- お役立ち記事
- Multilayer film formation technology and optimization method with uniform thickness using thermoplastic resin
月間77,185名の
製造業ご担当者様が閲覧しています*
*2025年2月28日現在のGoogle Analyticsのデータより
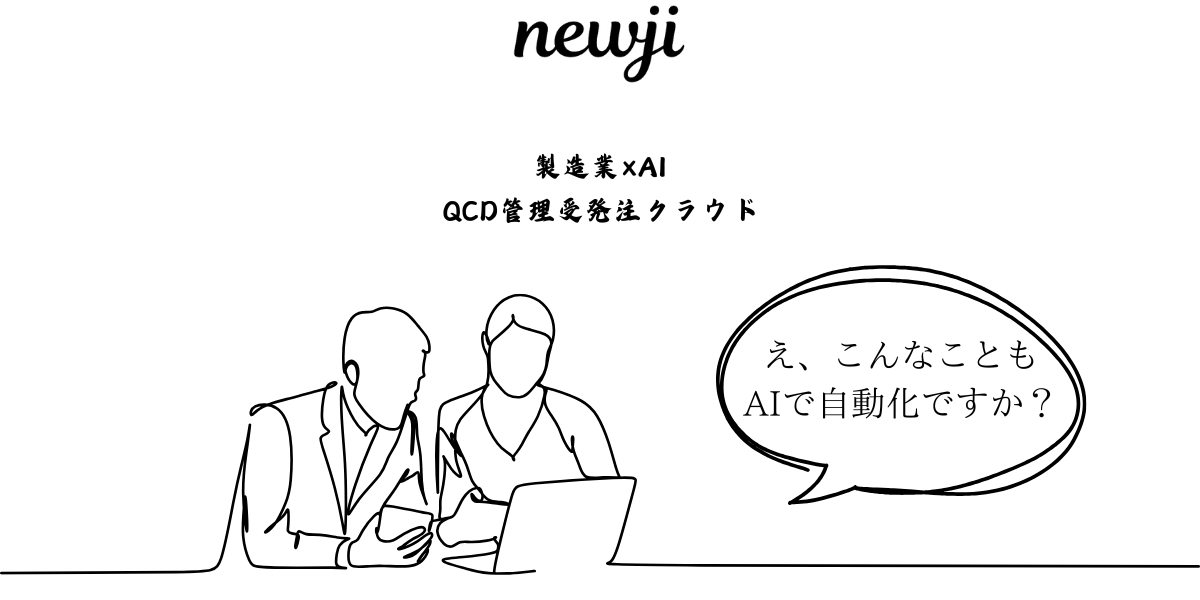
Multilayer film formation technology and optimization method with uniform thickness using thermoplastic resin
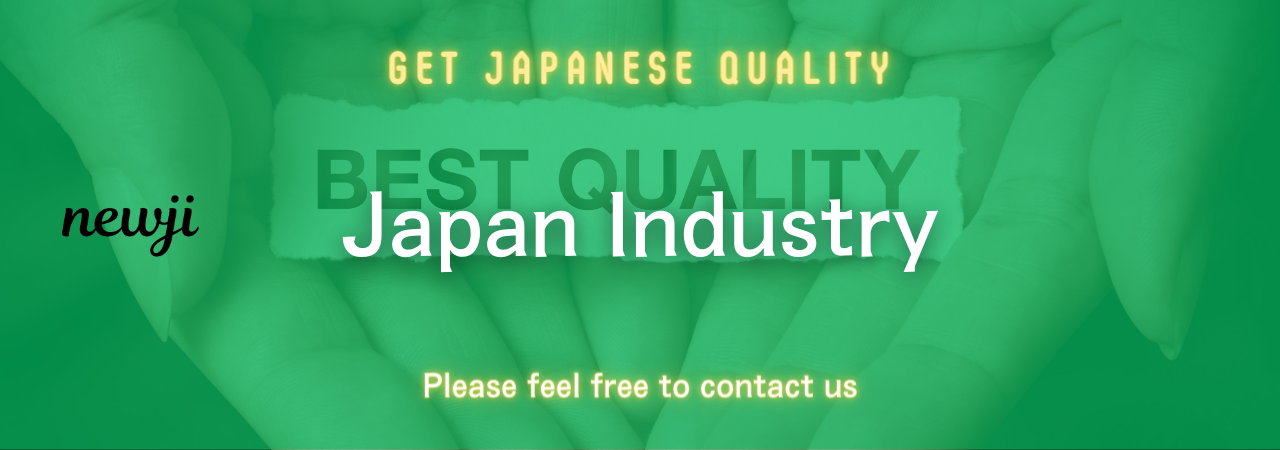
目次
Introduction to Multilayer Film Formation
Multilayer film formation is a critical process in many industries, involving the creation of films comprising different layers, each with specific properties and functions.
