- お役立ち記事
- Mold Design for High-Speed Injection Molding and Successful Case Studies
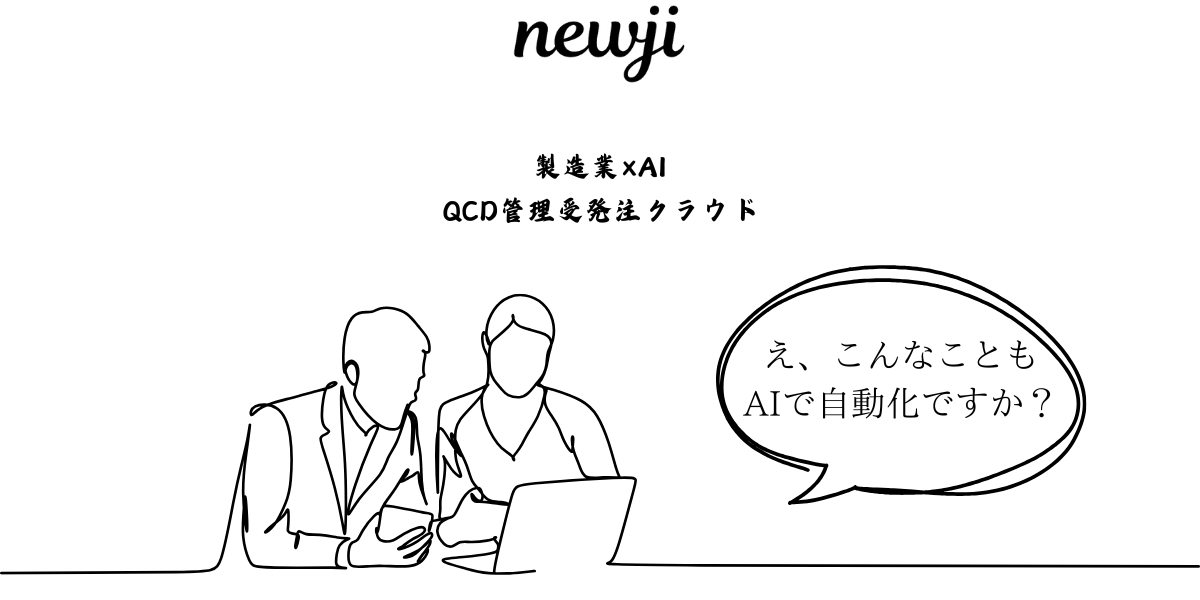
Mold Design for High-Speed Injection Molding and Successful Case Studies
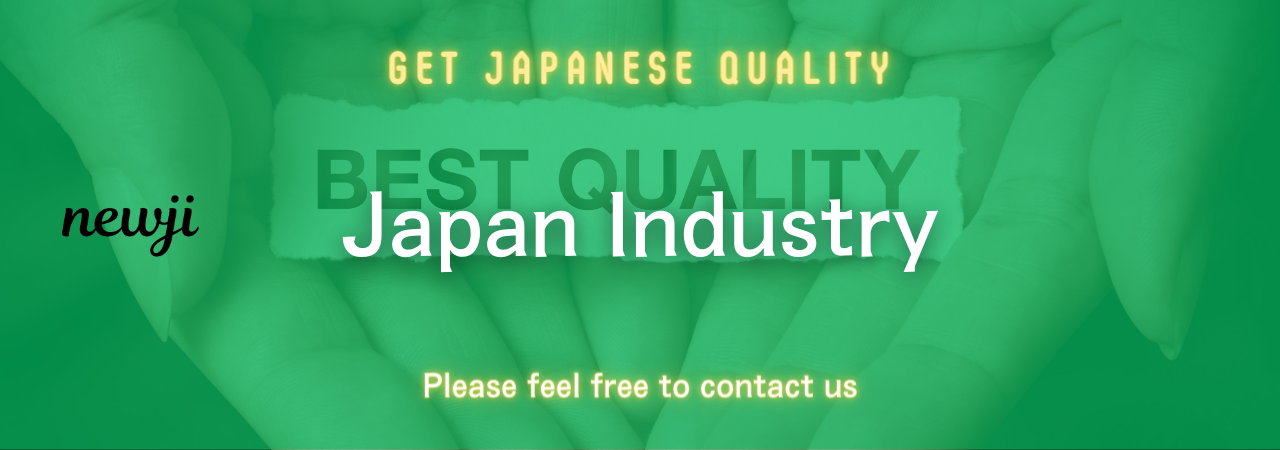
目次
Understanding Mold Design for High-Speed Injection Molding
Mold design plays a crucial role in high-speed injection molding, a method widely used in the production of plastic components.
This process demands high precision and efficiency, making it essential to design molds that can withstand such rigorous conditions.
