- お役立ち記事
- Multi-supplier strategy to diversify risk by optimizing safety stock
Multi-supplier strategy to diversify risk by optimizing safety stock
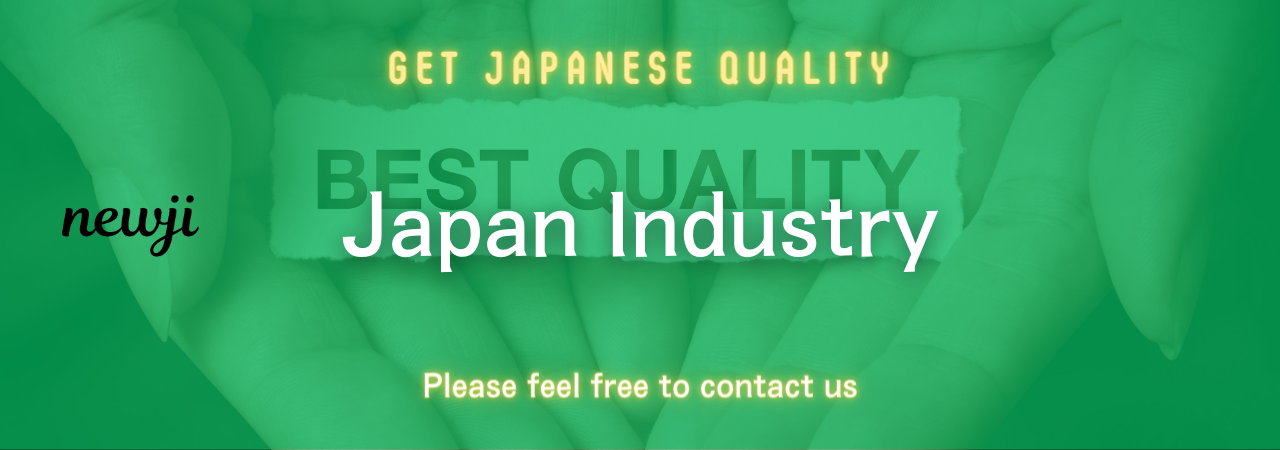
目次
Understanding the Multi-Supplier Strategy
In today’s fast-paced business environment, companies are constantly seeking ways to mitigate risk and enhance supply chain efficiency.
One effective approach to achieving this goal is through a multi-supplier strategy.
This strategy involves partnering with multiple suppliers for the same goods or services instead of relying on a single supplier.
By doing so, companies can diversify their risk, improve resilience, and optimize safety stock.
A multi-supplier strategy enables businesses to spread their dependencies and reduce the risk of disruptions in supply.
Relying on a single supplier may expose a company to significant risks, especially if that supplier faces operational issues, financial difficulties, or logistical challenges.
With multiple suppliers, a company can maintain a steady flow of products, even if one supplier encounters problems.
The Importance of Diversifying Risk
Supply chain disruptions can occur due to various factors, such as natural disasters, geopolitical tensions, market volatility, and unforeseen circumstances.
By having a multi-supplier strategy, companies can effectively spread risk across different suppliers located in diverse regions.
This risk diversification ensures that if one supplier is unable to deliver, others can step in to fulfill the demand.
Moreover, a multi-supplier strategy allows companies to negotiate better terms with suppliers, as they are not solely dependent on any single source.
This competitive advantage helps businesses to secure more favorable pricing, payment terms, and service levels.
Ultimately, this approach reduces the supplier’s bargaining power and enhances the company’s overall supply chain resilience.
Optimizing Safety Stock
Safety stock plays a crucial role in preventing stockouts and ensuring customer satisfaction.
It acts as a buffer against demand fluctuations and supply chain uncertainties.
However, maintaining the right amount of safety stock is a delicate balance.
Too much safety stock can lead to increased holding costs, while too little can result in missed sales opportunities.
A multi-supplier strategy can help companies optimize safety stock levels.
By sourcing from multiple suppliers, companies can analyze lead times, reliability, and performance metrics of each supplier to determine the optimal amount of safety stock required.
This analysis enables businesses to maintain adequate inventory levels without overstocking, thus minimizing holding costs while ensuring product availability.
