- お役立ち記事
- Mid-level employees in the production management department should learn how to improve production efficiency using MRP (Material Requirements Planning)
月間76,176名の
製造業ご担当者様が閲覧しています*
*2025年3月31日現在のGoogle Analyticsのデータより
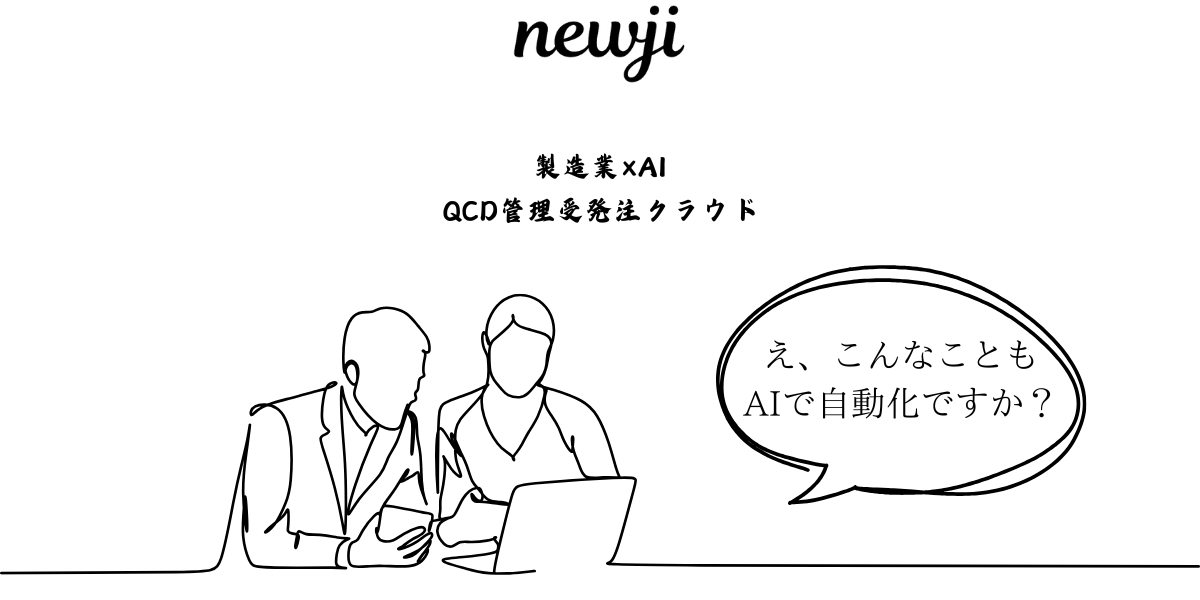
Mid-level employees in the production management department should learn how to improve production efficiency using MRP (Material Requirements Planning)
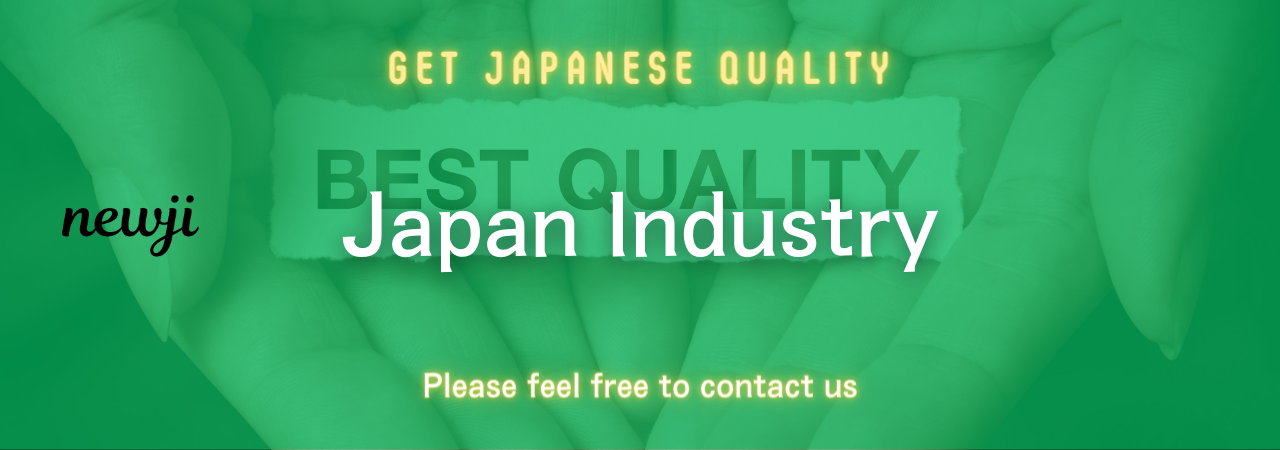
目次
Understanding MRP: The Basics
Material Requirements Planning, or MRP, is a powerful tool used in production management to enhance efficiency in manufacturing processes.
At its core, MRP helps businesses determine what materials are needed, the quantities required, and when they should be ordered to meet production goals.
MRP systems are designed to streamline inventory management and ensure that resources are available just in time for production, minimizing waste and optimizing costs.
For mid-level employees in the production management department, understanding MRP is crucial to improving production efficiency.
By utilizing MRP, managers can better align production schedules with demand forecasts.
