- お役立ち記事
- Multinational supplier management challenges and solutions faced by purchasing departments
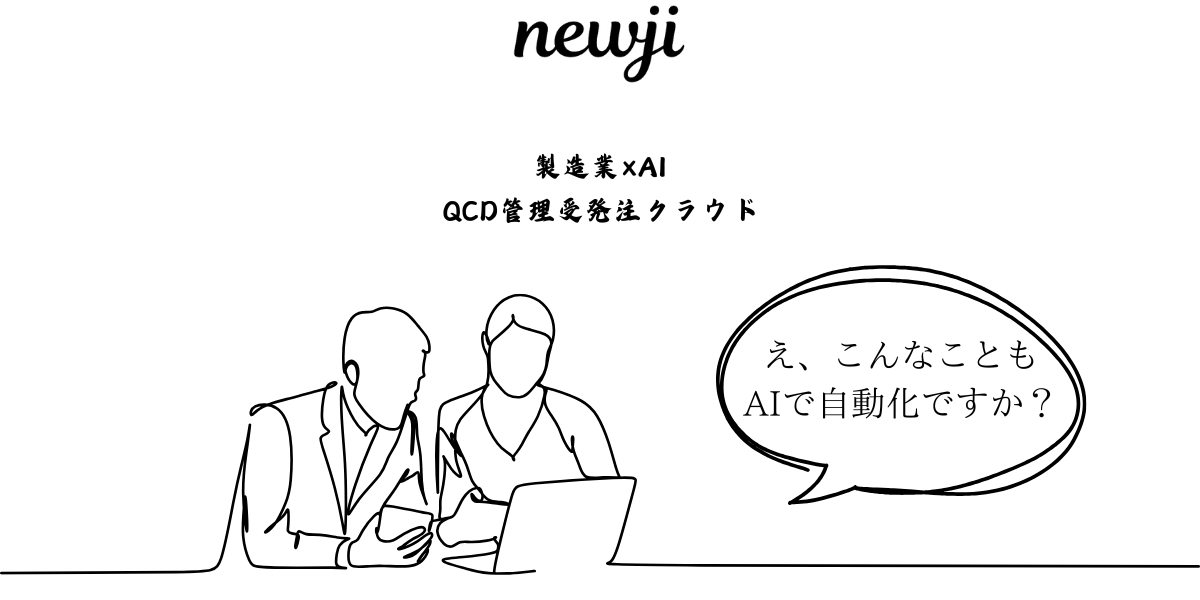
Multinational supplier management challenges and solutions faced by purchasing departments
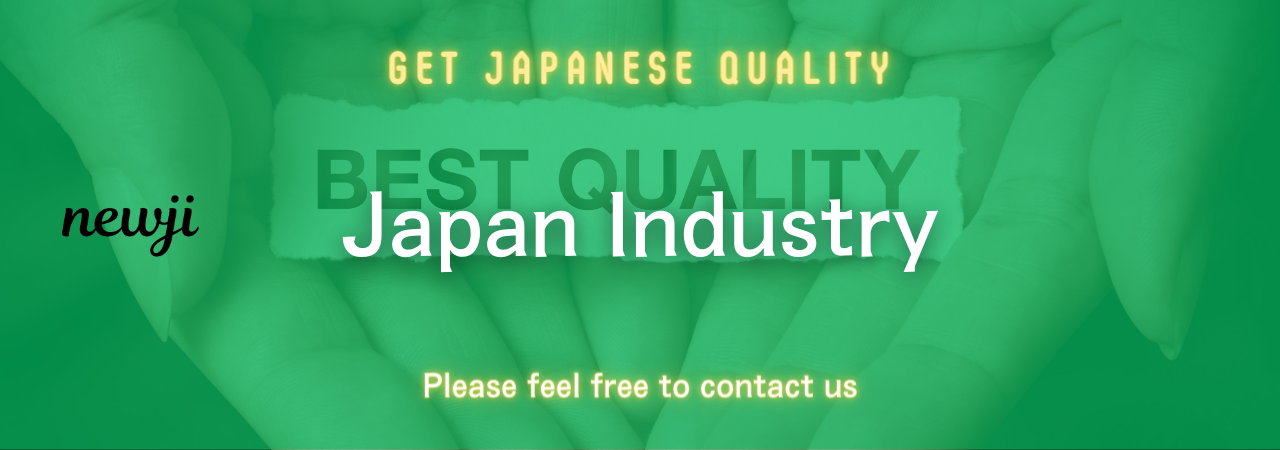
目次
Understanding the Complexities of Multinational Supplier Management
In today’s globalized economy, purchasing departments increasingly rely on multinational suppliers to meet their needs.
While this approach offers numerous advantages, it also presents unique challenges.
Managing suppliers across different countries involves complex logistical, financial, and cultural dynamics that can affect the efficiency and success of the purchasing process.
Handling these complexities requires a strategic approach, with an emphasis on effective communication, robust risk management, and fostering strong supplier relationships.
Cultural and Communication Barriers
One of the primary challenges in multinational supplier management is navigating cultural and communication barriers.
Different countries have distinct business practices, languages, and cultural norms.
These differences can lead to misunderstandings and misinterpretations, which can adversely affect negotiations and contracts.
For purchasing departments, it’s crucial to understand the cultural nuances of each supplier’s region.