Calculating Optimal Safety Stock Levels
To effectively optimize safety stock, companies need to consider several factors.
These include the lead time variability of each supplier, demand variability, and the desired service level.
By evaluating these elements, businesses can calculate the appropriate safety stock levels to mitigate risks caused by supply chain disruptions.
Using statistical methods, such as standard deviation and z-scores, companies can derive safety stock levels that align with their service level objectives.
For example, a business aiming for a high service level may choose to carry more safety stock to ensure availability during unexpected demand spikes.
Conversely, a company with a higher tolerance for stockouts may opt for a leaner safety stock strategy.
Implementing a Multi-Supplier Strategy
Implementing a multi-supplier strategy requires careful planning and coordination.
Here are some steps to effectively adopt this approach:
1. Assess Supplier Capabilities
Identify potential suppliers for your products or services and evaluate their capabilities, reliability, and geographical location.
Understanding their strengths and weaknesses will help you make informed decisions about which suppliers to engage with.
2. Negotiate Terms and Agreements
Once you have identified suitable suppliers, negotiate favorable terms and agreements.
Ensure that the contracts specify quality standards, delivery schedules, and pricing arrangements.
Establish communication channels to address any issues that may arise during the partnership.
3. Monitor Supplier Performance
Regularly monitor the performance of your suppliers to ensure they meet the agreed-upon standards.
Implement key performance indicators (KPIs) to track delivery times, product quality, and responsiveness to changes in demand.
This monitoring will help you assess the reliability of each supplier and make necessary adjustments to your strategy.
4. Utilize Technology for Supplier Management
Leverage technology to streamline supplier management processes.
Supply chain management software can provide real-time data on inventory levels, supplier performance, and demand patterns.
This information enables businesses to make data-driven decisions and optimize their multi-supplier strategy effectively.
Benefits of a Multi-Supplier Strategy
A well-executed multi-supplier strategy offers numerous benefits for businesses:
Enhanced Risk Mitigation
By diversifying supplier relationships, companies reduce the risks associated with supply chain disruptions.
This, in turn, minimizes the impact of unforeseen events and enhances overall business continuity.
Improved Flexibility and Resilience
A multi-supplier approach provides companies with greater flexibility in responding to changes in demand and market conditions.
It allows for a more adaptable supply chain that can quickly adjust to unforeseen challenges.
Cost Efficiency
With multiple suppliers, companies can negotiate better pricing and terms, leading to potential cost savings.
This competitive advantage helps optimize total procurement costs while ensuring the availability of high-quality products.
Conclusion
In an increasingly complex and unpredictable business landscape, adopting a multi-supplier strategy is a prudent choice to diversify risk and optimize safety stock.
By collaborating with multiple suppliers, companies can enhance their supply chain resilience, improve risk management, and achieve cost efficiency.
As businesses continue to navigate uncertainties, a robust multi-supplier strategy will remain a valuable asset in safeguarding their operations and meeting customer expectations.
資料ダウンロード
QCD調達購買管理クラウド「newji」は、調達購買部門で必要なQCD管理全てを備えた、現場特化型兼クラウド型の今世紀最高の購買管理システムとなります。
ユーザー登録
調達購買業務の効率化だけでなく、システムを導入することで、コスト削減や製品・資材のステータス可視化のほか、属人化していた購買情報の共有化による内部不正防止や統制にも役立ちます。
NEWJI DX
製造業に特化したデジタルトランスフォーメーション(DX)の実現を目指す請負開発型のコンサルティングサービスです。AI、iPaaS、および先端の技術を駆使して、製造プロセスの効率化、業務効率化、チームワーク強化、コスト削減、品質向上を実現します。このサービスは、製造業の課題を深く理解し、それに対する最適なデジタルソリューションを提供することで、企業が持続的な成長とイノベーションを達成できるようサポートします。
オンライン講座
製造業、主に購買・調達部門にお勤めの方々に向けた情報を配信しております。
新任の方やベテランの方、管理職を対象とした幅広いコンテンツをご用意しております。
お問い合わせ
コストダウンが利益に直結する術だと理解していても、なかなか前に進めることができない状況。そんな時は、newjiのコストダウン自動化機能で大きく利益貢献しよう!
(Β版非公開)