This leads to a more organized workflow, reduces the chances of material shortages, and enhances the overall profitability of the production process.
The Importance of MRP in Production Management
MRP is not just a tool for inventory management; it’s an integral part of the production management strategy.
When effectively implemented, it provides several key benefits that can significantly enhance production efficiency.
Firstly, MRP helps in accurate demand forecasting.
By analyzing historical data and market trends, it assists managers in predicting future demand more precisely.
This means that the production department is better equipped to respond to changes in market demand without overproducing or underproducing, which can lead to either high inventory costs or lost sales, respectively.
Secondly, MRP optimizes the production schedule.
With an MRP system, production managers can create a detailed schedule that outlines when each material is needed.
This leads to a leaner production process, reducing idle times and ensuring a continuous flow of production activities.
Reducing Waste and Enhancing Cost Efficiency
One of the primary goals of implementing MRP in production management is to reduce waste.
When materials are closely tracked and timed to the production process, the likelihood of overstocking or understocking is minimized.
This leads to a reduction in storage costs and decreases the chances of materials becoming obsolete or damaged while sitting in inventory.
Moreover, MRP enables companies to negotiate better prices with suppliers by ordering materials in optimal quantities.
This can enhance cost efficiency further and improve the overall bottom line of the company.
Challenges and Best Practices for Mid-Level Employees
While MRP systems offer substantial benefits, implementing them can come with challenges.
For mid-level employees, understanding these challenges and the best practices to overcome them is essential for successful adoption.
One of the common challenges is the integration of MRP systems with existing IT infrastructure.
Ensuring that the MRP system is compatible with other software, such as accounting and customer relationship management systems, is crucial for a seamless flow of information.
Additionally, data accuracy is vital.
Since MRP systems rely heavily on data, any inaccuracies in demand forecasts, inventory levels, or production schedules can lead to inefficiencies.
Therefore, regular audits and data verification processes are recommended to maintain accuracy.
Developing an MRP Implementation Plan
To leverage MRP effectively, mid-level employees should focus on the development of a comprehensive implementation plan.
This involves setting clear objectives, identifying key performance indicators, and establishing timelines for the adoption of the MRP system.
Training is another critical aspect of the implementation process.
Employees responsible for managing the MRP system should be provided with adequate training to ensure they are proficient in its use.
This includes understanding how to input data, generate reports, and make informed decisions based on the insights provided by the system.
Continuous Improvement and MRP Optimization
Once an MRP system is in place, the journey doesn’t end there.
For mid-level employees, it’s important to continually assess and optimize MRP processes to adapt to changing production needs and market conditions.
Regularly reviewing MRP reports can help identify areas for improvement within the production workflow.
For example, if certain materials consistently run out before new stock arrives, it might indicate a need for adjusted lead times or stronger supplier relationships.
Additionally, incorporating feedback from the production team can provide valuable insights into the practical aspects of the MRP system.
By maintaining an open line of communication with other departments, production managers can ensure that the MRP system aligns with real-world production challenges and opportunities.
The Role of Technology in MRP Advancement
Technology continues to play a significant role in the evolution of MRP systems.
With advancements in artificial intelligence and machine learning, modern MRP systems are becoming more capable of predicting demand with greater accuracy and automating routine tasks.
For example, AI-powered MRP systems can analyze large datasets to identify patterns and trends that may not be immediately apparent to human analysts.
This can lead to smarter decision-making and enhance the strategic planning capabilities of the production management team.
Conclusion: Embracing MRP for Enhanced Efficiency
For mid-level employees in the production management department, embracing MRP is a strategic move toward improved production efficiency.
By understanding the fundamentals of MRP, recognizing its benefits, and implementing best practices, production managers can lead their companies towards leaner, more cost-effective operations.
Ultimately, the successful implementation of an MRP system can lead to a more responsive manufacturing environment, better alignment with market demands, and a stronger competitive edge in the industry.
By continuously analyzing and refining MRP processes, mid-level employees can contribute significantly to their organization’s growth and success.
資料ダウンロード
QCD管理受発注クラウド「newji」は、受発注部門で必要なQCD管理全てを備えた、現場特化型兼クラウド型の今世紀最高の受発注管理システムとなります。
ユーザー登録
受発注業務の効率化だけでなく、システムを導入することで、コスト削減や製品・資材のステータス可視化のほか、属人化していた受発注情報の共有化による内部不正防止や統制にも役立ちます。
NEWJI DX
製造業に特化したデジタルトランスフォーメーション(DX)の実現を目指す請負開発型のコンサルティングサービスです。AI、iPaaS、および先端の技術を駆使して、製造プロセスの効率化、業務効率化、チームワーク強化、コスト削減、品質向上を実現します。このサービスは、製造業の課題を深く理解し、それに対する最適なデジタルソリューションを提供することで、企業が持続的な成長とイノベーションを達成できるようサポートします。
製造業ニュース解説
製造業、主に購買・調達部門にお勤めの方々に向けた情報を配信しております。
新任の方やベテランの方、管理職を対象とした幅広いコンテンツをご用意しております。
お問い合わせ
コストダウンが利益に直結する術だと理解していても、なかなか前に進めることができない状況。そんな時は、newjiのコストダウン自動化機能で大きく利益貢献しよう!
(β版非公開)