- お役立ち記事
- Modeling of controlled objects and application to adaptive model predictive control
月間77,185名の
製造業ご担当者様が閲覧しています*
*2025年2月28日現在のGoogle Analyticsのデータより
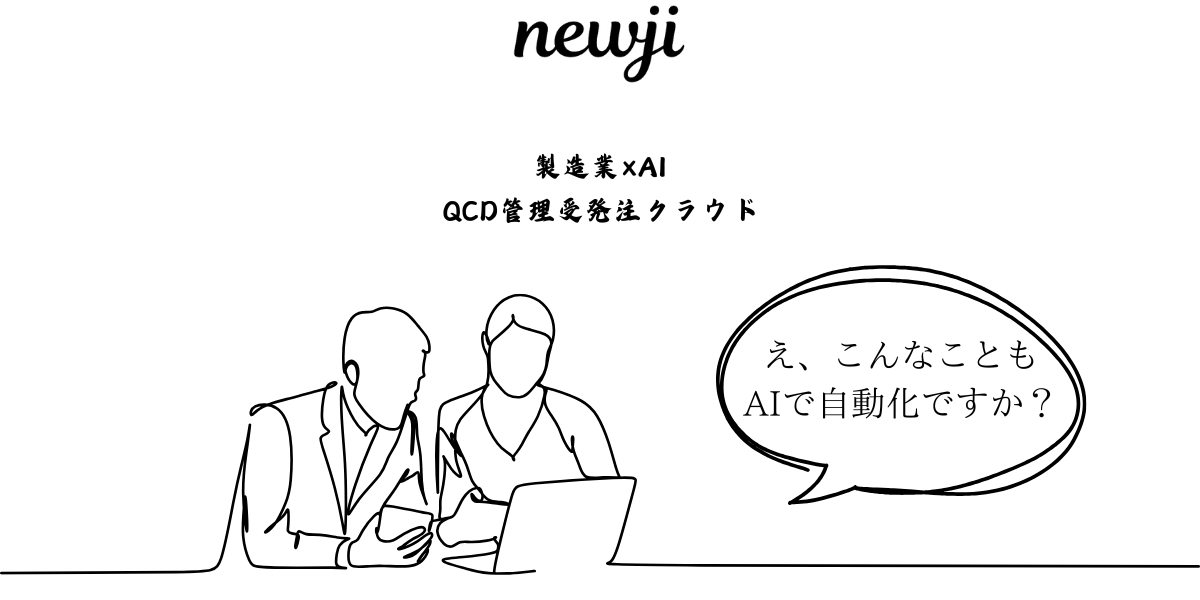
Modeling of controlled objects and application to adaptive model predictive control
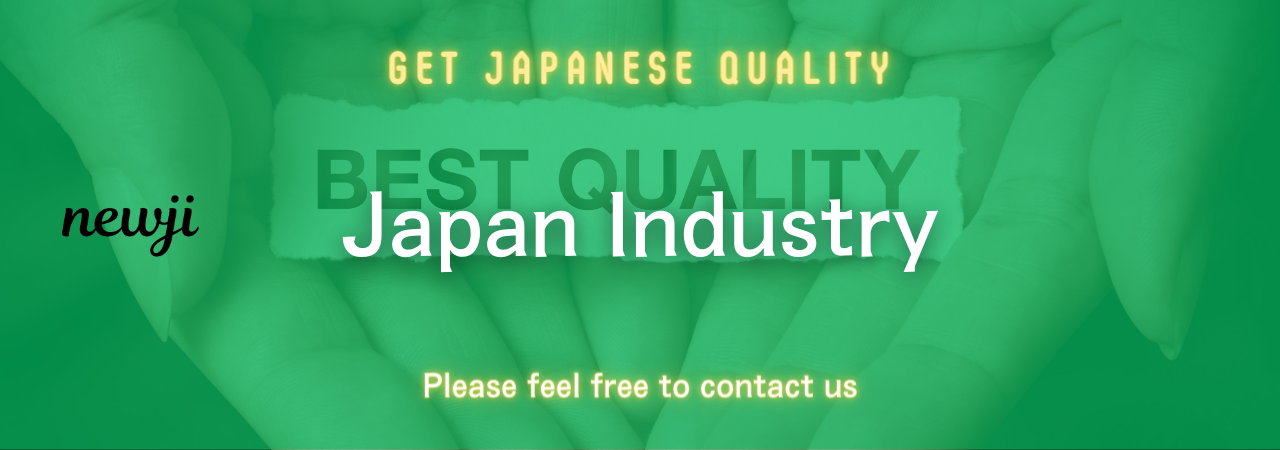
目次
Understanding Controlled Objects
In the world of control systems, a controlled object is an entity, system, or process that requires regulation and management to achieve a desired performance.
Imagine a car’s speed being maintained on a highway or the temperature being kept steady in a building.
These are examples of controlled objects, where the primary aim is to regulate certain variables to achieve specific goals.
Typically, controlled objects can vary from simple systems, like a household thermostat, to complex machinery in industrial manufacturing.
The modeling of controlled objects is an essential aspect of engineering and control systems design.
Without an accurate model, it is challenging to predict how the system behaves or how it should be controlled.
The Importance of Accurate Modeling
Modeling involves creating a mathematical representation of the controlled object.
This representation captures the dynamics and characteristics of what is to be controlled, which is crucial for effective control.