The mold must facilitate quick and smooth injection, rapid cooling, and rapid ejection to keep up with the speed of production.
A well-designed mold is a combination of art and engineering.
It begins with a detailed understanding of the product requirements, including size, shape, weight, and material properties.
Key Elements in Mold Design
A successful mold design involves several critical elements:
1. **Cavities and Cores**: These are essential components that shape the final part.
The cavity is the hollow part into which the plastic is injected, while the core forms the interior of the product.
For high-speed injection molding, these elements must be designed to allow precise and consistent filling.
2. **Cooling Systems**: Efficient cooling is vital in high-speed injection molding.
The design must include a network of cooling channels to remove heat rapidly and evenly, reducing cycle times and improving productivity.
3. **Ejection Systems**: These systems enable the removal of the part from the mold.
In high-speed scenarios, the ejection mechanism must ensure fast yet careful removal to prevent damage.
4. **Ventilation**: Proper ventilation helps prevent defects by allowing air to escape as the plastic fills the mold.
Poor ventilation can lead to surface imperfections and incomplete parts.
5. **Material Selection**: The choice of material for both the mold and the product can significantly affect performance.
Molds need to be strong and heat-resistant to handle the rapid cycles without deforming.
Advanced Techniques in Mold Design
To keep up with the demanding nature of high-speed injection molding, advanced mold design techniques have been developed.
Some of these include:
Computer-Aided Design (CAD)
CAD software is instrumental in today’s mold design processes.
It allows designers to create detailed and precise digital models, simulate the molding process, and identify potential issues before manufacturing begins.
This leads to increased accuracy and reduced development times.
3D Printing
3D printing has introduced revolutionary changes in prototyping stage.
Designers can create rapid prototypes of mold components to test designs swiftly and economically.
This helps in identifying and rectifying any design flaws early in the process.
Simulation Software
Simulation software enables designers to run virtual tests on mold designs.
By understanding how a mold will behave during the injection process, designers can make adjustments to optimize solidification and minimize defects.
Successful Case Studies in High-Speed Injection Molding
Exploring real-world applications and success stories can provide valuable insights into mold design for high-speed injection molding.
Case Study 1: Automotive Parts Manufacturing
A leading automotive parts manufacturer reduced production time by redesigning their molds for high-speed injection.
By incorporating advanced cooling systems and optimizing cavity design, they achieved faster cycle times and improved part quality.
This not only increased throughput but also reduced material waste and operational costs.
Case Study 2: Consumer Electronics
In the consumer electronics sector, a company utilized CAD and simulation technologies to enhance their mold design for smartphone components.
The integration of these tools allowed them to achieve precision in micro-features, vital for the compact and intricate designs of modern devices.
The improved mold design resulted in higher production efficiency and better product performance.
Case Study 3: Medical Device Manufacturing
For a medical device manufacturer, accuracy and consistency were paramount.
By utilizing 3D printing for prototype testing, they were able to perfect their molds before full-scale production began.
This approach minimized the risk of defects in sensitive medical components, ensured regulatory compliance, and accelerated time-to-market.
Conclusion
Mold design in high-speed injection molding is a multifaceted and evolving field.
Understanding the fundamental elements, leveraging advanced techniques, and learning from successful case studies contribute significantly to a manufacturer’s ability to produce high-quality, cost-effective products swiftly.
By focusing on precision, efficiency, and innovation, companies can remain competitive in a demanding market.
資料ダウンロード
QCD調達購買管理クラウド「newji」は、調達購買部門で必要なQCD管理全てを備えた、現場特化型兼クラウド型の今世紀最高の購買管理システムとなります。
ユーザー登録
調達購買業務の効率化だけでなく、システムを導入することで、コスト削減や製品・資材のステータス可視化のほか、属人化していた購買情報の共有化による内部不正防止や統制にも役立ちます。
NEWJI DX
製造業に特化したデジタルトランスフォーメーション(DX)の実現を目指す請負開発型のコンサルティングサービスです。AI、iPaaS、および先端の技術を駆使して、製造プロセスの効率化、業務効率化、チームワーク強化、コスト削減、品質向上を実現します。このサービスは、製造業の課題を深く理解し、それに対する最適なデジタルソリューションを提供することで、企業が持続的な成長とイノベーションを達成できるようサポートします。
オンライン講座
製造業、主に購買・調達部門にお勤めの方々に向けた情報を配信しております。
新任の方やベテランの方、管理職を対象とした幅広いコンテンツをご用意しております。
お問い合わせ
コストダウンが利益に直結する術だと理解していても、なかなか前に進めることができない状況。そんな時は、newjiのコストダウン自動化機能で大きく利益貢献しよう!
(Β版非公開)