These films are primarily used in packaging, automotive, and electronic applications, providing barrier properties, mechanical strength, and innovation in design.
Understanding Thermoplastic Resins
Thermoplastic resins are pivotal in producing multilayer films due to their versatility and recyclability.
They soften on heating and harden upon cooling, allowing for repeated reshaping and reformation.
Common thermoplastic resins include polyethylene (PE), polypropylene (PP), and polyvinyl chloride (PVC).
The choice of resin impacts the properties of the final multilayer film, such as its strength, flexibility, and resistance to environmental factors.
Importance of Uniform Thickness
Uniform thickness in multilayer films is essential for consistent performance in applications.
Non-uniformity can lead to weak spots, affecting the film’s strength and barrier properties, which could compromise product integrity.
Achieving a uniform thickness ensures reliable performance, quality control, and consumer trust.
Technologies for Multilayer Film Formation
Various technologies are employed to produce multilayer films, each with its advantages and limitations.
Co-Extrusion
Co-extrusion is a widely used technique where multiple layers of thermoplastic resin are extruded together.
This process allows precise control over the composition and thickness of each layer.
Typically, co-extrusion involves feeding different polymers through separate extruders, which merge in a common die to form a multilayer film.
Solvent Casting
In solvent casting, thermoplastic resins are dissolved in a solvent and applied to a surface where the solvent evaporates, leaving behind a thin film.
While effective for certain applications, solvent casting can be limited by the solvent’s volatility and environmental impact.
Lamination
Lamination involves bonding pre-formed layers of film using heat and pressure.
This method is excellent for combining various properties by layering different materials; however, it can be more labor-intensive and costly than other methods.
Optimizing Film Thickness
To achieve optimal thickness, it is crucial to focus on process design, material selection, and technological advancements.
Process Parameters
Fine-tuning process parameters like temperature, pressure, and cooling rate is vital for controlling thickness uniformity.
For instance, maintaining a consistent temperature profile across the die can prevent uneven thickness and unwanted gradients.
Material Characteristics
The intrinsic properties of the chosen thermoplastic resin, such as melt flow index and viscoelastic behavior, influence thickness control.
Selecting materials with appropriate flow characteristics can help maintain uniform film thickness during formation.
Advanced Techniques
Emerging technologies like in-line thickness measurement and real-time feedback systems provide new avenues for optimization.
These technologies allow for immediate adjustments during the film formation process, ensuring thickness consistency.
Challenges and Solutions
While promising, achieving uniform thickness in multilayer films presents challenges.
Material Compatibility
Different thermoplastic resins can exhibit compatibility issues when combined, potentially leading to delamination or weak interfacial bonding.
Using compatibilizers or exploring alternative materials can mitigate these risks.
Equipment Calibration
Regular calibration of production equipment is essential to ensure optimal performance.
Calibration helps detect deviations in machine functioning that could adversely affect film uniformity.
Environmental Considerations
Environmental factors such as humidity and temperature fluctuations can impact the film formation process.
Implementing controlled environments within production facilities can help stabilize the process.
Conclusion
Mastering multilayer film formation with uniform thickness using thermoplastic resins requires a combination of technology, material science, and process optimization.
By harnessing advanced co-extrusion, fine-tuning parameters, and leveraging real-time feedback, industries can produce high-quality films with predictable performance.
Despite the challenges, continuous innovation and technological advancements hold the promise of enhancing the efficiency and quality of multilayer films across various applications, benefiting both manufacturers and end-users.
資料ダウンロード
QCD管理受発注クラウド「newji」は、受発注部門で必要なQCD管理全てを備えた、現場特化型兼クラウド型の今世紀最高の受発注管理システムとなります。
ユーザー登録
受発注業務の効率化だけでなく、システムを導入することで、コスト削減や製品・資材のステータス可視化のほか、属人化していた受発注情報の共有化による内部不正防止や統制にも役立ちます。
NEWJI DX
製造業に特化したデジタルトランスフォーメーション(DX)の実現を目指す請負開発型のコンサルティングサービスです。AI、iPaaS、および先端の技術を駆使して、製造プロセスの効率化、業務効率化、チームワーク強化、コスト削減、品質向上を実現します。このサービスは、製造業の課題を深く理解し、それに対する最適なデジタルソリューションを提供することで、企業が持続的な成長とイノベーションを達成できるようサポートします。
製造業ニュース解説
製造業、主に購買・調達部門にお勤めの方々に向けた情報を配信しております。
新任の方やベテランの方、管理職を対象とした幅広いコンテンツをご用意しております。
お問い合わせ
コストダウンが利益に直結する術だと理解していても、なかなか前に進めることができない状況。そんな時は、newjiのコストダウン自動化機能で大きく利益貢献しよう!
(β版非公開)