- お役立ち記事
- Molded product design
月間76,176名の
製造業ご担当者様が閲覧しています*
*2025年3月31日現在のGoogle Analyticsのデータより
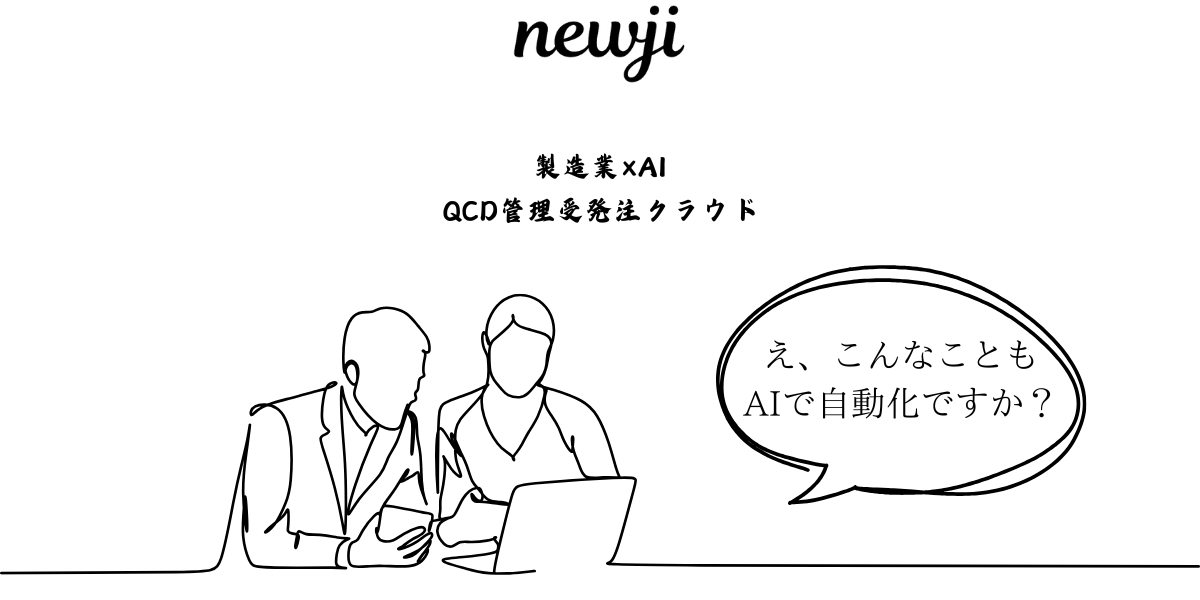
Molded product design
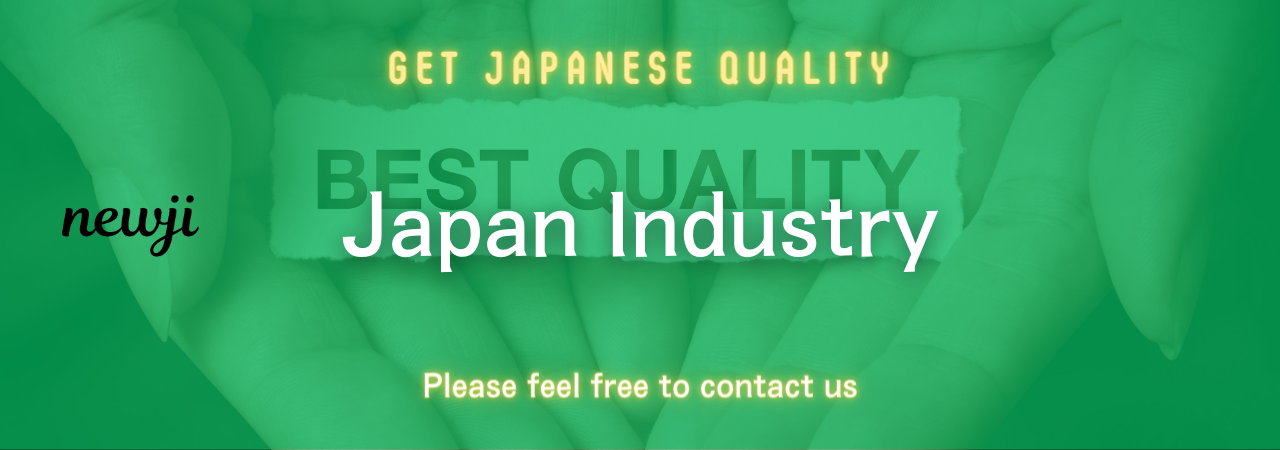
目次
Understanding Molded Product Design
Molded product design is an essential aspect of manufacturing that plays a crucial role in creating everything from simple household items to complex automotive parts.
It involves shaping materials into specific forms using molds, a process that necessitates precision, expertise, and creativity.
In this article, we will delve into the basics of molded product design, its various methods, and the importance of effective design in the manufacturing industry.
