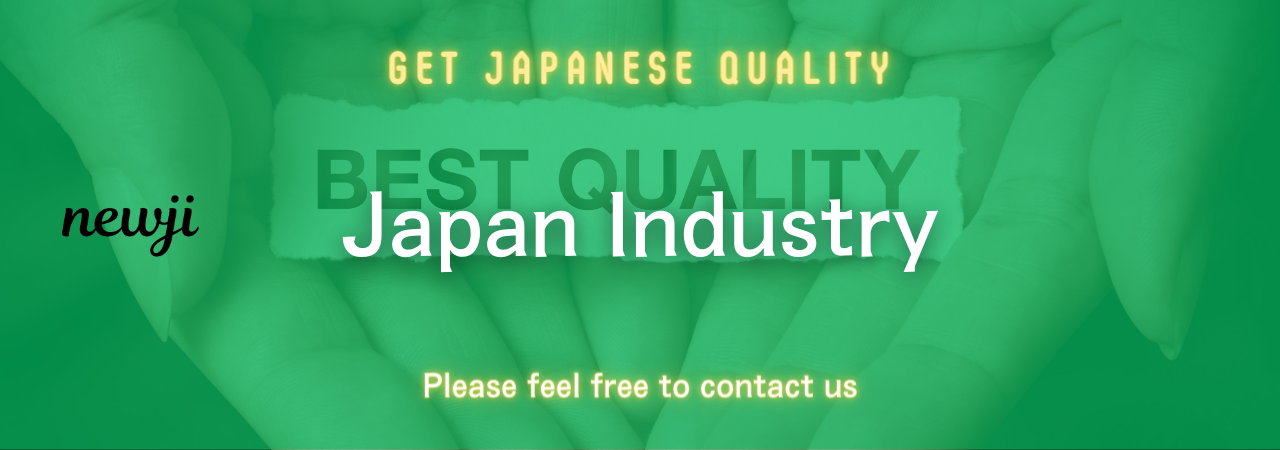
目次
Understanding the Importance of Cost Efficiency
In today’s businesses, maximizing cost efficiency is a primary goal for staying competitive and profitable.
Cost efficiency allows a company to produce goods or provide services using the least amount of resources.
One often-overlooked aspect of cost efficiency is the time factor involved in processes, such as filling.
Time is money, and reducing the time it takes to complete a task can significantly affect a company’s bottom line.
By shortening the filling time involved in production, shipping, or administration, organizations can make great strides in boosting their cost efficiency.
This article will explore various methods to effectively reduce filling times and, ultimately, maximize cost efficiency.
Streamlining Processes
The first step toward reducing filling time is streamlining existing processes.
It is crucial to understand each step involved and identify redundancies or bottlenecks.
Conduct a thorough analysis of the current workflow and involve staff members in the evaluation process, as they often possess valuable insights.
By eliminating unnecessary steps, you can significantly cut down on time wasted.
Implementing process automation tools can be a game-changer.
Technology such as robotic process automation can handle repetitive tasks faster and with fewer errors than humans, resulting in shorter filling times.
Utilizing Technology
Today’s technology offers a myriad of tools that can shorten filling times.
For instance, the use of software for digital document management can speed up administrative filling tasks by making information easily accessible and reducible to electronic forms instead of papers.
Barcode scanners and RFID technology can speed up data entry processes in inventory management by reducing the manual effort involved in product tracking and stocking.
Using data analytics tools to predict peak times and optimize scheduling can ensure that filling processes occur when they are most manageable, minimizing delays.
Upgrading to modern machinery with faster capabilities can accelerate manufacturing processes significantly.
Staff Training and Skill Enhancement
Well-trained employees can perform their tasks more efficiently, reducing the time needed for completion.
Investing in staff training to develop strong skills and a thorough understanding of their roles is paramount.
Regular training programs can introduce new techniques or productivity methods that help staff complete filling tasks faster.
Empowering employees to suggest improvements or take initiative can lead to innovative approaches that reduce filling times.
Encouraging a culture of continuous learning and improvement can keep staff motivated to work efficiently.