This might involve investing in language translation services or cultural training for staff.
Building a team with diverse cultural backgrounds can also enhance communication and mutual respect between parties.
Regulatory Compliance and Legal Considerations
Another significant challenge is understanding and adhering to the varying regulations and legal requirements of each supplier’s country.
These can range from import/export restrictions, labor laws, to environmental regulations.
Non-compliance can lead to legal penalties, shipment delays, and damage to the company’s reputation.
To mitigate these risks, companies should establish a strong legal team or partnership with local legal advisors who are well-versed in the regulatory landscape of the supplier’s country.
This proactive approach ensures that the purchasing department is always operating within the bounds of the law.
Logistical Challenges
Managing logistics with multinational suppliers involves overcoming several hurdles such as currency fluctuations, varying shipping times, and customs procedures.
These factors can impact cost efficiency and delivery schedules, making it essential for purchasing departments to have a robust logistics strategy.
Utilizing advanced supply chain management software can aid in tracking shipments, forecasting potential delays, and adjusting procurement plans to maintain supply chain continuity.
Regularly reviewing and optimizing logistics strategies can also help in keeping costs down and ensuring timely deliveries.
Risk Management
Supplier risk is amplified when dealing with multiple international partners.
Political instability, economic changes, or natural disasters can disrupt operations and affect supplier reliability.
To minimize these risks, purchasing departments should conduct thorough risk assessments of each supplier, considering geopolitical situations and potential economic crises.
Diversifying the supplier base is another effective strategy, as it spreads the risk and reduces dependency on any single supplier.
Establishing contingency plans and maintaining flexible contracts can also provide a safety net during unforeseen events.
Quality Control and Assurance
Ensuring consistent product quality from international suppliers can be challenging, especially when standards vary significantly between countries.
Purchasing departments must enforce strict quality control measures to uphold company standards and customer satisfaction.
Conducting regular audits, setting clear quality benchmarks, and maintaining an open line of communication with suppliers regarding quality expectations are essential steps in this process.
Strong relationships with suppliers can also facilitate collaboration in resolving quality issues amicably and promptly.
Strategies for Effective Multinational Supplier Management
While the challenges are significant, there are effective strategies that purchasing departments can employ to manage multinational suppliers successfully.
Building Strong Relationships
Cultivating strong relationships with suppliers can pave the way for successful collaboration.
Trust and mutual respect can lead to better negotiating terms, smoother operations, and improved conflict resolution.
Regular communication, joint goal setting, and periodic face-to-face meetings can strengthen these ties.
It’s also beneficial to acknowledge and reward suppliers who consistently meet expectations, fostering goodwill and loyalty.
Emphasizing Technology Integration
Leveraging technology can streamline many aspects of supplier management.
Implementing integrated supply chain management systems allows for real-time data sharing and collaboration across different geographical locations.
Technology can help in maintaining transparency, enhancing accuracy, and improving efficiency, which are essential for managing a network of suppliers across borders.
Conducting Regular Performance Reviews
Regularly evaluating the performance of international suppliers is vital to ensure they meet contractual obligations and quality standards.
These reviews should assess delivery times, quality of goods, compliance with regulations, and responsiveness to issues.
Feedback from these evaluations should be used to improve supplier performance, renegotiate terms, or, if necessary, end contracts with underperforming suppliers.
Staying Informed and Adaptable
The global market is dynamic and subject to rapid changes.
Purchasing departments must stay informed about global economic trends, political climates, and technological advancements that could impact their supply chain.
Adopting a flexible and adaptive approach enables businesses to quickly pivot their strategies in response to these changes, ensuring continuity and competitiveness.
Conclusion
Successfully managing multinational suppliers requires awareness of the myriad challenges involved and implementing thoughtful solutions.
By focusing on effective communication, compliance, risk management, technology integration, and relationship building, purchasing departments can overcome these obstacles.
In doing so, they will not only enhance their procurement operations but also contribute significantly to their organization’s overall success in a competitive global marketplace.
資料ダウンロード
QCD調達購買管理クラウド「newji」は、調達購買部門で必要なQCD管理全てを備えた、現場特化型兼クラウド型の今世紀最高の購買管理システムとなります。
ユーザー登録
調達購買業務の効率化だけでなく、システムを導入することで、コスト削減や製品・資材のステータス可視化のほか、属人化していた購買情報の共有化による内部不正防止や統制にも役立ちます。
NEWJI DX
製造業に特化したデジタルトランスフォーメーション(DX)の実現を目指す請負開発型のコンサルティングサービスです。AI、iPaaS、および先端の技術を駆使して、製造プロセスの効率化、業務効率化、チームワーク強化、コスト削減、品質向上を実現します。このサービスは、製造業の課題を深く理解し、それに対する最適なデジタルソリューションを提供することで、企業が持続的な成長とイノベーションを達成できるようサポートします。
オンライン講座
製造業、主に購買・調達部門にお勤めの方々に向けた情報を配信しております。
新任の方やベテランの方、管理職を対象とした幅広いコンテンツをご用意しております。
お問い合わせ
コストダウンが利益に直結する術だと理解していても、なかなか前に進めることができない状況。そんな時は、newjiのコストダウン自動化機能で大きく利益貢献しよう!
(Β版非公開)