The Basics of Molded Product Design
Molded product design starts with the concept of shaping a raw material, often plastic, metal, or ceramics, into a desired form using a mold.
A mold is a hollow container that forms the material into a final shape when it cools and solidifies.
This process is essential in mass production, allowing manufacturers to produce multiple items efficiently and consistently.
The design of the mold itself is crucial.
It must be crafted with precision to ensure that every part created from it is accurate and meets quality standards.
Mold designers use computer-aided design (CAD) software to create detailed models of both the product and the mold.
This technology allows them to visualize the final product and make necessary adjustments before physical production begins.
Different Methods of Molded Product Design
Molded product design employs various methods depending on the material and the complexity of the product.
Injection Molding
Injection molding is one of the most common methods used in molded product design, particularly for plastic parts.
In this process, the plastic is melted and injected into a mold where it cools and solidifies.
This method is highly efficient, making it ideal for producing high volumes of products quickly.
It is widely used for creating products like bottle caps, toys, and automotive components.
Blow Molding
Blow molding is used primarily for creating hollow objects such as bottles and containers.
In this method, plastic is first heated until it is pliable and then placed in a mold.
Air is blown into the material, expanding it against the mold walls and forming the final product.
Blow molding offers flexibility and is cost-effective for manufacturing large quantities of hollow items.
Compression Molding
Compression molding involves placing a pre-measured amount of plastic or other material into a heated mold.
Once the mold is closed, pressure is applied to force the material to conform to the shape of the cavity.
This method is well-suited for producing large, durable parts like automotive components and electrical switches.
Rotational Molding
Rotational molding, or rotomolding, is used for creating large, hollow products such as tanks, kayaks, and playground equipment.
The process involves loading powdered material into a mold which is then rotated continuously on multiple axes while being heated.
As the material melts, it coats the interior of the mold evenly.
Rotational molding allows for intricate designs and varied wall thicknesses.
The Importance of Effective Mold Design
Effective mold design is critical for several reasons.
Firstly, it ensures that the final product meets the desired specifications and quality standards.
A well-designed mold reduces the need for costly and time-consuming post-production adjustments.
Secondly, efficient mold design can significantly lower production costs.
By optimizing the design, manufacturers can minimize waste and reduce the cycle time for each product, leading to increased productivity.
Moreover, a well-conceived mold design enhances product functionality and aesthetic appeal.
Designers can incorporate specific features into the mold, such as textures and logos, that enhance the product’s usability and brand identity.
Challenges in Molded Product Design
While molded product design offers many advantages, it is not without its challenges.
One of the primary challenges is ensuring the precision of the mold, as even small errors in design can lead to large-scale defects in production.
This requires designers to have a strong understanding of material properties and manufacturing processes.
Another challenge is the initial cost of mold production.
Creating a mold involves significant upfront investment, so it’s crucial to ensure the mold will remain useful and adaptable for future production needs.
Additionally, the use of advanced technologies in molded product design, such as CAD software, demands a high level of skill and expertise.
Designers must stay updated with the latest technological advancements to remain competitive in the industry.
The Future of Molded Product Design
As technology continues to advance, molded product design is poised for exciting developments.
The integration of 3D printing technology, for instance, allows for rapid prototyping and more innovative designs.
This technology has the potential to streamline the mold creation process and enhance customization options.
Moreover, sustainability is becoming a major focus in molded product design.
Designers are increasingly exploring ways to minimize material waste and utilize eco-friendly materials in their molds and products.
In conclusion, molded product design is a dynamic field that is integral to the manufacturing sector.
With advances in technology and an increasing emphasis on sustainability, this field will continue to evolve, shaping the future of manufacturing and product design in the years to come.
資料ダウンロード
QCD管理受発注クラウド「newji」は、受発注部門で必要なQCD管理全てを備えた、現場特化型兼クラウド型の今世紀最高の受発注管理システムとなります。
ユーザー登録
受発注業務の効率化だけでなく、システムを導入することで、コスト削減や製品・資材のステータス可視化のほか、属人化していた受発注情報の共有化による内部不正防止や統制にも役立ちます。
NEWJI DX
製造業に特化したデジタルトランスフォーメーション(DX)の実現を目指す請負開発型のコンサルティングサービスです。AI、iPaaS、および先端の技術を駆使して、製造プロセスの効率化、業務効率化、チームワーク強化、コスト削減、品質向上を実現します。このサービスは、製造業の課題を深く理解し、それに対する最適なデジタルソリューションを提供することで、企業が持続的な成長とイノベーションを達成できるようサポートします。
製造業ニュース解説
製造業、主に購買・調達部門にお勤めの方々に向けた情報を配信しております。
新任の方やベテランの方、管理職を対象とした幅広いコンテンツをご用意しております。
お問い合わせ
コストダウンが利益に直結する術だと理解していても、なかなか前に進めることができない状況。そんな時は、newjiのコストダウン自動化機能で大きく利益貢献しよう!
(β版非公開)