Adopting Just-In-Time Practices
Just-In-Time (JIT) practices focus on reducing wait times in processes, which can significantly cut down filling times.
JIT involves making sure that materials and supplies are available when they are needed, reducing idle time waiting for products.
This approach requires precise coordination with suppliers, as well as implementing robust tracking and communication systems.
By embracing JIT, businesses can streamline operations, minimize inventory costs, and enhance overall efficiency.
Implementing Bottleneck Analysis
Identifying and addressing bottlenecks in processes is crucial to maximizing cost efficiency.
Bottlenecks slow down operations and can impact overall productivity.
By using bottleneck analysis, businesses can pinpoint these slow areas and assess why they are causing delays.
Solutions might include reallocating resources, upgrading equipment, or training employees to manage these tasks better.
Once bottlenecks are resolved, filling times can be significantly reduced, helping to achieve better cost efficiency.
Regular Monitoring and Feedback
Ongoing monitoring of processes is essential to ensure that filling time reductions are effective and sustainable.
Regular feedback from employees is invaluable, as they can highlight issues before they become significant problems.
Set up a system to track key performance indicators (KPIs) related to filling times.
Using KPIs to monitor performance allows for quick adjustments to processes that may be becoming inefficient.
This data-driven approach ensures that improvements in filling times are maintained and continuously optimized.
Maintaining Equipment
Regular maintenance of equipment is vital for ensuring smooth operations.
Machinery breakdowns or inefficiencies can cause significant delays, lengthening filling times.
By adhering to a strict maintenance schedule, you can avoid unscheduled downtimes and ensure that equipment is running at peak efficiency.
Investing in high-quality materials and conducting regular inspections can minimize the risk of malfunctions that could hinder production and prolong filling times.
Consider developing a preventive maintenance plan to keep your operations running smoothly with minimal interruptions.
Evaluating Supplier Relationships
Suppliers play a crucial role in a business’s ability to shorten filling times, especially in production and inventory management.
Building strong ties with reliable suppliers ensures timely delivery of materials, reducing potential hold-ups in operations.
Negotiating terms that favor quick turnaround times and having backup suppliers ready can help mitigate risks associated with supplier-related delays.
Establishing a transparent, communicative relationship with suppliers can foster a collaborative atmosphere where both parties work towards efficiency improvements.
Conclusion
Maximizing cost efficiency by shortening filling times is achievable through various strategies, including streamlining processes, employing advanced technologies, and ongoing staff training.
Implementing just-in-time practices, conducting regular bottleneck analysis, and ensuring equipment maintenance can also lead to considerable time savings.
Regular monitoring and evaluation, as well as strong supplier relationships, further support the mission of reducing filling times.
By adopting these methods, businesses can improve productivity, cut costs, and increase their competitiveness in the ever-changing market landscape.
Focusing on efficiency and continuous improvement is the key to success in maximizing cost savings and achieving long-term growth.
資料ダウンロード
QCD管理受発注クラウド「newji」は、受発注部門で必要なQCD管理全てを備えた、現場特化型兼クラウド型の今世紀最高の受発注管理システムとなります。
ユーザー登録
受発注業務の効率化だけでなく、システムを導入することで、コスト削減や製品・資材のステータス可視化のほか、属人化していた受発注情報の共有化による内部不正防止や統制にも役立ちます。
NEWJI DX
製造業に特化したデジタルトランスフォーメーション(DX)の実現を目指す請負開発型のコンサルティングサービスです。AI、iPaaS、および先端の技術を駆使して、製造プロセスの効率化、業務効率化、チームワーク強化、コスト削減、品質向上を実現します。このサービスは、製造業の課題を深く理解し、それに対する最適なデジタルソリューションを提供することで、企業が持続的な成長とイノベーションを達成できるようサポートします。
製造業ニュース解説
製造業、主に購買・調達部門にお勤めの方々に向けた情報を配信しております。
新任の方やベテランの方、管理職を対象とした幅広いコンテンツをご用意しております。
お問い合わせ
コストダウンが利益に直結する術だと理解していても、なかなか前に進めることができない状況。そんな時は、newjiのコストダウン自動化機能で大きく利益貢献しよう!
(β版非公開)