An accurate model allows engineers to simulate and analyze the system’s behavior under various conditions, leading to more informed decision-making.
An inaccurate model can lead to inefficient control, increased costs, or even catastrophic failures.
Imagine a robot arm in a factory moving unpredictably due to an imprecise model.
The risks and damages could be extensive.
Thus, developing a reliable model is a primary step in any control system project.
Types of Models
In the context of control systems, models can be categorized based on several factors, such as linearity, time dependence, and determinism.
1. **Linear vs. Nonlinear Models**:
Linear models assume that the response of the system is directly proportional to the input.
Nonlinear models, on the other hand, anticipate more complex relationships between inputs and outputs.
Most real-world systems are nonlinear, making nonlinear models more accurate yet more complex.
2. **Time-Invariant vs. Time-Varying Models**:
Time-invariant models assume that the system parameters do not change over time.
In contrast, time-varying models account for changes that might occur as the system operates over time.
3. **Deterministic vs. Stochastic Models**:
Deterministic models predict the system’s behavior with certainty given a certain input.
Stochastic models incorporate randomness, acknowledging that different factors might lead to variations in system performance.
Adaptive Model Predictive Control
Adaptive Model Predictive Control (AMPC) is an advanced control technique that leverages the robustness of Model Predictive Control (MPC) while incorporating adaptability to changing conditions.
MPC is well-known for its capability to handle multi-variable control problems, constraints, and predictive elements effectively.
AMPC distinguishes itself by its adaptive framework, which means it continuously updates the model of the controlled object in real-time as more data becomes available.
This adaptability is crucial for systems that operate in dynamic and unpredictable environments, where traditional control methodologies may falter.
How AMPC Works
1. **Real-Time Data Collection**:
The system constantly gathers data from various sensors and inputs.
This data reflects the current state and any changes in the controlled object’s environment or behavior.
2. **Model Adjustment**:
As new data comes in, AMPC updates the mathematical model of the controlled object.
This process involves recalibrating parameters to reflect the latest conditions accurately.
3. **Prediction and Optimization**:
Using the updated model, AMPC predicts future behavior over a specified horizon and optimizes control actions to meet desired objectives.
This involves optimizing a cost function subject to constraints, ensuring the best possible output while respecting any limitations.
4. **Implementation**:
The optimized control actions are then executed, steering the system towards desired outcomes.
Advantages of AMPC
AMPC offers numerous advantages, making it a popular choice in various industries.
1. **Flexibility and Scalability**:
Since AMPC adapts to changing conditions, it is highly flexible and can be applied across different industries, from automotive to aerospace.
2. **Improved Performance**:
By continuously adapting, AMPC can maintain high performance and efficiency, even when the system or its environment undergo unforeseen changes.
3. **Reduction in Manual Intervention**:
The adaptive nature of AMPC means less need for manual adjustments or interventions, saving time and reducing human error potential.
4. **Enhanced Robustness**:
AMPC can handle noise and disturbances more effectively, ensuring reliable operation under variable conditions.
Applications in Real World
AMPC is widely used in areas where conditions change rapidly and unpredictably.
1. **Industrial Automation**:
In manufacturing, AMPC helps in efficiently managing resources, optimizing processes, and enhancing product quality with minimal waste.
2. **Process Control**:
Plants dealing with chemicals or refineries leverage AMPC to maintain stringent process conditions, ensuring safety and compliance.
3. **Energy Management**:
In power grids and renewable energy, AMPC helps balance supply and demand, integrating renewable sources smoothly.
4. **Autonomous Vehicles**:
The automotive industry uses AMPC for advanced driver-assistance systems, where real-time adaptability is vital for safety and performance.
Conclusion
Modeling controlled objects and applying Adaptive Model Predictive Control is a powerful strategy for optimizing system performance across various fields.
As industries progress, the need for sophisticated control systems that can adapt to changing environments is becoming increasingly important.
With the continuous advancements in computation and data analysis, AMPC will play an even more significant role, leading the way in modern, efficient, and reliable control solutions.
資料ダウンロード
QCD管理受発注クラウド「newji」は、受発注部門で必要なQCD管理全てを備えた、現場特化型兼クラウド型の今世紀最高の受発注管理システムとなります。
ユーザー登録
受発注業務の効率化だけでなく、システムを導入することで、コスト削減や製品・資材のステータス可視化のほか、属人化していた受発注情報の共有化による内部不正防止や統制にも役立ちます。
NEWJI DX
製造業に特化したデジタルトランスフォーメーション(DX)の実現を目指す請負開発型のコンサルティングサービスです。AI、iPaaS、および先端の技術を駆使して、製造プロセスの効率化、業務効率化、チームワーク強化、コスト削減、品質向上を実現します。このサービスは、製造業の課題を深く理解し、それに対する最適なデジタルソリューションを提供することで、企業が持続的な成長とイノベーションを達成できるようサポートします。
製造業ニュース解説
製造業、主に購買・調達部門にお勤めの方々に向けた情報を配信しております。
新任の方やベテランの方、管理職を対象とした幅広いコンテンツをご用意しております。
お問い合わせ
コストダウンが利益に直結する術だと理解していても、なかなか前に進めることができない状況。そんな時は、newjiのコストダウン自動化機能で大きく利益貢献しよう!
(β版非公開)