- お役立ち記事
- Molded product design
Molded product design
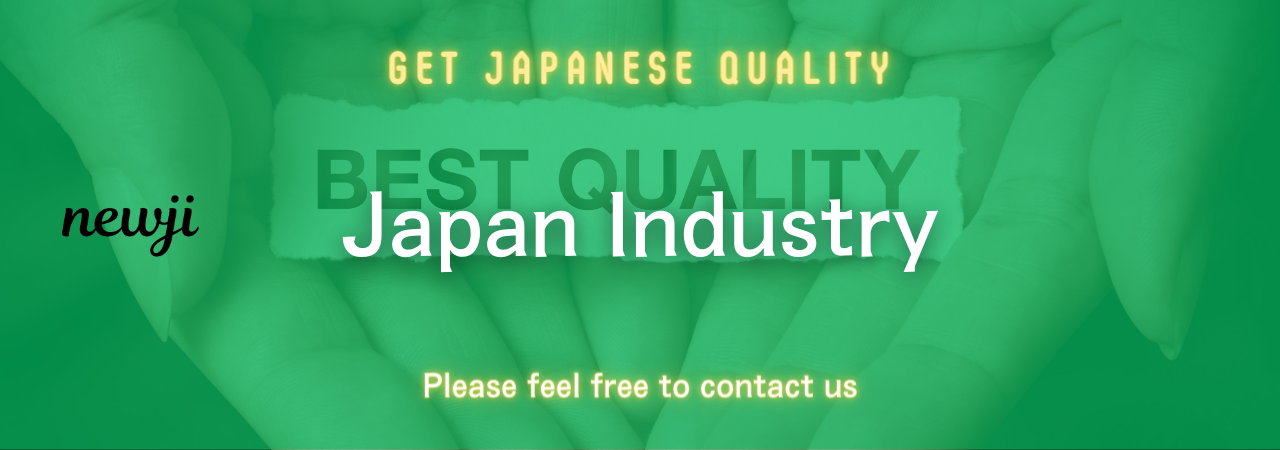
Understanding Molded Product Design
Molded product design is an essential aspect of manufacturing, affecting everything from the quality of the final product to the efficiency of the production process.
When we talk about molded products, we are usually referring to items that are made using a mold in shaping processes, typically with materials like plastic, rubber, or metal.
The design of these products requires careful planning and consideration to ensure that they meet specific criteria related to function, aesthetics, and production feasibility.
The Basics of Molded Product Design
At its core, molded product design is about creating items with a predetermined shape using a mold.
This process allows manufacturers to produce consistent and precise components at scale.
The process begins with a concept or idea, which moves into design specifications.
These specifications outline the desired shape, size, and features of the product.
Designers must consider the properties of the material to be used, as each material behaves differently under pressure and temperature changes during molding.
Materials Used in Molded Products
Selecting the right material is crucial in molded product design.
Common materials include plastics, metals, and rubbers, each chosen based on the product’s intended use and required strength.
Plastics are popular in molded product design due to their versatility and cost-effectiveness.
They are used in various applications, from automotive parts to consumer electronics.
Metals are chosen for their durability and strength, suitable for heavy-duty components.
Rubbers offer flexibility and can absorb shocks, making them ideal for seals and gaskets.
Design Considerations
When designing molded products, several key considerations come into play.
One of the primary considerations is the product’s dimensions.
Designers must be precise, ensuring that every measurement is accurate to ensure the mold’s effectiveness.
Additionally, designers need to think about the production process.
They must account for how the material will flow into the mold and any potential issues, such as air bubbles or incomplete filling.
The Role of Technology in Design
Advancements in technology have significantly impacted molded product design.
Computer-Aided Design (CAD) software allows designers to create detailed 3D models of products, test them in virtual environments, and make necessary adjustments before any physical production occurs.
Moreover, simulation tools can predict how materials will behave in the mold, helping to identify possible issues before they happen.
Prototyping and Testing
Before entering full production, prototypes are often made to test a design.
Prototyping allows designers and manufacturers to identify and resolve any issues with the product design or functionality.
Testing is crucial to ensure that the product can withstand the conditions it will face during its lifecycle.
This phase includes stress tests, drop tests, and other evaluations to guarantee quality and safety.
Manufacturing Techniques
Several techniques are employed in the manufacturing of molded products, each with specific benefits and applications.
Injection molding is one of the most common techniques, used especially for plastic products.
It involves injecting molten plastic into a mold where it cools and solidifies.
Compression molding is typically used for rubber and some plastics, where material is placed into a heated mold and pressure is applied.
Casting is another technique, often used with metals, where the material is poured into a mold and allowed to cool and harden.
The Importance of Quality Control
Quality control is a vital part of the molded product design process.
It ensures that all products meet the predefined standards and specifications.
During production, samples are regularly inspected for defects or inconsistencies using various techniques like visual inspections or automated scanning.
Ensuring quality control not only maintains product integrity but also builds customer trust and satisfaction.
Environmental Considerations
Modern molded product design also places an emphasis on environmental impact.
Companies are increasingly looking for sustainable materials and processes to minimize ecological footprints.
Biodegradable plastics and recyclable materials are becoming popular choices.
Additionally, optimizing the design to use less material can help reduce waste.
Future Trends in Molded Product Design
Looking ahead, molded product design is expected to continue evolving, driven by technological advances and changing consumer demands.
Additive manufacturing, or 3D printing, is becoming a valuable tool for prototyping and even production in some cases.
This technology allows for complex designs with less waste, offering tremendous potential for innovation.
Digital twins—a virtual model of a product or process—are also gaining traction, enabling designers to simulate and optimize designs efficiently.
In conclusion, molded product design is a complex but fascinating field that combines creativity with technical precision.
As technology advances, we can expect even more innovative and sustainable practices to emerge, ensuring that this essential aspect of manufacturing continues to thrive.
資料ダウンロード
QCD調達購買管理クラウド「newji」は、調達購買部門で必要なQCD管理全てを備えた、現場特化型兼クラウド型の今世紀最高の購買管理システムとなります。
ユーザー登録
調達購買業務の効率化だけでなく、システムを導入することで、コスト削減や製品・資材のステータス可視化のほか、属人化していた購買情報の共有化による内部不正防止や統制にも役立ちます。
NEWJI DX
製造業に特化したデジタルトランスフォーメーション(DX)の実現を目指す請負開発型のコンサルティングサービスです。AI、iPaaS、および先端の技術を駆使して、製造プロセスの効率化、業務効率化、チームワーク強化、コスト削減、品質向上を実現します。このサービスは、製造業の課題を深く理解し、それに対する最適なデジタルソリューションを提供することで、企業が持続的な成長とイノベーションを達成できるようサポートします。
オンライン講座
製造業、主に購買・調達部門にお勤めの方々に向けた情報を配信しております。
新任の方やベテランの方、管理職を対象とした幅広いコンテンツをご用意しております。
お問い合わせ
コストダウンが利益に直結する術だと理解していても、なかなか前に進めることができない状況。そんな時は、newjiのコストダウン自動化機能で大きく利益貢献しよう!
(Β版非公開)